How Additive Manufacturing Can Unlock Boeings Biggest Challenges

Boeing stands to reap great gains from a considered adoption of additive manufacturing by viewing this megatrend from a strategic perspective, beyond just a narrow tactical one
Boeing: Process Improvement And Program Cost Management
While most literature on additive manufacturing and aircraft manufacturers has focused on the impact the former will have on the weight of the aircrafts produced using 3D printing and the subsequent gain in energy efficiency, there is much to be said about the impact it could have on how the industry manages process improvement.
Managing process improvement is core to the profitability of the industry and to Boeing in particular. A typical aircraft program line involves a heavy upfront tooling and setup cost, followed by a complex network of suppliers and assembly lines. Boeing typically expects that substantial process improvement learning will occur early in the course of a multi-decade program. As a result, the unit cost of the first units produced is dramatically higher than it is with later units. Without sharp and meaningful improvement in process over the course of the production program, project profitability would remain evasive. Expectedly, this involves a great deal of predictive budgeting on behalf of Boeing and it is precisely its reliance on, and vulnerability to, this lengthy forecasting that has led to a growing disconnect between cost forecasts and realized costs. The latest and perhaps greatest of such programs is the 787 program which faced massive cost overruns.[1, 2]
Effective Process improvement is therefore central to the aircraft manufacturing model and additive manufacturing can potentially overhaul how Boeing and its competitors approach this issue. A Boeing manufactured aircraft involves what is perhaps the most complex network of suppliers and subassemblies. In fact, this complexity is a key driver of the process inefficiencies early in the life of a program. Additive manufacturing is expected to allow for Boeing to consolidate many of these processes under its direct control by reducing the number of parts as well as making redundant many of the virtues of specialized subassemblies. Case and point, GE has recently certified an engine that is 30% additive while reducing the number of parts needed from 855 to 12! [3] This simplification then consolidation will expectedly reduce the space for and reliance on process improvement learning, thereby making aircrafts production programs more stable and predictable from a cost perspective over time. By ‘flattening’ the improvement curve – bringing the unit cost of the earlier units closer to that of later ones – additive manufacturing would have a profound impact on Boeings business model.
Product Development: Cycle Time Reduction Through Rapid Prototyping
Another feature that marks the aircraft manufacturing process is the lengthy product development cycle for new aircraft. Typically, this can run from four to eight years.[4] Be it by reengineering existing product frameworks or by designing wholly new ones, Boeing is constantly trying to stay a step ahead of its competitors on this front. In fact, a short product development cycle time is a critical core competency that Boeing needs to maintain and improve on if it is to remain relevant in the aviation market. “Getting to market earlier means that the company will have more opportunities to dominate a particular market segment before a competitor can react.”[4]
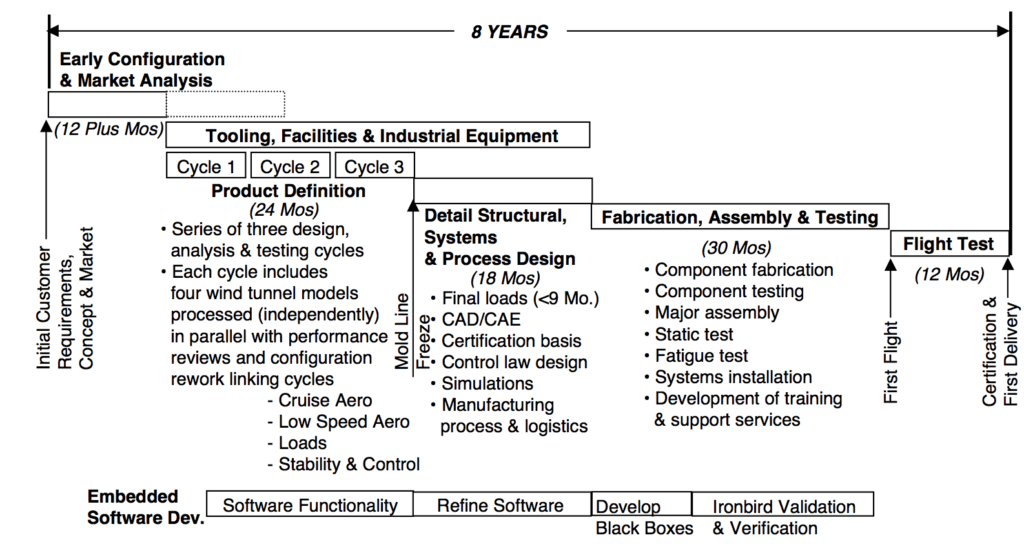
Additive manufacturing can have a dramatic impact on the product development cycle time by making it quick, easy and cheap to iterate, experiment with and modify different component designs. Consequently, this also gives Boeing the flexibility of offering its customers incremental product improvements that do not require a fundamental retooling or redesign of the assembly process.
How Boeing Is Currently Responding
Boeing has been an early adopter of additive manufacturing, beginning with its satellite and space programs. It has also increasingly utilized the technology for its flight programs to the tune of nearly 1000 distinct parts. [5] Furthermore, it plans to produce part of the new 777X folding wing using 3D printing (breaking the Guinness world record for largest 3D printed object). [6]
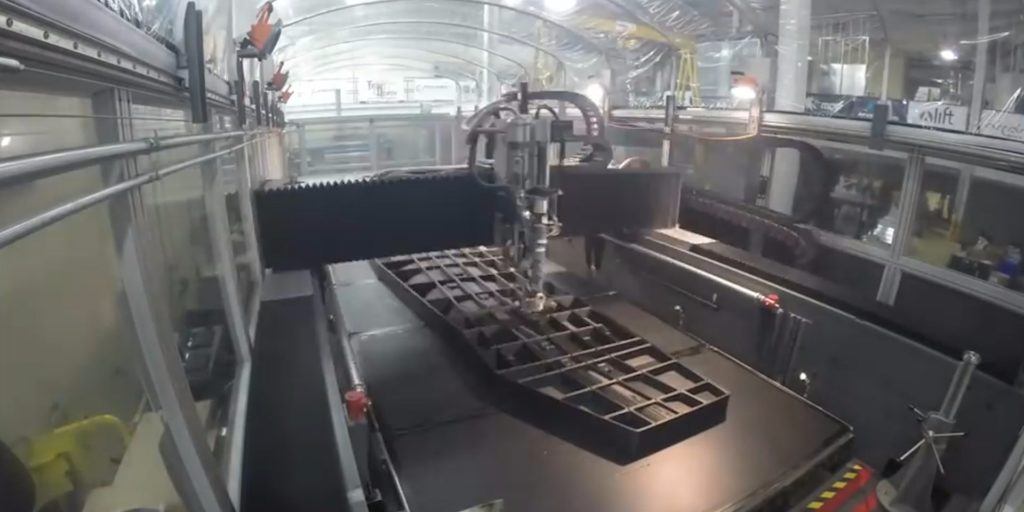
What Should Boeing Do
Boeing would do well to look at additive manufacturing from a strategic perspective beyond just a narrow tactical one. While the benefits of using additive manufacturing on a case by case basis for complex, lightweight and customized parts are obvious and direct, it is the strategic value of reducing Boeing’s reliance on realizing a steep process improvement curve that is most promising. This would mean, that beyond a case by case cost-benefit analysis, Boeing should aim to radically reimagine its assembly process to create a sustainable edge over its competitors. This would have the added benefit of making redundant Boing’s need to use the controversial method of program accounting. [7, 8] Moreover, with the advantage inherent in reducing the product development cycle time, Boeing stands to reap great gains from a considered adoption of additive manufacturing.
Further Investigation
To what extent would special materials used in aircraft limit the systemic adoption of 3D printing?
(795 words)
Sources
[1] James Allworth, “The 787’s Problems Run Deeper Than Outsourcing.” The Harvard Business Review, January 30 2013, https://hbr.org/2013/01/the-787s-problems-run-deeper-t, accessed November 2018.
[2] Dominic Gates, “Will 787 program ever show an overall profit? Analysts grow more skeptical,” The Seattle Times, October 17, 2015,https://www.seattletimes.com/business/boeing-aerospace/will-787-program-ever-show-an-overall-profit-analysts-grow-more-skeptical/, accessed November 2018.
[3] A. Brown. “Chain reaction: Why additive manufacturing is about to transform the supply chain,”Mechanical Engineering 140, no. 10, October 2018: 30–35.
[4] NASA, Development Cycle Time Simulation for Civil Aircraft, https://pdfs.semanticscholar.org/29f5/d06c43530f7b52973b95178ab413c18cc6b8.pdf, accessed November 2018.
[5] Boeing, 3D printing done right, Applying additive manufacturing in integrated mechanical designs, https://www.boeing.com/features/innovation-quarterly/nov2017/feature-thought-leadership-3d-printing.page, November 2018.
[6] Trevor Mogg, “Boeing’s new 3D-printed tool for making wings is so big it set a world record,” Digital Trends, August 30, 2016, https://www.digitaltrends.com/cool-tech/3d-printing-world-record, accessed November 2018.
[7] Jon Ostrower and Doug Cameron, “Boeing Shares Fall on Accounting Probe Report,” The Wall Street Journal, February 11, 2016, https://www.wsj.com/articles/boeing-shares-fall-on-probe-report-1455215511, accessed November 2018.
[8] David Ingram and Dena Aubin, “Boeing Uses an Accounting Method that Others Have Left Behind,” Reuters, February 12, 2016, http://www.reuters.com/article/us-boeing-probe-accounting-idUSKCN0VL2K0, accessed March 2017.
Love the article and the way you thought about beyond the obvious manufacturing usage of the 3-D printing technology towards leveraging it in the overall supply chain of the business. I am still struggling to understand, however, what exact use cases can be there in the supply chain. While I do see the huge advantages of 3D printing in product development, agile development and faster iterations, I am not entirely clear on the usage in the supply process…I found this article interesting to look at it from a different perspective: https://www.sdcexec.com/risk-compliance/blog/12062956/five-ways-3d-printing-is-transforming-the-supply-chain …
Love the fact that you were able to pick a topic that was relevant to our Boeing case in FRC! When reading the case, I was shocked to hear that Boeing used a methodology based on cost forecasting over the course of a given program. While the use of additive manufacturing in the supply chain for an aircraft was not surprising (in terms of using fewer parts, sub-assemblies, consolidating the supplier base, etc.), I did not appreciate how effective the concept could be when applied to product development. The ability to quickly re-design and re-manufacture components can speed up time to market (and be a game-changer from a competitive positioning perspective) and allow for an acceleration in innovation, a benefit I did not foresee.
Your question at the end of the article is interesting – I am excited to see how capabilities in additive manufacturing will develop over time and ultimately what % of components in aircraft manufacturing are candidates for 3D printing. The stats from the GE engine were shocking, and I didn’t appreciate that we were this far along.
One other question to think about – is there anything Boeing can do from a strategic perspective to leverage additive manufacturing to provide new value-add to its customers (rather than simply internal processes)?
The article brought up very interesting perspectives on how additive manufacturing can effectively reduce program costs of Boeing aircrafts. To your question about 3D printing of special materials, I believe extensive research is being conducted to develop technologies to print special material components. The benefits are two-fold: 3D printing can significantly reduce wastage during the manufacturing process, and new designs can be printed with much less part than traditional manufacturing techniques. For example, Boeing’s 787 makes extensive use of titanium parts, and 3D printing can cut costs associated with these parts significantly [1].
Currently, the costs of 3D printing large parts are prohibitively expensive, and traditional tooling methods still have an advantage over additive manufacturing during the mass production stage. I think we will definitely see more complex parts being produced through additive manufacturing, but Boeing still needs its suppliers for large parts.
[1] https://www.theverge.com/2017/4/11/15256008/3d-printed-titanium-parts-boeing-dreamliner-787
This is a great perspective on how additive manufacturing can improve the production processes, which is such an important issue to Boeing to solve given the volatility of the industry and the past failing experiences of matching cost forecast with realized cost. However, I wonder, if there is a solid comparison between the costs of using 3D printing for manufacturing vs. the traditional way of doing it- is it going to substantially reduce the cost? What about the tooling cost of setting up 3D printing?
I am a big fan of Boeing and I find the complexity of developing, designing, and manufacturing an aircraft to be absolutely fascinating.
I would be very disappointed if Boeing does NOT use additive manufacturing as a strategic move to accelerate its process improvement! Due to the unique nature of an aircraft program – extremely heavy upfront costs, much lower unit cost in the later part of production than at first – Boeing will have so much potential benefit to reap, if additive manufacturing is used to their advantage. As you pointed out, it can help flatten Boeing’s learning curve. And I think the resulting savings early on will allow Boeing to innovate at a much faster pace. Each program no longer needs to run for 20 years to breakeven – Boeing can free up its resources much earlier on to continue to develop the next best aircraft.