3D Printing Toyota’s Headlights: The Sourcing Decision
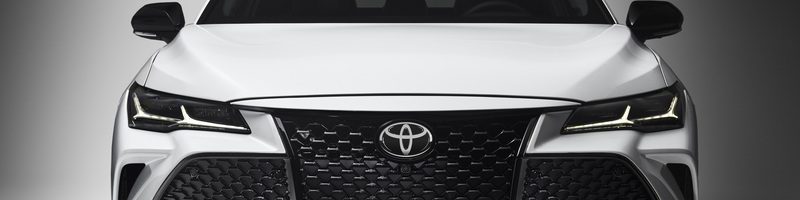
Wondering how 3D printing will really affect our vehicles? Here's how I approached it at Toyota.
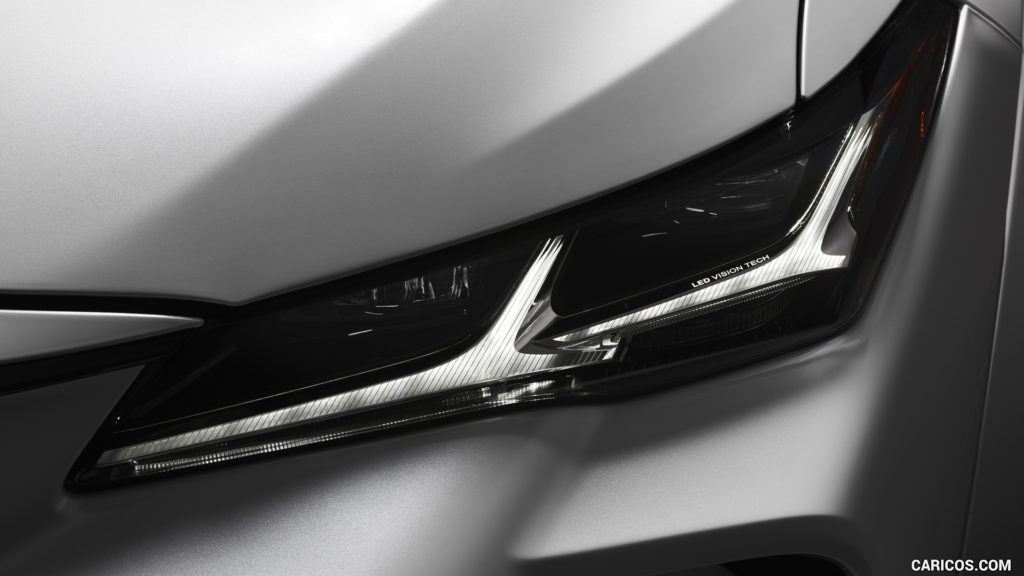
Additive manufacturing (AM, or 3D printing) made its initial splash in automotive as a fast, cheap prototype producer. However, as its technology improved, benefits with endless application emerged for manufacturing. From producing complex geometries with zero waste to reducing fixed cost and improving product flexibility, the automotive industry recognized the opportunity to innovate. As an engineer at Toyota, I worked with a team to study how AM would impact the headlights that I was profit responsible for, and determine whether or not AM would be feasible for production in the near future.To do so, I evaluated how AM would disrupt many of Toyota’s long established advantages and the plastic injection molding industry. Tradeoffs for both scale and quality had the most conflict with the Toyota Production System. [1]
Why is additive manufacturing a challenge?

Scale: For AM to meet the takt time of a Toyota assembly line (approximately 1 car every 50s) is a tremendous challenge. For traditional plastic injection molded parts, the cycle time is around 30s/ piece. Depending on the complexity of the part, a 3D printed plastic part of the same specification may take 2 hours to print. To achieve scale in a Just-in-Time environment, printers must choose between huge investments in multiple machines, or banks of inventory. [5]
Quality: An advantage to AM is the low direct labor content required for a 3D printed part versus traditional manufacturing. The injection molding process requires high labor, low skill content (picking a part from the machine every 30 seconds). AM requires only set up time, with no direct labor content, allowing one technician to run several machines at once. Though 3D printers are capable of making highly complex parts, there is still skepticism around quality standard and durability. Many parts may require skilled labor for inspection, polishing, and measurement after printing. [1]
What’s Toyota doing about this?
In the short term, I looked at two major problems are affecting manufacturing firms.
- The impact of high tooling costs on vehicle profitability, and
- The long production life of low volume, specialty parts.
Most automotive suppliers quote and compete for business on a price per piece basis including fixed and variable costs. For example, the reflective plastic part of the headlamp will require investment of $400,000 to buy an injection molding tool. In order to make a decision on this investment, I’d amortize the investment over every plastic part expected to be made from that tool. High volume programs have a low investment per piece, while low volume, specialty parts will have a higher investment price per piece. AM saves the initial $400,000 investment, but requires higher variable costs (renting the printing machine, expensive raw materials). [5, 8]
Toyota suppliers are required to be able to supply parts for a vehicle approximately 15 years after the vehicle goes out of production.Though volumes are very low (1-2% of production volume), the factory must maintain all the tools and equipment needed to make the part for a total of 20 years. As automakers take on more customization and variation (additional sport and luxury versions), the number of tools needed to make a vehicle compounds. Factories are building new warehouses and allocating floor space to accommodate a huge number of tools. Additive manufacturing eliminates the need to keep and maintain these tools to meet the low volume requirements. [7]
From my research, I recommended that AM be adopted for extremely low volume projects only in the short term. Until the variable costs of AM can be reduced, there is still significant economic benefit to traditional manufacturing.

Long term considerations for Toyota
Currently, If a Toyota engineer needs to make a change to a traditional plastic injection molded part, the manufacturer must physically refurbish the mold used to form the part at a tool shop. These changes are costly and time consuming. With an aging skilled workforce and high demand, it can take up to six weeks for a toolmaker to refurbish a tool and send it back to the factory. With AM, an engineer can rewrite a printing program in minutes, not weeks, significantly decreasing the development lead time of products. Schedule risk associated with traditional tool changes is not considered in the price per piece, but can dramatically impact overall project agility. Toyota managers must consider moving forward AM’s improvement on the development schedule. [3]
How to move forward?
Toyota must consider their partners in producing vehicles. Only about 25% of a vehicle’s content is actually produced by Toyota, the rest depends on the Tier I supply base. How should Toyota approach learning this immature market? Among a few large industry experts, there are several smaller businesses in this space with varying expertise and value propositions. Should they trust their supply chain to vet the different technologies, or should they vertically integrate for more control?
Word Count: 798
Sources:
- B. Roca et al., Getting past the hype about 3-D printing (Links to an external site.)Links to an external site.. MIT Sloan Management Review 58, no. 3 (Spring 2017): 57–62.
- Brown. Chain reaction: Why additive manufacturing is about to transform the supply chain (Links to an external site.)Links to an external site.. Mechanical Engineering 140, no. 10 (October 2018): 30–35.
- Cruz, C. (2018). Production Engineering at TMMK: Additive Manufacturing’s Impact.
- Giffi, C., Gangula, B. and Illinda, P. (2018). 3D opportunity in the automotive industry. [ebook] Deloitte University press. Available at: https://www2.deloitte.com/content/dam/insights/us/articles/additive-manufacturing-3d-opportunity-in-automotive/DUP_707-3D-Opportunity-Auto-Industry_MASTER.pdf [Accessed 13 Nov. 2018].
- Holwef. The limits of 3D printing (Links to an external site.)Links to an external site.. Harvard Business Review Digital Articles (June 23, 2015).
- Kerns. What’s next for 3D printing? The disruptive technology continues to grow thanks to lower costs and greater accessibility (Links to an external site.)Links to an external site.. Machine Design 90, no. 1 (January 2018): 36–42.
- Stratasys.com. (2018). Will 3D printing replace Injection Molding?. [online] Available at: http://www.stratasys.com/ [Accessed 13 Nov. 2018].
- Styles, G. (2018). 3D Printing Not Yet Ready to Disrupt Plastic Injection Molding. [online] Machine Design. Available at: https://www.machinedesign.com/3d-printing/3d-printing-not-yet-ready-disrupt-plastic-injection-molding [Accessed 13 Nov. 2018].
The gulf between the current state of additive manufacturing and what is required on a Just-In-Time production line is quite startling – 30 seconds per part versus 2 hours per part. I wonder how quickly this time will come down as we make advancements in the fields of robotics, 3-D printing and material science. Right now it seems like competing against scale driven manufacturing processes in the auto industry is a battle additive manufacturing will not be able to win. I’m also wondering what innovations in additive manufacturing are required to minimize the after work that needs to be done on the parts after printing.
The real opportunity looks to be having an additive manufacturing machine that is capable of producing all of Toyota’s low volume supply parts that are not subject to the strict Just-In-Time requirements. Eliminating the requirement of tooling seems like the biggest win here. It sounds like there is a case for ‘made to order’ parts for very low volume lines belonging to the out of production vehicles described above.
I really appreciated the problem of having to maintain tooling for components over extremely long periods, the difficulty of changing tooling in the auto industry and the costs this create for suppliers and OEMs alike. The idea of using AM to help address some of these issues is quite intriguing. In addition to some of the issues you mentioned, I believe another topic that would interesting to delve more deeply into with AM is the quality/durability of the parts per unit cost added to the piece price.
Hopefully OEMs like Toyota can continue to invest in these technologies to help bring them mainstream and make them more cost efficient solutions!
Fantastic piece. I’m particularly intrigued by your question around whether Toyota should trust its supply chain to vet new AM technologies, or should move towards a vertical integration model. Given the need, as you point out, to seriously consider migrating to AM in the long-term, I wonder if there’s a third option here. Perhaps Toyota should consider partnering with its supply chain to develop technological capabilities “approved” or “vetted” by Toyota itself to sustain its supply chain in the longer term. This way, Toyota still only maintains responsibility for 25% of vehicle content, but holds greater sway over it’s Tier I Supply Base. Of course, a partnership such as this would depend on Toyota’s willingness to consider long-term contracts and obligations with these suppliers – but this trade-off may be worthwhile for Toyota to use with its best-in-class suppliers given the high up-front costs of developing AM. I’m curious to see how AM continues to develop as the traditional shops in injection molding begin to age out their workforce.
Great explanation of the contrasts between two topics we’ve covered this term. Integrating AM with JIT seems like a logistical nightmare right now, but the technology is improving rapidly. As Andrew mentioned above, it’s on AM manufacturers to improve the technology for widespread factory use, and at a worthwhile price. Still, as you mentioned, there’s a lot of value in developing prototypes using AM, and integrating it in small ways will free up floor space. Great piece!
Interesting point on JIT combined with AM. I would have expected if AM ever becomes real, it would be the perfect manufacturing tool for replacing your external suppliers. AM could effectively reduce the expertise needed for arbitrary parts manufacturing. I’m not questioning this assumption or at least the rate at which it would occur.
Well done! Nicely put questions, and I found them quite valid. However, I still believe that the OEM relationship is hard to break. I once had a client who were the headlight manufacturer for Toyota. I remember the manufacturer was simply investing in a brand new, multi-million dollar facility to just produce the headlights of Toyota’s then-upcoming C-HR model. Given that how those companies see Toyota as their bloodline, I find it very difficult to see how this relationship should be replaced by 3D printing. Not only those companies very much rely on their relationship with Toyota, but they also use the know-how they acquired from Toyota as well as the “Toyota Supplier” brand into their other operations. I would anticipate a lot of resistance against this.
Well written piece! It appears the main driver in all sourcing decisions at this point boils down to cost and time, and in particular projected costs going into the future / how to maintain the competitive edge. I wonder if there are estimates on the timeline of development for AM technologies, and at what point the economics and production times will make sense. As AM technology develops and becomes economically feasible, it would make sense for Toyota to vertically integrate, especially as one of the main functions of suppliers (i.e., holding inventory) will no longer be relevant.
Thanks for an inside look at Toyota and their approach to AM. From your article it seems that as the technology currently stands, it is not a viable solution yet for mass production, i.e. the economies of scale is not reached. For standard cars, I suspect the traditional technology will continue being important, but what are your thoughts on after-sale spare parts? Are there ways that Toyota can partner with its dealers to get spare parts in the hands of its consumers faster? Also the other aspect that they may already be exploring is around customization. Could AM help Toyota customize certain aspects of the car much quickly, thus helping them charge a premium for customization and adding it to their revenue stream?
One of the biggest problem AM is facing right now is the speed of printing. I think your suggestion that auto companies focus on AD only for low volume parts makes a lot sense. Low volume parts still require a huge upfront investment. However, due to the volume of the parts, the company has to charge higher price per part in order to recover its upfront investment cost. it will be interesting to hear if/how Toyota is using AD for prototyping new models? Has this allowed the company to prototype at a faster rate/has led to more innovation?
Thanks for the article Liz! This is a really fascinating topic. After considering your questions, I tend I agree with Sgt. Piggy. I really feel like the best path forward here is vertical integration, at least for certain low-volume units. Additive manufacturing really seems like the perfect tool to replace (or at least reduce dependence on) your external suppliers!
Liz, great article and superb info on how additive manufacturing will transform the auto industry. One concern that I would have is regarding jobs. Having machines creating many of the required pieces, a great concern would be that people would lose their jobs. This is a concern that others have addressed with universal basic income as the answer. How could companies like Toyota rise up to the challenge of passing on certain profits to a UBI fund to offset the lost jobs in an industry? Should they?