Digitization at Boeing: Printed Parts and Just in Time Maintenance
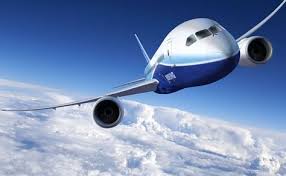
Boeing’s use of 3D printing and RFID technology in its production process has allowed for shorter lead times and less complexity in their supply chain.
The supply chain in the aviation industry is arguably one of the most complex and highly regulated in the world. Stringent quality requirements paired with an intricate ecosystem of suppliers makes aircraft production uniquely complicated. Additionally, the relatively low production volumes associated with aerospace parts keep suppliers from maintaining high inventories on hand both for building new aircraft and replacing broken parts.[1] Supply chain innovation in the aviation industry is now more important than ever because with increased demand; having even one aircraft down for maintenance can be detrimental to an airline’s bottom line. According to The Economist, while demand for aircraft production in 2015 was on the rise, there was concern that even if Airbus and Boeing had the capacity to assemble enough planes, their suppliers would struggle to deliver the parts.[2] Boeing is seeking to solve the supply problem in two ways: with the use of 3D printing to reduce lead times in production, and the use of RFID technology to increase replacement part predictability.
Boeing was a relatively early adopter in the space of 3D print technology. The advent of 3D printing allowed Boeing to not only reduce the cost and weight of aircraft structures, but also order less individual parts from its suppliers because the print assemblies generally allowed several structures to be converted into one piece. [3] As early as 2014, Boeing used tens of thousands of 3D printed parts on its aircraft.[4] The 787 Dreamliner had 30 x 3D printed parts, including air ducts and hinges.[5] Until 2017, Boeing’s use of 3D printed parts was limited to non-load bearing components. Due to increased innovation, however, the Federal Aviation Authority will now allow Boeing to use 3D print technology to produce titanium load-bearing parts for its newest 787 Dreamliners. This new opportunity makes aircraft production not only more cost effective, but also more efficient because it cuts down on both raw material costs and energy usage.[6] In the next two years, Boeing hopes to get more 3D printed load bearing parts approved by the FAA and increase the number of suppliers willing to invest in the technology.[7] Boeing even made a prototype of an entire printed cabin and perhaps sees a future in printing an entire airplane.[8]
Boeing is also investing in technology to tackle the issue of replacement parts for its aircraft that are already in the fleet. Radio Frequency Identification Devices (RFIDs) that are added to aircraft components during the production process allows data about each individual part to be tracked and analyzed. This information is particularly useful for parts that are not stocked in large quantities by suppliers. The tags can record conditions such as leaks, noise and extreme temperatures as well as maintenance information as to when the part was installed, removed or modified.[9] Analyzing this information can then be useful to suppliers as a “heads up” that the part may soon be ordered for replacement. The re-engineered process has allowed Boeing to reduce the lead time for certain parts through the supply chain by 97%.[10] This may be increasingly useful in military applications in the coming years where lead times are longer due to remote delivery locations.
With digital technology in its production and supply chains, Boeing seeks deliver to deliver a higher quality products to its customers in a shorter period of time. In the short term, I would recommend to Boeing’s management to keep a close eye on aircraft demand and ensure the supply chain can keep up. In the medium term, continue to invest in 3D print and RFID technology to make the supply chain process as streamlined as possible. There still remains a host of questions while analyzing this complex industry. Is there a limit to 3D printing and will consumers be willing to fly in planes with printed wings? Are there more efficient ways to cut costs and increase predictability in aircraft production?
Words: 789
References
[1] Dietrich, David and Elizabeth A Cudney, “Methods and considerations for the development of emerging manufacturing technologies into a global aerospace supply chain,” International Journal of Production Research Vol. 49, No. 10, (2011) via ProQuest accessed Nov 2017.
[2] The Economist: “Aerospace manufacturers: Good, in parts,” Oct 4th 2014 https://www.economist.com/news/business/21621851-fixing-one-supply-chain-problem-planemakers-may-be-creating-another-good-parts accessed Nov 2017.
[3] Nathan, Stuart, “Aerospace takes to additive manufacturing” October 2015 https://www.theengineer.co.uk/aerospace-takes-to-additive-manufacturing/ accessed Nov 2017.
[4] Ibid.
[5] Gilpin, Lyndsey, “3D printing: 10 companies using it in ground-breaking ways” Tech Republic March 26, 2014,
https://www.techrepublic.com/article/3d-printing-10-companies-using-it-in-ground-breaking-ways/ Accessed Nov 2017.
[6] Vincent, James, “3D-printed titanium parts could save Boeing up to $3 million per plane,” The Verge Magazine Apr 11, 2017, < https://www.theverge.com/2017/4/11/15256008/3d-printed-titanium-parts-boeing-dreamliner-787> accessed Nov 2017.
[7] Ibid.
[8] Gilpin, Lyndsey, “3D printing: 10 companies using it in ground-breaking ways” Tech Republic March 26, 2014,
https://www.techrepublic.com/article/3d-printing-10-companies-using-it-in-ground-breaking-ways/ Accessed Nov 2017.
[9] Coop, Phil. “RFID Intergrated Solutions System Optimizes Maintenance Efficiencies” Aero Magazine http://www.boeing.com/commercial/aeromagazine/articles/2012_q1/pdfs/AERO_2012q1_article2.pdf Accessed Nov 2017.
Super interesting article! funny that you wrote about planes
I remember that several years ago 3D printing was this buzz word that everybody used, but there weren’t many actual applications.
It is interesting to see how Boeing succeeded to integrate the use of 3D printed parts in its planes, and by doing so provided a solution to so many challenges that this industry is facing.
In your last sentences you asked about the consumer and about other ways to cut cost. I wonder how will the use of 3D printed parts change this industry – will Boeing become a vertically integrated player? What will happen to its supplier? And what is their reaction today?
Very interesting and informative read! The merits of 3D printing in the highly complex airline industry are certainly exciting. While likely a longshot, I wonder whether the decline in production costs associated with the adoption of 3D printing will ultimately reduce costs to a point where the barriers to entry in the airline manufacturing industry are low enough to encourage new manufacturers to enter the industry and challenge Boeing.
We are certainly a long way away from something like this potentially happening, but I expect that innovations such as 3D printing have the potential to redefine the airline manufacturing landscape in the long-term.
Cristin, awesome article! I do believe that there might be a possibility in which consumers are afraid of the risk from flying in a 3-D printed plane. Boeing could do probably do tests and modeling to show that 3-D printing is safer, something akin to what we saw in the America’s Cup case. Personally, I consider that the point you mentioned about 3-D printing allowing a plane to have fewer individual parts may be reassuring to the consumer. If you think how friction and wear and tear of tiny parts such as nuts and bolts affect machinery, or how a chair after being used for several years starts to lose its spare parts, then I think that airlines can communicate these benefits to the consumer.
Part of your article focused on the RFID identification and I wondered: who would be in charge of inspecting a plane, Boeing employees or the customer’s employees (i.e. airlines or the military)? I would think that since the customer is actually in possession of the plane for most of its life, it seems that the most significant benefit of this technology would be for the customer’s mechanics. This way, when they conduct routine inspections, they can be informed of the part’s history and know if a part needs to replacements or reparations every X years.