The Bouygues Group: will additive manufacturing disrupt the construction industry?
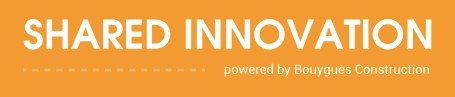
The Bouygues Group recently partnered with Nantes University to create one of the first 3D printed homes. How will additive manufacturing affect the construction industry going forward, should incumbents be worried, and what can they do to defend against these threats?
The Bouygues group is a large, diversified company in the construction industry who regularly win contracts for many high-profile civil and commercial construction projects around the globe, including large underground tunnels, bridges, high-rises, hospitals, and major highways.[1] They recently partnered with the University of Nantes to produce one of the first ever houses using additive manufacturing. I believe this was an excellent partnership and is an example of what they and other large construction companies should increasingly do to remain competitive into the future.
Why might additive manufacturing relevant to the construction industry?
Additive manufacturing (AM) has been adopted in many applications in architecture and design, but the construction industry has yet to see huge strides using the technology. This does not mean, however, that the industry is not ripe with potential applications. According to some industry analysts, 3D printing is expected to disrupt the construction industry by the late 2020s by both lowering the turnaround time of construction and reducing the labor needed in a labor constrained market.[2] But 3D printing is still in the very early days and limited to small-scale projects that have yet to be commercialized. One academic study comparing additive manufacturing to traditional pre-cast fabrication construction suggested that 3D printing may not actually be faster.[3] So how relevant is AM to the construction industry?
According to a BCG report titled “Will 3D Printing Remodel the Construction Industry?” a compelling argument is made for the potential application of AM in construction. The report illustrates how the value proposition of 3D printing aligns closely with the challenges faced by the construction industry. For example, the construction industry has long been a tight margin industry, and one that is highly dependent on speed of delivery. The exhibit below further outlines how the characteristics of 3D printing align well with the construction industry.[4]
What is Bouygues management doing to address the threat of additive manufacturing?
In 2016 Bouygues Construction added “Shared Innovation” as a new tagline for the company and shortly thereafter, in September 2017, the group partnered with the University of Nantes to produce one of the first ever houses using additive manufacturing (see photos below).[5] As opposed to many other experimental homes produced using 3D printing which were limited to one or two bedrooms, the YHNOVA house was a five-bedroom, 95 square meter (1022 sqft) facility which will shortly have actual tenants.[6] Despite this investment in a commercial application in the residential market, however, there is no additional evidence that Bouygues is investing in broader applications of AM in the various industries they play in, such as civil, industrial, and commercial markets.
What other opportunities in AM should Bouygues (and other large construction firms) consider?
There are two additional opportunities which the Bouygues management team, as well as other management teams of large established construction firms, should consider pursuing.
The first opportunity is to invest heavily in research and development internally of AM capabilities. This space is new and emerging, and large opportunities exist for any companies which are willing to make a commitment and advance the field. However, established firms often have difficulty “disrupting” themselves, and ideas that could threaten the established business need room to grow. For this reason, I would recommend they create a separate group to oversee and develop these applications. Establishing a separate division or even a separate company allows the business room to grow.
A second opportunity is to invest in startups who are pushing the frontier of additive manufacturing in the industry. For example, the leading manufacturer or homes in the U.S., D.R. Horton, recently participated in a $9M series A round for ICON – a Texas based firm developing AM technology for the construction industry.[7] Because the technology is so new, an investment strategy is an excellent way to place bets in promising new technology in the sector.
Key questions moving forward
- Is it realistic to expect that additive manufacturing can disrupt the construction industry?
- Should established construction companies invest in internal R&D, or should they simply bring the capabilities internally once the technology is proven (either through acquisitions or hiring talent)? What are the tradeoffs of the two approaches?
(721 words)
[1] https://www.bouygues-construction.com/en/page-historique/65-years-build
[2] https://www.quantumrun.com/company_profile/future-of-dr-horton/16054
[3] Krimi, I., Lafhaj, Z., & Ducoulombier, L. (2017). Prospective study on the integration of additive manufacturing to building industry—Case of a French construction company. Additive Manufacturing, 16, 107-114.
[4] https://www.bcg.com/en-us/publications/2018/will-3d-printing-remodel-construction-industry.aspx
[5] https://blog.bouygues-construction.com/en/en-direct-des-chantiers/imprimee-en-3d-la-maison-yhnova-a-ete-inauguree/
[6] http://batiprint3d.fr/en/
[7] https://www.housingwire.com/articles/47196-dr-horton-invests-in-tech-focused-builder-that-can-3d-print-a-house-in-24-hours
Justin, I really enjoyed reading your article as it shed light on a trend in an industry that I was unaware of. I particularly enjoyed your second question, “should established construction companies invest in internal R&D, or should they simply bring the capabilities internally once the technology is proven?” In response, I would argue that construction companies should invest in internal R&D before the technology is proven. If Bouygues Construction were to wait for the technology to be validated, there is a good chance it would lose its competitive edge and would not be able to catch up to its peers, such as D.R. Horton. Taking a risk and incorporating the technology now, either through an acquisition or hiring talent, has the potential to have significant payoffs down the road. I would also argue that being a first mover or early mover in this case is the best way for Bouygues Construction to solidify itself as a 3D printing player in the construction landscape.
Thank you Justin – this article was very enlightening on a topic I wasn’t familiar with! I like that you highlighted M&A as a strategy that large, established construction firms could use to build these capabilities. This approach seems much more practical that building R&D in-house, given how difficult it would be to attract the right engineering talent for construction firms that aren’t generally thought of as “innovators.” I would be interested to further explore the social good that could come from this lower cost, faster to produce housing – it sounds like this has the potential to reduce homelessness, particularly in developing regions and cities with out of control housing markets.
This is such a cool application of additive manufacturing, and great to be able to see what the concept looks like in practice. I agree that there is a tension between internal R&D vs. acquisition. Given the benefits that additive manufacturing offers in the construction industry, I would argue that it is imperative Bouygues invests in developing and designing their own process for 3D printing.
Beyond advancing the field and getting ahead of competition, the technology could help to reduce current costs to the business. Although the technology is still in its infancy, any investments in developing 3D printing could be used immediately to supplement current processes. I don’t think the company needs to wait for the perfect application, or for the technology to mature, but rather introduce parts of the 3D printing technology slowly into the current building cycle. An entire 3D printed home is an interesting test case, but I think the more interesting piece of this application is how companies can use the technology piecemeal to reduce labor or resource intensive parts of the construction process, making the entire project more efficient overall.
Thanks Justin!! You bring up very interesting points. To your question of “how realistic it is for AM to disrupt the construction industry”, I think that the answer is heavily dependent on which market and which geography we are talking about. Construction tends to boom in countries with younger demographics, and typically, these countries tend to be rather developing nations. There are two main challenges in trying to disrupt the construction market in developing countries. First, housing is usually a very politicized sector due to the number of jobs that it generates for the “bottom of the pyramid”. Consequently, low-income housing tends to be subsidized by the government, making it harder for AM construction to compete. Additionally, the labor cost of construction workers in such nations is really low. Hence, the advantage of reducing labor would not be so high on a cost basis. Nonetheless, the housing market in developed countries is still very large, and probably much more feasible to disrupt due to the lack of the two factors mentioned above.
Thank you for the insightful read and the interesting questions, Justin. To your first point, I am confident that AM can disrupt the industry by massively lowering construction costs. Illustratively, according to press releases, there is a Chinese company, WinSun, that completed 10 homes in one day with 3D printing at a fraction of the cost of traditional construction. In light of this, I would even argue that AM could be an answer to housing affordability and homelessness problems in countries around the globe. In closing, another interesting question worth considering is, as machines replace humans for assembly work, how will the labor force be impacted? My hypothesis is that people skilled in technology, programming, and engineering will remain in demand, but the potential detriment to blue-collar factory workers could be severe.
Thank you Justin for this article on a great French company! You shed light on a topic that I was not too familiar with. Because Bouygues is a conglomerate I am wondering if they could use additive manufacturing in some of their other businesses. In fact, beyond Bouygues Construction they also have a real estate, a rail road and a telecom / media businesses. My question would thus be can they start using AM in these other businesses and will it also be a source of disruption in these other markets?