Additive Manufacturing in Medical Device: Can Johnson & Johnson stay ahead of the curve?
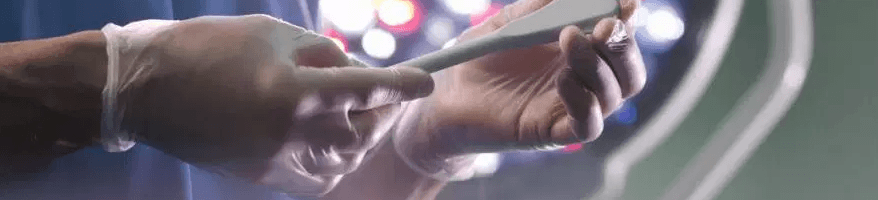
Additive Manufacturing offers substantial promise to medical device products and supply chains, but it also presents an existential threat to the incumbents in the industry.
Additive manufacturing will drive significant value within the supply chain of Johnson & Johnson’s (J&J) medical device business. Medical device companies need to offer a diverse set of products because humans are diverse – different sizes, different materials, and different constructions drive a large SKU portfolio [1]. The larger the portfolio the more difficult it becomes to accurately measure and plan for demand. There is also uncertainty related to the actual product required for a specific patient. For instance, the surgeon may not know which implant or implant size is required until the surgery is underway. This requires companies to send many different options for a single surgery driving substantial inefficiencies. Finally, due to the nature of certain surgeries, such as trauma, products need to be available to hospitals with short lead times to ensure surgeries aren’t delayed.
To maintain service levels on these large product portfolios companies such as J&J hold large days of inventory within their supply chain to guarantee a high level of customer service. In fact, the average days of inventory for a medical device company is around 150 days compared to ~50 days within the Consumer Industry [2].
Additive manufacturing will allow J&J to combat this inefficiency by manufacturing localized patient specific products improving the supply chain’s agility and ability to adapt to changes in customer demand. Though additive manufacturing presents a promising opportunity, it is also a major risk to the company, as competition, both current and new, attempt to achieve breakthroughs in the field. [3]
J&J is taking a leading role in developing and deploying this technology in the industry. They’ve established the Johnson & Johnson’s 3-D Printing Center of Excellence [4] “which is working to change the landscape of healthcare through 3-D printing innovations.” This group is focused on developing customized patient solutions and the ability to print devices more quickly and at a lower total cost than current methods. J&J has also established a partnership with AMBER, a material science institute focused on the bioprinting, broadening their area of focus beyond metals and polymers for this technology [5].
Longer term J&J appears to be taking a strategy where they’re not solely focused on the manufacturing of medical devices but rather on the comprehensive product and service combinations related to a surgery. J&J has formed a partnership with Guys and St. Thomas’ NHS Foundation Trust to create an Orthopedic center of excellence where J&J takes on a more active role in the end-to-end activity related to a surgery [6]. They have also recently acquired a German software company that specializes in standardization and digitalization of surgical workflows in the operating room [7]. The changes hint at a strategic maneuver toward embedding themselves within the surgical process placing J&J in a strong position to be directly involved in the industry’s potential transition to localized manufacturing made possible by additive technology [8].
In terms of other steps, I recommend the organization takes, in the short-term I believe their focus should be on three areas. First, they should aim to progress the technology to augment their current products and processes. For example, they should improve their supply chain by achieving the inventory benefits that come with reduced production lead time. Next, they should understand the changes to the regulatory pathway driven by additive manufacturing. The FDA has published Technical Considerations for Additive Manufactured Medical Devices [9] that J&J should ensure are efficiently designed within their processes. Finally, they should keep abreast of the use of this technology by competitors. Stryker has recently invested 400 million to progress the use of additive manufacturing in their products [10] and has launched new products using 3D Printing [11].
In the medium term, I would recommend the company take a more aggressive approach to working directly with hospitals on localized manufacturing. The more experiments in this area the company operates the more likely they’ll stay ahead of the changes this technology will drive in the medical device supply chain. Additionally, I would recommend that J&J’s leadership meets on a regular basis with internal and external experts in the field to stay abreast of latest applications of the technology to ensure their strategy is continuously adjusted to account for developments as they occur.
The key question J&J needs to answer in the future is how their role in the medical device value chain changes as barriers to entry to the industry are significantly reduced by additive manufacturing enabling faster and cheaper design and production. Do they move closer to the hospital and patient and focus on embedding themselves in the operating room? Do they attempt to maintain their competitive advantage in device innovation and design when it becomes easier for smaller players to launch a product?
(785 Words)
Sources:
[1] Xu, Xiaofan, and Maria Rey. “Understanding Demand: Are You Keeping the Right Amount of Inventory?” Recently Filed RSS, 21 Nov. 2017, www.scmr.com/article/understanding_demand_are_you_keeping_the_right_amount_of_inventory.
[2] Tribe, Bill, et al. “What’s Next for Medical Device Supply Chains.” ATKearny.de, AT Kearny, 2017, https://www.atkearney.de/documents/856314/13942554/What%27s+Next+for+Medical+Device+Supply+Chains.pdf/a03da9f3-66c0-4394-a912-eb54ee78b963.
[3] Scott, Clare. “The Impact of 3D Printing on the Medical Device Industry.” OrthoFeed, 27 July 2018, https://orthofeed.com/2018/07/27/the-impact-of-3d-printing-on-the-medical-device-industry/.
[4] Brewster, Signe. “The Power of 3-D Printing: How This Technology Is Blazing New Medical Frontiers.” JNJ.com, Johnson & Johnson, 27 Mar. 2017, www.jnj.com/innovation/how-3d-printing-is-blazing-new-medical-frontiers.
[5] Saunders, Sarah. “AMBER and Johnson & Johnson to Establish Collaborative 3D Bioprinting Laboratory.” 3DPrint.Com | The Voice of 3D Printing / Additive Manufacturing, 21 Feb. 2018, www.3dprint.com/204533/amber-johnson-johnson/.
[6] Sharda, Angela. “London Trust Agrees Partnership for New Orthopaedic Theatres.” Healthcare Leader, 23 Nov. 2017, www.healthcareleadernews.com/london-trust-agrees-partnership-for-new-orthopaedic-theatres/.
[7] “Johnson & Johnson Medical GmbH to Acquire Surgical Process Institute.” JNJ.com, Johnson & Johnson, 19 Oct. 2017, www.jnj.com/media-center/press-releases/johnson-johnson-medical-gmbh-to-acquire-surgical-process-institute.
[8] “Medical Additive Manufacturing/ 3D Printing 2018 Annual Report.” SME.org, SME, 2018, www.sme.org/uploadedFiles/Medical_Additive_Manufacturing/2018-SME-Medical-AM3DP-Annual-Report.pdf.
[9] Center for Devices and Radiological Health. “Science and Research (Medical Devices) – Additive Manufacturing of Medical Products.” U S Food and Drug Administration Home Page, Center for Drug Evaluation and Research, www.fda.gov/MedicalDevices/ScienceandResearch/ucm477366.htm.
[10] Brown, Alan S. “Chain Reaction: Why Additive Manufacturing Is About To Transform The Supply Chain.” Mechanical Engineering, Oct. 2018, pp. 30–35.
[11] “Stryker’s Spine Division Receives FDA Clearance for 3D-Printed Tritanium TL Curved Posterior Lumbar Cage.” About | Stryker, www.stryker.com/us/en/about/news/2018/stryker_s-spine-division-receives-fda-clearance-for-3d-printed-t.html.
Fascinating article – good job outlining how uncertainties in certain surgeries and trauma situations necessitate large inventories. Interested to get a sense of how quickly prototypes in J&J’s “center of excellence” can produce an item – are they anywhere near a fabrication time that could enable completion of a customized item during surgery – applying Just-In-Time inventory to the operating theater?
Thank you for the thoughtful article! You raised many good points on the ways that additive manufacturing is changing the manufacturing of medical devices and impacting J&J’s business model. If I were at J&J my primary focus would be on managing this transition to localize manufacturing and leveraging the J&J expertise to secure a continued role within hospitals and surgical care.
Really interesting post, Ti. I also lean towards getting closer to the hospital and patient in order to optimize responsiveness to the end customer (in this case, the hospital). Part of my thinking in this regard relates to a recent healthcare development on the pharma side of things, where Intermountain Healthcare and other large delivery networks have teamed up to launch a generic drug manufacturing company. They chose to do so primarily to combat (1) the high prices of pharmaceuticals and (2) to ensure more stable supply. While the medical device industry has not come under fire for its pricing practices like pharma has, this development would drive me to work even more closely with my customers with higher service and quality in order to dissuade them from bringing manufacturing in-house.
Given the new nature of this manufacturing (and materials, in many cases), it will be interesting to see where the FDA lands in the formal approval process for these devices. Currently, they are allowing them under the 510(K) and de novo pathways, but have required more manufacturing information than a standard 510(k) submission. Given the critical nature of device material to patient safety and the relative novelty of 3D printing, how would your stance on this change if the FDA decides not to allow these pathways but instead creates a new comprehensive pathway that is subject to manufacturing process approval?
Ti, this is a fascinating take on how J&J can utilize additive manufacturing both in supply chain perspective and a product perspective. I agree with your suggestions to take a multi-prong approach and using advancements in this technology on multiple fronts. A challenge I would add for J&J is developing expertise with innovative medical 3D printing products for healthcare purposes, perhaps by acquiring a company or investing in a startup. If we look ahead into the future of orthopedics or oral maxillofacial surgery, there is promise in using additive manufacturing technology on a real-time basis with patient-specific implants, structures, or even drug delivery devices.
Fascinating article, Ti! I really like your observation that AM is critical for J&J by enabling faster and cheaper production. I am wondering what will be the implications of that technology beyond developed markets but also on market dynamics:
+ For emerging countries: Will that enable emerging countries to get greater access to medical devices? or will J&J – and other players – focus more on innovation instead of reducing costs therefore limiting the impact on patients in developing countries?
+ For market dynamics: Will that foster greater competition in the medical devices industry by lowering barriers to entry? or will the impact be limited given the number of regulations to launch a new medical device?