Additive Manufacturing at Porsche
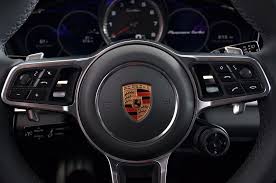
A look at the role of 3D printing in the future of Porsche
Background.
Additive manufacturing, more commonly known as 3D printing, is a method whereby an object is constructed through the addition of layers (Figure 1), rather than by subtraction or injection molding. In subtractive manufacturing material is removed, like when a woodworker whittles a figurine from a block of wood; in injection molding, as the name suggests, a molten material is injected into a mold, which is then removed. One great advantage of additive manufacturing is that it gives designers much more freedom to make structures which would normally be prohibitively complex due to factors like lack of tool access (subtractive manufacturing) or undercutting (injection molding). 3D printing is also a very versatile process, while often associated with small cheap plastic objects, 3D printers can be designed to print using almost any media, ranging from metals to food to bone.[1]
1.
The company I am looking at for the megatrend of additive manufacturing is Porsche. Porsche is a German automobile manufacturer focusing on high-end high-performance vehicles. Additive manufacturing will be an important factor for product development in two main ways. The first is the ability of 3D printers to build novel and complex architectures. In particular, hollow parts will allow Porsche to make lighter components, and thereby lighter cars, without having to sacrifice performance. In the automotive industry, weight is an incredibly important consideration, as it affects things like fuel efficiency, acceleration, handling, and braking.[2] The second benefit of additive manufacturing is that a single 3D printer can make a variety of parts, thereby removing tooling costs which are typically the most expensive fixed costs for low volume production. You can see how this bears out in a reduced cost for production of metal part below quite high volumes (Figure 2).
2.
In the short term Porsche is positioned to use 3D manufacturing for obsolete replacement parts.[3] In the auto industry, original factor parts are typically in good supply for 5 years, but cars are kept (in the US) for an average of 11.4 years.[4] This clearly means that older cars, and especially classic cars, are very hard to repair with genuine parts. There is little incentive to produce these parts, because the fixed costs to reproduce a part with volumes at such low levels is prohibitively expensive. With 3D printing on the other hand, Porsche can make even just one or two copies of a part for a classic car at roughly same cost per part as a new mass-produced part, and even using the same machine.
Replacement parts for classic cars is an extremely niche market, and so it would not be worth it for Porsche to move into 3D printing unless they have a longer-term strategy over the next 5-10 years. After establishing 3D printing for replacement parts, Porsche will look to 3D printing for mass production of parts, with an eye towards pushing performance benchmarks through weight reduction. With global sales of roughly a quarter million cars per year[5] across all sub-brands and models, the cost to manufacture all of their larger parts through 3D printing would be financially comparable to (or even cheaper than) traditional methods; this will all be possible while reducing the weight of parts through techniques like hollowing out, without reducing durability.[6]
3.
In the short term I would suggest that rather than 3D printing obsolete parts, that Porsche distributes their .3D files (a format usually used to digitally render the object to be printed) for these parts to individuals or garages. The benefit of this is that they will create a lot of goodwill with loyal car enthusiasts, while giving up what is a very small market.
In the longer term (5-10 years) I see two main additional uses for 3D printing: customization and Just-In-Time manufacturing. 3D printing will provide greater flexibility in the building of parts, and could allow for made to order cars with some level of customization; customization would need to be limited to specific parameters in order to maintain high performance and safety, but for example, trunk length might be customizable depending on customer need. More importantly, being able to produce parts on demand and as needed, will allow for Toyota Production System Just-In-Time part creation.
4.
An open question remains about whether additive manufacturing can make car production a local endeavor. Will 3D printing become simple but robust enough so that dealership lots full of new cars will be replaced by buildings for manufacturing customized cars made to order?
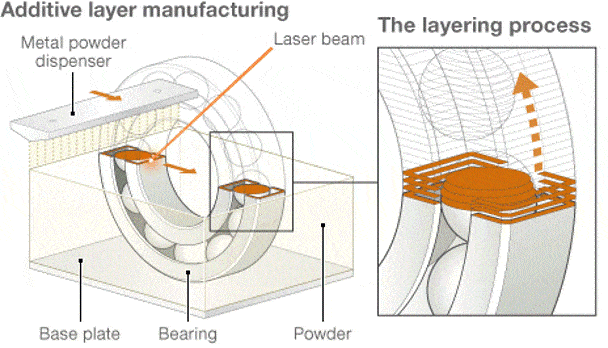

(765 words)
I found your idea of providing CAD files of classic parts for free to be very interesting. While I agree that the benefit of goodwill likely outweighs the potential financial benefits from selling the parts, I think there is potential for ill will as a negative externality to this decision. Once consumers can access the files, they can print the part on any machine, and with any material they choose. This could lead to failures of the printed part which could then cause accidents that may associate Porsche as a brand with safety issues. I think the question of safety and control may be a key area of focus in deciding how to approach production of replacement parts.
I found the CAD file perspective very interesting as well. I wonder to what degree Porsche would be willing to release its proprietary information due to the high costs of R&D. I think in practice, Porsche would be hesitant in allowing 3D-printing for parts critical to the function of the car, and steer towards design/auxiliary parts such as customized dashboard or interior features. If they are willing to release these CAD files, Porsche may be able to incorporate user input into the design of future cars (as an “open innovation” of sorts).
I question whether additive manufacturing can make car production a local endeavor. Like other forms of manufacturing, there are still economies of scale or 3D printing, and idle time (even if it’s at a local building) seems like it would be inefficient for global company. Beyond that consideration, I know that the auto industry is hyper-focused on quality control and inspection, which would be a big hurdle to localize.
I love the concept of using local shops to 3D print replacement parts, particularly for older/less common models, and can totally see a market need for that!
I struggle to see a localized 3D printing manufacturing process as a replacement for “Big Name” retailers. As pointed out in the essay, this system opens up the possibility of being improved by JIT manufacturing process. In that scenario, I believe the scale of the major autoplayers will be impossible to compete with. At the same time, despite its potential for car enthusiasts, more consumers would rank value and reliability when selecting their car, which would most likely lead them to picking a known brand.
Using additive manufacturing in luxury automobile production is an interesting concept, but it has the potential to destroy value in the industry. With respect to obsolete parts for older cars, many of these classic cars have high values due to rarity. If you make replacement parts and the entire vehicle easier to replicate, there’s a chance that you increase unit volume while reducing value per unit. With respect to new cars, I suspect that people are willing to pay a significant premium for hand-made luxury cars. Rolls Royce, Bentley, and certain models of the highest-end German cars are carefully marketed as being hand-made and trade at large premiums to factory-line vehicles.
I’d suggest using your recommendations for lower-end, mass production cars, to maximize value.
I wonder if we will ever get to the point of individuals having 3D printers in their own garages and being able to print their own replacement parts? In that regard, Porsche will be able to charge customers for the .3D file rather than having to manufacture parts themselves. If that becomes reality, then Porsche will become more of a design firm than a car manufacturer. The downside of that trend is that smaller companies and startups will be able to compete with large car manufactures. It takes less capital and infrastructure to create .3D files than to build manufacturing plants. Porsche should strategically think about how much power they are willing to give up and the long term benefits/consequences of outsourcing manufacturing.
Very informative piece on how 3D printing is affecting the automobile industry. I believe the analysis hits on several key points, such as hollowing parts to reduce part weights and solving the service parts longevity issue. Coming from an industrial hardware background, I understand that by eliminating the service parts issue, this would free up Porsche to make more sourcing & design decisions without worrying about part support.
This piece brings up some creative ideas which I wanted to provide a few counterpoints to facillate a more well-rounded discussion.
First, Figure 2 suggests that the breakeven point for casting vs. 3D printing is in the 6-digit (hundred thousands) order of magnitude. I wonder if this actually makes sense for Porsche, given that their car unit sales in 2016 alone were 237,778 units [1]. There may also be some parts that are used more than once in a single car, multiplying the part demand as well. In this case, the cost by using a traditional manufacturing technique seems to be lower. Would there be other qualitative reasons to using 3D printing?
Second, I think the idea of distributing Porsche’s .cad files to distributors to be an idea that may backfire in business terms. To me, the biggest reason to purchase a manufacturer branded replacement part is the trust in the quality, given that it was the original manufacturer. Furthermore, I wonder if there will be reverse-engineering concerns if Porsche distributed the .cad files since there may be nuanced design decisions that can be picked up more easily in a digital file than trying to reverse engineer a physical part by competitors.
Finally, I agree that heading forwrad 3D printing could provide tremendous value in terms of customization. This makes even more sense given that Porsche focuses on the high end automobile market. However, I am not sure if 3D printing would actually allow for Just-in-time manufacturing. It would be interesting to explore the actual printing time for some of the car’s parts. Based on personal experince, I would expect the difference in cycle time between casting and 3D printing to be more than 50x. I think it would be interesting to explore how 3D printing speeds are accelerating over time as well.
[1] “Porsche Sets New Sales Record.” Porsche Newsroom, 10 Jan. 2017, newsroom.porsche.com/default/en/company/porsche-deliveries-2016-sales-record-13310.html.
Thank you for this article! It is great news that 3D printing is used to manufacture replacement parts that are not being produced anymore due to high setup times and fixed costs. I am also very much intrigued by the application of 3D printing to build novel parts with hollow parts to improve performance. This could result in significant performance and efficiency enhancements and serve as a strong competitive advantage for Porsche in the high-end high-performance car market.
In the case of Porsche, I disagree with the idea that Porsche should share their .cad files with individuals or garages. In addition to the quality trust point raised by commenter EL, vintage car appraisers and collectors are adamant that only original parts are used. As a premium brand, Porsches will only retain their value if all parts are original and replaced by an official dealer. That being said, I do think your idea has a lot of potential in the mass car market.
I think there is a high likelihood that over the medium- to long-term, 3D printing will enable great customization and make production a more local endeavor. However, again I see the most potential in the mass car market, rather than in the premium luxury market, as customers typically place a lot of value on the manufacturing location. For example, a Porsche in Germany is also referred to a “car from Zuffenhausen”.