Could Additive Manufacturing (3D-Printing) Be the Answer to Boeing’s Program Accounting Woes?
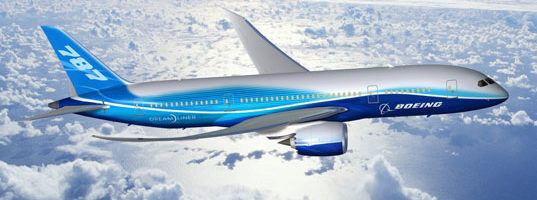
Boeing has committed to investing in and expanding its use of additive manufacturing, helping to improve upon the company's complex production of select commercial jet parts. But the company will need to continue to push the limits of 3D-printing if there is a broader future for this technology to more meaningfully control manufacturing costs and efficiency for their Dreamliner and future jet models.
Many of us are all too familiar with Boeing’s use of program accounting and commitment to decrease costs of producing commercial jets over time. Additive manufacturing (“AM”, “3D-printing”), might be one way to help deliver efficiencies needed to reach the ~$40m projected program accounting cost per plane (vs. their current $265m) [1, 2].
AM uses computer-aided design to take digital images that can be used by professional-grade printing machines to manufacture parts through adding materials layer-by-layer vs. traditional manufacturing subtraction – as a result, this can decrease costs, while increasing efficiencies in several ways [3]. First, AM allows developers to test, iterate, and build more effectively by not constraining production to molds and producing complex three-dimensional items with any geometry [1]. Second, AM enables producers to combine separate parts into single units – for example, through it’s use of AM, GE reduced the number of parts required for fuel nozzles from 18 to 1, decreasing assembly costs and improving the manufacturing process [2]. Last, by manufacturing through “additive means” rather than “subtracting”, companies can eliminate material waste, further decreasing costs [1]. In one use of AM by Boeing, the company reduced the use of titanium by $2-$3m per plane or ~15% [2]. In an industry that produces parts in small quantities, requiring them to be lightweight, strong, and geometrically complex, AM has significant potential for Boeing to produce parts that improve the performance of their jets and reduces costs in the process [3].
Although in many ways AM would seem to be too good to be true, it has its drawbacks. Aside from the upfront costs of the machines, AM is limited by the types and sizes of parts that can be produced, as well as the speed at which they can be produced (e.g. AM can produce ~1.5 inch cube / hour vs. multiple of the same size / minute for injection molding) [3]. Even more, AM requires incredibly precise specifications across a vast number of parameters including materials (sizes, purities), designs (geometry), layouts (part orientation, proximity), processes (applied energy, inert atmosphere), and post-processes (heat treatment, surface smoothing) [4].
Despite these constraints, Boeing is already benefiting from AM and has demonstrated its commitment to the process by operating 20 sites using 3D-printing and producing over 50,000 installed 3D-printed parts to date across its programs [5]. This commitment has been demonstrated by both short- and long-term investments in AM technologies. Boeing has already focused on collecting data necessary to drive AM processes and, in 2017 adopted Dassault Systemes’ 3DEXPERIENCE across its organization to consolidate data and determine ideal parts to produce through AM, create those processes, and improve all aspects of production [4]. Further, in 2016 Boeing partnered with Stratasys Ltd. [6] and in 2017 signed a 5-year partnership with Oerlilken, to further expand AM to aerospace, advance the printing process, reduce complexities, and provide higher quality prints [7]. Boeing is also thinking ahead to how it can protect the digital data it uses for 3D-printing, and in May 2018 signed an agreement with Assembrix to secure its inventory of 3D-printable parts [8]. In August 2018, Boeing invested in Digital Alloys, a company working to develop high-speed, multi-metal AM systems, and Boeing believes that investments such as these will enable them to produce parts faster and in higher volume than ever before [9].
In addition to these efforts, I think Boeing should take a fresh look internally at their current manufacturing processes, especially regarding commercial jets. Within Boeing Space and Missile Systems, although AM alone did not offer advantages, the team was able to use AM alongside new materials to create a lighter-weight and lower-cost part for one of their spacecraft [10] – similarly, within the commercial jet division, teams should look for ways to combine processes and materials with AM to produce new parts at lower costs. Boeing should also be continually expanding its use of AM, even just in testing, in order to collect more of the data necessary to power future decisions to use AM for specific parts and ultimately design production specifications [4]. Last, given the airline industry is highly regulated, Boeing should simultaneously focus externally to ensure they make progress on FAA approval for their AM processes and parts – the company will need to demonstrate consistent and repeatable processes, which should start now [4, 7].
As Boeing continues to adopt and invest in AM, improving costs and production across one of the most complicated pieces of manufactured equipment (airplanes), the question remains whether the upfront cost and time will ever be fully compensated by the savings or product improvements? Even more, if AM is eventually worthwhile for each individual part, could we reach a state where most components of an airplane are produced using AM or could an airplane become close to one part itself?
(796 words)
[1] Heese, J., Srinivasan, S., Lane, D., & Barnett, J. (2017). Accounting Turbulence at Boeing. Harvard Business School, 1. Acccessed November 7, 2018.
[2] Boeing Saves Millions in Manufacturing Costs with Titanium 3D Printing. (2017). Protolabs. Accessed November 7, 2018, from https://www.protolabs.com/resources/blog/boeing-saves-millions-in-manufacturing-costs-with-titanium-3d-printing/.
[3] Ford, S. L. (2014). Additive Manufacturing Technology: Potential Implications for U.S. Manufacturing Competitiveness. Journal of International Commerce and Economics. Accessed November 7, 2018, from https://65.121.221.243/publications/332/journals/vol_vi_article4_additive_manufacturing_technology.pdf.
[4] Alba, M. (2018). Are 3D-printed Planes Coming to a Sky Near You? Engineering.com. Accessed November 7, 2018, from https://www.engineering.com/DesignSoftware/DesignSoftwareArticles/ArticleID/16848/Are-3D-printed-Planes-Coming-to-a-Sky-Near-You.aspx.
[5] Boeing, 2017 Annual Report, p. 8, Boeing Investor Relations. Accessed November, 7 2018 from http://s2.q4cdn.com/661678649/files/doc_financials/annual/2017/2017-Annual-Report.pdf.
[6] Stratasys Builds 3D Printing Partnership with Boeing & Ford. (2016). Zacks Equity Research. Accessed November 7, 2018, from https://www.nasdaq.com/article/stratasys-builds-3d-printing-partnership-with-boeing-ford-cm670665.
[7] Szondy, D. (2018). Boeing and Oerlikon Team Up to Advance 3D Printing of Titanium Aerospace Components. New Atlas. Accessed November 7, 2018, from https://newatlas.com/boeing-oerlikon-titanium-3d-printing/53488/.
[8] Jackson, B. (2018). Boeing Collaborates With Assembrix to Secure 3D Printing. 3D Printing Industry. Accessed November 7, 2018, from https://3dprintingindustry.com/news/boeing-collaborate-assembrix-secure-3d-printing-133379/.
[9] Catalani, V. (2018). Boeing HorizonX Ventures Invests in High-Speed Metal 3D Printing Company Digital Alloys. Boeing Press Release. Accessed November 7, 2018, from http://investors.boeing.com/default.aspx?SectionId=5cc5ecae-6c48-4521-a1ad-480e593e4835&LanguageId=1&PressReleaseId=a05ac66c-bf19-4fc0-9812-0813e9428b08.
[10] Aston, R. (2017). 3D Printing Done Right. Boeing Innovation Quarterly. Accessed November 7, 2018, from https://www.boeing.com/features/innovation-quarterly/nov2017/feature-thought-leadership-3d-printing.page.
I think there will be push-back to 3D printed plane parts from commercial airline customers. It seems like a less reliable manufacturing method to those who don’t know enough about it. I came across this article from 2017 about how the aerospace industry is advocating for FAA approval of AM (https://spacenews.com/faa-prepares-guidance-for-wave-of-3d-printed-aerospace-parts/). It would be interesting to see Boeing partner with military and space-related organizations to champion AM and increase confidence among customers.
This is awesome! I disagree with the comment above. I think this will ultimately be the way of the future, and I don’t believe customers will notice. We are already 3D printing shoes, homes are in the works, airplanes is a logical next step. I don’t think most customers will even be privy to the means of manufacture of these planes. It will be smooth sailing in the friendly skies.
Very cool to think about the future of AM within the aerospace industry. While I would want to get certain AM processes safety-approved for more critical components of the plane, I agree that this is a strong contender for the future of airplane manufacturing. I think the biggest concern is that the technology does not exist to create large parts all at once, so I would want to see airline manufacturers to start investing heavily in AM process development before I’d buy into the idea that it will take over the traditional manufacturing process.
I can definitely see AM becoming a game changer in aerospace manufacturing, but I believe that the scope of disruption will be limited. Firstly, from a financial perspective, companies such as Boeing have undergone incredibly high capital expenditures to establish their current manufacturing processes. Cost savings and additional benefits must reach very high levels before the switch can be justified. Secondly, certain parts of the plane such as the hull or engines (Rolls Royce is the market leader here) cannot be readily produced using AM due to size, complexity, etc. (at least not yet). These are definitely obstacles that can be overcome, however, especially if AM technology continues to improve.
Even though the airline industry is getting closer to developing 3-D printing of metal pieces for plane manufacturing[1], I still think the regulatory environment will be a main detractor of this trend from becoming widespread in the world. The FAA says the industry is getting closer to manufacturing and approving the use of 3-D printed parts for critical components in the plane [2] but I remain skeptic on how long it will the rest of the world to understand this technology, the specifications of the parts and its maintenance, repair and overhaul. I also believe that (much like self-driving cars) this technology will be held to a more strict quality standard than what is currently in place proving very risky for plane manufacturers and their relationships with clients.
[1] McBride, Stephen. 2018. “If You’ve Missed The Iphone Revolution, This Device Is Your Second Chance”. Forbes. https://www.forbes.com/sites/stephenmcbride1/2018/10/31/if-youve-missed-the-iphone-revolution-this-device-is-your-second-chance/#4f692346584f.
[2] Werner, Debra. 2018. “FAA Prepares Guidance For Wave Of 3D-Printed Aerospace Parts – Spacenews.Com”. Spacenews.Com. https://spacenews.com/faa-prepares-guidance-for-wave-of-3d-printed-aerospace-parts/.
Awesome post – thanks for sharing! I fully agree that an investment in additive manufacturing can be a way to solve Boeing’s program accounting woes. Airplane parts can be produced much more quickly and cheaply, enabling the company to start testing planes and incorporating learnings way sooner. This effectively shortens the new product development cycle and brings down the cost of the project – the potential benefits are huge.
On your second question, however, I also agree with the comments above. I think we are pretty far away from a world where airplanes are produced fully through 3-D printing given the FAA / the regulatory environment and low awareness of customers.
Thanks for the interesting read. I believe there will be an upper limit on the types of parts that can be manufactured by AM in aviation in the medium term. Some parts used in aviation have to be precision engineered to adhere to very strict technical tolerances. There is also a limitation on the type of materials that can used in AM. I would imagine stretched-skin type designs that we see in aircraft today will feature some sort of heat-resistance coating (titanium alloy?). Any part failures could have catastrophic consequences. Thus, I think the industry will forward cautiously with adopting AM for may of the key aircraft parts.
Great piece. Absolutely, regulation on airplane manufacturing would be an important consideration/potential roadblock to implementing this AM program at a large scale in Boeing and other airplane manufacturers. Specifically, although AM provides methods of producing lighter weight and cheaper parts, it begs the question of what has to be given up in quality (if any)? Testing the durability of AM produced parts against traditionally made ones, and showing equal or even greater performance will be key to getting buy-in/confidence from regulators..and even passengers like me!
I see quality standards and FAA control as key challenges to overcome. As we learned in class, with new disruptive technologies, we tend to hold 0% defect or failure rate as our mental standard, when rationally the quality standard should just be higher than what we have today. If an airplane accident happens, and it was revealed that many of its parts were manufactured through 3D printing, that could hinder the overall progress significantly even if it wasn’t at fault.
Secondly, due to the size and complexity of airplanes, I don’t see a full plane being produced through additive manufacturing in the near future. The value is much more likely from parts, service parts, etc.
Excerpt from the New York TOMs review:
With his typical flair for the audacious and avant-garde, Mr. Hughes imagines a world in which an airplane consists of a single 3D-printed part. Fascinating though this proposal is, it is a shame that Mr. Hughes does not go farther towards answering his own question with an investigation of how printing costs vary with the size of the equipment. Is it sublinear, linear, or perhaps even exponential? Knowing the answer to this question as well as its history and trends would inform the discussion of how AM at Boeing is likely to proceed. However, Mr. Hughes’ recommendation that Boeing expand its AM testing across the company, progressing towards FAA approval in the process, is highly sensible and will likely surface more of the information needed to understand the shape of technological progression. Towards this end, the investment in Digital Alloys’ multi-metal systems is the most exciting of Boeing’s recent partnerships, and an investigation of Digital’s own progression may allow the author to extrapolate towards Boeing’s likely progress in the next 5-10 years.
AM is the future of manufacturing. This technology needs players like Boeing to heavily invest upfront to drive costs down in the future. What concerns me is the quality control processes that need to be implemented to usher this new age of manufacturing. The future of manufacturing unions need also be considered. How will the human element drive or inhibit the acceleration of AM? Aviation may also pose safety concerns that would change the credibility of AM for years to come. Perhaps big industry can instead build AM’s capability my investing in printed unmanned rockets to secure public confidence?
Great post. In response to the questions you posed, I think Boeing needs to consider two additional factors when deciding whether to further invest in AM and where to invest (what parts/components). One is the value of maintaining a stable inventory and minimizing supply disruption. For example, if Boeing is able to use AM to manufacture parts that are currently experiencing shortage issues on a frequent basis, there is value in investing in AM, even if direct cost-benefit analysis does not support investment. Minimizing supply disruption and expediting plane production is a worthy goal that needs to be prioritized. Second, on the flip side, leveraging AM means that Boeing will in-source production of parts that it currently procures from other vendors. This vertical integration will subject Boeing to additional risks (such as fluctuation in raw material prices) and requires expansion of capabilities (such as additional purchasing and inventory management) — potentially making Boeing’s earnings more cyclical and making Boeing harder to value (do investors value it as an airplane producer or a 3D manufacturer? What valuation multiple should be used?). I think Boeing needs to carefully consider how this will translate to the investor community and impact the company’s valuation before committing to the act.