GE Additive: Additive Manufacturing and Aerospace
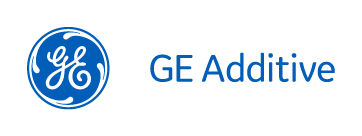
GE unleashes the power of Additive Manufacturing
GE Additive: Additive Manufacturing and Aerospace
Additive Manufacturing
Additive manufacturing (AM), often referred to as 3D printing, is a manufacturing process where components are assembled layer by layer according to a computer assisted design drawing, rather than the traditional method of cutting material away. Using technology referred to as powder bed fusion, material is deposited onto the build area before an energy source such as a laser heats the cross-sectional area to melt the particles and then rapidly cool them.[i] 3D printing usage has been limited historically due to high cost of capital and slower production speeds, as well as a complicated regulatory environment in many industries.[ii] GE’s recent investments in this technology reflect a confidence in its potential benefits including waste reduction, weight reduction, part simplification, reduced time to market, and improved performance.
Applicability to Aerospace
3D printing is relevant to GE and the aerospace industry in general as aircraft components continue to become increasingly complex. Due to the high cost of equipment and the relatively long cycle times, additive manufacturing is a poor substitute for low complexity, high quantity manufacturing. In the standard subtractive process of manufacturing, complex components with internal cavities require multiple subcomponents fastened together through a variety of processes. As 3D printing is additive in nature, it can create identical components as singular objects, allowing for fewer inspections and improved workflow efficiency. For example, GE engineers used 3D printing to produce half of a 900-piece LEAP jet engine in 16 components.[iii] Material wastage is also decreased, as the only material consumed in the process is that which is used in building the component. 3D printing also has the potential to simplify supply chains, allowing components to be produced in additional locations rather than relying on specific manufacturing sites. This can reduce shipping costs as well as ground time for aircraft.
Current Strategy
The head of GE additive sums of the high potential and disruptive nature of additive manufacturing: “Once you start thinking about it, you realize both intellectually and emotionally ‘Oh my God, if I don’t start moving, somebody else will.’[iv]” In the short and midterm, GE is pursuing a strategy of rapidly expanding capability through acquisition and growing its internal knowledge base. When designing the LEAP jet engine, GE engineering designed revolutionary fuel nozzles unable to be cast in traditional ways. These components were able to be produced through AM processes combining 20 parts into a single component, weighing 25 percent less, and having five times the durability. They purchased their partner from the LEAP nozzle printing, Morris Technologies, in 2012 and expanded their portfolio in 2014 with $1 billion investment in Arcam AB and Concept Laser. GE Additive was officially formed in 2016, with a stated goal to develop their additive capabilities to $1 billion in revenues by 2020 (from $300 million in late 2017). Engineers from throughout the business are trained in AM in “manufacturing boot camps” and sent back to find new possible implementations.
Future Potential
GE Additive should continue its current strategy as well as review existing components for compatibility, educate regulatory bodies, and pursue parts-on-demand strategies. As the 3D printing process has lower output but higher efficiency in small production runs, one use would be to delegate replacement components to existing aircraft to AM while utilizing traditional manufacturing processes for mass production. Government familiarity with AM is a potential concern, so GE should partner with the government when possible to streamline the regulatory approval process. This began in late 2018, as GE worked with the FAA to authorize a “change in design” allowing AM clips in GE’s GEnx engines, taken from design to production in less than 10 months.[v] Finally, research into the application of parts-on-demand will reduce inventory costs and decrease ground time for aircraft.
Open Questions
GE is well situated to capitalize on the additive manufacturing revolution. While their general strategy has been to make rapid acquisitions and expand into the AM field while exploring a wide assortment of potential uses, what challenges should it prioritize? Who are the best potential partners for GE?
(Word Count: 799)
[i] IEEE Potentials, “An Overview of 3D Printing in Manufacturing, Aerospace, and Automotive Indsutries”, https://ieeexplore-ieee-org.ezp-prod1.hul.harvard.edu/document/7517429/references#references, accessed November 2018
[ii] Frost & Sullivan, “Global Additive Manufacturing in Aerospace, 2018”, https://cds-frost-com.prd1.ezproxy-prod.hbs.edu/p/71319/#!/ppt/c?id=9AB0-00-5E-00-00&hq=additive%20manufacturing, accessed November 2018
[iii] Kellner, T. (2018). How 3D Printing Will Change Manufacturing – GE Reports. [online] GE Reports. Available at: https://www.ge.com/reports/epiphany-disruption-ge-additive-chief-explains-3d-printing-will-upend-manufacturing/ [Accessed 13 Nov. 2018].
[iv] Kellner, T. (2018). How 3D Printing Will Change Manufacturing – GE Reports. [online] GE Reports. Available at: https://www.ge.com/reports/epiphany-disruption-ge-additive-chief-explains-3d-printing-will-upend-manufacturing/ [Accessed 13 Nov. 2018].
[v] GE Additive. (2018). First additive manufactured part to be installed on GEnx commercial airline engines. [online] Available at: https://www.ge.com/additive/press-releases/first-additive-manufactured-part-be-installed-genx-commercial-airline-engines [Accessed 13 Nov. 2018].
Additional References:
- C.W.J. Lim, K.Q. Le, Q. Lu, and C.H. Wong. An overview of 3-d printing in manufacturing, aerospace, and automotive industries. IEEE Potentials 35, no. 4 (2016): 18–22.
Application of 3D printing in aerospace is a very interesting topic. In recent years, almost all of the leading manufacturers in this sector are using 3D printing to realize flexible manufacturing. For instance, Boeing is already 3D printing more than 300 of its airplane parts, and the production lead time has been reduced greatly from months to less than one month. When I think about the potential partners / use cases of 3D printing for GE, I think in the short term, GE can apply its technology and expertise in 3D printing from aerospace department to other departments, e.g. medical device. Same as aerospace, production of medical device is very costly. Using additive manufacturing will enable GE to reduce manufacturing costs and do R&D in a more agile way.
Given the lower waste, higher flexibility and higher efficiency of 3D printing, it makes sense that aerospace suppliers like GE are turning to 3D printing to build low quantity pieces. Going forward, I wonder about the overall role of 3D printing in the industry. Will it be primarily utilized as a way to more efficiently produce current products that are produced in standard ways? Or instead, will it primarily be used to potentially create new, innovative products that previously were inconceivable based on old manufacturing capabilities? It will be interesting to see how the industry evolves as these capabilities expand to enable completely new products to be produced.
This is very interesting to read. I understand that it is difficult for additive manufacturing to extract value from economies of scale and therefore more relevant in low-volume manufacturing. It is fascinating to know that a company as large and capital-heavy as GE, which I would assume would like to leverage of economies of scale, has identified product lines where low quantity manufacturing process will work and is using AM to be more flexible and to improve efficiency.
I like your point about how this process could potentially lead to a simplified supply chain by reducing the number of manufacturing sites required. As far as the challenges that GE should take on first it sounds like they are already addressing one of the biggest ones with the government, which could be a huge advantage down the road. I would also like to see if they are going to take on a role of working hand in hand with their suppliers in order to increase their capabilities in additive manufacturing or if they will instead start producing more parts in house as they begin to gain expertise.
The two most interesting point that you brought up were the reduction of waste with AM and the possibility of parts-on-demand in the future. For GE this seems like the most logical way to progress with this technology. The reduction of waste would fit with GE’s sustainability initiatives, since for many industries AM can signficantly reduce waste products during the manufacturing process. Instituting parts-on-demand may require GE to collaborate with their suppliers and increase training programs, not only for their internal engineers, but for their customers technicians. GE should focus on pitching these benefits to their customer and partner closely with them during their proof-of-concept process.