Will 3-D Printing Take Us to Mars? Relativity Space Thinks So.
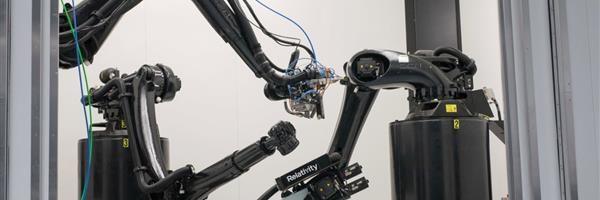
Relativity Space is trying to 3D print a space rocket, and if successful, could revolutionize the space launch industry
Since its invention, additive manufacturing (referred to as ‘AM’ or 3D printing) has captured the attention of many industry observers with its promise of a simplified supply chain: parts would be stored digitally, lead times would be minimized, tooling would be uncommon, and economies of scale would make way for mass customization. Several decades later, there is agreement that the promises of additive have sprinted ahead of what the technology can actually deliver [1], and there is still debate around whether any of those promises will actually materialize in the near future [2].
Believers of 3D printing would argue that in order to make a manufacturing process simpler, one must first shift the complexity into the technologies that enable it. In other words, technologists have been busy building the tools that will enable the simple manufacturing processes of tomorrow. If you adhere to this line of thought, you’d be hard-pressed to find a better example than Inglewood-based Relativity Space. With over $45MM in venture funding to back it [3], the company’s mission is ambitious: to build a space rocket from scratch in only 60 days. The kicker? They want to print it. To do so, they plan to use the world’s largest metal 3D printer, which they are also building [4]. If successful in its mission, the company’s rocket will be almost entirely composed of 3-D printed parts and able to carry a metric-ton payload into lower-earth orbit.
While most traditional organizations are still grappling to understand additive manufacturing and how it affects their process improvement, Relativity’s survival is squarely dependent on their ability to create a fundamentally improved process, that if successful, would allow them to build and fly rockets in an extremely cost competitive way [5]. To achieve this lofty goal, the company has been developing a large robotic, wire-fed, laser-welding 3D printing system named Stargate. The vertically integrated factory uses real-time data and advanced imaging to achieve both a higher throughput and a dramatic reduction in parts, which results in lower costs across the board [6]. Management’s focus in the short term is to deliver the technological innovations that will allow Relativity to outperform traditional manufacturing. Because of this long-term bet on AM, exploring the viability of the company’s strategy is a good exploration of the competitive advantages of 3D printing.
So how exactly does Relativity plan to use AM to design, develop, and build rockets faster than its competitors? First off, AM allows them to reduce total part counts by nearly two orders of magnitude. This not only decreases the overall complexity of the computer-aided designs, but also streamlines production by not requiring the formation of an assembly line. AM can also manufacture the components as a single piece, increasing reliability and reducing the need for more inspection [7]. Secondly, because their AM processes don’t require heavy tooling and the metal-deposition process is much faster vis-a-vis conventional methods, they are able to prototype and iterate much faster. Not only could they reduce the development phase from years to months, but the company believes that Stargate’s build-rate will allow them to produce a 100-foot-tall, 7-foot-wide rocket from scratch in only 30 days (requiring 30 more days for assembly and testing). All of this, combined with the high automation of the system, achieved mainly through collaborative robotics and real-time process controls, could allow them to redefine traditional rocket-building timelines [8].
Relativity’s medium-term objective is to service growing demand for medium-sized satellites by offering space launches for $10 million, compared to the $62 million that SpaceX currently charges on it’s much larger Falcon 9 rocket [9]. Their long-term goal is slightly more ambitious: they want to support long-term human presence on Mars. In the words of their founder, humanity will eventually “want to make rockets [in Mars] to fly things back” and the technology Relativity is developing here on Earth is really a set of “stepping-stones toward figuring out how to do [it]” [10].
Putting aside the future success of the company’s inter-planetary ambitions, what I find most intriguing about Relativity is that while they are certainly taking on tremendous technology development risk, if successful, they could truly revolutionize an entire sector. When it comes to mega-trends such as AM, machine learning, or open innovation, most of the use cases we read about showcase how larger corporations have made incremental changes to their existing processes. While many companies are still trying to fit additive into their strategy, Relativity built its competitive strategy around it. I wonder what other potentially transformative companies could be architected around frontier technologies? If the revolutionary promises of additive manufacturing begin to materialize, which is still to be determined, what other traditional supply chains could be disrupted?
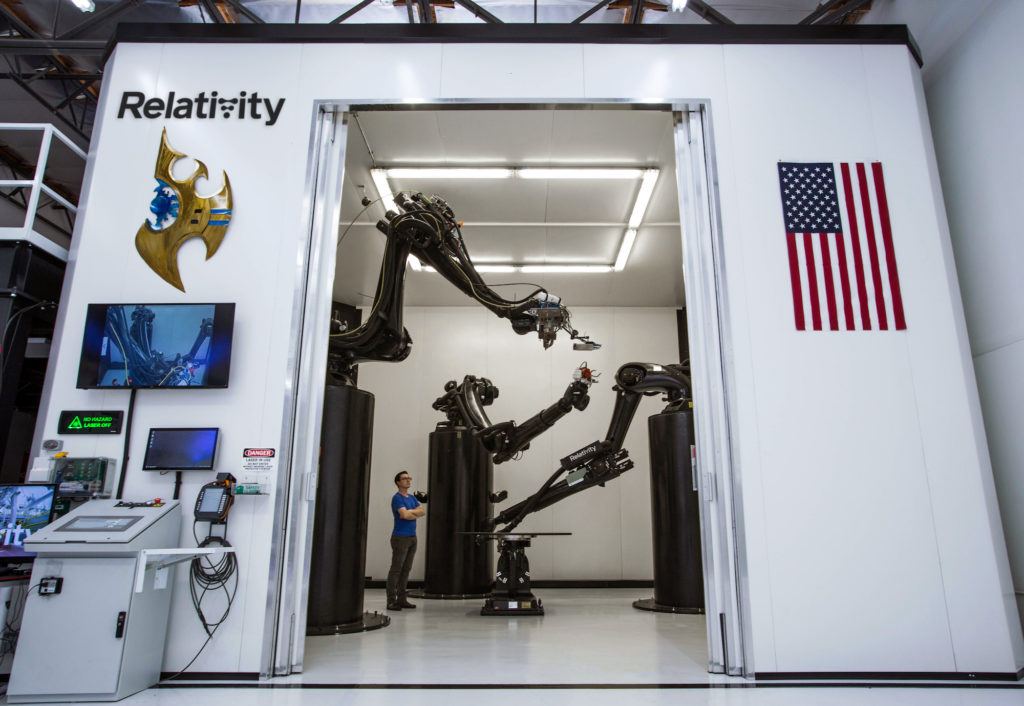
(786 words)
References:
- J.B. Roca et al., Getting past the hype about 3-D printing. MIT Sloan Management Review 58, no. 3 (Spring 2017): 57–62.
- M. Holwef. The limits of 3D printing. Harvard Business Review Digital Articles (June 23, 2015).
- “Relativity Space Raises $35M Series B Funding Led by Playground Global as It Extends Full-Stack Rocket Production Leadership and Reinvents Satellite Launch and Deployment” press release, March 27, 2018, Businesswire, https://www.businesswire.com/news/home/20180327005511/en/Relativity-Space-Raises-35M-Series-Funding-Led , accessed November 2018.
- Masunaga, Samantha. “Entrepreneur seeks to boldly go where no one has gone before: 3-D printing nearly an entire rocket.” Los Angeles Times, April 27, 2018. http://www.latimes.com/business/la-fi-rocket-tim-ellis-relativity-20180427-story.html , accessed November 2018.
- Billings, Lee. “Q&A: 3-D Printing Rockets with Relativity Space CEO Tim Ellis” Scientific American, April 16, 2018, https://www.scientificamerican.com/article/q-a-3-d-printing-rockets-with-relativity-space-ceo-tim-ellis/, accessed November 2018.
- Relativity Space. “Stargate.” https://www.relativityspace.com/stargate/, accessed November 2018
- C.W.J. Lim, K.Q. Le, Q. Lu, and C.H. Wong. An overview of 3-d printing in manufacturing, aerospace, and automotive industries. IEEE Potentials 35, no. 4 (2016): 18–22.
- Ibid.
- Masunaga, “Entrepreneur seeks to boldly go where no one has gone before: 3-D printing nearly an entire rocket.”
- Billings, “Q&A: 3-D Printing Rockets with Relativity Space CEO Tim Ellis”
This is a very cool application of additive manufacturing, and I am keen to see whether the company will be successful in its venture. Even if its rockets don’t work, however, the successful development of the largest metal 3D printer could in and of itself become the company’s main product, so there may be potential for Relativity outside of space travel too.
It’s worth pointing out that it isn’t clear from the article whether Relativity’s 100-foot-tall, 7-foot-wide rocket is intended for orbital or suborbital launches, though obviously the company’s ambitions for interplanetary transport implies an eventual goal for the former. For reference, SpaceX’s current orbital launcher is the 233-foot-tall, 12-foot-wide Falcon 9, while Blue Origin’s still in development orbital launcher is the 313-foot-tall, 23-foot-wide New Glenn. SpaceX’s Falcon 1 was a much smaller orbital launcher that was scrapped in favour of the Falcon 9 due to the former offering worse economics to the company than the latter. (On the other hand, Blue Origin’s much smaller New Shepard is meant for suborbital launches.) It will be interesting to see how and whether the economics of the business of space will permit such a launcher size in the market.
Although the use of 3D printing already permeates industrial sectors such as aerospace, automotive, and manufacturing, I believe the benefits are even greater in the healthcare space, where a reduced time to develop and produce certain parts at a lower cost can have a significant impact on patients’ lives. An article I was reading mentioned that some key parts of the human body, such as a trachea, can already be 3D printed using “biocompatible and bioresorbable materials”, and in the future they expect to be able to “produce heart tissue, cartilage implants (for noses, ears, knees and vertebral discs), skin grafts and even corneas”. In a world where time is of the essence, a reduced “supply chain” timeline for organ transplants could actually save lives. Additionally, in response to rising Healthcare costs, companies like like OpenΒionics, an open-source initiative for the development of affordable, light-weight, modular robot hands and prosthetic devices, are using 3D printing to change the game: “robot hands cost less than $100 and weigh less than 200g while their new anthropomorphic prosthetic hand costs less than $200 and weighs less than 300g.”
https://www.3dprintingmedia.network/ways-3d-printing-impacting-world/
And circling back to the topic at hand (space travel)… another benefit of 3D printing is being able to create items in hard-to-reach places. I wonder if we’ll ever see a day where food can be 3D-printed in space to address the challenge of supplying enough food on space missions and ventures?
Very interesting article, while it seems to me that their ideas here are highly ambitious and that additively manufacturing an entire spacecraft seems unlikely in the short to medium term. However, it is encouraging to see a company betting the farm on AM, outside the realm of simply producing printers for commercial sale. I would guess that what will end up coming of this will be improvements and insights into different methods of printing and a great knowledge base regarding new design methods that could be applicable throughout the aerospace sector.
Very interesting article – think you did a good job explaining the benefits that AM offers in this model.
I hadn’t thought about this before, but it seems to me that current AM technology is particularly attractive to the aerospace given A) the large size of the products (because miniaturization adds complexity) and B) high manufacturing complexity / cost.
One aspect of Relativity’s model that I’m skeptical of is their proposed pricing. Charging 1/6th of the current low cost provider seems overly aggressive to me, especially in a market like satellites, where overall market demand probably isn’t all that price sensitive (hard to imagine that the world launches >6x as many state lites if they only cost $10M vs $60M).
This was a very interesting read! The idea of using AM to build what is still pretty much out of reach for the average person creates makes what RS is doing even more intriguing. In addition to the space exploration piece, their potential learning and success could be a huge disruptor for the travel industry (air and land) on Earth. We’d be able to much more quickly produce changes to our transportation infrastructures therefore solving many of our current problems such as deadly accidents, pollution, energy consumption to name a few.
I really liked reading this one – thanks Mario. This application of AM seems strange to me. As I understand it, the advantage of AM over traditional approaches to product assembly (apart from the supply chain benefits that you mentioned) is that AM lowers the cost of building one of something – so prototypes and customization are both cheaper. Once Relativity has a working rocket that uses ~100x fewer parts that what SpaceX is doing, why can’t someone else build rockets the same way?
Thanks for the article Mario, I really enjoyed it and I didn’t know you were a fan of the space industry. There are a couple of questions that I had while reading the article:
1. How will the company address gravity, atmosphere and materials restrictions if it plans to, at some point, send its 3d printers to Mars where it could print rockets to send things back?
2. How is the company planning to compete against rockets with full re-usability, like the Big Falcon Rocket that Space X is working on, which plans to have a cost of $7M per launch with a much higher load capacity. Is Relativity thinking about building reusable rockets at some point? Are there technical restrictions? Will Space X be interested in acquiring Relativity to incorporate its AM techniques?
Thanks for the article. Here is the source of the $7M per launch I found so we can discuss later.
https://www.nextbigfuture.com/2017/10/spacex-bfr-to-be-lower-cost-than-falcon-1-at-7-million-per-launch.html
Extrapolating on my limited from hardware product development experience, I would think that in the future, the person/company with the best 3D printer wins the manufacturing game. Ideally the manufacturing will be mostly commoditized that the differentiating factor will be 1. who has the better design and 2. who owns the bigger(better) 3D printer. It is still uncertain how it will pan out, but one could imagine a world where everyone owns a 3D printer at home and download the design file and print stuff out. Only the raw material to be fed into the 3D printer will be delivered to your house. Thank about it: 3D printers printing 3D printers!
Imaginations aside, I would think that the best way to shorten the development period and the associated cost is to apply AI to the engineering design phase and run as much test as possible, ideally simultaneously, to come up with a design that would require minimal prototyping and testing.
This is an extremely well written article as you explained complex ideas in a simple manner to comprehend. This article has pointed out a very interesting point as we set very challenging and ambitious goals it tends to accelerate the development of technology tremoundsly. As mentioned in the case with SpaceX or even if we go back to Kennedy’s mission of choosing to go to the moon. Relativity’s goal is clearly ambitious and as society we will learn a lot about 3D printing as they push the edges of the field. I believe another industry that could be transformed in a similar matter is the real estate construction industry. If we think of the ways buildings are being constructed it is a very tedious and inefficient process. In theory could we 3D print a building? This is a major question. Today some real estate firms are trying to move towards modular buildings where you produce some of the units in factories and just do the assembly on site instead of constructing everything on site. But 3D printing a building would required creating printers on a completely new size and scale and is definitely a challenge worth exploring!