The Mahindra Group: Driving towards India’s Digital Automotive Age
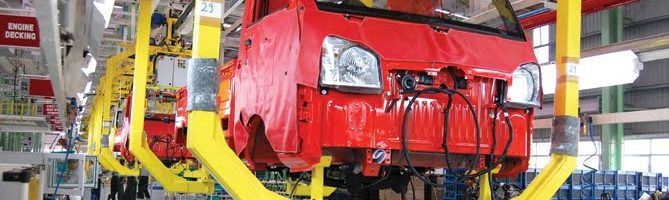
Can Mahindra and Mahindra’s new Connected Factory successfully help it cross the chasm of the automotive revolution?
India has emerged as an important global automotive market and offers huge growth potential due to low vehicle penetration and improving economic fundamentals. The sector accounts for 7% of India’s GDP and employs about 19mn people. [1]
Mahindra & Mahindra
Mahindra & Mahindra (M&M), part of The Mahindra Group, is one of the largest vehicle manufacturers by production in India. It produces and sells over 500,000 units per year across SUVs, tractors, pickups, commercial vehicles, and motorcycles.
Connected Factories in Industry 4.0: Digitalization of Automotive Manufacturing
Over the last decade, several new technologies have disrupted the automotive manufacturing process, none as much as the Industrial Internet of Things (IoT) creating a connected factory environment. IoT-driven manufacturing allows real-time operation by continuously tracking processes and resources.
Concerns at M&M
M&M has for long enjoyed a prime position in the Indian markets. However, with markets slowing down internationally, global automotive players are seeking new markets, with India a lucrative target. The entrant of global suppliers with deeper pockets, digitally enabled supply chains into a competitive market with a large range of products, for an extremely price sensitive customer, has created a strong pressure on M&M to have a hyper-efficient plant that is also flexible to meet changing customer demands – providing extreme flexibility with mass production capabilities. However, for Mahindra, moving from a traditional setup to a digitalized supply chain requires not only an empowered top management to execute the vision, but also a significant investment in research and technology.
There are three key trends that are influencing this transformation at Mahindra:
- Capacity to capability: Manufacturing flexibility is critical to respond to variable market demand
- New production models: M&M will look to move from a make-to-stock approach to embrace more make-to-order, configure-to-order, and engineer-to-order production models.
- Workforce engagement: People will continue to provide decision-making capabilities to handle increasing operational complexity. These higher levels of collaboration have a critical need to build a seamless man-machine information flow. [3]
M&M Opens the ‘Factory of the Future’
M&M invested $3Bn to deploy a Connected Factory of the Future in Chakan, Pune, India. Built with a vision of “connecting the top floor to shop floor”, the plant is automated with IoT and Cloud technologies and can seamlessly manufacture 40 models using a new generation of systems that enable real-time, automatic interactions among machines and assets.
- The Connected Engineering framework enables the acquisition of data from all the connected sources:
- Track & Trace connects all of the 20,000 tools on the shop floor to determine the location to an accuracy of 30 cm. [4]
- All tools relay real-time information to a central database and can be remotely programmed and provisioned for specific tasks.
- Real-Time Manufacturing and Maintenance
- Analytics on the stored data provide insight on key parameters and ensure quality and conformance to stringent regulations.
- Any disruption in manufacturing is quickly identified. Real-time control systems help in routing and tracking of vehicles as well as in quality assurance and equipment performance monitoring. [3]
Results of the new factory
Compared to other plant rollouts, M&M achieved:
- Changeover time reduction
- Lower defect rates and early fault detection and rectification
- Improved and centralized reporting for complete measurability and controllability [3]
Thinking About the Future
The next challenge is to seamlessly integrate the robots with shop floor in a scalable model. To this effect, the company is looking to leverage its research arm, Tech Mahindra, by launching a Factory of the Future Lab which is primarily involved in bringing down the cost of robotic operations, which is at $6 per hour currently. [5]
Recommendations for M&M management
- Transforming at Scale: A new factory can only serve as a prototype – technological integration is always a challenge at scale. M&M will have to upgrade existing facilities while continuously running them. They should now build IoT implementations that work with and on top of existing equipment and enterprise systems. It is important that there is a framework that can facilitate communication and be adaptable to different ecosystems with minimal cost implications. Further, M&M should add not only the flexibility of technology to accommodate increasing variety of products but also the adaptability of existing products into new supply chain models
- Predictive Analytics: M&M’s supply chain has traditionally been reactive. They need to integrate machine data with performance analytics to introduce proactive maintenance hence reducing downtime
- Connected vehicles: M&M should now leverage this framework for customer delight through connected vehicles that can enable service provision and maintenance management through onboard diagnostics.
Key Questions
- When future planning, how should M&M account for disruptive manufacturing technology such as 3D printing?
- With mechanization of processes, M&M will be downsizing labor. How should a company of this magnitude execute the downsizing while avoiding any backlash or reputational damage?
[796 Words]
[1] “Making India A World Class Automotive Manufacturing Hub”. 2017. Ey.Com. http://www.ey.com/Publication/vwLUAssets/EY-making-india-a-world-class-automotive-manufacturing-hub-1/$File/EY-making-india-a-world-class-automotive-manufacturing-hub.pdf.
[2] Berttram, Philipp, and Stefan Schrauf. 2017. “Industry 4.0: How Digitization Makes The Supply Chain More Efficient, Agile, And Customer-Focused”. Strategyand.Pwc.Com. https://www.strategyand.pwc.com/reports/industry4.0.
[3] Holmes, Christopher. 2017. “Designing And Implementing The Factory Of The Future At Mahindra Vehicle Manufacturers”. Cisco.Com. https://www.cisco.com/c/dam/en/us/solutions/collateral/industry-solutions/idc-manufacturing.pdf.
[4] “Digital Transformation With The Internet Of Everything”. 2017. Iottalent. https://www.iottalent.org/sites/default/files/digital-transformation-with-the-internet-of-everything.pdf.
[5] Hector, Darlington. 2017. “Smart Manufacturing: With Factory Of The Future Lab, Tech Mahindra Places A Futuristic Bet”. The Financial Express. http://www.financialexpress.com/industry/smart-manufacturing-with-factory-of-the-future-lab-tech-mahindra-places-a-futuristic-bet/612503/.
Impressive results from the roll out of a radical new system for the company; the story very easily could have been about the all-digital catastrophe in the plant at Pune.
You raise some very insightful questions. With regards to 1), my understanding of the market is that we are a long ways off from mass market 3D printing for low-end passenger vehicles, particularly for any metallic parts. While such technology, for now, is too slow and too expensive, it may very well become an issue within the life of the plant of 20-30 years. 2) The best way to cope with reputational damage from layoffs is to avoid them in the first place. M&M should be thinking now about re-education or labor re-allocation programs so that current employees can be retained.
I disagree with the point above that the onus is on Mahindra & Mahindra to re-educate or re-allocate the labor most efficiently. It would be unrealistic for the firm to take that on, as I would expect either an efficient labor market or government regulation to take on ownership of a problem of this scale. However, the point still stands that perception is extremely important as it concerns public relations. The best thing that M&M can do is treat the employees with the respect that they deserve while giving generous severance packages and contracting a specialized firm to provide outplacement services for the employees. It is important that the company maintain a respectfully unapologetic external front in case of future needs for lay-offs and for it to do these reorganizations in one fell swoop where possible rather than a “death by a thousand cuts” scenario.
M&M’s Connected Factory of the Future is quite impressive. I would love to learn more about the resources and analytics technology employed to derive actionable insights from their data.
The rise of IoT driven manufacturing creates a wealth of new data. But how difficult is it to make sense of that information? Some companies, like SAP, are creating software for supply chain control towers to help tackle this challenge. [1] It will be interesting to see how companies like M&M approach the issue.
[1] https://www.forbes.com/sites/stevebanker/2014/04/10/the-new-sap-supply-chain-control-tower/#4989a9496097
Nicely written article! One concern that I’d imagine is top of mind at Mahindra is the increasing exposure to cyber risk that their plants will bear as they become increasingly reliant on a digitized supply chain. The author provides several useful recommendations to management regarding making the supply chain less reaction through the use of predictive analytics – and I’d suggest that management should be equally focused on hardening the supply chain process to protect against disruptions from hackers and other malicious software. The company should have contingencies in place to cope with unexpected shutdowns, potentially carry additional inventory in safety stock as a buffer, and possess a robust insurance coverage.
As to the points above on labor, I think there can be a middle ground. Of course the aggregate number of workers is likely to be lower, and the firm cannot bear the entire responsibility of retraining and allocating these workers – that will be a problem for society to figure out. But, at least so far as we know today, humans will still need to be involved in the manufacturing process and to interact with the machines. Therefore I’d suggest Mahindra management should absolutely be focused on a level of re-training sufficient to ensure it has a supply of workers capable of executing these more advanced tasks.
The Mahindra group is making a clear push towards improved efficiency and lower per unit cost by leveraging advancements in digital production tools. I assume that they are using the data collected from the location of assembly line tools to streamline their movement and ultimately increase their utilization. It was very interesting to learn about the differences between Industry 3.0 and 4.0 over the last few decades. However, I was surprised that the usage of robotics was a next step for this organization.
The recommendations put forth were concise and accurate. Point 1 regarding the scalability of such a capital-intensive model is particularly relevant. I do wonder how readily Mahindra can update traditional factories as opposed to starting from scratch.
Following up on the first key question, 3D printing will certainly continue to be used and grow as a proportion of manufacturing methodologies. I would recommend Mahindra should get ahead of the trend and integrate it into their processes as much as possible today.
Thank you for sharing this wonderful example of Industry 4.0 put into practice in the Indian auto industry.
While it was interesting to learn about how digitization helps to connect the key elements of the manufacturing process within the factory, I think another critical aspect of digitization / Industry 4.0 is the integration of the manufacturing process with the ordering and sales process. This is especially relevant in the context of “made-to-order” as you mentioned in the article. Historically, the CRM and ERP systems of a company are designed and deployed separately from the manufacturing system, making it difficult for the customer orders, order specs and product sales information to be flow into the manufacturing system seamless and for the manufacturing process to be adjusted and optimized accordingly. What has Mahindra done in this area and how effective has it been?