PlanGrid – Digitizing Construction
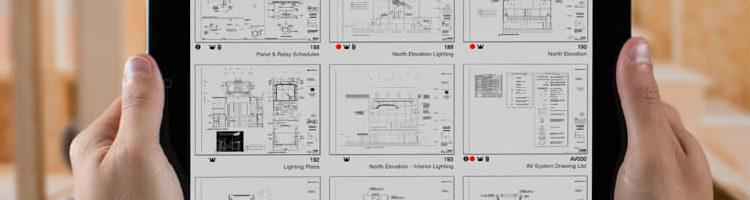
How PlanGrid is changing information flows by bringing technology into the construction site.
Construction Industry
The construction industry has lagged the general economy in improvements in labor productivity and is among the least digitized segments of the economy. It employs nearly 10 million people in the US (6.5% of the labor force) and is thus a significant contributor to overall labor productivity statistics [1]. The industry is at the heart of the question of whether and how industrialized economies and companies can solve the puzzle of declining labor productivity which, for the first time since the 1980s, has turned negative [2].
This is coupled with a growing recognition of the need for infrastructure investment, particularly in the US. A recent report by the American Society of Civil Engineers gave US infrastructure a D+ grade, arguing that upwards of $3.3T investment will be required between 2016 and 2025 in order to maintain and improve the country’s roads, highways, bridges, airports and buildings [3]. The US can expect a $4T hit to GDP if it continues to underinvest in infrastructure, due to everything from lost sales, higher costs and depressed incomes [4].
But a funding gap of $1.4T and the underlying lack of productivity in the industry make hitting these targets a Herculean task. When McKinsey surveyed the construction industry, it found that large projects are, on average, 20% past schedule (20 months) and 80% over budget [5]. Three main drivers for these problems are poor organization and information flow, poor issue tracking, and inadequate communication and consistency in reporting.
PlanGrid
Tying each of these root causes together across stakeholders in the value chain are project blueprints and specifications. This is the primary way that asset owners, designers, architects, general contractors and subcontractors communicate, which to-date remains through physical paper and printed materials. About 3% of all construction project costs are material costs for paper alone, as even minor updates to specifications or layouts require reprinting and distribution to stakeholders. In the field, this entails significant information delays and results in re-work costs of 10% of total project costs. Further compounding the costs of re-work are labor costs that range from $60-$120 per hour for skilled contract work. [6]
This is the problem that PlanGrid is seeking to solve, primarily for contractors who bear the brunt of these cost overruns and productivity declines. The company has created a mobile first platform designed for iPad and Android tablets that allows for contractors, architects and asset owners to dynamically update blueprints in the field. In addition, it allows for two-way collaboration between field workers and project managers, vastly increasing the responsiveness of key decision makers to problems on the ground. This has changed the traditional top down nature of information flow to one that allows for bottoms up adjustments to design implementations. Information flows to the end customer as well, who is able to monitor projects in real time and communicate directly with project managers via the platform. All of these exchanges are then documented via the system, providing contractors a more robust audit trail that minimizes risk and poor quality claims from customers.
Contractor as Partner
When Stanford University Health Care was considering contractors for its new South Bay Cancer Center, it decided to go with a bid from Turner Construction largely in part because of the cost, time and transparency advantages the company had gained from using PlanGrid’s software. It saved $114,000 (30%) on its construction budget through a reduction of over 780 labor hours, paper purchases, and rework costs [6][7]. Considering the average project runs 80% over budget, and that contractors absorb most of those excess costs, Turner Construction was both able to bid more competitively while simultaneously improving its operating margins.
PlanGrid’s technology has helped to change the nature of the relationship between project owners, architects and contractors from a service model to a partnership model. This is from an increase in information transparency and a reduction of the traditional frictions caused by lags between design and specification changes and information flows.
By changing this dynamic, the company has opened up opportunities to expand beyond a project’s construction phase to the full lifecycle of operation and maintenance support. Doing so will require competing against a cottage industry of specialized software applications, many created internally by developers and asset operators. The company has made its first step towards this expanded role by creating an open API for developers to integrate its functionality into 3rd party applications, but a full scale product suite is still forthcoming. The sooner the company can build out its offering, the more likely it is to sustain its position with contractors and increase the stickiness of customer relationships.
Word count: 769
[1] “Total employed persons in the U.S. in 2015 by industry”. Statistia Statistics Portal. https://www.statista.com/statistics/200143/employment-in-selected-us-industries/.
[2] “The mystery of weak US productivity”. Edward Luce. May 29, 2016. https://www.ft.com/content/315f8b88-2364-11e6-9d4d-c11776a5124d.
[3] “Failure to Act”. American Society of Civil Engineers. May 2016. http://www.infrastructurereportcard.org/wp-content/uploads/2016/05/ASCE-Failure-to-Act-Report-for-Web-5.23.16.pdf.
[4] “US infrastructure decay forecast to cost trillions.” Sam Fleming. https://www.ft.com/content/6aa759f8-16c0-11e6-b197-a4af20d5575e.
[5] “Imagining construction’s digital future”. Rajat Agarwal, Shankar Chandrasekaran, and Mukund Sridhar. June, 2016. http://www.mckinsey.com/industries/capital-projects-and-infrastructure/our-insights/imagining-constructions-digital-future.
[6] PlanGrid internal sales pitch document. October 2016. https://docs.google.com/presentation/d/1Q5FECA9RNwx-U3Rqk-wqMvY4_pQZ3SMm_tV-sA56Hqs/edit?ts=582c95ee#slide=id.g13ebe1cbca_1_37.
[7] Phone conversation with Jon Monfred, Sales Representative at PlanGrid. November 15, 2016.
Adam, very interesting article! It sounds like PlanGrid could be beneficial for all stakeholders in the construction process. However, given the last paragraph of your article, I wonder how much effort and investment would be needed for a firm to transition over to PlanGrid. Even if Plan Grid was able to make a more robust suite of offerings, would firms be hesitant to change over to the new system due both the riskiness of committing to a new system and the investments necessary to train employees on the new system? I wonder if its possible for current software providers to simply make a version of PlanGrid for their own platform, thereby convincing customers to stay with their current system while supplementing it with a program similar to PlanGrid.