Rio Tinto – Digging into the Data and Autonomous Vehicle Technologies
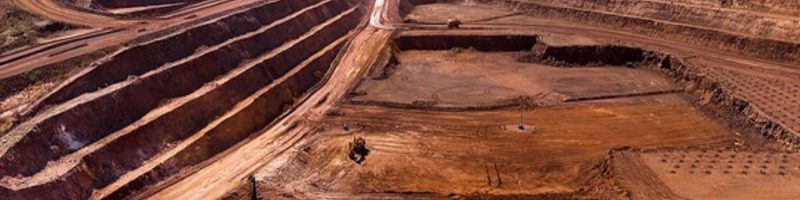
Leading mining companies like Rio Tinto are developing and deploying autonomous haulage technologies in-house and using big data to make smarter real-time decisions at the rock face. What are some of the opportunities and challenges presented by these advances?
Rio Tinto’s operation in the Pilbara is the second largest exporter of iron ore in the world, integrating 16 mines, four port terminals, and 1,700 km of rail and related infrastructure [1]. The complex is expected to produce and ship approximately 330 million tonnes in 2017 [2].
Rio Tinto markets iron ore tailored to the needs of steel mill consumers, an example being the Pilbara blend. No single Rio Tinto mine can produce the blend, so the company must plan the final product by adjusting and sourcing materials from its remote mines, tracking the material, mixing the final product, and shipping it [3].
Product Quality Variance from Mean [Exhibit 1]
Mining operations have historically acted as independent entities that exhibit significant production variations on any given day. Mines had generally infrequent communication between themselves, and decisions were often made in the field, with limited information. With big-data and autonomous systems, new opportunities for big-picture, real-time decisions have emerged.
Rio Tinto has seized these opportunities, integrating multiple complex operations through an Operations Center in Perth, which supports and oversees its production network. From this nerve center, operators oversee a fleet of mobile equipment, including self-driving haul trucks and a network of autonomous trains [4].
In Q2 2017, around 20% of Pilbara tonnage was transported autonomously by rail the mine sites to the port through a technology that Rio Tinto calls Autohaul [2]. Rio Tinto plans to complete the project by the end of 2018, transporting approximately a million tonnes a day of iron ore from its Pilbara network autonomously [2]. Tests have already shown reduction of variability and throughput time of iron ore transportation [Exhibit 2], which will lead to lower hauling costs, more efficient blending operations, and reduced bottlenecking at material transfer sites.
A >1hr reduction in average cycle time with Autohaul during H1 2017 [Exhibit 2]
Unlike the operations of the past, which stopped for shift changes, autonomous equipment can operate 365 days a year, 24 hours a day [5].
Rio Tinto will be able to make use of its operation center and integrated operations to drive maximum efficiencies from its assets. Beyond debottlenecking, the miner will be able to draw conclusions from its massive sensor data, using its mobile fleet’s aggregate history to respond to sensor reports, pre-emptively moving equipment which report problems into maintenance, rather than suffering equipment damage or undertaking less efficient, reactive maintenance. Sometimes components may even last longer than advertised – Rio Tinto will be able to predict component failure times from its own data, rather than needing to rely on guideline specs provided by the manufacturer [6].
In the short and medium terms, management will have to fine-tune the Pilbara material transport network, identify the next target sites in the firm for rollout of the existing tech, and identify what other mining processes can be rendered autonomous economically.
Total supply chain visibility will present several competitive advantages in the future for Rio. The firm should be able to push on or cut out external traders simply by being more effective operationally. Through synchronization, coordination and automation within its production chain, Rio Tinto could disintermediate existing trader networks by knowing its position relative to the market at any moment. [6]
Visibility combined with autonomous control could allow Rio Tinto being able to change its product mix rapidly, responding to short-term price variations between iron ore blends. If Rio’s operations are able to flexibly adjust their production to demand (almost unheard of in the industry), the firm’s sales and marketing arm could capture more value in the marketplace.
In this vein, the organization should explore how integrating ships, traditional or autonomous, into the Rio Tinto Pilbara Operations network will allow the firm to further reduce costs and drive margins.
Rio Tinto will be able to mine both data and rock to maintain its position as a flagship natural resources firm. But its technology also poses several dilemmas.
New mines will always need to be built. Communities have been open to mines in part due to the jobs the industry creates. As mining continues to automate, there will be fewer jobs in the space. Those that remain will be far from operations and require more schooling than existing positions. If the mines do not provide significant employment opportunities to communities in which they operate, the mines risk their social license to operate, and projects may be difficult to start. To what extent should the industry automate?
Can Rio Tinto remain a technological leader in this space as a mine operating company facing startups and tech giants? Is it more cost-efficient for Rio Tinto to push forward on this technology itself, or should it seek partnerships with other operating companies? Could value be created by selling advice or in-house technology to other firms?
[796 words]
References
[1] Riotinto.com. (2017). Driving Productivity in the Pilbara. [online] Available at: http://www.riotinto.com/australia/pilbara-4691.aspx [Accessed 16 Nov. 2017].
[2] Rio Tinto Q2 2017 Report. (2017). [online] Rio Tinto, p.2. Available at: http://www.riotinto.com/documents/170718_Rio_Tinto_releases_second_quarter_production_results.pdf [Accessed 14 Nov. 2017].
[3] Rio Tinto Groundbreakers. (2017). Pilbara Blend. [online] Available at: https://riotintogroundbreakers.com/30-pilbara-blend/ [Accessed 16 Nov. 2017].
[5] The Digital Revolution – Mining starts to reinvent the future. (2017). [ebook] Deloitte, pp.1-13. Available at: https://www2.deloitte.com/content/dam/Deloitte/global/Documents/Energy-and-Resources/deloitte-au-er-digital-revolution.pdf [Accessed 16 Nov. 2017].
[6] Digital Transformation Initiative – Metals and Mining Industry. (2017). [online] Accenture, pp.4-12. Available at: https://www.accenture.com/t20170116T084456__w__/us-en/_acnmedia/Accenture/Conversion-Assets/WEF/PDF/Accenture-Mining-And-Metals-Industry.pdf [Accessed 16 Nov. 2017].
[Exhibit 1] RT Chartbook. (2017). [online] Rio Tinto PLC, p.44. Available at: http://www.riotinto.com/documents/RT_chartbook.pdf [Accessed Nov. 2017].
[Exhibit 2] Riotinto.com. (2017). Iron Ore Roadshow p 19. [online] Available at: http://www.riotinto.com/documents/170809_Presentation_Iron_Ore_roadshow.pdf [Accessed Nov. 2017].
Having worked in the Rio Tinto Iron Ore division several years ago while the remote operations center was being established, i can confirm the enormous impact on the efficiency of the entire system. This impact is well conveyed in the article and serves to demonstrate the value of digitization in supply chains. This roll-out across a supply chain entirely owned and operated by Rio Tinto provides a good example of the inefficiencies gained when a supply chain works together. The friction points that exist between separate owners of production/rail/port are removed and this connected solution can thrive. Anecdotally, this connectivity has reduced unit costs by over 10% on the worlds largest raw input material, iron ore. Imagine the impact if the global mining industry could replicate this for the majority of production in all metals. The raw input costs of durable goods would drop and provide a genuine boost to global GDP through increased construction and consumption at a lower price point. How do we take this model and apply it to supply chains with different actors to increase the pie for everyone? Will this realistically ever happen or will individual company preferences stifle this productivity gain.
The author’s point about employment dynamics is a fascinating one that certainly warrants further exploration. While increased efficiency can be touted as positive, mines have seen enormous backlash from the communities in which they operate due to the extractive and degradative nature of the work. If Rio Tinto and other mining companies who follow suit are no long providing the employment that they once offered, how will local communities react? What benefit will communities see to allowing a mine to operate in their backyard? What about local governments who are often a critical player to enabling mining operations? Rio Tinto should focus on ways to redeploy their employees in this new world of a highly digitized supply chain. This would ensure that employment levels are not drastically reduced, but rather overall output increases such that the productivity of each employee goes up.
Very well written article !
I indeed completely agree with you that major improvements will happen thanks to digitalization.
However, I don’t think this is the core business of Rio Tinto to digitalize itself alone. Indeed, these new technologies are extremely complex and need careful fine-tuning to be efficient. I believe that you need to get the help of a specialist if you want to take out the most out of this trend. Rio Tinto core know-how is mining, not developping software.
I think that Rio Tinto should seek partnership with other companies in order to design a taylored product that will take the most out of the new technologies that Rio Tinto can’t manage itself.
I agree with the author that automation and digitization holds great potential to improve the productivity of mining companies. Given the high fixed costs associated with mine operation, any improvement in production yield and asset utilization in a given unit of time with a given amount of equipment will flow directly to the bottom line. Self-driving vehicles and sensor-equipped technologies, as the author points out, achieves better efficiency in the production process. However the efficiency gains need not be limited to mine production. What I find most exciting about the author’s article is the potential to use data to integrate miners’ sales & marketing operations with its production to adjust output rate and product mix according to market demand. I agree this will be the natural next step for Rio Tinto to take its current technology. As to concerns about local job creation, I think this is not a unique problem posed by higher-tech mining, but a more general issue our society will face with the rise of Artificial Intelligence and automation which also permeates to many other sectors. I suspect the right channel to tackle this issue is a complete rethinking of our current income distribution system – after all when machines are productive enough, we no longer need to employ all humans to maintain the same level of societal wealth. The question is how to redistribute the productivity gains from the technology owners and operators to the remaining population. A minimum guaranteed income scheme as proposed in several Scandinavian countries may be a good start.
Great article! I also liked Jonathon McCarthy’s point about the potential for this 10 percent improvement penetrating the entire mining industry, and the subsequent impact on global goods production. I finish this article feeling optimistic, yet curious about how it is to be done. I see two challenges in particular: implementation and successive roll-out.
In terms of implementation, I am curious how Rio Tinto would pursue this from a human capital, physical capital, and technological capital standpoint. I’d imagine that the firm doesn’t currently have the core competencies to execute on this successfully. Moreover, I’d imagine it is tough to attract the right talent internally for global deployments. Is Rio Tinto to work with tech companies or tech services companies? If so, what is the longer-term plan? Would Rio Tinto try to build competencies in-house? Either way, I wonder how this translates to the cost-effectiveness of this initiative.
And in terms of roll-out, what is the true cost of aggregating data at scale, when so many of these mines are in the most remote parts of this planet?
Again, I am so enthused to read about the potential of this initiative! I am curious how its implementation may translate to actual savings.
Nice analysis, Andrew! This is something many company are facing now. Since digitization is inevitable, how much can they leverage digitization to become their competitive advantage. What companies need to do to become a leader in digitization?
My own perspective, technology itself is not enough.
Companies need to build an entire organization around new technology and new way of working. Toyota way of working is a great example.
Technology will always become outdated, but the culture will never be. If the company can re-organize in such a way that innovations and new technologies are constantly embraced and experimented. They will become the industry leader in the end.
This is quite fascinating, Andrew. I’m curious if there could be a good company that Rio Tinto could acquire to conduct/oversee much of the digitization process. It’s not the core competency of Rio Tinto to oversee that digitization and I fear that the process of fully integrating tech into everything that it does could be rather difficult. Further, I wonder how labor utilization will be affected if technological innovations truly do take hold. Also, are there regulatory matters (specifically labor law/unions) that Rio Tinto should worry about as well? This might halt or stem the tide of technological change.
Interesting article, Andrew! I would like to add two key issues to automation in mining, which I think are crucial obstacles that need to be tackled in order to achieve a successful implementation:
– Safety: this is definitely one of the top concerns for any large mining player. Autonomous vehicles need to be calibrated and integrated into complex operations in which the human element is very significant. Premature implementation of such technologies, without an adequate people management strategy and enough trials, could jeopardize the safety of the mines. This is exactly what happened in BHP’s Jimblebar site (1): a self-driving truck collided with a manned vehicle, causing significant damage to both. The accident was caused by human error, as the driver failed to understand what the autonomous vehicle was intending to do. The human element is often the cause of automation-related accidents, what emphasizes the relevance of training and change management in this kind of initiatives.
– Acceptance from unions: having worked in mining in South America, I have experienced the power that unions have in emerging markets and how influential they can be on any decisions that affect the working dynamics at the site. They will certainly be against this kind of initiatives as they directly reduce the mine headcount, and this is a key factor to be considered for implementing automation in mines in emerging markets.
(1) “Mining automation: The be all and end all?”, Australian Mining Magazine, September 2015. https://www.australianmining.com.au/features/mining-automation-the-be-all-and-end-all/
Very unique and interesting article, yet the you have highlighted a very key social issue that is a hot topic globally. Is automation good for the world, the industry, the communities, job creation and so many other aspects? You have addressed part of the community impact and specially on the loss of job and change in the type of jobs needed. Similar to mining, many in the auto industry struggle with a similar concept. Is automation bad for the company? On the one hand it provides real time data and all the benefits that go along with it, it makes the job safer most of the times, improves quality and brings a level of consistency that cannot be expected of humans. On the other hand, it does shift the workforce platform. In some cases it simply reduces the number of roles needed and in some, it changes from one role to another. One practice some of the companies are considering is using the same workforce and investing in them by training them in the higher skills needed, paying for higher education and combining hands on experience with the new technology. Very interesting topic and if able to, would love to discuss further.