Daimler Trucks: Print Spare Parts Today, Print Trucks Tomorrow
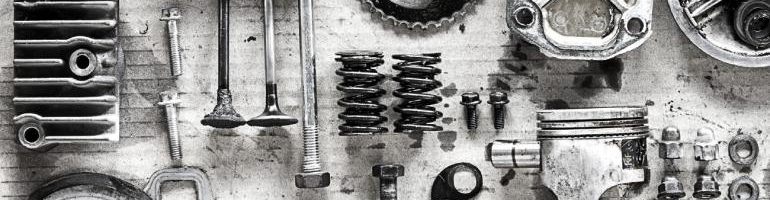
Daimler Trucks rolled out on-demand 3D-printed spare parts service as a first step towards its long-term ambition to print trucks in the full-scale manufacturing process. What are the benefits and risks of 3D printing?
Daimler Trucks is the world’s largest truck manufacturer. Like many other automotive producers, it applied 3D printing – the process of producing three-dimensional projects directly from digital designs through additive layering of material – to develop prototypes in a faster, cheaper and more flexible manner during the early days of the technology[1]. However, as affordability and reliability of the technology improved, Daimler began to explore the applicability of 3D printing in its wider supply chain.
In September 2016, Daimler Trucks started to offer on-demand 3D-printed plastic spare parts as part of its after-sale production process[2]. This experimentation with 3D printing was likely motivated by the potential to enhance both customer experience and product economics and the pressure to stay ahead of competition.
Customer satisfaction in the spare parts business depends highly on the availability of the parts ordered, no matter how old the truck models are, and the lead time to delivery. Traditional manufacturing requires warehouses to carry a large assortment of parts to ensure high level of customer services, with complex logistical handling to optimize the balance between inventory carry costs and delivery time. 3D printing, on the other hand, greatly simplifies the supply chain[3]. Each vehicle service centre could store unlimited number of inventory virtually in the form of digital files at very low cost and print individual parts upon customer orders. Printing could be decentralized and done in the facilities closest to the customer to minimize delivery time. 3D printing also greatly reduces waste compared to CNC milling and eliminates the scale economy, making production of one customized part as cost-efficient as production of one hundred standardized parts[4]. This further enhances Daimler’s ability to offer differentiated and customized products with competitive after-sale services.
Daimler is not alone in recognizing the huge potential of 3D printing, as many automotive producers actively integrate 3D printing into its supply chain beyond prototyping. For instance, its competitor, Audi, also began printing car components in 2016[5]. To stay ahead of competition, Daimler needs to continue investing in the technology to accumulate relevant experience and ramp up the learning curve of managing supply chain integrated with 3D printing.
In the short term, Daimler plans to continue rolling out on-demand 3D-printed spare parts service by expanding the number of parts printable and number of markets covered. For instance, Daimler began to offer printed metallic spare parts in August 2017 in addition to the plastic spare parts offered the year before[6].
In the long term, Daimler aspires to integrate 3D printing, also known as additive manufacturing, into its large-scale manufacturing process. In May 2017, Daimler partnered with Premium AEROTEC, a subsidiary of Airbus Group, and EOS, an industrial 3D printing solution provider, to launch the NextGenAM project[7]. Leveraging expertise of its partners, the project marked an ambitious effort to systematically design and commercialize the full additive manufacturing process, including processes that occur before and after printing which can account for up to 70% of overall production cost.
As Daimler ventures into the realm of 3D printing, I would recommend the management to concurrently upgrade its software infrastructure and quality control process to support the new requirements of its supply chain. To the extent that both traditional and 3D-printing-enabled supply chains will co-exist in the short term, software programs that provide features such as real-time cost comparison between manufacturing and 3D printing alternatives on each customer order and timely alignment of 3D printable parts catalogue with new product launches could help ensure the efficient and seamless interaction between both supply chains. In addition, as spare parts are now printed in decentralized facilities, stringent quality control procedures need to be designed and enforced to ensure quality of each individual part printed[8].
In the long term, as a large part of production process migrates towards additive manufacturing, Daimler should be keenly aware of cyber-security related risks inherent in this decentralized and networked manufacturing process and invest in relevant safeguards accordingly. One such risk is intellectual property (IP) theft, as all products will be stored in the form of digital files and shared in a decentralized manner across manufacturing sites. Another risk could pertain to hacking and corruption of the digital files transmitted in the company network[9]. An altered digital file undetected could cause fatal product failures, including threat to driver safety in the case of a truck.
Overall, 3D printing seems to present a greater opportunity than threat to the automotive industry as it shows promises of saving significant cost, enabling complex innovation and enhancing customer experiences. However, can it become a source of sustainable competitive advantage for Daimler, or just an efficiency enhancement initiative required to stay relevant?
(Word Count: 778)
[1] Bentur, A., “The Fast Lane: Additive Manufacturing in the Automotive Industry,” LEO Lane (Mar. 22, 2017)
[2] Taylor, E. and Cremer, A., “Daimler Trucks to use 3D printing in spare parts production,” Reuters (Jul. 13, 2016)
[3] “3D printing and the future of supply chains,” DHL Trend Research (Nov. 2016)
[4] Bogers, M, Hadar, R, and Bilberg, A. “Additive manufacturing for consumer-centric business models: Implications for supply chains in consumer goods manufacturing,” Technological Forecasting and Social Change, vol. 102 (2016), pp. 225-239
[5] “Audi invests in 3D printing,” Materials Today (Sep. 13, 2016)
[6] Press Release, “Premiere at Mercedes-Benz Trucks: New from the 3D printer: the first spare part for trucks made of metal,” Daimler (Aug. 12, 2017)
[7] Press Release, “Premium AEROTEC, EOS and Daimler prepare the next generation of industrial 3D printing,” Premium AEROTEC (Apr. 19, 2017)
[8] “3D Printing: The Next Revolution in Industrial Manufacturing,” UPS and the Consumer Technology Association (2016)
[9] Biggs, J., “Researchers sabotage 3D printer files to destroy a drone,” TechCrunch (Oct. 21, 2016)
3D printing is a fascinating topic for the manufacturing world and is a great current case study in the adoption of an innovative new technology in an otherwise very traditional and old-fashioned industry. In particular, I think the adoption will go through a series of different phases, with each phase being characterized by increasing presence of 3D printing. As you mentioned in the write-up, it started with the ability for rapid prototyping and eventually Daimler went on to start using 3D printing for parts. However, I’d argue that this is still very much in the dabbling phase, as you’re simply replacing a traditional manufacturing process with a new one ONLY at the last step – the actual manufacturing.
One of the main advantages of additive manufacturing is that you can actually completely redesign how you create products from the very beginning – the design phase. Currently, car manufacturers assemble a ton of parts together (millions?), as they’ve found it to be the most efficient way of doing so. However, additive manufacturing will enable them to design the car with far fewer parts, as incredibly odd shapes that used to take multiple parts and many bridging parts (e.g., screws) can now be printed as a single part. This reduction in number of parts will also hopefully lead to increased quality, as fewer moving parts means that fewer things can go wrong. Do you know if Daimler or any other auto manufacturer has started looked at redesigning their processes by fundamentally integrating 3D printing?
Really interesting article. Chloe. When 3D printing was first introduced to the market, the technology was prohibitively expensive for many industrial applications. My previous company used a 3D printer only for prototypes of our power inverters due to the high cost of running the printer. 3D printing makes a lot of sense for prototype production due to the high avoided cost of contracting a traditional offsite manufacturer to make a one-off part, which itself was being iterated and changed very quickly. I’d be interested to see how prices of industrial 3D printing have decreased over time and the forecasted prices. The speed of innovation here will inform the extent of investments that companies will make to integrate this new technology into their manufacturing process. Also, to build on Jon’s comment: I wonder if there are limitations to the redesign process to enable 3D printing. Are there quality losses due to the design changes that need to be made to accommodate manufacturing parts in this way?