3-D printing our way to space?
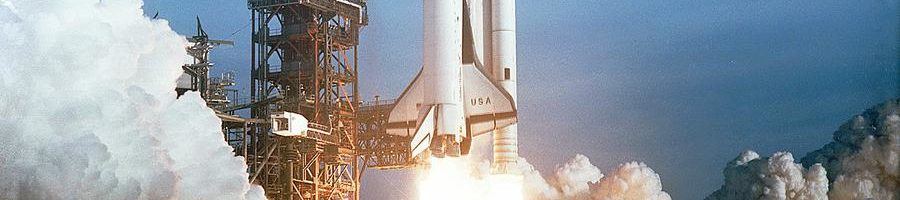
Additive manufacturing has already begun to revolutionize NASA’s R&D processes, but, despite its innovation potential, NASA must be wary of its application beyond developmental processes.
Source: NASA
Additive Manufacturing (“AM”), or 3-D printing, has been primed to disrupt the manufacturing design, prototyping, production and supply chain processes for over 3 decades, but only recently have years of advances begun to find consistent economical applications [1]. For NASA, an organization on the forefront of exploration, the opportunities that AM presents from a design and prototyping standpoint are both ripe and widespread.
First, AM enables structural innovation and the creation of manufactured pieces that simply cannot be produced through traditional subtractive methods (complex geometries and captivity-based geometries) [2]. Second, AM enables the facilitation of wide-ranging, rapid and economical experimentation. It empowers researchers to be nimble in the creation and subsequent testing of prototypes with a range of materials, composites, infills, shapes / sizes, and weight efficiencies [3] [4]. AM enables experimentation to be cost-efficient and time-efficient without the need for third parties and helps tackle the need for innovative, flexible, unconstrained, custom solutions to meet NASA-specific needs and quality requirements [5] [6] [7]. In short, AM has created the opportunity to enhance the product development and product improvement processes at NASA.
The advancement of AM’s application, quality, costs and speed is ever-changing, and, to date, NASA has been on the forefront of applying AM [7] [8]. Successful test announcements from NASA include the successful testing of a rocket engine injector in 2013, the creation of a full-scale copper rocket engine part in 2015, and the production of a copper combustion chamber liner in 2018. In each of these developments, NASA reduced costs materially (up to 70%) and often cut timelines from weeks to days, with additional cost and time-efficiencies on the horizon [5] [9] [10]. Each of these successive prototyping projects built on each other and created unique solutions to challenging problems. These announcements also point to further AM applications at NASA, with the organization noting, it’s now “ready to move on to demonstrate the feasibility of developing full-size, additively manufactured parts” [9].
Given the innovative promises associated with AM, NASA should lean into the use of AM for prototyping purposes; however, it should be extremely cautious when exploring AM capabilities beyond experimentation applications. The cause for caution is amplified when thinking about the “failure is not an option” mantra at NASA and the “unknown unknowns” associated with any nascent technology (no long-term track record) [11].
NASA needs to be keenly aware of the AM’s many challenges. First, quality control and testability are particularly challenging and there are no well-defined standards [12]. AM is a new technology: there is limited knowledge of potential weaknesses, it is unclear whether conventional tests are appropriate for integrity verification, and there are many unknown unknowns about AM in the extreme environments of space [2] [12]. Second, there is significant endurance ambiguity, with the absence of data to understand performance. Third, variability between CAD designs and AM outputs (as well as between different build iterations), needs to be carefully monitored, measured and tested [2] [13] [14]. Lastly, to date, most AM components have been designated for nonstructural and noncritical use cases, which limits the incremental data available for integrated components into mission critical structures and should give NASA pause about the developmental stage of the technology [2].
Looking ahead, NASA should continue to explore the use of AM, particularly in no-stakes, small-scale prototyping phases; however, like its highly incremental approach to exploring the use of AM in space, it should remain cautious and take an incremental approach to considering AM components for mission-related applications [15]. In this pursuit, NASA should be focused on i) working with the International Standards Organization (ISO) to continue to develop standards for AM [16]; ii) sharing industry best practices with corporations to advance AM methodologies; iii) not becoming overly reliant on AM for the production of mission-critical components due to NASA’s own acknowledgement that “gaps exist in the basic understanding of AM Materials and Processes, creating potential for risk to certification of critical AM Hardware” [15].
As seen in 1986 Space Shuttle Challenger disaster and the failure of O-ring seals, one, seemingly insignificant, component can create systemic weaknesses and result in catastrophe [17]. Initial AM research on-earth suggests that critical defects are rare from selected AM samples, but there is little to no data to support measurement, integrity and endurance of AM in space [18]. From all of this, two questions standout for NASA looking forward: 1) what thresholds must be met before NASA uses AM for critical, load-bearing, structural components? 2) should NASA focus resources on the development of “in-space” AM on the International Space Station for non-critical components or are such efforts simply distracting?
[Words: 767]
References:
- Mark Cotteleer, Jonathan Holdowsky, Monika Mahto. “The 3D opportunity primer: the basics of additive manufacturing, Deloitte Insights, Deloitte University Press, 06 March 2014. URL: https://www2.deloitte.com/insights/us/en/focus/3d-opportunity/the-3d-opportunity-primer-the-basics-of-additive-manufacturing.html [Accessed 12 Nov. 2018]
- W. J. Lim, K. Q. Le, Q. Lu and C. H. Wong, “An Overview of 3-D Printing in Manufacturing, Aerospace, and Automotive Industries,” in IEEE Potentials, July-Aug. 2016, 20 July 2016. DOI 10.1109/MPOT.2016.2540098. URL: http://ieeexplore.ieee.org.ezp-prod1.hul.harvard.edu/stamp/stamp.jsp?tp=&arnumber=7517429&isnumber=7517414 [Accessed 12 Nov. 2018]
- Eleonora Atzeni & Alessandro Salmi, “Economics of additive manufacturing for end-usable metal parts,” in Int J Adv Manuf Technol, pp. 1147–1155, 2012. 8 Feb 2012. DOI 10.1007/s00170-011-3878-1 https://link-springer-com.ezp-prod1.hul.harvard.edu/content/pdf/10.1007%2Fs00170-011-3878-1.pdf#page=9 [Accessed 12 Nov. 2018]
- National Research Council. 2014. 3D Printing in Space. Washington, DC: The National Academies Press. PDF ebook, pp.62-71. DOI: https://doi.org/10.17226/18871 URL: https://www.nap.edu/read/18871/chapter/6#64 [Accessed 12 Nov. 2018]
- “NASA Advances Additive Manufacturing For Rocket Propulsion,” press release, May 9, 2018, on NASA website, URL: https://www.nasa.gov/centers/marshall/news/nasa-advances-additive-manufacturing-for-rocket-propulsion.html [Accessed 12 Nov. 2018]
- Matt McFarland, “A Formula 1 team is 3D printing race car parts,” CNN Business, April 11, 2017, URL: https://money.cnn.com/2017/04/11/technology/formula-1-3d-printing/index.html [Accessed 12 Nov. 2018]
- Kelly Marchese, Jeff Crane, Charlie Haley. “3D opportunity for the supply chain: Additive manufacturing delivers
- Driving supply chain transformation,” Deloitte Insights, Deloitte University Press, 02 September 2015 URL: https://www2.deloitte.com/insights/us/en/focus/3d-opportunity/additive-manufacturing-3d-printing-supply-chain-transformation.html [Accessed 12 Nov. 2018]
- “NASA, Industry Test Additively Manufactured Rocket Engine Injector,” press release, July 11, 2013, on NASA website, URL: https://www.nasa.gov/press/2013/july/nasa-industry-test-additively-manufactured-rocket-engine-injector-0/#.W-q4E5NKg2x [Accessed 12 Nov. 2018]
- “NASA 3-D Prints First Full-Scale Copper Rocket Engine Part,” press release, April 21, 2015, on NASA website, URL: https://www.nasa.gov/marshall/news/nasa-3-D-prints-first-full-scale-copper-rocket-engine-part.html [Accessed 12 Nov. 2018]
- Donald H. Rumsfeld, Secretary of Defense, DoD News Briefing, Washington, D.C., February 12, 2002. Transcript provided by U.S. Department of Defense, URL: http://archive.defense.gov/Transcripts/Transcript.aspx?TranscriptID=2636 [Accessed 12 Nov. 2018]
- Roca, J., Vaishnav, P., Mendonca, J., & Morgan, M. (2017). “Getting Past the Hype About 3-D Printing Although additive manufacturing techniques hold great promise, near-term expectations for them are overoptimistic,” MIT Sloan Management Review, 58(3), 57-62.
- Frazier, William E., “Metal Additive Manufacturing: A Review,” Journal of Materials Engineering and Performance (2014), June 2014, Volume 23, Issue 6, pp 1917–1928. URL: https://link.springer.com/article/10.1007%2Fs11665-014-0958-z [Accessed 12 Nov. 2018]
- Wei Gaoa, Yunbo Zhang, Devarajan Ramanujana, Karthik Ramani, Yong Chenc, Christopher B. Williams, Charlie C.L. Wang, Yung C. Shina, Song Zhang, Pablo D. Zavattieri, “The status, challenges, and future of additive manufacturing in engineering,” Computer-Aided Design, Volume 69, December 2015, Pages 65-89. DOI: https://doi.org/10.1016/j.cad.2015.04.001 https://engineering.purdue.edu/ZhangLab/publications/papers/2015-cad-review.pdf [Accessed 12 Nov. 2018]
- National Aeronautics & Space Administration Science Technology Office, “In Space and For Space Additive Manufacturing Initiatives at NASA Marshall Space Flight Center,” PowerPoint Presentation at 2nd Symposium on Additive Manufacturing for Defense and Government, Washington, DC, May 13-15, 2015. Presented by R. G. Clinton Jr., Deputy Manager. URL: https://ntrs.nasa.gov/archive/nasa/casi.ntrs.nasa.gov/20150016177.pdf [Accessed 12 Nov. 2018]
- Naden, “ISO and ASTM International Unveil Framework for Creating Global Additive Manufacturing Standards,” press release, Oct. 7, 2016, on ISO website, URL: https://www.iso.org/news/2016/10/Ref2124.html [Accessed 12 Nov. 2018]
- Report of the Presidential Commission on the Space Shuttle Challenger Accident, vol. 1, chapters 3 and 4, Washington, DC, U.S. Government Printing Office, 1986). URL https://er.jsc.nasa.gov/seh/explode.html [Accessed 12 Nov. 2018]
- Brad L. Boyce, Bradley C. Salzbrenner, Jeffrey M. Rodelas, Laura P. Swiler, Jonathan D. Madison, Bradley H. Jared, Yu‐Lin Shen, “Extreme‐Value Statistics Reveal Rare Failure‐Critical Defects in Additive Manufacturing,” Advanced Engineering Materials, Volume 19, Issue 8, August 2017, April 21, 2017. DOI: https://doi.org/10.1002/adem.201700102. URL: onlinelibrary.wiley.com/doi/pdf/10.1002/adem.201700102 [Accessed 12 Nov. 2018]
I agree that NASA should continue to advance cautiously given the many “unknown unknowns” that impact even a relatively simple component. The risks associated with moving too quickly and using AM for mission-critical components is too high. To your point – no one wants another Challenger disaster. That being said, it could be highly useful for NASA to test the validity of AM in-space on non-critical components. If that is the ultimate goal and their process is incremental by design than they would benefit from starting the learning process earlier. Start small as they have with on-earth components but at least start since gathering data is critical to their steady, gradual approach. The data they gather from in-space AM could also further inform how AM works on earth. Of course, the question of funding for these many projects is another issue entirely and could potentially limit NASA’s ability to test AM both on earth and in space.
I would question the hesitancy of NASA to move forward with AM for mission critical components. I agree that there are many unknowns and high risks associated with this practice, but it would benefit NASA to prioritize studying and derisking these unknowns. The use of AM for mission critical components would have several key benefits, primarily reducing cost of space shuttles. The Space Shuttle Endeavour cost NASA, and therefore tax payers, approximately $1.7 billion [1]. Through the use of cheaper, but reliable, parts from AM could have a significant impact about the amount of government spending on space shuttles and could potentially increase scientific discovery by sending more lower cost shuttles in space.
[1] NASA, “Space Shuttle and International Space Station” URL: https://www.nasa.gov/centers/kennedy/about/information/shuttle_faq.html#1 [Accessed 15 November 2018]
When considering the cost of failure in manned space flight, safety must remain the number one concern for NASA. There are ways to tackle testing and cost saving efforts simultaneously. By utilizing non-mission critical components to target for AM applications, NASA can learn what the weakness or “points of failure” are in the unforgiving environments of launch, near Earth orbit, space, and re-entry of the atmosphere. As these components are analyzed, the way forward for further research and applications will become apparent.
Very interesting application of AM, but I’m a bit disappointed by its incremental approach. In your last paragraph, you describe the failure of a single O-ring and its catastrophic implications. Would the vision someday to have 3D printers in the space station so that they could just print a new O-ring? Obviously given the current nascent state of AM, we would just send a thoroughly test O-ring from Earth. But if we go deeper into space with transport times becoming ever longer and resources becoming more scarce, could 3D printers allow us to be more resourceful further out in space?
Very thoughtful and interesting article!
I’d be interested to know how, if at all, AM technologies are utilized by SpaceX and more broadly by other high-performance industries, such as sports cars, aviation, navy etc? Could there be an opportunity to take some ready and tested techniques from these areas? Conversely, I think it could make sense to look for applications of some NASA technologies to less extreme and more consumer-oriented industries?
To the safety concern point, I think unmanned flights or small open space experiments could help mitigate this risk to some extent. In general, I think it’s important to bear in mind that, although safety cannot be compromised in any way, postponing some AM applications could actually imply a use of less reliable and riskier traditional technologies only because they have well-known threats and limitations.
Interesting read! I am familiar with most of AM’s advantages but “complex geometries and captivity-based geometries” is definitely something I’ve missed in industrial AM. Someone also wrote about Lockheed’s move in AM and maybe the two companies could partner or share best practices to advance AM together? As for thresholds for NASA to uses AM for critical, load-bearing, structural components – I believe it could be used Day 1 as long as it passes all other tests that NASA currently uses to qualify materials. I love the idea to develop “in-space” AM on the International Space Station! As mentioned above, it would be much more handy than waiting for a part to be made and transferred from Earth. I now believe we can fly, further.