O&G Technological Revolution – Using Digital Technology In The New World Of Low Oil Prices
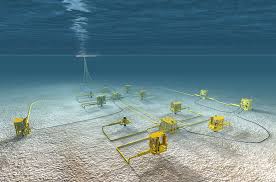
Digitization of the Oil Field- Using Digital Technology In The New World Of Low Oil Prices
In light of the oil and gas industry’s downturn, there has been a renewed interest in operational efficiency, ensuring long-term reliability of offshore equipment, and increased operational production per capital spent. Digitization has been making inroads within the industry, but the new economics of the oil and gas (O&G) has hastened the trend and become a new reality to be an industry leader. The influx of new data from digitization has begun to transform the organizational models within the major oil companies and improve the economics of the industry.
BP through the use of GE Intelligent Platforms Software launched a production optimization project connecting all of BP’s oil wells globally to the intranet. The field engineers for BP will have data for common machines and production data for all wells. The intent with this data will be to improve efficiency, prevent failures and minimize costly downtime. Furthermore, given the new availability of data the technology can be used to ensure the entire oil reservoir is considered and assessed prior to intervention in one well.
Cost of Downtime
A major focus for oil field service companies (Schlumberger, Baker Hughes, Halliburton, etc.) and oil and gas operators (Exxon, BP, EOG, etc.) has been to dramatically improve the reliability of the equipment and predict unplanned production downtime prior to the event. Industry averages show that for each week a well is not producing oil the operator losses $3 million in revenue[1]. The digitization of the offshore oil field has allowed for improvements to the existing reservoirs and reduced operating cost, since it is projected that “improving problem detection and treatment design can reduce operational costs by 10-25% through fewer interventions and more efficient resource utilization”[2].
Furthermore, by getting information across all of the equipment BP can look at facility reliability by looking at it at the system process level. Predicting failures early and with planned downtime putting measures in place to prevent the excess build up on sludge in the line, a higher probability with unplanned shutdowns, and a threat to the well production. By continual monitoring and engineering judgement, issues can be addressed during the annual planned downtime and associated turn around (TAR), improving the up time for the facility and the economics of the well.
Oil Reservoir Sensitivity and Importance of Holistic Thinking
The significant improvement in information gathering and distribution will allow for production engineers to assess the current overall reservoir system when making decisions, rather than historically relying on single well analysis. Few people outside of the industry are aware of the impact that one mistake in one drilled well can have on the overall reservoir.
Oil reservoirs are not like the ocean where time has made the chemical makeup overall very homogeneous from location to location, within reservoirs there are pockets of natural gas and hydrogen sulfide (H2S) that if disturbed can fundamentally impact the economics of the system. A method of well intervention in one area, i.e. water injection to maintain pressure or shutting a well down temporarily, can have impacts on the other wells. The use of technology to gain an understanding of how all the wells are currently operating and inform the decision making on a single well is a significant step forward to ensuring the integrity of the reservoir over production that can span decades.
Furthermore, improved information gathering on a wide scale and applied lessons learned can be used to predict the production of future wells whether within an existing reservoir or a brand new project. This increase in data to support future projects is parallel to a new trend where many companies are more aggressively addressing reservoir concerns by introducing water injection and gas injection into the system during the first stages of the asset life, rather than as a response to production decline.
Additional Steps
Though explicitly not stated in the articles I used for this TOM Challenge, the data being generated and lessons learned needs to be fed back into the safety systems currently used by oil and gas majors. BP, along with most super major/major oil companies have centralized command centers to track the performance of the offshore wells and rigs within a region. As the new data allows for better prediction of production stoppages and issues, it also should and can be sent to the command centers to predict the risk of safety issues. I have friends work on offshore oil rigs and their safety is a significant concern of mine. Having the ability analyze data from the individual wells and generate synthesized reports of the safety concerns for a rig at any given time can fundamentally change how process safety is managed within the industry.
Word Count: 781
Citation
[1] “GE’s Industrial Software to Boost Efficiency Across BP Global Operations.” GE, 5 July 2015. Web. 14 Nov. 2016.
[2]“GE Oil & Gas Launches New Digital Solutions Business, Pilot Program with BP and Partnership with Paradigm.” GE, 28 Jan. 2016. Web. 14 Nov. 2016.
Image: “Conditions and Performance Monitoring.” FMC Technologies, n.d. Web. 14 Nov. 2016.
I see how digitization can help avoid downtown, but in the current economic environment, operators are less concerned about avoiding downtown. Since crude oil prices have crashed, it’s not as expensive for companies to turn off a well for an intervention. The cost of downtime needs to be weighed against the cost of digitization and maintaining that technology, and the results of this comparison shifts with the change in oil price.