Additive Manufacturing in Construction
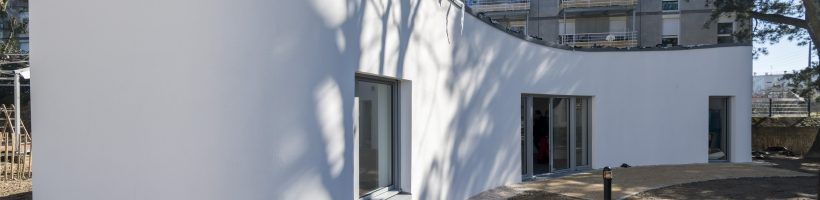
How important will additive manufacturing be in the future of construction? Over the years, additive manufacturing has been a constant topic of discussion in the industry. For the most part, the discussion revolves around trying to understand the limitations, applications and the overall impact on the cost of construction.
Introduction
How important will additive manufacturing be in the future of construction? In a construction site, you face several challenges: lack of consistency between jobs, labor inefficiency, schedule delays, exceeding budget projections, delays on material delivery and high percentage of material waste. I have observed these issues during my experience on job sites and constantly challenged myself to realize creative ways to mitigate these problems. However, 3D printing is promising to extinguish some of these challenges. Over the years, additive manufacturing has been a constant topic of discussion in the industry. For the most part, the discussion revolves around trying to understand the limitations, applications and the overall impact on the cost of construction.
Opportunities and Challenges
3D printing has the potential to revolutionize the industry. Some companies have already started working with this innovation. Bouygues, a French company with global presence is one of those companies. In partnership with Nantes University, they built the first 3D house in Nantes. “Using 3D technology, the 95m² home became a reality in just three days via the arm of a polyarticulated robot: two polyurethane walls with concrete poured between them. This process has a number of advantages, including free-form capabilities and speed of execution. Also, the thermal insulation is already in place at the end of the construction process.” [1]
The advantages of this process do not stop there. It provides consistency between jobs, increases labor efficiency, streamlines the production, provides strength/durability to the building or house, lowers the cost of production, reduces material waste and has the potential to add sustainable materials. [2] The implementation of the additive manufacturing will also change the working environment, reducing the amount of accidents and safety hazards, due to the automation of the process. [3]
Nevertheless, the implementation of 3D printing in the industry also has its disadvantages: high cost of a large-scale printer, the need for a specialist to operate the printer and rough finishes are some of the issues. [2] But most importantly, is the need to further explore and research developments to improve the technology focused in construction. Even though additive manufacturing is being widely used in other industries, the process needs refinement before it really transforms the construction industry. “This field is still in its infancy, without standardized testing and quality control to compare or benchmark these recent advancements. Furthermore, many of these early projects and AM technologies are proprietary, lacking publically available, detailed information on the methodology and final part quality, making comparison or evaluation of new AM technologies more challenging. While much work is needed to fully realize AM as a cost-effective and reliable option in the construction industry, the potential benefits it can provide are worthy of further research and development.” [4]
In 2015, an expansion of The Lewis Grand Hotel in the Philippines was under construction using the new technology. The structure was the first fully permitted structure that would actually be put to use. Yakich, a material science engineer, alongside with Andrey Rudenko, castle 3D printer developer, were responsible for the project. “The Philippines is actually a great place for concrete printing because of the weather. Currently everything is made out of concrete, and it’s a third world country so it can do a lot of good in disaster zones, etc.,” Yakich told 3DPrint.com. The project has about 1,500 square feet and it took approximately 100 hours of print time. [5]
Expansion of The Lewis Grand Hotel in the Philippines [5]
Evolution of the technology
There are a lot of companies today involved with 3D printing. However, since several contractors are still not making use of this technology, most of these companies are active in the construction phase of the value chain; in the short term, it’s more likely that companies will look for integrated solutions – in which they will use inhouse resources for the design, engineering, equipment, software, material, and construction. [3]
In the medium/longer term, as the technology develops and matures, it’s expected that subcontractors specialize in 3D printing and turn the additive manufacturing into a construction technique such as prefab. This would allow more companies to take advantage of the technology, since it would require less capital and local knowledge, expanding the use of 3D printing in construction sites. [3]
Some questions are still unanswered regarding the implications of 3D printing in construction. Will regulations be an obstacle for the advancement of the technology? Will the use of this technology substitute construction workers?
(Word Count: 746)
References
[1] Bouygues Construction, “Innovations”, https://www.bouygues-construction.com/en/innovation/all-innovations/3d-printing, accessed November, 2018
[2] Seyed Hamidreza Ghaffar; Jorge Corker; Mizi Fan, “Additive manufacturing technology and its implementation in construction as an eco-innovative solution” https://www-sciencedirect-com.ezp-prod1.hul.harvard.edu/science/article/pii/S0926580517309731, accessed November, 2018
[3] BCG, “Publications” https://www.bcg.com/en-us/publications/2018/will-3d-printing-remodel-construction-industry.aspx, accessed November, 2018
[4] Daniel Delgado Camacho; Patricia Clayton; William J. O’Brien; Carolyn Seepersad; Maria Juenger; Raissa Ferron; Salvatore Salamone, “Applications of additive manufacturing in the construction industry – A forward-looking review”https://www-sciencedirect-com.ezp-prod1.hul.harvard.edu/science/article/pii/S0926580517307847, accessed November, 2018
[5] 3D Print, “Lewis Grand Hotel Erects World’s First 3D Printed Hotel, Plans to Print Thousands of Homes in the Philippines Next”, https://3dprint.com/94558/3d-printed-hotel-lewis-grand/, accessed November, 2018
This is really interesting. Though some people may push back against AM because it will eliminate human jobs, it can deliver a lot of social benefits as well. Specifically, AM in construction could help solve the affordable housing crisis in the US (https://www.thedailybeast.com/can-3d-printed-homes-solve-the-urban-housing-crisis). Government-backed projects and public works could help get AM construction off the ground and shift public perception around the technology.
I agree that this technology could have big implications for the construction industry. One big challenge the industry is currently facing is labor shortage and increased costs, so this could actually be beneficial if it will reduce the labor required on each job site. Although the technology reduces the construction time, it is still not proven to reduce the costs for a developer. It will be interesting to see if this technology becomes widely adopted but I am concerned about how companies will scale since construction zoning/permits vary by locality.
This is a fascinating article on technology that will likely have a huge impact on the construction industry. Additive manufacturing has the potential to reduce costs in what is a very costly industry, through reduction of labor and material costs. This could have a big effect on housing in underdeveloped areas. I agree that a key question is around regulation, and whether or not it will be an obstacle for the advancement of additive manufacturing in construction. While there may be some concerns around the efficacy and safety of this technology, I believe regulators will approve the use of this technology as they will understand that it would substantially increase housing accessibility.
This is a very thought-provoking article; it almost seems as if the potential applications of additive manufacturing are endless. When it comes to construction, I believe that additive manufacturing may very well become the future of small-scale units such as single-family homes and side projects (new pool, new patio, etc.). Given the sheer scale and engineering required, I do not see additive manufacturing changing the game for skyscrapers or high rises.
As additive manufacturing proliferates, construction jobs will most definitely decrease. I would make the financial analogy of replacing labor expenses with capital expenditures. Therefore, one factor to keep in mind is the pushback from unions and the labor community in general.
A side thought: complex architectural designs often incur very high construction costs. With the help of additive manufacturing, we could also significantly reduce this added cost item.
The construction industry feels like a natural fit for additive technology. However, I’m particularly interested in how additive manufacturing in construction will affect labor. You noted that the automation of the technology can decrease accidents and safety hazards. However, since 3D printers don’t need to eat or sleep, I wonder what impact this will have on labor demand in the industry. While the technology will likely need careful human supervision – at least for the foreseeable future – labor content will decrease. While this may decrease the number of jobs in some geographies, it could address a skills shortage in construction in many high-income countries [1].
[1] [1] de Laubier, Romain. “Will 3D printing remodel the construction industry?” BCG, January 23, 2018.
This technology offers a lot of promise across the construction industry, but I’m curious where it is likely to have an impact first. With the ability to build small structures quickly it seems like a natural fit for affordable housing on the surface, but those developments are made economically feasible by using low cost materials and constructing significant density (a large structure with many small apartments) both of which may not be possible given the restrictions of additive manufacturing. Instead, it will need to be coupled with modular construction processes, where sections of a home (or even full apartments) are built offsite and then assembled to make the final structure, almost like building a Lego set.
Great insights, thank you! I’m really interested to see whether (or how) this technology will overlap with prefabricated home construction. Additive construction offers efficiencies not seen in traditional construction, but how do the economics compare to modular/prefab design like that offered by Blokable (https://blokable.com/solution/)? Both minimize time onsite, but I imagine the process for integrating infrastructure like wiring and plumbing is quite different.
I think the implications for AM in construction are very interesting, but may be difficult in practice. Construction projects are still largely technologically unsophisticated — many construction managers still struggle to use technology for project management or inventory planning. For example, on most work sites engineers are still more comfortable carrying around sketches of blueprints then iPads or computers with the plans on them. I think it might take a bit of time to get buy in from all of the constituents.
For this reason, I wonder if your first target should be architects. They are typically already comfortable with using technology to develop designs, and have the creativity to fully utilize the power of AM. Could they be the first logical user?
This is a very interesting topic and I believe that the new 3D printing technology will replace some human workers in the construction sector because of its efficiency and productivity. The author mentioned that in the medium to long term, the new 3D printing technology becomes more economical and available for small construction firms. However, I suspect that large construction firms will soon buy the cutting-edge 3D printing technology and internally research and improve the technology further by spending a lot of capital that smaller competitors don’t have. As a result, I am a little worried that monopoly in the construction industry will intensify because the smaller companies without enough capital to compete against the latest 3D printing technology will lose relative competitiveness against the larger peers. I would like to know what the author thinks about this potential competitive dynamics in the construction industry.
I believe this article addresses an important technology that can be used to revolutionize the housing industry in many areas of the world, most specifically ones that are impacted by disaster and those in areas of poverty. In considering the concern that regulations will be an obstacles. I only believe that this will be relevant in the developed world, where the need for this type of housing is less relevant, therefore I don’t think this will be a significant challenge. When it comes to the substitution of construction workers, this will likely happen, however the trade-off is that instead of having families wait months or years for safe housing they now only have to wait hours. Therefore when considering Maslow’s Heirachy of needs and the importance of food and shelter, in this type of situation I think the public good far outweighs the potential jobs lost.
Large-scale 3D printing represents an excellent opportunity to create affordable housing options in a short amount of time. I’ve read about 3D printed houses providing temporary relief post natural disasters. I do wonder, however, whether quality and longevity will become problematic in the long-term. How will repairs and updates be made to these homes? Will the 3D printer need to remain in the local area in case the need for replacement walls arises?
While some might be concerned about job replacement within the construction industry, a significant portion of construction jobs are quite risky. Deploying 3D printing could reduce construction-related injuries and even create jobs in supporting roles.
Also, 3D printing allows the construction industry, typically very conservative with respect to innovate, to be on the cutting edge of technological advancement. [1] These advances could help boost productivity across all stages of the design process through a digitization of the entire process.
[1] “Will 3D Printing Remodel the Construction Industry?” https://Www.bcg.com, http://www.bcg.com/en-us/publications/2018/will-3d-printing-remodel-construction-industry.aspx.
Wow, 3 days to build a house is very impressive! And it also looks nice!
One important concern that I have is regarding the safety of the actual building. Are structures created through 3D printings structurally sound? Also, how can we handle structures in areas where we need good foundations, or in earthquake-prone areas? This, in combination to the open points that you mention (e.g. rough ages, quality issues, high cost of the 3D printer) make me believe that we are far away from the wide adoption of 3D printing in construction.
Nevertheless, being a civil engineer myself, I am convinced that it is the future, especially for non-residential buildings. If the problems of safety, cost and quality are resolved, the construction industry will focus more on the trend. And if that happens, regulations will adapt overtime. Don’t forget that regulation always lags behind innovation!
I would be interested in more information on the cost and speed of additive manufacturing. At first glance, construction seems like an excellent application of additive manufacturing and this technology should be scaled around the world. In addition to the social benefits that @Nathaniel described above, this technology could radically transform cities by potentially reducing the amount of time and money spent on construction projects. If we could apply this to housing and transportation projects, we could more rapidly address the homelessness and mobility challenges facing our cities.
In response to the questions you raised, I agree that this technology poses the risk of ultimately reducing the number of construction jobs available. However, in the short term, I believe that this technology can help grow the overall construction industry, due to the quantity of construction work currently needed around the world.
Great article. I think AM is the future of manufacturing. What concerns me is the substitution of automation for construction workers. In developing countries like the Philippines, construction provides a crucial outlet for many citizens to make a living. I’d like to see how the human element plays in the construction of these printed homes. Are people serving merely as a quality control supervisor or does the equipment require multiple operators. I think the challenge with technology is not only making things easier for society, but also creating value by diverting the work force to larger issues in need. Perhaps the adoption of AM can push more employees into the related fields of architecture or city planning?
Most folks in the dialogue thus far have commented on the impact of additive manufacturing in construction on labor and construction jobs — however, I’m most curious about the long-term impact on city development. For example, given the large capital investment in generating the 3D printer, laser cutter, and underlying model design relative to the much lower variable cost of producing each incremental new 3D home, I imagine the effect on cities is mass uniformity in how people live in homes. In particular, there will likely be an increase in more standardized floor layouts, blueprints, and design. Another impact is that home-buying will become more of an “equalized” process, and more accessible across socioeconomic factors, as costs of home-building and buying are reduced due to automation and reduced waste. As a result, in the long run, rather than home-owning being a ‘milestone’ in individuals’ lives, it may become a more transactional, mundane part of daily human life.
This article is a great overview of the development and possible implications of 3D printing in construction. To your questions, I think it’s fair to always anticipate some regulatory pushback at the start. That sad, unlike automated vehicles where there is a clear likelihood — and recently, realization of the risk of death to consumers, that seems less likely here (though of course still possible during construction or if construction is shoddy, later on). Nonetheless, I’m very optimistic the regulatory environment would prove very favorable, especially given this technology has the potential to bring tons of manufacturing jobs back to the developed world. While some jobs, as you write, might be lost to machines, many will be won back from the developing world. I think this will mitigate some of the concern other commenters above expressed about pushback from unions (and, quite frankly, for better or worse, unions have the least influence they’ve ever had in this country).
Thanks for sharing! It’s really interesting and great to see that 3D printing in manufacturing can be particularly helpful “disaster zones.”
Although the regulatory process for approval in each new locality could be slow, the technology definitely shows a lot of promise. In the mean time, I wonder how often 3D printing is being leveraged in construction for modeling purposes. Especially in non-residential development, I would expect 3D printing would be a great way to model and iterate different architectural designs.