Digitalization Takes Off at The Boeing Company: Building a Next Generation Supply Chain
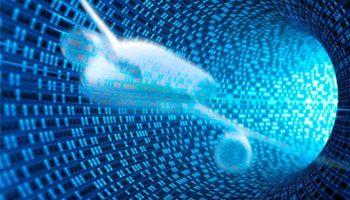
As it prepares to roll out its newest aircraft models, The Boeing Company is investing heavily in new technologies and supply chain innovation.
In the wake of the supply chain issues rampant within the 787 program, The Boeing Company will reclaim many manufacturing responsibilities in house as it prepares for the upcoming 777X aircraft. In addition, the company looks to integrate new technologies within its existing production lines to further cut costs and distinguish itself as a supply chain leader in the digital age.
Boeing had attempted a revolutionary new sourcing strategy with the 787 Dreamliner – choosing to outsource over 70% of the aircraft’s parts (versus ~30% for legacy programs, e.g. 737) to external suppliers around the globe.1 Although meant to reduce both costs and time to market, the complexity of the global supply chain led to massive delays and inventory overruns. Boeing was committed to learn from its mistakes as it marched toward the rollout of the new 777X in 2018.
Selected components of the 787 Dreamliner and associated supplier locations.1 Participating countries highlighted in blue.
Additionally, as the political climate in the US continues to evolve under the new administration, Boeing must take a hard look at reducing its internal supply chain costs. Given President Donald Trump’s efforts to retain more manufacturing jobs domestically, his decision to exit the Trans Pacific Partnership, and the ongoing discussions surrounding the future of NAFTA, the threat of retaliatory trade deals looms in the years to come.2
Boeing has looked at ways to use digitalization throughout the entire value chain to achieve long term cost savings and increase efficiency. The company has slowly begun to integrate new technologies in its inbound inventory logistics and manufacturing processes. For example, lost and damaged parts due to misplacement on the shop floor became a common problem during production. To help solve the problem, the company began installing RFID chips on over 7,000 components.3 The solution helped cut costs two-fold: first, it reduced labor required for rework and lost time, and, second, it significantly reduced labor costs during final delivery and inspection as less manual work was required.
Boeing also announced in April 2017 that it would partner with Norsk Titanium AS, a supplier of additive-manufactured titanium components, to produce four 3D printed parts for the newest model of the 787. Using additive manufacturing techniques instead of traditional methods is projected to save the company upwards of $3 million for the four parts it will outsource to Norsk.4 Achieving Federal Aviation Administration (FAA) approval for 3D printed parts is a huge step for Boeing and its partners, and opens the door for tens of millions of dollars of additional cost savings.
Boeing is also looking into longer-term strategies to incorporate robotics into its manufacturing processes for the 777 and 777X programs, as well as the 737 MAX. The company has recently invested in automation on its existing 777 line – employing the Fuselage Automated Upright Build (FAUB) process to construct major sections using robots (see video below).5 In preparation for the next generation of aircraft, Boeing has constructed a new Composite Wing Center (CWC) at its final assembly campus in Everett, Washington. The facility will house production of the 777X wings, a shift from the 787 who’s wings are made in Japan and shipped to Boeing for assembly using the 787 Dreamlifter.6 The CWC will rely heavily on automated manufacturing equipment in an effort to reduce labor costs, even more so than the 777.
Watch the 777 FAUB process in action!
As Boeing prepares to ramp up production of the new 737 MAX, it is currently in the process of updating the machinery it uses to assemble the wing spars. New Spar Assembly Line cells are smaller and faster than the existing tools, rely more on automation, and require less oversight from human operators. The increased capacity will allow Boeing to increase monthly output while continuing to decrease labor costs.7
As Boeing advances more digital initiatives it should be proactive to take its primary suppliers on the innovation journey with them to ensure that new technologies are also being introduced at the Tier 1 and Tier 2 levels, and at the lowest costs. Boeing implements a program known as “Partnering for Success”8 where it works hand in hand with key suppliers to reduce their own supply chain costs. If the company wants to stay ahead of the curve it should work closely with its partners to not only continue to drive costs down, but also to share technologies that could revolutionize production.
There are also several questions that Boeing should consider as it marches forward with its innovation plan. As was well illustrated with the 787 program, the company did not appropriately account for the risks associate with instituting massive changes to the production system. What risks are associated with increased introduction of robotics into aircraft manufacturing and how might they impact the supply chain?
Sources:
- Tang, Christopher S., and Joshua Zimmerman D. 2009. “Managing New Product Development and Supply Chain Risks: The Boeing 787 Case.” Supply Chain Forum 10(2): 74-86.
- Zhang, Benjamin. “Trump just used Boeing’s new global airliner to attack globalization.” February 17, 2017. http://www.businessinsider.com/boeing-trump-administration-policies-effects-dreamliner-787-2017-2, accessed November 2017.
- RFID Journal. “Boeing Deploys RFID In-House for Assembly Management.” May 20, 2016. http://www.rfidjournal.com/articles/view?16325, accessed November 2017.
- Norsk Titanium. “Norsk Titanium to Deliver the World’s First FAA-Approved, 3D-Printed, Structural Titanium Components to Boeing.” April 10, 2017. “http://www.norsktitanium.com/norsk-titanium-to-deliver-the-worlds-first-faa-approved-3d-printed-structural-titanium-components-to-boeing/,” accessed November 2017.
- The Boeing Company. “Mechanic and Machine: Boeing’s Advanced Manufacturing Improves 777 Assembly.” February 23, 2017. http://www.boeing.com/features/2017/02/faub-777-assembly-02-17.page, accessed November 2017.
- The Boeing Company. “$1 Billion 777X Composite Wing Center Opens.” http://www.boeing.com/features/2016/05/777x-composite-wing-center-05-16.page, accessed November 2017.
- Gates, Dominic. “Boeing ramps up automation, innovation as it readies 737MAX.” February 14, 2017. https://www.seattletimes.com/business/boeing-aerospace/boeing-ramps-up-automation-innovation-as-it-readies-737max/, accessed November 2017.
- “How Boeing Is Trying to Cut Costs Ahead of Its 100th Anniversary.” Fortune.com, July 7, 2016. http://fortune.com/2016/07/07/boeing-budget-cuts/, accessed November 2017.
(774 words)
Very interesting post! When reading the post, I got the impression that the bottleneck of Boeing’s digitization could be legislative, because the company needs to obtain the Federal Aviation Administration approval. Even if Boeing had a right strategy for achieving digitize its whole supply chain, it would not be able to sell planes without government approval. Another risk associated with digitization in general is security. If all the information of Boeing’s supply chain is shared through internet, the risk of hacking may increase. Although it may create some problems at the beginning, I am optimistic about the long term improvements!
Great post! The first risk that comes to mind around automation is the likely loss of jobs in Washington state, and the impact it could have on future tax breaks negotiated with the state. Over the years, Boeing has benefited from billions of dollars in tax breaks based on the premise that the company would continue to create jobs in the area. However, if automation leads to job cuts, the state could reclaim these benefits. Boeing should work closely with the state to mitigate this risk.