Rolls-Royce increases its share of the US$5.3 trillion civil aviation market through digitalisation
Rolls-Royce is the current marker leader in the wide-body aircraft segment. The intense competition in the market results in manufacturers willing to sell their products without profit, but capture significant value from the MRO (maintenance, repair and overhaul) business driven by digital data. As a result, digital technologies not only transform Rolls-Royce’s product supply chain from initial concept to aircraft delivery, but also the company’s service offerings and aftermarket supply chain. Now the question is how can Rolls-Royce develop its existing workforce to be more adaptable, change-ready and digitally savvy?
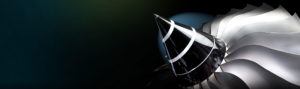
The demographic and economic growth of the countries around the world result in anticipated air traffic increase of 4.4% annually, requiring approximately 35,000 new aircrafts at a value of US$5.3 trillion over the next 20 years (1). In addition, driven by environmental concerns and the pressure on airline ticket prices from low-cost carriers, airlines demand more fuel-efficient aircraft engines, resulting in more-technologically complex designs and shorter development cycles (2). The challenge of delivering a greater volume of more-sophisticated jet engines creates significant disruption to the engine manufacturers’ supply chains. This is where the adoption of digital technologies and their integration with the existing supply chain becomes not only a competitive advantage for the jet engine manufacturers but also determines the companies’ long-term prospects.
The jet engine market is dominated by three companies: General Electric, Rolls-Royce and Pratt & Whitney. Rolls-Royce is the current marker leader in the wide-body aircraft segment (aircrafts having a fuselage wide enough to accommodate two passenger aisles) and has approximately 50% share of the new orders (3). The intense competition in the market results in manufacturers willing to sell their products without profit, but capture significant value from the MRO (maintenance, repair and overhaul) business driven by digital data. As a result, digital technologies not only transform Rolls-Royce’s product supply chain from initial concept to aircraft delivery, but also the company’s service offerings and aftermarket supply chain.
In order to shorten the product development cycle as well as reduce costs, Rolls-Royce is moving towards a completely digital design-and-test process for the jet engines it builds. The company has an already integrated planning and manufacturing execution system and the medium-term goal is to move all data on the cloud, so that it can be accessed in a controlled and selective fashion by all parties involved in the supply chain.
Furthermore, Rolls-Royce is embracing Industry 4.0, by bringing together robotics, virtual manufacturing and digital workflow, where all information related to design and manufacturing is transferred digitally across the entire supply chain (4). Another major technology Rolls-Royce is adopting is ALM (Additive Layer Manufacturing)/ 3D printing that provides the opportunity to design and manufacture much more complex products that are unachievable with conventional manufacturing technologies (5). Rolls-Royce produced in 2015 the largest component ever built using ALM and the company’s focus in the short-term is on using ALM in manufacturing prototypes to accelerate the product development cycle (6). In the medium-term, the company is looking at adopting ALM for the manufacturing of increasing number of engine components as the speed of the process and the number of materials certified for aerospace use increase.
In the service supply chain, Rolls-Royce is looking at using augmented reality to allow a technician at an airport to access maintenance data and 3D models and trouble-shoot a jet engine. In addition, an engineer at the headquarter can observe through real-time streaming the operation’s progress and guide the technician if required. This results in reduced disruptions to the airlines’ operations and lower maintenance costs for Rolls-Royce.
Rolls-Royce’s Engine Health Management (EHM), where data is streamed from engines in operations for analysis and trouble-shooting, is a pioneer in the advanced data analytics area. The short to medium-term goal for the company is to expand the service’s digital capabilities and develop EHM into a predictive data analytics tool that goes beyond physical models to proactively detect the unexpected through AI.
Further steps Rolls-Royce can take, building on its EHM capabilities, is the adoption of digital technologies based on RFID, allowing the company and its supply chain to store and retrieve valuable engine and parts information accurately. This can be developed also in retrofit packages and implemented during scheduled engine shop visits. Moreover, utilising the Internet of Things (IoT), the engine manufacturing and maintenance can be further improved by integrating digital sensors during the parts manufacturing allowing traceability, real time analysis and ability to take prompt actions, therefore reducing lead times and improving process efficiency.
In the medium term, once the technology is economically feasible, Rolls-Royce can look at positioning ALM machines at its airport service centers and using them to manufacture spare parts on-demand, further reducing the maintenance cost and customers’ disruption. Moreover, to ensure that the 3D models delivered to the ALM machines for manufacturing are original and haven’t been hacked, Rolls-Royce can use blockchain technology (7).
Finally, Rolls-Royce can gain further competitive advantage in the industry by developing an ecosystem/ platform that allows the OEM, supply chain and customers’ data integration, analysis and proactive trouble-shooting. In doing so, Rolls-Royce can further reduce the product development cost as well as generate value from new service-centric business models.
- How can Rolls-Royce develop its existing workforce to be more adaptable, change-ready and digitally savvy?
- How can Rolls-Royce address the challenge of collecting the ever-increasing amount of data from multiple systems and players in a consistent form?
(Word Count: 787)
- Aircraft.airbus.com (2017) Global Market Forecast 2017-2036 [online] Available at:
http://www.aircraft.airbus.com/market/global-market-forecast-2017-2036/
[Accessed on 15 Nov. 2017]
2. Capgemini.com (2009). The Changing Face of the Aerospace & Defense Industry [online] Available at:
[Accessed on 15 Nov. 2017]
3. Rolls-Royce.com (2017) Country sites – Markets [online] Available at:
https://www.rolls-royce.com/country-sites/singapore/markets.aspx#civil-aerospace
[Accessed on 15 Nov. 2017]
4. Siemens.com (2017). Manufacturing’s Digital Dividend [online] Available at:
[Accessed on 15 Nov. 2017]
5. Rolls-Royce.com (2017). Insights – Neil Mantle on 3D printing [online] Available at:
http://www.rolls-royce.com/media/insights/neil-mantle.aspx
[Accessed on 15 Nov. 2017]
6. Rolls-Royce.com (2015). Rolls-Royce to fly Trent XWB with largest-ever 3D-printed part [online] Available at:
[Accessed on 15 Nov. 2017]
7. HBR.org (2017). Global Supply Chains Are About to Get Better, Thanks to Blockchain [online] Available at:
https://hbr.org/2017/03/global-supply-chains-are-about-to-get-better-thanks-to-blockchain
[Accessed on 15 Nov. 2017]
Stefan – great article! The two questions you raised at the end of your piece were two of the same ones that I thought of as I read. On the workforce front, I am particularly interested in how the AR maintenance offering would effect the size and composition of the workforce. Would it reduce the total number of maintenance workers, change the training required, shift geographic allocation?
As it relates to using ALM for jet engine parts – I am curious where we are in ensuring the safety of 3D printing manufacturing. The cost of a part failing is immense, so the company needs to make sure this technology is ironclad, just as it needs to ensure the machines producing the machines cannot be infiltrated by hackers
Great topic Stefan! I still wonder how is Rolls-Royce going to maintain its competitive advantage as competitors adapt the incredibly growing 3D printing trends in the aerospace market. As of April 2017, General Electric was planning on mass-producing 25,000 LEAP engine nozzles with 3D printing (1). At the same time, according to Professor Moataz Attallah, director of Advanced Material and Processing Lab at the University of Birmingham in the UK, that switching to 3D printing brings in additional challenges such as higher costs when compared to established manufacturing technology like casting and forging, and additional labor needed in post-processing is also needed, reducing the level of autonomy.
However, given the size of these players in the aerospace industry I believe that they are able to take all the steps further to secure an efficient implementation of such technology, even solidifying their relationships with suppliers of raw materials like powder metals.
[1] Kerns, Jeff. “Aerospace Opportunities Demand Quick Resolution to 3D-Printing Issues”. Apr 20th, 2017; http://www.machinedesign.com/3d-printing/aerospace-opportunities-demand-quick-resolution-3d-printing-issues; Accessed on November 30th, 2017
Stefan, thanks for sharing this article. I was particularly interested in the use of ALM machines to build prototypes and eventually manufacture spare parts on-demand through airport service centres. Producing these parts on-demand would certainly minimize maintenance costs and customer disruption. I wonder if reduced customer dependence on Rolls-Royce’s maintenance activities would impact its MRO business.
My second question relates to the use of 3D printing technologies through the ALM machines at Rolls-Royce. As 3D printing technologies become more commercialized in the mass market, do you see an opportunity for smaller disruptors to manufacture spare parts for Rolls-Royce’s engines? Would Rolls-Royce welcome the “outsourced” production of spare parts by other manufacturers, or would the company like to preserve the production of these parts within its own supply chain?
Stefan – thanks for sharing this piece. It is great to see industry incumbents, such as Rolls-Royce, fully embracing technology to maintain their competitive advantage. I think that it is fascinating that Rolls-Royce is looking at cutting edge technology such as augmented reality, as this type of technology has the potential to streamline and improve Rolls-Royce’s servicing operations. What timeline does Rolls-Royce have in mind to start rolling out this program? I believe that a key stakeholder that Rolls-Royce’s management team needs to consider are the technicians in the field. I am quite curious to know what steps Rolls-Royce takes to secure the buy-in of experienced technicians who may be skeptical of this type of technology.
Great paper and a very interesting topic. I am curious to see how 3D printing is rolled out at the individual airport services centers and the breakpoint of economic feasibility when deciding to house a printer on-site. Currently are suppliers providing parts to service centers and therefore needing to keep a minimum inventory of replacement parts? Will this help suppliers by reducing inventory demands?
Using EHM appears to be a game changer when it comes to predicting what will go wrong with an engine. I wonder what value this will bring to the airlines who are leasing the engines in terms of less downtime. Will Rolls-Royce be able to monetize this added benefit, or will it be quickly replicated by competitors as an industry standard?
Great article, Stefan. Very interesting to read how RR is investing in technology to stay ahead of competition.
First of all, I am curious to see whether 3D printing can assure the same level of quality of parts, and whether it will be able to convince regulators.
Secondly, I am wondering to what extend RR can maintain its competitive advantage, as more and more companies are entering this 3D-printing industry.
Very informative article Stefan! The second question you raised is a very interesting problem that all large companies face. I believe that Rolls-Royce will have to standardize how it inputs information from its various players, only storing the key information. Identifying the correct standard will require a large amount of research and likely the employment of a consulting firm. The risk of not standardizing is losing key information in transition from one party to the next.
Another concern for Rolls-Royce is cybersecurity with ever increasing digitalization. As one of its medium-term goals, moving all data to the cloud comes at a large risk. This data gives insight into the company’s competitive advantage. Additionally, the digitalization of the EHM is a key operational efficiency, but can present safety risks if hacked. Is the cybersecurity protection utilized by Rolls-Royce today adequate to protect the company’s digital platform as it grows?