Additive Manufacturing at GE Aerospace
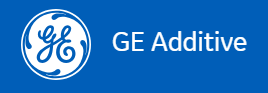
Additive Manufacturing – the Future of General Electric’s Competitive Differentiation in the Aerospace Supply Chain
While still early in its adoption curve across the industry, additive manufacturing (“AM”; also known as 3-D printing) has the potential to disrupt the future of aerospace manufacturing. The time, weight, and cost benefits of AM techniques are clear and numerous:
- Waste Reduction: a study of traditional manufacturing techniques relative to AM showed that “for every 1 kg of titanium part produced, a total of 10 kg of titanium is wasted”, much of which can be reduced using AM by replacing subtractive with additive processes [1].
- New Design Possibilities and Subassembly Reduction: AM is capable of building parts with complex geometries that are difficult or impossible to create using traditional manufacturing processes. Not only does this enable new possibilities in part design, but it will also help reduce part counts by replacing subassemblies with single components, thereby decreasing complexity, testing and monitoring burdens, and overall material costs [2].
- Weight Reduction: New geometric possibilities also permit the creation of lighter parts, which is of critical importance in aerospace given OEMs’ focus on aircraft fuel efficiency [3].
- Faster Prototype Design: Lastly, AM can expedite prototyping. Since AM processes eliminate traditional intermediate steps, it is possible to make alterations in real-time. When compared to traditional prototyping, AM offers a more dynamic, design-driven process [4].
However, despite AM’s clear benefits relative to traditional techniques, a few key barriers and complexities have prevented quicker adoption and roll-out across the industry. First, the cost of failure in commercial aerospace is incredibly high, creating the need for strenuous certification and qualification requirements for parts, which often take multiple years to receive. Second, the full effect of fatigue and aging on AM alloys isn’t fully-known, which has restricted their use primarily to non-structural and non-critical parts [1].
Nonetheless, most experts agree on the importance of AM in the future of aerospace manufacturing and the necessity for today’s manufacturers to develop differentiated techniques to maintain their market positions as AM knowledge and certification increase.
General Electric has long recognized the importance of AM in aerospace’s future. Although GE’s Additive unit is less than 2.5 years old, since its creation management has consistently delivered a message of investment and focus. Through December 2016, GE had invested approximately $1.5 billion in manufacturing and additive technologies and had earned 346 patents in powder metals used for the additive process [5].
In 2015 received FAA clearance for the first ever 3D-printed part for use in a commercial jet engine [4] (CFM’s LEAP engine, which is used in over 1,000 aircraft, including the Airbus A320 and Boeing 737) [6]. Additionally, in November 2018, GE announced that it received FAA clearance to replace a part in the Boeing 747’s GEnx engine with an AM part, the first ever used in the engine. The new part reduces manufacturing waste by as much as 90% and weighs approximately 10% less than the conventionally manufactured part, all while reducing GE’s unit production cost for the part [7].
Lastly, in July 2018 GE launched its Manufacturing Partner Network, with the intention of creating “an open, competitive marketplace that will accelerate both supply and demand for additive manufacturing” by “addressing several commercial challenges to ensure the additive industry reaches its next inflection point” [8]. Specifically, the initiative will promote knowledge sharing across the network, including partner access to over 150 GE consultants and technical support and the use of new GE additive technologies for testing, feedback, and future product development.
Going forward, I recommend that GE adopt a dual focus on its own internal capabilities and its Manufacturing Partner Network. I believe that the company recognizes the barriers to mass adoption within the industry and smartly is looking toward a larger network to collectively help move the industry forward. While doing so, however, GE should continue to proprietarily develop its own capabilities and technologies, as the aerospace supply chain is relatively consolidated, and most contracts are won by a single supplier for a high dollar amount.
A key question for GE as it looks toward the future is how it balances its own proprietary capability development vs. knowledge sharing with its partners for the benefit of broader industry progress. Which should GE prioritize, and is it possible to be both a collaborative partner and the clear industry leader with differentiated capabilities? Additionally, while outside the scope of this writing, how does GE balance investments in other AM applications with more immediate and monetizable near-term uses but less long-term potential (such as auto, medical, etc.) with investments in aerospace AM? Lastly, in light of the larger issues GE as a whole is facing, how does the company ensure that AM receives adequate investment and support amid management’s restructuring and cost cutting initiatives?
(785 words)
[1] C. W. J. Lim, K. Q. Le, Q. Lu and C. H. Wong, “An Overview of 3-D Printing in Manufacturing, Aerospace, and Automotive Industries,” in IEEE Potentials, vol. 35, no. 4, pp. 18-22, July-Aug. 2016. doi: 10.1109/MPOT.2016.2540098. URL: http://ieeexplore.ieee.org.ezp-prod1.hul.harvard.edu/stamp/stamp.jsp?tp=&arnumber=7517429&isnumber=7517414
[2] Marchese, K., Crane, J. and Haley, C. (2015). 3D opportunity for the supply chain: Additive manufacturing delivers. [online] Deloitte Insights. Available at: https://www2.deloitte.com/insights/us/en/focus/3d-opportunity/additive-manufacturing-3d-printing-supply-chain-transformation.html [Accessed 11 Nov. 2018].
[3] Kroll, E. and Buchris, E. (2018). Weight reduction of 3D-printed cylindrical and toroidal pressure vessels through shape modification. Procedia Manufacturing, 21, pp.133-140. Available at: https://www.sciencedirect.com/science/article/pii/S2351978918301380 [Accessed 11 Nov. 2018].
[4] GE Additive. (2018). What is Additive Manufacturing?. [online] Available at: https://www.ge.com/additive/additive-manufacturing [Accessed 11 Nov. 2018].
[5] General Electric (2016). GE makes significant progress with investments in additive equipment companies. [online] Available at: https://www.ge.com/additive/press-releases/ge-makes-significant-progress-investments-additive-equipment-companies [Accessed 11 Nov. 2018].
[6] CFM International (2018). CFM LOGS $15.7 BILLION IN ORDERS AT 2018 FARNBOROUGH AIRSHOW. [online] Available at: https://www.cfmaeroengines.com/press-articles/cfm-logs-15-7-billion-orders-2018-farnborough-airshow/ [Accessed 11 Nov. 2018].
[7] General Electric (2018). First additive manufactured part to be installed on GEnx commercial airline engines. [online] Available at: https://www.ge.com/additive/press-releases/first-additive-manufactured-part-be-installed-genx-commercial-airline-engines [Accessed 11 Nov. 2018].
[8] General Electric (2018). GE Additive Launches Manufacturing Partner Network. [online] Available at: https://www.ge.com/additive/press-releases/ge-additive-launches-manufacturing-partner-network [Accessed 11 Nov. 2018].
A great article that not only addresses the 4 questions posed by the Challenge but also adds additional in-depth of why the megatrend matters to the industry and GE in particular. I especially appreciate the flow of you article as for most layman, it’s not clear what exactly the technology does and why it has become a hot potato in recent years. Your bullet points in the beginning sets a solid foundation for the later parts of the article where you elaborate on how GE has adopted the technology in a chronological order. Lastly, by introducing MNF, the article brought in business complexity arisen from the technology. At the end of the day, technology should only be assisting business. It’s how the management leverage AM to make profit that justify the usage of it. Well done.
Thanks, Warrior Cat, for a very clear explanation of the advantages of AM.
You mentioned that AM has been important to GE for a long time, but they only created a dedicated additive unit within the last few years. I’m curious about the history—when did they start getting involved in activities that might be termed “additive,” for example? And will they be able to draw much on what they have learned in past efforts as they develop this new unit?
In such a heavily regulated industry as aircraft manufacturing, I wonder what the regulator’s perspective is. Does the Federal Aviation Administration (FAA) have a positive attitude toward AM, or are they more suspicious about safety issues with AM compared to conventional manufacturing methods? Given GE’s size and dominance in the market, I suspect that they have an opportunity to work with the FAA to craft best-practice guidelines for the use of AM in aircraft.
Your questions carry significant weight, especially given the current turmoil that GE’s management (and stock price) are facing. How can a company, in the midst of a corporate restructuring, even begin to dedicate investments into something as long-term and experimental as AM? To adopt our model from LEAD, this vision needs to be endorsed from the top-down level. What’s challenging now, however, is how do you sustain an investment project across different generations of leaders? As the company continues to evolve its leadership, it will be ever more important to be wholly committed to these long-term projects such that they can cling onto their competitive advantage before it’s too late.
Very interesting article! GE seems to be a natural early adopter in the AM industry, given the industrial nature of the company and its reach to customers in various industry verticals. One concern I have (which you alluded to) is that given how capital intensive AM is, I wonder if GE could continue to invest as heavily as it used to, given the company is in financial trouble (the company recently cut dividend to almost zero and announced to sell many of its assets). I agree the solution you propose for GE to find industry partner is a great one!
I wrote about the impact of AM on the footwear / apparel industry, and it’s interesting to see the similarities and differences in terms of cost / benefit across industries. The benefits are similar – rapid prototyping, cost savings through additive rather than subtractive processes, weight reduction for improved performance, etc. However, there is a lot more to lose in aerospace. As you mentioned, there are questions around the long term reliability of these materials, which is less of an issue in retail. It’s interesting to think about the variety of applications and the decision points for these firms, as you’ve outlined so well at the end of the article.