IoT in Shipping: Getting Cargo to Move with the Speed of Information
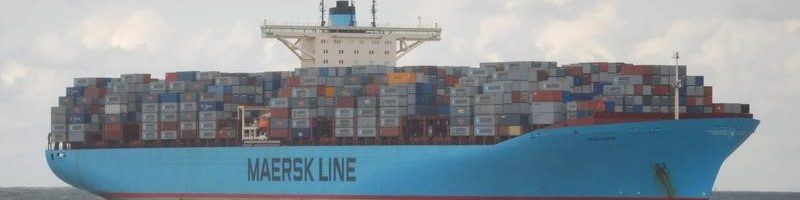
How a market leader in shipping is pioneering digitization that can reduce pricing for everyone.
A Little Context
I recently bought a new t-shirt for $29.99. This price includes consideration for raw materials, labor, direct overhead, corporate SG&A, and transportation. This shirt in particular was made in El Salvador, which means it had to travel over 2,200 miles to get here.
Like electricity, we oftentimes overlook our dependence on shipping despite its critical role in our everyday lives. Today maritime shipping represents 70% of global trade by value and 80% by volume[i]. Despite having evolved drastically over the centuries, the COO of Maersk Line (the largest shipping line in the world owned by Danish A.P. Moeller-Maersk; Mkt Cap: ~$185Bn) has stated that shipping lags when it comes to digitization[ii].
From a business model perspective, Maersk would be able to provide value through digitization by increasing communication throughout the supply chain. As seen with Barilla and the ITC eChoupals in the 1990s, increased communication has the ability to generate value for all parties involved. In the shipping industry, this allows for more efficient operations, such as allowing on-shore logistics providers to better manage the infrastructure needed to support container ships. IoT allows for optimal placement of containers on ships to reduce offloading times, which, coupled with the ability to track precisely when a ship will arrive in port, reduces the cost of wait time for trucks waiting to move the containers to their next leg.
This reduction in wait time can be passed along to the ultimate product owners and reflected as a reduction in transportation costs, which can then be translated into lower retail costs. Essentially, increased communication in shipping means that the next t-shirt I buy might be cheaper.
The question then becomes how to implement IoT into the operating model and create this value. In 2011 Maersk partnered with Ericsson to build a remote monitoring network that can track individual cargo loads and provide real-time information back to Maersk Line customers[iii] to solve this issue. This IoT solution is meant to help with route optimization, asset tracking and equipment monitoring.
Route Optimization
The introduction of radios in the maritime shipping industry around the turn of the 20th century (and further motivated by the sinking of the Titanic) was a major improvement to relying on visual cues for communication (think of semaphore)[iv]. This new communication between ships helped determine more efficient routes and avoid collisions. However, errors and inefficiencies could be further reduced. With improvements in IoT, positions can be tracked live and location information can be sent to other ships on the same network, allowing captains and land-based offices to track and alter ships’ movements easily to achieve objectives such as minimizing fuel consumption. The first results from IoT at Sea in Oslo, Norway suggested expected fuel savings up to 15% per year[v].
Asset Tracking
The Emma Maersk, one of the largest container ships in the world, can carry up to 15,000 20’ containers at any given time[vi]. This includes containers with explosives and hazardous materials, refrigeration, electronics and other consumables all positioned in different areas throughout the ship. Keeping track of this number of containers is no easy task, but has come a long way since the manual management of break bulk cargo. Digitization allows companies to monitor the status and temperature of cargo in real time: this information can be transmitted immediately to buyers and suppliers to facilitate immediate action-taking and improved operations[vii]. Imagine transporting bottles of wine: Maersk now provides the capability to track the temperature of the wine throughout its shipment, allowing manufacturers, wholesalers and retailers to know whether the temperature was inappropriate and has thus spoiled the juice.
Equipment Monitoring
Traditionally, ship operators would have to wait for engines or other critical components to show signs of breakage before undertaking any sort of repair. A five-week overhaul can cost ~$3MM per ship[viii], and unpredictable outages that occur during peak demand periods could be devastating to operators. To solve this, Maersk is using IoT and predictive maintenance to cut its repair bills by having sensors report when equipment needs care[ix]. Specifically, Maersk has partnered with Ericsson’s Maritime ICT Cloud business to connect embedded engine- and hull-monitoring systems with bridge communications to reduce inefficiencies, risks and overall cost[x].
Conclusion
As observed by the Economist, what Maersk does in digitization is likely to be followed by the rest of the industry in fairly short order; even Maersk’s rivals admit “we just watch what Maersk does and copy it.”[xi] While many shipping companies do not have the resources available to cut unit costs by building bigger ships, even the smallest firm can learn to apply big data to optimize its operations, increasing total value up and down the supply chain.
(798 words)
[i] http://www.rcrwireless.com/20160727/internet-of-things/maritime-industrial-internet-things-tag31-tag99
[ii] http://www.economist.com/news/business/21706556-shipping-business-crisis-industry-leader-not-exempt-profits-overboard
[iii] http://readwrite.com/2016/07/28/ericsson-iot-maersk-line-tl4/
[iv] http://www.gmdss.com.au/history.html
[v] http://www.rcrwireless.com/20160727/internet-of-things/maritime-industrial-internet-things-tag31-tag99
[vi] http://www.emma-maersk.com/specification/
[vii] http://newswire.telecomramblings.com/2015/09/maersk-teams-with-att-to-track-and-monitor-cold-shipping-containers/
[viii] http://www.rcrwireless.com/20160727/internet-of-things/maritime-industrial-internet-things-tag31-tag99
[ix] http://www.economist.com/news/business/21706556-shipping-business-crisis-industry-leader-not-exempt-profits-overboard
[x] http://www.rcrwireless.com/20160727/internet-of-things/maritime-industrial-internet-things-tag31-tag99
[xi] http://www.economist.com/news/business/21706556-shipping-business-crisis-industry-leader-not-exempt-profits-overboard
Very fascinating article … and as a Dane, I appreciate that you chose to write about Maersk!
Another thing that Maersk is looking into is 3D printing (http://www.maersk.com/en/the-maersk-group/about-us/publications/maersk-post/2014-3/spare-parts-just-press-print). As the ships are (hopefully) most often at sea, there are few opportunities to easily get new spare parts – 3D printing could be a solution.
As you write, route optimization is crucial to ensure high capacity utilization and make the trips across the Atlantic worthwhile. This is an optimization problem that could be solved together with other shipping lines to share capacity. I know of one new project aiming to do this “xChange” (https://xchange.bcg.com/public/index.html). I’m curious to see if this is a solution that will be adopted.
Very interesting post mon ami. I had no idea that shipping represents 80% of global trade volume. It’s amazing that although it is extremely capital intensive to build a cargo ship a the simple improvement in communication can produce massive savings. I am excited to watch how the shipping industry uses technology to better coordinate shipments.
This is such a cool post Pierre! Very informative piece about an industry that we don’t think about often but impacts our everyday lives. Two questions:
1. Maersk seems to bring a lot of technological innovation to its shipping business. I am curious how they come up with idea after idea after idea on how to apply existing digital technology in innovative and meaningful ways. Do you know if there is some sort of internal process that they follow (almost like an internal innovation funnel) that allows them to regularly comb through new technological advances and consider how Maersk might be able to apply them to their own business?
2. Hanjin, one of Maersk’s rivals, filed for bankruptcy this year. It seems that Hanjin was unable to stomach the sudden drop in shipping prices as excess capacity far outweighed demand industry-wide [1]. Maersk was not immune to this building spree as it “had been at the forefront of the mega-ship frenzy, ordering 20 of some of the biggest vessels on the market in 2011” [2]. Do you think Maersk has been using its value-add services, such as temperature monitoring of individual containers, to subsidize the impact of low shipping costs during this glut in shipping capacity? If so, can they use this as a way to deliberately wage price wars to price out less technologically advanced rivals in the future?
[1] http://www.latimes.com/business/la-fi-hanjin-shipping-industry-crisis-20160913-snap-story.html
[2] Ibid.