JD.com – Smart Warehousing For The Future
As the express delivery market grows rapidly, JD.com is investing in smart logistics capabilities to meet demand.
E-commerce companies like JD.com are well-positioned to continue growing rapidly as more and more consumers do their shopping online. However, with this shift towards online shopping also comes increasing customer expectations for express shipping and delivery. Today’s customers expect to receive their items within days and sometimes even hours. In China, this market is growing particularly rapidly as the number of express deliveries reached 31 billion in 2016 and has been growing at an annual rate of more than 50% in the last five years.[i] The supply chain infrastructure required to service these customer’s expectations is incredibly expensive and can be slow[ii] – this is where the use of intelligent technology to automate warehouse processes comes in. For the management of JD, warehouse automation presents an opportunity to significantly cut down the company’s logistics costs while also speeding up delivery time and improving accuracy. In fact, studies have shown that companies with highly digitized supply chain operations can typically expect efficiency gains of 4.1% annually and revenue gains of 2.9% a year.[iii] As demand for express delivery and online shopping continues to skyrocket both in China and around the world, the survival of these ecommerce companies will depend on how successful they are at automating their logistics processes to meet consumer demand. Not only is automation a source of competitive advantage for these companies, it’s necessary for the future.
JD has been a market leader in the intelligent logistics sector, already having invested significant amounts of money in drone and driverless deliveries. The company is doubling down on its efforts in the automation space. This year, JD quadrupled the size of its Silicon Valley research and development center to 120 people, and it set up the JD Logistics division to focus specifically on trucks, delivery people, warehouse, robots and drones.[iv] Just this past September, JD debuted its first fully automated sorting center outside Shanghai. The center utilizes an intelligent equipment management and control system that loads and unloads goods with unmanned automated vehicles and does the work of approximately 180 human workers. Parcels are transported around the facility on an automated conveyor belt. The entire facility processes about 9,000 parcels per hour, which is about four times the capacity that traditional human-run sorting centers can process.[v] The company’s goal is for the majority of its logistics processes to be intelligent in the next 12 years, and it is taking steps in the shorter term, with its R&D investments and continued buildout of smart warehouses, to reach that more long term goal.
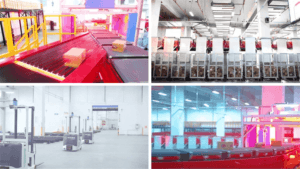
As JD’s management continues its push into automated and intelligent warehouses, I would recommend that the company also focus on building out certain internal and external capabilities to enable their smart supply chain to be more successful going forward. The “smart” transformation of the supply chain represents a significant change for the entire company and impacts the organization and processes by which the organization works. The most obvious consequence of automation is the loss of jobs,[vi] and it will be important for JD to spend time educating its people on the implications of the new technology in order to help them understand how they can best add value in the new environment. While a number of people will unfortunately lose their jobs, there are still opportunities for workers to pivot into different roles at the company. In addition to communicating and educating its people, JD will need to establish a new set of processes and criteria for hiring, performance management, and ways of working to adapt to its new business focus. The new workforce will need to be comfortable with technological change and capable of working cross functionally. The way performance is measured and evaluated will have to be changed as well to align more closely with the company’s vision of achieving automation. Externally, JD will need to partner more closely with its merchants as its own supply chain success is dependent on the success of the entire supply chain ecosystem.
A couple of open questions to think about further:
- What exactly will the role of the human worker be once warehouses become fully automated?
- Is there a limit to how much automation is optimal for a warehouse – is some human involvement still beneficial in the delivery process?
Word count: 800
[i] Fan Feifei, “JD.com opens first unmanned sorting center,” China Daily, August 3, 2017. http://www.chinadaily.com.cn/business/tech/2017-08/03/content_30338693.htm
[ii] Hiawatha Bray, “Robots taking over in warehouses,” Boston Globe, May 1, 2017. https://www.bostonglobe.com/business/2017/05/01/robots-taking-over-warehouses/PV9i4ZDvBc9mtHSSAvRGjJ/story.html
[iii] Stefan Schrauf and Philipp Berttram, “Industry 4.0: How digitization makes the supply chain more efficient, agile, and customer-focused,” Strategy&, September 7, 2016. https://www.strategyand.pwc.com/reports/industry4.0
[iv] Steven Millward, “Chinese ecommerce giant shows off its first ever robot warehouse,” Tech in Asia, September 6, 2017. https://www.techinasia.com/china-fully-automated-sorting-center-jd-ecommerce
[v] Millward.
[vi] Nick Wingfield, “As Amazon pushes forward with robots, workers find new roles,” New York Times, September 10, 2017. https://www.nytimes.com/2017/09/10/technology/amazon-robots-workers.html
Thanks for this article! It’s clear that automation of warehouses both reduces costs and increases productivity, but I wonder if there are diminishing returns to these investments. While JD is doubling down on warehousing, many competitors are likely investing in the next, and longest, leg of the delivery process- actually moving the goods from warehouse to end consumer. If companies don’t invest in both areas might they be left behind?
Am very intrigued by automated warehouses and always keen to peek inside new ones–thanks for sharing. I think your push on human capital issues is a good one. I wonder if there is an opportunity for JD to shift some of those factory workers into sales or customer service? I would imagine there might be roles which employees could get excited about and would represent climbs up the career ladder. This would require training investments, but I think if done well it could result in a highly satisfied and competent workforce.
I’ve been a loyal customer of JD.com for years, and the reason I shifted from other Chinese e-commerce platforms to JD.com was precisely due to its unparalleled shipping efficiency. Purchased items would normally arrive at your door within 48 hours, even half a day if you reside in a tier-1 Chinese city such as Beijing and Shanghai. When Liu Qiangdong, JD’s founder, announced that the company would build its own warehouses nationwide, he faced massive skepticism since many believed that self-built logistics would incur heavy costs and hence significant financial burden to the company. The strategy has, however, proved to be a wise move over the years and become a core competitive advantage. I am eager to learn about the impact digitization would create on its supply chain, particularly curious about how it could guarantee timely shipping during promotional events such as the Single’s Day (Double 11). I also wonder how JD.com would partner more closely, as you mentioned at the end of the essay, with its merchants to ensure supply chain success in the digitized era.