Boeing: “Adding” to the Manufacturing Process
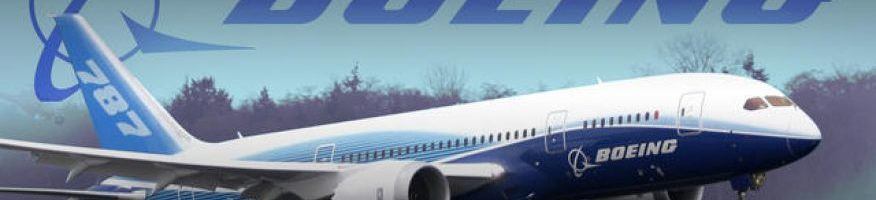
Boeing has leveraged additive manufacturing to improve upon its existing production processes. To what extent can Boeing continue to capitalize off of these capabilities and what obstacles stand in its way?
Additive manufacturing (AM) is an innovative manufacturing process that utilizes 3D model data to join materials together layer by layer in order to create an object [1]. Contrary to the traditional method of subtractive manufacturing, which creates objects by beginning with a block of material and subsequently cutting pieces away, AM presents a number of process advantages that organizations are beginning to take notice of, specifically within the aerospace industry.
The Boeing Company (Boeing), the world’s largest aerospace company, is one of the organizations at the forefront of AM innovation, having installed over 50,000 AM-produced parts within its commercial, space, and defense programs [2]. Boeing continues to try to find ways to increase AM within its organization, due to the numerous advantages that AM brings to its processes. These advantages are primarily associated with the following:
- Cost Reductions – A considerable portion of cost savings associated with AM is the ability to reduce the length of Boeing’s supply chain, whether by bringing certain manufacturing processes in-house or simply decreasing the time of production. According to research, AM can reduce lead times up to 80%, substantially reducing inventory carrying costs [3]. The AM process also results in a substantial reduction in waste, as it requires roughly 25% of the energy and 10% of the raw materials than that of a traditional manufacturing process [4]. These gains in efficiency are primarily associated with the layer by layer approach, allowing for optimal utilization of resources.
- Complex Design Opportunities – Due to the complex nature of the parts within the industry, each part typically requires a great deal of individual components that are connected by fasteners at the end of the manufacturing process. Each of these separate connections ultimately reduce the part’s reliability [5]. Due to the flexibility that AM provides, Boeing is able to produce these complex parts without having to build each separate component, limiting the number of connections. This has allowed Boeing to develop parts that are lighter in weight and more reliable than the parts manufactured in a traditional manner. Figure 1 demonstrates the innovative design possibilities of AM [6].
Figure 1. Right side of each arrow demonstrates the improved part design when using AM [6].
In the near term, Boeing has made great strides in continuing to build out its AM capabilities, most notably with its investment in Digital Alloys, a US Company developing high-speed, multi-metal AM systems utilized in the production of complex parts for aerospace and other industries. Digital Alloy’s patented Joule Printing technology avoids the cost and complexity of existing power-based AM systems and can rapidly combine multiple high-temperature alloys into each part [7]. This investment serves as a complement to Boeing’s existing relationship with Norsk Titanium, where the companies have implemented the first titanium structural components developed through AM processes [8]. In the medium term, Boeing expects to continue capitalizing on strategic partnerships and investments, focusing its efforts on making additional advancements in speed and scale in order to capture customer value [9]. Through this combination of strong partnerships and AM capability developed internally, Boeing expects to sustain continuous advancements amongst its competitors going forward.
Although Boeing has made significant advancements in AM within the aerospace industry, it needs to address the risk associated with the implementation of these parts in order to maintain its position amongst the forefront of innovation. Due to the stringent safety standards within the aerospace industry, a lack of understanding on the effects of AM processes on alloys has raised concerns amongst regulators, leading to a delay in commercialization of parts. One key area of focus has been the understanding of the aging of AM alloys. Due to limited research on these parts, organizations within the aerospace industry have not been able to make regulators comfortable with this topic. This has led to a majority of parts being restricted to noncritical use [10]. As a result, Boeing must focus on obtaining clear data on the useful life of AM-produced parts. A potential way to obtain this information in the near term would be to conduct a set of simulations internally, stress testing the general durability of each of the parts. Additionally, a more long term approach will be to closely monitor the replacement and failure rates on installed parts. Such statistical evidence will allow Boeing to make regulators more comfortable and potentially mitigate the hindrance of process improvements in the future.
As Boeing continues to make strides in the advancement of AM, what do you see as the biggest obstacle in Boeing’s way for complete commercialization of these products? Do you think that Boeing has taken the correct steps to date to allow it to make sustained innovations within AM?
(764 words)
References:
[1] Khorram Niaki, M., & Nonino, F., Additive manufacturing management: a review and future research agenda, International Journal of Production Research, 55 (5), 1419–1439, https://doi-org.ezp-prod1.hul.harvard.edu/10.1080/00207543.2016.1229064.
[2] The Boeing Company, 2017 Annual Report, http://s2.q4cdn.com/661678649/files/doc_financials/annual/2017/2017-Annual-Report.pdf, accessed November 2018.
[3] Schiller, G. J., Additive manufacturing for Aerospace, 2015 IEEE Aerospace Conference, Big Sky, MT, 2015, pp. 1-8, https://ieeexplore- ieee-org.ezp-prod1.hul.harvard.edu/stamp/stamp.jsp?tp=&arnumber=7118958&tag=1.
[4] U. S. Department of Energy, Additive Manufacturing: Pursuing the Promise, https://www1.eere.energy.gov/manufacturing/ pdfs/additive_manufacturing.pdf, 2012.
[5] Schiller, G. J., Additive manufacturing for Aerospace, 2015 IEEE Aerospace Conference, Big Sky, MT, 2015, pp. 1-8. https://ieeexplore- ieee-org.ezp-prod1.hul.harvard.edu/stamp/stamp.jsp?tp=&arnumber=7118958&tag=1.
[6] Aston, R., “3D Printing Done Right,” Innovation Quarterly Blog, November 2017, https://www.boeing.com/features/innovation- quarterly/nov2017/feature-thought-leadership-3d-printing.page, accessed November 2018.
[7] “Boeing invests in high-speed metal 3D Printing company,” Aerospace Manufacturing Magazine, August 9, 2018, https://www.aero- mag.com/boeing-horizonx-invests-digital-alloys-3d-printing-metal-additive-manufacturing-aerospace, accessed November 2018.
[8] Spaeth, D., 3D Printing is Changing the Face of Multiple Industries, ECN: Electronic Component News 61, no. 9 (October 2017): 21–23, http://web.b.ebscohost.com.ezp-prod1.hul.harvard.edu/ehost/pdfviewer/pdfviewer?vid=1&sid=75d5b552-2f58-4f62-bc57- bfd065acb234%40sessionmgr120.
[9] “Boeing’s Additive Ambition,” interview by Paul Tate, Manufacturing Leadership Council,, May 2018, https://www.manufacturingleadershipcouncil. com/2018/05/03/boeings-additive-ambition/.
[10] W.J. Lim, K.Q. Le, Q. Lu, and C.H. Wong. An Overview of 3-D printing in manufacturing, aerospace, and automotive industries, IEEE Potentials35, no. 4 (2016): 18–22. https://ieeexplore-ieee-org.ezp-prod1.hul. harvard.edu/stamp/stamp.jsp?tp=&arnumber=7517429.
Thanks for your insights! I always think it’s great when blue chip companies, such as Boeing, start embracing these technologies, as that would signal to me that the technology is gaining mainstream acceptance. Reading more about Boeing, it appears that the R&D for additive manufacturing and other novel technologies are carried out through its venture arm, HorizonX. [1] From an organizational perspective, it makes a lot of sense to me that these teams are built out separate from the large commercial parts of the business, which are focused on, quite literally, delivering the “nuts & bolts”. Thinking back to the market perception map from the Product Development Fundamentals note, it makes a lot of sense that there would be a small dedicated group working on these breakthrough technologies. I’d be interested to know at what point an initiative like additive manufacturing moves past the “tiger team” or “skunkworks” approach and becomes a technology integrated into the larger business.
[1] Rajiv Lalwani, et al. “What Did Dennis Say at Laguna?”, Morgan Stanley, September 13, 2018, https://amr.thomsonone.com/, accessed November 2018.
Great article buddy!
3D printing has huge potential and Boeing clearly knows it. However, I presume that 3D printer for sophisticated aviation parts requires large upfront capital. Given the rapid growth of 3D printing technology, is it possible that current 3D printer(let’s say Boeing’s asset) become obsolete? What if something goes wrong during flight operation and everyone blames Boeing’s “additive manufacturing”? The pioneer should bear so much pressure and take risks to success. I hope the day would come!
It was definitely interesting to read about how much Boeing has invested in additive manufacturing, particularly given our discussions about Boeing in class and their emphasis on a very protracted and highly costly product development cycle. Innovations in this field can be a huge advantage for the company, but the question is how they will be able to proof out the concept to appease regulators and the general public in terms of safety standards and perceptions. Boeing might have to devote additional resources in marketing, safety R&D, and testing because they are at the forefront of AM in their field.
Cool article! I can definitely see the benefits for Boeing on implementing AM. I think a major challenge is convincing the regulatory bodies about the reliability of the components manufactured with AM. Specially in this highly-regulated industry. I thin Boeing and other OEMs should start working with local governments and regulators to certify AM components. Maybe one way they could start doing this is by introducing such components on military aircrafts/applications, since Boeing and its rivals work on several projects with the army/government.
The biggest direct obstacle facing Boeing is the FAA. Obviously this really means they need to find a way to create a consistent product which can adhere to appropriate safety standards. From my understanding of the current technology it is difficult to ensure the needed consistency and thus would make the entire process more expensive. If Boeing can mature the technology and solve some of these problems I see it creating many advantages for them. In particular it will increase their overall output rate of parts while also making better parts that are lighter and stronger. This will impact operating costs as planes will require less fuel. Overall the technology needs time to mature in order to ensure success.
I agree with you that safety is definitely a very important challenge for Boeing to widen the scope of AM parts. I read another TOM challenge essay about the use of 3D-printing in cars, which has also been limited to minor accessories thus far. I think one way to accelerate the useful life testing of AM-produced parts is to actually collaborate with Airbus on the project. It may sound counter-intuitive, but I think this is an important step towards helping to reduce costs for the whole industry and the efforts of two giants will definitely yield better results than Boeing alone.
Interesting article! The aerospace industry seems like a compelling fit for 3-D printing – significant value could be unlocked by Boeing if airplane parts could be printed relatively quickly and to quality standards. The point you raised about the potential to eliminate 80% of supply chain lead time is especially striking. With those types of opportunities, I am not surprised that Boeing is investing heavily in this technology and building out their own internal 3-D printing capabilities. Boeing should keep this program a priority and push to get their printed parts across the finish line (approved by safety regulators). I agree with Mike’s suggestion that rigorous internal stress testing is a good place to start.