Shell: “printing” your oil
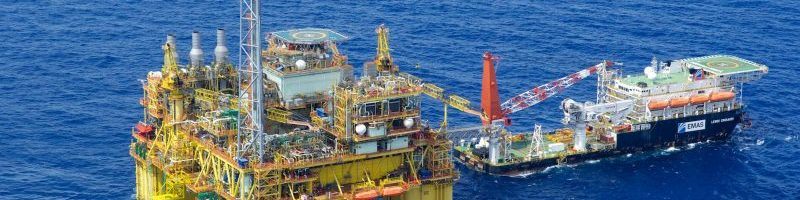
How technological innovations such as 3D printing can help oil and gas industry to adapt to a new low oil price environment
Innovative/disruptive technologies in oil & gas industry
The oil crisis of 2014 when oil price dropped from $115/barrel in June 2014 to $46/barrel in January 2015 and then to $28/barrel in January 2016 [1], caused a huge financial impact on oil & gas (O&G) companies. Most O&G companies reacted by shutting down uneconomic projects and making people redundant to minimize costs. Once O&G community realized that oil price will stay “lower for longer”, companies started investing in the digital transformation to reduce costs in long-term. According to The Digital Transformation Initiative report from 2017 World Economic Forum [2], O&G companies started investing in a wide range of innovative digital technologies:
Why 3D printing?
Among many disruptive technologies that just started penetrating O&G industry, the 3D printing revolution stands out by transforming traditional obsolete & non-flexible global O&G supply chain into a local and agile supply chain. It provides an opportunity to shift manufacturing closer to the customer and build interactive relationships between manufacturer and customer.
3D printing technology provides solutions to many challenges industry has been facing for years. Some examples include:
- Optimization of supply chain operations: change manufacturing location, reduce inventory costs, minimize delivery lead times, reduce costly downtime, enable on-demand/on-site production of replacement parts.
- Prototyping of major construction projects would significantly reduce time to develop an accurate design.
- The environmental benefit is the reduction of 2 million tons in CO2 emissions.
Shell’s 3D printing experience and short/mid-term objectives
Several O&G companies began to adopt 3D printing technology:
- GE Oil & Gas reduced the development cycle of a NovaLT™16 gas turbine by 50% by printing 3D prototype [4], [5]
- BP added 3D printing to disruptive forces considered in long-term forecasting [6].
But the most remarkable example of the application of innovative 3D technology was shown by Shell that used 3D printers to prototype the deepest drilling station in the world – Stones project in the Gulf of Mexico. The team produced a scaled-down 3D plastic version of the platform including every minor detail in just 4 weeks. The prototype helped to improve components before building the real-life buoy in the construction yard and optimize assembly sequence for the buoy. [3]
Shell accelerated project timeline and also saved $40 million by highlighting design flaws at an early stage. The prototype was also used to demonstrate to the US authorities how platform would operate in the rough sea environment. It helped to speed up government approval decision. The video below provides a brief overview of the project.
YouTube video: 3D printing at Shell
Shell’s success in the Stone project demonstrated the company is well positioned to take competitive advantage of this disruptive technology going forward. 3D printing offers great value by significantly reducing the time required for prototyping, producing, reworking and redesigning components of complex projects. Shell is on the right track to fully develop and utilize 3D printing technology in the near term ahead of many competitors. In the mid-term, however, the biggest challenge is to transition from a small plastic prototypes to small metal products and eventually to large metal products. Shell continues investing in R&D to solve this challenge.
Recommendations to Shell
One of the major concerns regarding adopting 3D printing technology in the O&G industry is safety liability for potential failures of the printed equipment. Big operating companies (like Shell) would much prefer to hedge their risks and get a warranty from a third-party 3D printing company. Another concern is that 3D printing often requires special raw printing materials that O&G companies might not have. In addition to that, O&G companies need to manage the intellectual property issues associated with 3D printing. Intellectual properties and patents will restrict the ability of O&G companies to print certain type of the equipment.
The above-mentioned concerns lead to a recommendation for O&G companies to work closely with 3D printing contractors. While O&G companies have significant resources to invest in R&D and build in-house 3D printing capability, they need to ensure that independent service providers are also developing and following the new trend.
Final considerations
In the long term, 3D printing is positioned to play a key role within the O&G supply chain by transforming how components of a wide range of equipment are produced and delivered. 3D printing technology will create significant value, particularly in locations where the supply of replacement parts is limited, or where shipping and customs clearance are likely to cause time delays.
But how do we know that 3D printing technology is reliable in the O&G context? Shell had success with the Stones project. Is that enough? When do we know that 3D printing technology is reliable enough to be used at the industry-wide scale for multi-billion construction projects that could impose significant environmental and safety risks?
(Word count: 795 words)
References
[1]”Brent Crude Oil Prices – 10 Year Daily Chart”, Macrotrends – The Premier Research Platform for Long Term Investors, accessed 10 November 2016, http://www.macrotrends.net/2480/brent-crude-oil-prices-10-year-daily-chart
[2] “Digital Transformation Initiative: Oil and Gas Industry”, White Paper, World Economic Forum, January 2017, http://reports.weforum.org/digital-transformation/wp-content/blogs.dir/94/mp/files/pages/files/dti-oil-and-gas-industry-white-paper.pdf
[3] “Grand designs: how 3D printing could change our world”, Shell website, accessed 10 November 2016, http://www.shell.com/inside-energy/how-3d-printing-is-changing-the-world.html
[4] “GE’s co-creation process opens new doors to true value”, GE Oil & gas website, accessed 10 November 2016, https://www.geoilandgas.com/case-study/ges-co-creation-process-opens-new-doors-true-value
[5] “Oil rigs set to see 3D printing soon”, Magazine of the National Society of Professional Engineer, October 2015, Vol. 28 Issue 10, p7.
[6] “BP to study impact of 3D printing on growth of oil industry”, Financial Times, January 2017, https://www.ft.com/content/6ef4bda6-e3d5-11e6-8405-9e5580d6e5fb
As you mentioned, shell is an operating company that has no experience in constructing oil rigs. coming from oil&gas myself, I can say that this industry, especially when it comes to the operations side of it, is extremely risky and people’s lives are on the line every day. hence, while I admire the digitization initiative, cost cutting had previously led to disastrous outcomes, most notably the Deepwater horizon oil spill in the Gulf of Mexico, and that did not include any innovation or creative initiatives. in terms of the product itself my concern would be that the initial production was performed under lab conditions and not real-life conditions, secondly, even if it was taken out on the field, there are so many drilling conditions that the buoy can face which the 3D printed part did not take into consideration, or at least it was not clear to me, such as the depth, speed, and pressure of the well or field. I think when peoples lives are on the line digitization should be slowly implemented with rigorous testing.
Pretty informative article. I wasn’t aware of how operators are utilizing 3d printing technology to their advantage. Services companies, such as Halliburton looked at the technology a couple of years back but I haven’t seen much progress. Why do you think the service companies have failed to go mass scale with 3D printing? Could it be because of push back from operators? Maybe Deepwater Horizon incident has significantly reduced any operators appetite for innovative technologies?
https://www.reuters.com/article/ge-3dprinting/oil-industry-joins-world-of-3d-printing-idUSL5N0KW2OA20140123
It’s good to see that O&G companies are finally taking advantage of novel prototyping methods to rapid prototype their designs, but I agree that the most interesting challenges ahead are in seeing if 3D printing can be used in the actual manufacturing of O&G components. I see the sheer size of many of the parts, like the huge buoys for the rigs, as a major manufacturing challenge moving forward. 3D printing will certainly help with design, but it has to be properly incorporated into the design process in order to ensure the engineers are actually using the new technology as a means of answering questions earlier, rather than just as a shiny new toy.
Fascinating article, Konstantin! Indeed, 3D could be seen as a huge benefit for companies operating in remote parts of the world with long lead times and expensive shipping costs (in Chukotka it the lead time was +13 months by ship to Pevek). As you touched on, liability for replacement goods “printed” may be a concern. This may void the warrant on complex pieces of machinery, for example (i.e. print a coupling for the drill and the drill is no longer under warranty). Also a lot of safety equipment is rigorously tested and certified which may protect the company in the event of an incident. Using safety equipment (i.e. supports) that are not “stamped” and certified may pose a liability to the oil and gas company. Nonetheless, having this technology on a remote oil and gas platform or somewhere else remote will be a huge benefit one day!