Additive Manufacturing Takes Flight – GE Aviation’s Integration of 3D Printing to Enable Innovation
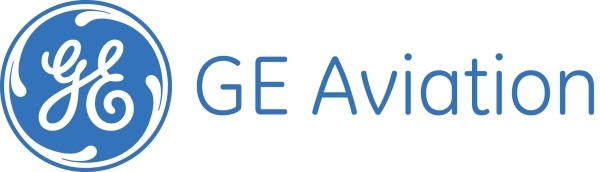
GE, a manufacturing conglomerate recently under heavy scrutiny for its operational capabilities, is heavily invested in re-imagining how its aviation business innovates and operates through the use of additive manufacturing.
General Electric is one of the largest manufacturing conglomerates in the world today. Even as critics mount in attacking the long term viability of their business units, GE is relentless in its pursuit of pushing the boundaries with additive manufacturing – particularly within its aviation division – with the goal of driving more efficient innovation and operating processes [1]. Use of additive manufacturing can have widespread benefits that are limited not by the concept design but rather by the sheer scale of the printer itself [2]. Additive manufacturing (“AM”), or 3D printing, is the use of computer aided design to direct a machine to deposit layers of material per the input design to create highly precise objects [3]. In contrast to traditional manufacturing processes, where layers of material are shaved off of an original base, AM builds pieces from scratch. The AM process is highly automated once fully functioning, allowing for rapid design implementation through updates to input computer aided designs.
Development in the aviation industry has been slow and arduous since its inception. Constrained by slow production cycles and low feasibility of due to the scale of products, design processes are typically long and costly [4]. Due to this lethargic pace of innovation, the industry is prime for disruption via additive manufacturing. Through years of commitment to this technology, GE Aviation is at the forefront of integration of additive manufacturing [1]. With one of their latest developments, the GE Catalyst, a turbine constructed using more than one third 3D printed components, GE is starting to see the results of years of investing and testing [2].
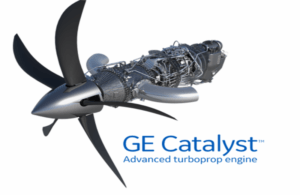
The implementation of the AM process allows the development team at GE to think creatively. Designs that were previously deemed ‘too complex’ or ‘too expensive’ for traditional manufacturing process before are now easily coded into the machine for prototyping [5]. At its most technologically advanced facility in Italy, GE works with all different types of materials that are cut by an electron beam, which brings a heightened level of precision to the large scale turbine manufacturing process [4]. Another benefit of additive manufacturing for GE is that their life cycle for one prototype shrunk down to just a few weeks, drastically improving their ability to test new concepts and ideas [2]. Lastly, the use of additive manufacturing has allowed GE to significantly reduce the number of component parts within each engine, from 855 to twelve for the GE Catalyst, reducing the weight of the engine and in turn decrease fuel consumption by up to 20% [2]. The radical change from traditional to additive manufacturing should allow GE Aviation to tap in to a level of innovation not seen in this industry before.
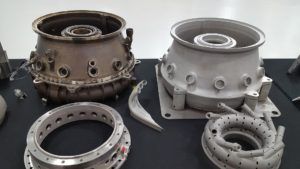
GE has invested heavily in the past to lower the barriers to innovation within the aviation division. Most notably, their Additive Technology Center in Cincinnati Ohio is one of the world’s largest and most advanced additive manufacturers, housing six of the largest 3D printers as of early 2018 [2]. The continued investment in its factories, both of this scale and smaller scale globally, and its scientists will be critical to the near term success. GE is also trying to harness the growing worldwide knowledge of additive manufacturing by its acquisition of two European companies this past year and planning to construct a factory in Italy of similar scale to that in Ohio [2]. These decisions will enable the collective knowledge of additive manufacturing within GE to organically grow and permeate across geographies as they bring in more expertise and allow more trial among different divisions of their business lines.
Currently, GE is focused on isolating product development projects in their entirety for the additive manufacturing process, however I would recommend that they perform a larger scale review their existing products in production to potentially integrate 3D printed components as soon as feasible. The goal is to target multiple components that might pose the greatest design challenges and can be replaced by 3D printed components in a limited scope at first. The end result would be to isolate key design criteria that would result in the largest impact on design efficiencies. Longer term, I believe GE would benefit from partnering with advanced academic or research institutions focusing on 3D printing processes given that 3D printing is a young but technologically intricate process.
While this technology has shown promise for an individual product at GE, is this something that can scale across other product lines within the Aviation division? One concern I have for GE is that the aviation industry seems to be the perfect choice, as production is highly specialized and bespoke, thus I question if it possible for other business lines at GE to reap the same benefits of the larger investments in the additive manufacturing process.
(793 words)
Sources:
- D’Aveni, Richard. “General Electric Should Defy Wall Street Pressure To Break Up.” Jan 2018. https://www.forbes.com/sites/richarddaveni/2018/01/19/now-is-the-worst-time-for-ge-to-break-up/#1c8b5ce82f0d
- Kellner, Tomas, and Bovalino, Yari. “Printing Heads: 3D Printing Has Launched a New Era in Aircraft Design.” Mar 2018. https://www.ge.com/reports/printing-heads-3d-printing-launched-new-era-aircraft-design/
- Frost & Sullivan. “Impact of Additive Manufacturing (3D/4D Printing) on the Global Energy Sector. Aug 2018. https://cds-frost-com.prd1.ezproxy-prod.hbs.edu/p/71319/#!/ppt/c?id=MC1B-01-00-00-00&hq=3d%20printing
- Kellner, Tomas, and Bovalino, Yari. “How 3D Printing and Digital Technologies are Altering the Face of Aircraft Engine Manufacturing in Italy.”Net, 2017. ProQuest, http://search.proquest.com.ezp-prod1.hul.harvard.edu/docview/1871316832?accountid=11311.
- Kellner, Thomas. “The Devil Is In The Details: How GE Found A Way To Bring 3D Printing To Mass Production.” Oct 2018. https://www.ge.com/reports/devil-details-3d-printed-part-jet-engine-part-now/
Great post! My main question / reaction after reading this piece is how GE Aviation should consider the risk of cybersecurity breaches in its deployment of 3D printing across its organization. It seems like a 3rd party hack could severely jeopardize the safety of its production processes (and national safety) as the designs and structural details / potential weaknesses of its aircraft and its components become exposed. Assuming that appropriate encryption and cybersecurity protection measures are in place, however, I agree with your assessment that 3D printing can really revolutionalize the manufacturing process within the aviation industry, especially when it comes to replicating complicated machinery and detailed prototypes. Very insightful analysis!
Very insightful read! Additive manufacturing does represent a very exciting frontier in the world of innovation and prototyping. I however wonder whether if as 3D printing technology becomes more commoditized in the near future, the ability to easily replicate prototypes given the required digital information would not leave GE prone to corporate espionage in the sense that would-be infiltrators would find it easier to steal and implement design secrets since they would just need to feed digital designs into their own 3D printers to obtain copies of the prototypes. This development would eliminate any competitive advantages in manufacturing that GE may have with regard to its machining infrastructure for various mechanical products. My question is, are the potential risks associated with the safety of intellectual property worth the incremental benefits of scaling up this technology?
Very interesting read! the 20% fuel consumption reduction seems very drastic for the aviation industry. I wonder how long it will take for these cost savings to translate into price benefits for the consumer, if that is ever to happen. It might be difficult given the asset-intensive nature of the aviation industry, but perhaps in other business units these benefits will actually reach the end consumer.
I found this very interesting, mostly because 3D printing is not something I would associate with building parts for airplanes, where quality is such a critical factor. It makes sense though that if quality is not a concern, or if the technology of 3D printing has advanced to that level, that there would be HUGE cost savings to this additive manufacturing method. It would also be interesting to know how GE’s competitors or other airplane part manufacturers are using this tech. The speed of innovation that is possible, along with the cost benefits, should certainly exist for even for less specialized products, though likely not to the same degree.
Awesome read! This trend in aviation is so intriguing and I’m very curious how the material science works. With narrow over design margins in aerospace (as opposed to automotive) due to weight, additive manufacturing seems like it would be perfect for the industry as you may be able to add strength/redundancy without adding weight. However, the raw materials that can be used in “3D printing” are limited therefore the components eligible to be printed are limited as well. Hopefully through driving innovation in the parts that can be printed, GE will also drive innovation in the process of additive manufacturing itself!
I agree that 3D printing can bring GE a lot of advantages in terms of prototyping. Many of the advantages mentioned in the article (e.g., shorter life cycles) referred to prototypes but not necessarily to large scale production. While 3D printing brings less cost advantages in very large scale production, I wonder what the threshold would be in terms of number of units to use 3D printing vs. traditional manufacturing (after the prototype is built). Would 3D printing work for the entire production or just for the prototyping? Thanks!
Thanks for the article! Additive manufacturing seems to be a great fit for GE’s aviation division. However, they have had significant difficulties upfront and mixed results thus far. GE is fairly decentralized by division from my understanding. I wonder if they will be able to use this technology across their other divisions or if they will be able to get the full buy in from other divisions given the difficulties the aviation division faced and the overall struggles GE has been facing recently. My guess is that this will be a hard sell for management to get other divisions to implement additive manufacturing.
Interesting article! It is clear that 3D printing could be the catalyst to improving performance at GE’s manufacturing operations starting with the aviation division. I also suspect given the amount of capital investment required GE has bought themself some time wherein this can be a significant competitive advantage relative to peers. One area I think would be interesting to assess is the efficacy of 3D printed parts relative to their traditional counterparts given existing products still heavily rely on majority traditional components.
Really cool. Thanks for writing about this. I agree with your recommendation that GE should conduct a broader review of its product lines and work to integrate 3D printing more broadly where that’s productive. Considering the breadth of their product line, it would be surprising if they did not find a host of other applications for the technology. I could imagine a lot of benefit in the more technical parts of their “Critical Power” or “Industrial Solutions” divisions, for example. Even if they did not want to stray too far from the ways that they are using 3d printing in aviation, it seems like there could be a lot in same “highly specialized and bespoke” niche that they have found.
Thanks for the post. As an aviation enthusiast, I agree the benefits of additive manufacturing would be most easily seen in GE’s aviation division. If the usable space within a 3D printer is used to maximum capacity, each “print run” can be used to create multiple custom parts for a variety of products, which is one way to help scale the process. The ability to form complex, supportive structures while using less material and reducing weight would benefit GE Renewables and their design of wind turbine components.