JBS and Robot Butchers
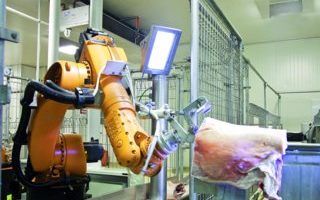
The world's largest meat processing company begins experimenting with machine learning in their plants. Developing and implementing these smart machines, capable of performing skilled and dexterous tasks, is pushing the current boundaries of automation.
JBS is the world’s largest meat processing company. With revenues of over $51 billion, it operates over 300 production units worldwide specializing in the processing of pork, beef, poultry, and lamb [1]. As meat and protein remain a mostly commoditized industry, JBS continually strives to maximize efficiency in all aspects of the value chain. To increase its processing efficiencies and worker safety, JBS bought a controlling share of New Zealand based Scott Technology, an automation and robotics company in late 2015 [2]. This move accelerated the implementation of machine learning in meat processing plants.
While automation had been introduced in the meat processing industry long before 2015, Scott Technology’s machines are unique because they utilize artificial intelligence and deep learning in their processes. Each time the robots receive a carcass, they utilize X-ray and Computerized Tomography (CT) scans to map it out and decide how to most efficiently cut the unit. They then use this data not only to maximize efficiency on that specific unit, but to learn and become more efficient over time [3]. While the current process is being implemented successfully at the JBS Bordertown lamb processing plant in Australia, worldwide implementation has not yet been achieved [4]. A lack of carcass uniformity across the different units coupled with large upfront costs have been the key factors slowing the spread of the technology. According to JBS beef division president Bill Rupp, relying on sight rather than touch is the key limitation preventing robots from being successful in beef processing. Beef, where unit weights can vary by over 500 pounds, is the most non-uniform carcass to process and presents the biggest challenge to this technology [5].
Scott’s website currently lists several specialized machines which can complete complex several key individual tasks from kidney fat removal to brisket cutting [6]. While these machines seem to operate individually, they are reliant on the X-ray and CT scanning machines to both provide and collect data. This data allows the systems to both operate and continually improve their processes. While individual tasks are constantly being developed and implemented, a fully automated process seems distant. A slow and incremental approach seems to define JBS and Scott’s current strategy towards automating the plants.
In addition to increasing efficiency, the robotics have the added benefit of making the workplace safer. According to the Occupation Safety and Health Administration (OSHA) and the Bureau of Labor Statistics, injuries in the meat packing industry are 2.5 times higher than the national average [7]. Cheap and plentiful labor, dexterous tasks, and steep barriers to entry in automated processes have also reduced the spread of robotics in the industry. Despite these large obstacles, low public tolerance towards workplace accidents and the recent increased interest in food processing transparency has led to a push in safer, cleaner, and more economical practices in meat processing plants.
Increasing the efficiency of this process requires costly experimentation, both from the machinery and raw materials aspect. To achieve the goal of a safer and more efficient workplace, JBS and Scott need to prioritize their efforts and tackle the most dangerous meat processing jobs followed by the ones which produce the most waste through worker variability. These machines have the potential to eliminate worker variability in terms of both time and waste. Maximizing these efficiencies can have large impacts on plant profitability, especially when dealing with expensive raw materials. In addition to prioritizing the efforts of their incremental approach, pushing the development of a small-scale, mostly automated processing plant prototype could serve as a proof of concept which helps define the future goals of the industry. Radical change may be necessary as small, efficient, mobile, and automated processing facilities could upend the regionally centralized model which currently dominates the industry. An automated prototype with the potential to operate on a small scale could solve many of the waste and sustainability issues plaguing the meat industry and protein production.
While machine learning seems destined to revolutionize the industry, important questions remain when considering the future of this new technology in meat processing. In addition to inputs from carcass mapping and all previous processing data, are there any other inputs that JBS should consider when trying to get maximum output and profit per unit from their robots (commodity prices by meat and cut type, changing consumer behavior, shipping costs and per pound profitability)? Also, is the incremental approach the best way to solve this problem, or should JBS and Scott strive for radical change within the industry? (748 words)
[1] JBS (2018). Retrieved from https://jbssa.com/about/
[2] Condon, J (2015). JBS moves to Invest in Robotics Technology Company. Retrieved from https://www.sheepcentral.com/jbs-moves-to-invest-in-robotics-technology-company-video/
[3] Garfield, L (2016). The world’s biggest meat producer is planning to test out robot butchers. Retrieved from https://www.businessinsider.com/jbs-meatpacking-testing-robot-butchers-2016-10
[4] Scott (2015). Retrieved from https://www.youtube.com/watch?v=BLrfJ0UvPhg
[5] Runyon, L (2016). World’s largest meatpacking firm wants to test out robotic butchers. Retrieved from https://www.npr.org/sections/thesalt/2016/01/05/461377861/worlds-largest-meatpacking-firm-wants-to-test-out-robot-butchers
[6] Scott (2018). Retrieved from https://www.scottautomation.com/products/
[7] OSHA (2018). Retrieved from https://www.osha.gov/SLTC/meatpacking/
Quite a meaty article Blake – I love it (preferably on a BBQ).
Interesting to understand how this could shake up the cost base of these larger organisations for high-volume animal products, but for me, there’s also a huge benefit in terms of waste reduction. Given the pressure the industry is under to reduce carbon emissions and overall wastage, this seems a timely opportunity to prove action is being taken.
This is a very interesting concept of the barriers to a company employing automation and ML in a commoditized industry where a massive CAPEX is just not realistic. I think the greatest opportunity is to separate automation from data collection, as building a massive library of training data to employ when they have a proven product they can afford to move on is essential. I really like your idea of radical change to a small, possibly mobile plant, but this certainly does not need to be exclusive of JBL, an internal entrepreneurial arm could accomplish this and serve as a proof of concept. It may also allow them to reduce shipping costs (which I assume are a major element of commodity costs) by reducing the carcass to the most efficient packaging size at a location closest to acquisition. I really enjoyed this article, it’s nice to see the efforts of a non-startup that doesn’t have massive amounts of cash to throw at innovation try to solve these issues incrementally for a change!
Fascinating article, extremely informative. I appreciated that you brought this topic to light, because while I consume meat on regular basis, I was not aware of the innovation that is beginning to happen in the supply chain of meat.
I felt your proposal for automated prototype made much sense and would be a catalyst to change the industry in a steady manner.
As for other possible sources of data, I struggled to think of one. You mentioned that, while the technology can replace human sight, it is the sense of “touch” that is difficult to replicate. Perhaps the company could collaborate with doctors and medical companies to uncover ways to diagnose the meat without relying solely on the trained sense of butchers. (I’m thinking of something like a mammogram for meat…). It could also benefit from working with various different types of meat species around the world to gain variety of data for its learning.