Building a Better Future – 3D Printed Housing at WinSun
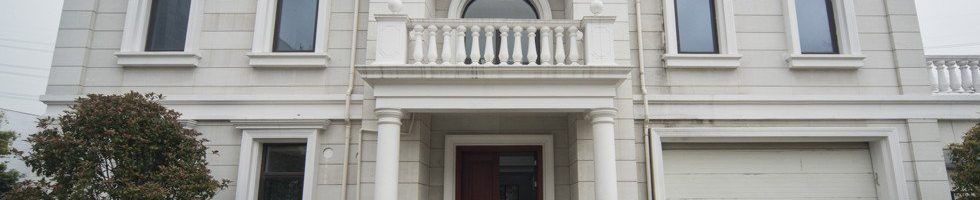
WinSun is using 3D printing in construction to lower costs and timelines while protecting against pollution and corruption
In 2008, Shanghai WinSun Decoration Design Engineering Company became the first company to create a building using a 3D printer. It later gained attention in 2014 for printing ten homes in 24 hours, and for 3D printing its own production plant building. Located in the Jiangsu province of China, WinSun is using additive manufacturing to gain an edge against traditional construction companies in China and abroad [1].
WinSun’s current additive manufacturing process varies greatly from traditional subtractive manufacturing construction. Instead of manually sizing and assembling raw materials into a frame at the job site, WinSun uses its 492ft long 3D printer to build concrete-like structures, which are then shipped from its Suzhou Industrial Park plant to the job site. The printer builds structures using a spray nozzle to layer “ink”, concrete-like composites created using 100% recycled materials, into digitally designed structures such as building walls. The inks are even claimed to have improved properties over concrete, including better resistance against seismic and wind activity.
While some argue that the gray layered-concrete design is not very visually appealing, the benefits to the construction process, both from a financial and time perspective, seem very attractive. Compared to traditional construction of buildings, the WinSun construction process uses 30-60% less new raw material, saves 50-70% in construction time, saves 50-80% in labor, and is 50% cheaper (HK$30,000 for a 645sqft home in 2014). In addition to these benefits, there are some improvements to the construction process that have an out sized impact in China specifically.
3D printed buildings address two key issues faced in the Chinese construction process: pollution and corruption. Various government mandates have been put in place to address the air pollution problems in China [2] which WinSun addresses by building off-site, which reduces dust and other pollution in the job sites in cities. Aligning to policy should make it faster to go through the approvals part of the construction process. In regards to corruption, construction is among the industries with the highest incidence rates in China – roughly 40% [3]. WinSun offers a defined set of prototypes, has very few intermediaries, and provides an upfront price for each building which differs from traditional construction’s inability to compare projects, changing budgets, and multiple stakeholders. This protects WinSun from costly bribes and time-delaying stakeholder roadblocks.
WinSun’s short and long term plans appear to focus on foreign markets and new product development. WinSun has been in talks with the Saudi Arabian government to potentially build 1.5 million homes over a five year period. Additionally, It has also been in talks with the Iraqi government on a potential sale of 3D printers for a 10,000 home project [4]. WinSun’s chairman, Ma Yihe, has stated that he believes the future growth of the business will come from selling its ink composites and licensing the printer technology, under the protection of its dozens of international patents. What is described as their biggest future project is supplying pillars and seats for Elon Musk’s Hyperloop project, which pushes WinSun into different products than the residential homes it has previously built.
As WinSun continues to look to grow in the future, it has a few options. In the short term, it could solely continue to look for government partnerships to build large quantities of homes. The problem with only focusing on these government partnerships is that they may create an association with 3D printed homes as existing only for mass production housing relief. Instead, WinSun could license the technologies, as they have been contemplating, and focus internally on improving the design and visual appeal of homes so that they can eventually work with private consumers that are willing to pay a bit more for a higher quality homes. In regards to the construction process, WinSun should spend the next decade refining their 3D printers to be mobile, so that they can build a house on-site, while engineering for a minimization of pollution. This engineering improvement should reduce the production times associated with shipping and assembling separate pieces of building, and should also help provide more control at the job site to achieve those higher quality designs.
As I picture Ma Yihe gazing out of his 3D printed window at WinSun’s main plant, I think about what concerns are top of his mind. I would wonder how the additive manufacturing process can be further improved to reduce cost and time, while increasing quality. I would also think about what challenges I may face when entering new countries related to both culture and consumer preferences.
Word Count: 756
[1] Aldama, Z. (2017). ‘We could 3D-print Trump’s wall’: China construction visionaries set to revolutionise an industry rife with graft and old thinking. [online] scmp.com. Available at: https://www.scmp.com/magazines/post-magazine/long-reads/article/2093914/we-could-3d-print-trumps-wall-china-construction [Accessed 9 Nov. 2018].
[2] Chen, T. (2018). China Smites Smog With an Iron Fist. [online] wsj.com. Available at: https://www.wsj.com/articles/china-smites-smog-with-an-iron-fist-1516185003 [Accessed 9 Nov. 2018].
[3] Levick, R. (2015). New Data: Bribery Is Often ‘An Unspoken Rule’ In China. [online] Forbes.com. Available at: https://www.forbes.com/sites/richardlevick/2015/01/21/new-data-bribery-is-often-an-unspoken-rule-in-china/#53b14f979c6d [Accessed 9 Nov. 2018].
[4] Iraqi government looking at WinSun`s 3D printed homes for post-war rebuilding efforts. (2016). Real Estate Monitor Worldwide; Amman. [online] Available at: http://search.proquest.com.ezp-prod1.hul.harvard.edu/docview/1812510052?accountid=11311 [Accessed 9 Nov. 2018].
Interesting article! I think there are some real questions about this model though. What strikes me as most innovative relative to the traditionally construction model for WinSun is actually less additive manufacturing and more the systems based approach where components of the house are pre-built in a factory and then assembled on site. This reminds me of what the startup Katerra is working on right now in the US (see some interesting links below). The systems based approach creates tremendous costs improvement due to procurement, standardization, and avoiding layers of contractors and subcontractors relative to the traditional model of building on site. With WinSun, I wonder how much of the efficiencies realized is due to the systems based approach and how much is the 3D printing. Additionally, I question how innovative WinSun’s “3D printing” technology actually is because layering the “ink” of this concrete-like material to create shapes doesn’t seem intuitively different from using wet concrete to create shapes. Finally, concrete (and presumably concrete like structures) are more susceptible to damage in major earthquakes and floods.
https://www.nytimes.com/2018/01/24/business/dealbook/katerra-softbank-vision-fund.html
https://archpaper.com/2018/04/katerras-craig-curtis-pushes-standardization-customization/
The article provides very insightful and concise information on how the 3D printing is improving the time and costs of construction, but I found particularly interesting the reasoning behind how this technology is also helping to address two “non-numerical” but extremely important issues, such as corruption and environmental impact. Think about the future, the most important challenges seem to be related with the entry in new markets and the response on competition, but for me, another fundamental question related to whether this technology, as it is, is sustainable and long lasting, and if not, how much should the company continue investing in R&D to keep being at the forefront.
Wow. I am in awe of the way WinSun is using 3D printing to build houses! I never could have imagined a printer could create something as sturdy and large as a house. I’m having trouble imagining what a 500-feet printer looks like. I love how you outline 2 country and culture-specific major issues WinSun could help address: pollution and corruption. There is a clear need and impact for this product/process.
To achieve broad impact, I agree with you that the manufacturing process must be made more efficient and cheap. In terms of how, I would suggest looking at other players who have been successful. Cazza has developed technology to automate its own construction processes, and has made their machines more portable (which they say is their differentiator) [1]. Even if WinSun invested in making their PROCESS more efficient/cheaper, this will be all for naught if their shipping costs are extremely high. Therefore, in my eyes it’s essential that WinSun prioritizing making their machine and process compatible with portability, especially as they consider expanding all around the globe.
As for your second question, I think WinSun’s ability to capture a new market will depend on how they can meet consumer preferences in various geographies around the globe. Thus far, from your article, it sounds like the only material they use is concrete, which may not meet the preferences of consumers or companies building homes in various places. Additionally, I worry how many new designs, molds, etc. WinSun would have to make to meet different tastes, preferences, and demands, and wonder how difficult this would be. Given the machine is 500 feet long, I have no idea how flexible it is; if there are not several flexible settings, I could see it being hugely capital-intensive to invest in building too many different styles of homes. To me, that begs the question of whether they should focus initially on the Chinese market while they hone their product + processes, or if they should continue with their ambitious global growth goals.
[1] https://www.forbes.com/sites/suparnadutt/2017/06/14/this-startup-is-ready-with-3d-printing-robots-to-build-your-house-fast-and-cheap/#2f7826236e8e
It’s very interesting to me to think about how this concept and business model could be applied in developing vs developed countries. In particular whether there would be any form of brand cannibalization if one were to go after different segments of the market (affordable vs. upscale), and if one could mitigate this by fundamentally different designs.
I did not even think about the potential to build something as large as a house! But if possible to gain efficiencies and reduce waste, which is a huge problem is construction, and thus reduce costs this could really transform how and where houses are built vs. assembled.
Thanks for sharing this article about WinSun! I was not familiar with the company and it seems it has the potential to disrupt the construction industry in China. I see value in the company’s ability to standardize the construction process and offer lower, more reliable rates. As we’ve been learning in FRC, trust is critical to building a thriving market, and this company is creating trust in a market current plagued by corruption. My question, however, is what makes this company unique relative to others using 3D printing. Without a competitive advantage, it seems like this approach can be easily replicated. Additionally, I wonder if the bulk of the value delivered here is related to the provision of affordable housing. How do we avoid creating a new version of Levittown – a community of cookie-cutter houses? I agree with your intuition that WinSun could create value for customers by focusing on high quality design. By creating more custom design, however, does the efficiency of 3D printing go away?