Additive Manufacturing for The Final Frontier: How 3D Printing Can Take Us to Mars (and Beyond)
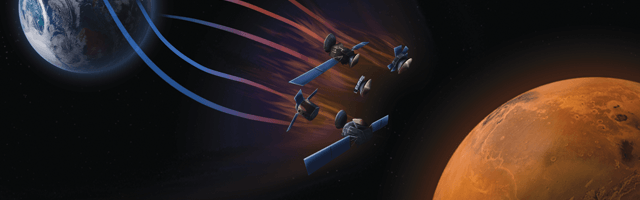
A look at how NASA is using additive manufacturing on Earth and in orbit to realize the future of space exploration.
Context and Challenges
NASA has committed to sending humans to Mars within the upcoming decades.[1] This is the next step toward the organization’s long-term goal “to expand permanent human presence beyond low-Earth Orbit.”[2] Manned deep space missions will require spacecraft to be self-sufficient for months, even years at a time.
To meet these ambitious targets, NASA will need cost-effective tools and processes for transport of raw materials and manufacturing equipment, and fabrication of finished goods using materials from Earth and those found in-situ.
Additive Manufacturing Advantages in Aerospace Processes and Product Development
At approximately $10,000 per pound of payload[3], weight costs are the driving factor in aerospace economics. Additive manufacturing is transforming the industry by allowing for complex, weight-optimized, finished parts and high-efficiency usage of raw materials.
The complex geometries of aerospace components are challenging, expensive, and time-consuming to create using conventional processes.[4] Additive manufacturing can fabricate the same components more easily, often with fewer parts, thereby reducing set-up, tooling, and assembly costs, and speeding up production.[5] In 2013, engineers at NASA’s Marshall Space Flight Center 3D-printed a rocket engine injector in 2 pieces, versus 115 for the traditionally made version[6], lowering the $300,000 standard cost by 80%.[7] Critically, additive manufacturing techniques can yield 40-60% weight reduction while maintaining other important physical properties.[8] Furthermore, traditional subtractive manufacturing wastes the majority of raw material, with only 10% or so remaining in a final part, while additive manufacturing can achieve material efficiencies of 90%.[9]
Finally, additive manufacturing offers possibilities for reclaiming unnecessary parts through recycling, further reducing costs. NASA recently partnered with aerospace company Tethers Unlimited to develop the world’s first “refabricator,” capable of converting 3D-printed items back into feedstock and then re-printing new parts.[10] The device recently arrived at the International Space Station (ISS), where astronauts will use it to investigate the reusability of 3D-printed material.
As Chris Singer, director of the Marshall Center Directorate explains, “Additive manufacturing will improve affordability from design and development to flight and operations, enabling every aspect of sustainable long-term human space exploration.”[11]
NASA’s Pursuit of Additive Manufacturing in Aerospace Applications
NASA has been experimenting with additive manufacturing in aerospace applications through internal and external pathways.
The first 3D printer in space launched to the ISS in September 2014.[12] After successfully demonstrating the viability of 3D-printing in zero-gravity, the ISS upgraded to permanent additive manufacturing infrastructure in the form of the Additive Manufacturing Facility (AMF).[13] The AMF “allows for immediate repair of essential components, upgrades of existing hardware, installation of new hardware…and the manufacturing capability to support commercial interests.”[14]
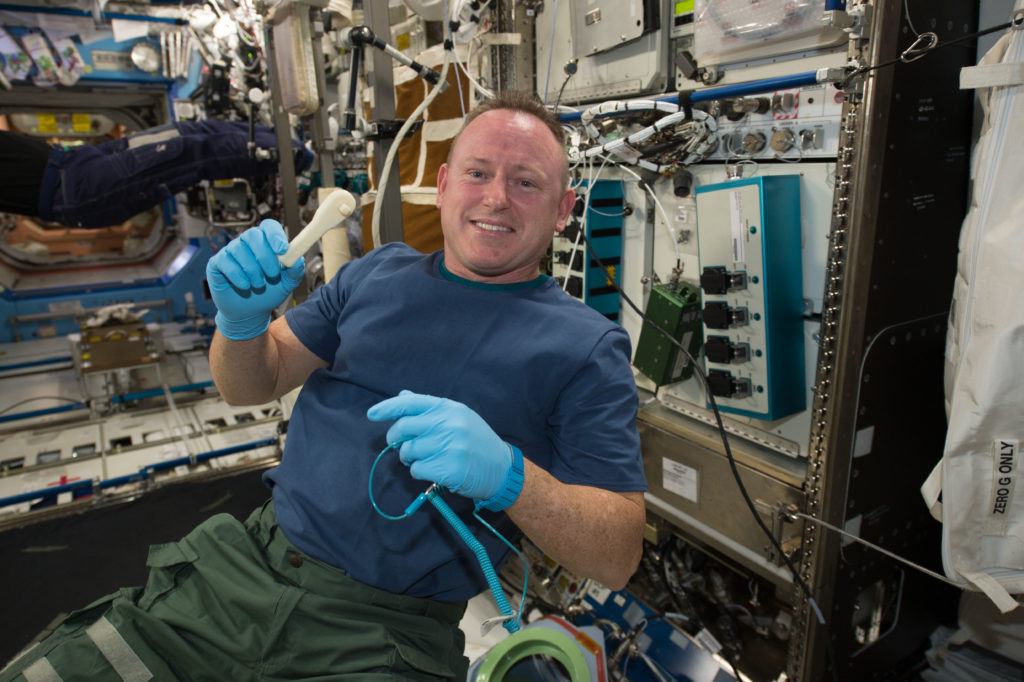
Source: “Space Station 3-D Printer Builds Ratchet Wrench To Complete First Phase Of Operations.” Edited by Jennifer Harbaugh, NASA, NASA, 23 Dec. 2014, www.nasa.gov/mission_pages/station/research/news/3Dratchet_wrench. 13 November 2018.
Back on Earth, NASA pushes the boundaries of additive manufacturing with ventures like the Low Cost Upper Stage-Class Propulsion Project. The agency employed new metal alloy 3D-printing techniques to construct a combustion chamber, which it will use for various rocket propulsion tests.[15]
Through academic connections and the Small Business Technology Transfer and Small Business Innovation Research programs, NASA supports universities and commercial enterprises in prototyping and testing aerospace-focused 3D-printing solutions.[16][17] An example is the ongoing 3D-Printed Habitat Challenge, a multi-year competition to develop proofs-of-concept for structures that could be 3D-printed on Mars using endogenous materials.[18] Recent winners of the contest’s Phase II consisted of American and international architecture and construction firms, a space-tech start-up, and Northwestern University.[19]
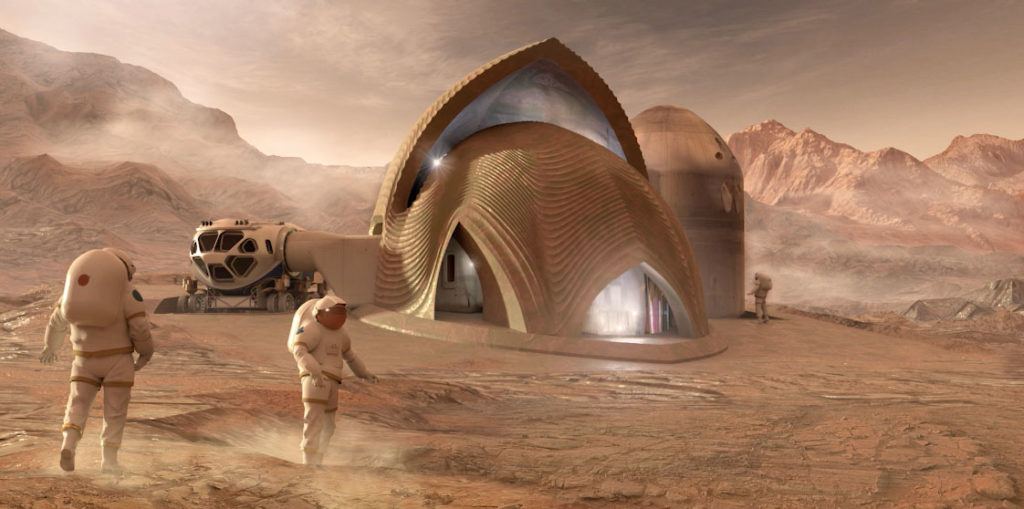
Source: “Five Teams Win a Share of $100,000 in 3D-Printed Habitat Competition.” Edited by Jennifer Harbaugh, NASA, NASA, 23 July 2018, www.nasa.gov/directorates/spacetech/centennial_challenges/3DPHab/five-teams-win-a-share-of-100000-in-virtual-modeling-stage. 12 November 2018.
In the near-term, NASA will continue to leverage its partnerships with other institutions to parallelize the exploration of additive manufacturing capabilities.
Recommendations
The brutal environment of outer space exacts a toll on man-made objects. Currently, astronauts put themselves at risk performing space walks in order to assess and fix damages on the ISS, while other structures may not receive repairs at all. NASA could invest in building robots that use additive manufacturing to restore existing structures. They could, for instance, 3D print covers for holes caused by micrometeorites and other space debris.
More abstractly, NASA should take advantage of the less restrictive nature of additive manufacturing to expand the creativity of their product design process. NASA has a history and an image of relying on rigid, regimented thinking and design, while 3D-printing and computational manufacturing offer avenues for more organic, integrated architectures. Additive manufacturing opens the door to constructing single-material components with gradients of physical properties and to generating composite materials with optimized properties. It also easily handles novel shapes that would be difficult or impossible to achieve with standard tooling methods. By relying on additive manufacturing, NASA engineers can augment their ideation space and feel less constrained by the fabrication process.
Balancing Innovation and Responsibility
Additive manufacturing has tremendous potential for space exploration, yet also carries more unknowns than traditional manufacturing processes,[20] translating to greater risk.
How can and should NASA maintain its pursuit of innovation in their product development processes as a large federal organization whose core mission revolves around safety critical systems?
Word Count: 800
References
[1] United States, Office of Inspector General. NASA’S TOP MANAGEMENT AND PERFORMANCE CHALLENGES, NOVEMBER 2017. 6 November, 2017, https://oig.nasa.gov/reports/MC-2017.pdf. 11 November 2018.
[2] National Aeronautics and Space Administration Authorization Act of 2010. Pub. L. 111- 267. 124 Stat. 2805. 11 Oct 2010. GPO. Web. 11 Nov. 2018.
[3] “Advanced Space Transportation Program Fact Sheet.” Edited by Brooke Boen, NASA, NASA, 12 Apr. 2008, www.nasa.gov/centers/marshall/news/background/facts/astp.html. 11 November 2018.
[4] Prater, Tracie. “Additive Manufacturing: From Rapid Prototyping to Flight.” https://ntrs.nasa.gov/archive/nasa/casi.ntrs.nasa.gov/20150006951.pdf. Slide 11. 11 November 2018.
[5] “Industrial 3D Printing of High-Tech Aerospace Components.” EOS, EOS, www.eos.info/aerospace. 11 November 2018.
[6] “NASA Tests Limits of 3-D Printing with Powerful Rocket Engine Check.” Edited by Brooke Boen, NASA, NASA, 27 Aug. 2013, www.nasa.gov/exploration/systems/sls/3d-printed-rocket-injector.html. 11 November 2018.
[7] Witze, Alexandra. “NASA to Send 3D Printer into Space.” Nature, vol. 513, no. 7517, 10 September 2014, pp. 156–156., doi:10.1038/513156a. 11 November 2018.
[8] “Industrial 3D Printing of High-Tech Aerospace Components.”
[9] Titomic – Industrial Scale Additive Manufacturing, 3D Printing, Titanium, Innovative, Melbourne, Australia, www.titomic.com/aviation-space.html. 11 November 2018.
[10] “NASA to Demonstrate Refabricator to Recycle, Reuse, Repeat.” Edited by Kristine Rainey, NASA, NASA, 28 Aug. 2017, www.nasa.gov/mission_pages/centers/marshall/images/refabricator.html. 11 November 2018.
[11] “3-D Printed Rocket Parts Rival Traditionally Manufactured Parts.” Edited by Brooke Boen, NASA, NASA, 24 July 2013, www.nasa.gov/exploration/systems/sls/3dprinting.html. 12 November 2018.
[12] Prater, Tracie, et al. “3D Printing in Zero G Technology Demonstration Mission: Summary of On-Orbit Operations, Material Testing and Future Work.”
https://ntrs.nasa.gov/archive/nasa/casi.ntrs.nasa.gov/20160013371.pdf. Slide 6. 11 November, 2018.
[13] Snyder, Michael P. “Additive Manufacturing Facility (Manufacturing Device).” NASA, NASA, 19 July 2018, www.nasa.gov/mission_pages/station/research/experiments/2198.html. 11 November 2018.
[14] Ibid.
[15] “NASA Advances Additive Manufacturing For Rocket Propulsion.” Edited by Lee Mohon, NASA, NASA, 9 May 2018, www.nasa.gov/centers/marshall/news/nasa-advances-additive-manufacturing-for-rocket-propulsion.html. 11 November 2018.
[16] Bean, Quincy. “3D Printing In Zero-G Technology Demonstration .” NASA, NASA, 6 Dec. 2017, www.nasa.gov/mission_pages/station/research/experiments/1115.html. 11 November 12 2018.
[17] IDTechEx. “Improving Additive Manufacturing for Space Missions.” 3D Printing Progress, IDTechEx, 5 November 2018, www.3dprintingprogress.com/articles/15748/improving-additive-manufacturing-for-space-missions. 11 November 2018.
[18] Coldewey, Devin. “NASA’s 3D-Printed Mars Habitat Competition Doles out Prizes to Concept Habs.” TechCrunch, TechCrunch, 27 July 2018, www.techcrunch.com/2018/07/27/nasas-3d-printed-mars-habitat-competition-doles-out-prizes-to-concept-habs/ . 11 November 2018.
[19] Ayoubi, Ayda. “NASA Awards Five Teams $100,000 in 3D-Printed Habitat Competition.” Architectmagazine.com, Architect Magazine, 30 July 2018, www.architectmagazine.com/technology/nasa-awards-five-teams-100-000-in-3d-printed-habitat-competition_o. 11 November 2018.
[20] Vickers, John. “The Crucial Role of Additive Manufacturing at NASA.” https://ntrs.nasa.gov/archive/nasa/casi.ntrs.nasa.gov/20170000638.pdf. Slide 27. 11 November 2018.
Awesome article! This is a really interesting article since the most prohibitive part of space exploration is the insane costs to get anything from the ground into space. Additive manufacturing looks like a great way to be able to do quick fixes or improvements. Testing the creations and products heavily before widespread use would be crucial here. Additionally, it could be really useful if we could use material commonly found in space as raw material to be used in 3D printing, to lower the cost burden even further.
An interesting and thought-provoking read! The space industry seems to be well-positioned to benefit from 3D printing technology due to the ability to reduce weight, a key consideration in space travel. I was surprised and impressed by the level of cost (80%) and material (90%) efficiency that can be achieved by this application of 3D printing. The ability for 3D printing technology to operate in space (under zero gravity conditions) appears to have been a crucial success factor at NASA; operation in space presents many opportunities for in-mission production and repair work. Large organizations can often become closed-minded and bureaucratic, and should constantly push to improve innovative idea-generation processes. Therefore, I completely agree with the recommendation that NASA use 3D printing to expand creativity in product development. Another important recommendation that I would add is a program of training and change management for employees, to ensure that they understand the benefits of 3D printing and its applications in their respective fields. This can help to combat the fear of change that can come with introducing a new technology.
I think that partnerships in this space are critical to success and maintaining competitive advantage, by enabling NASA to achieve rapid scale and leverage existing 3D printing knowledge and insight. NASA’s partnership with Tethers Unlimited enabled them to leverage advanced 3D printing recycling technology that otherwise could have taken many months to develop. NASA’s support of university and commercial prototyping is another way that it effectively outsources learning and technology development.
In response to your question about how NASA can pursue 3D printing applications safely in the context of its organization, the best approach would be to significantly modify product development, testing and approval processes. 3D printing technology is fundamentally different from traditional technology and the associated risks are different. Processes should be aligned to these new risks and the more iterative approach required by this new technology. Processes should ensure that appropriate risk management is conducted before approving 3D printed technology for use. As mentioned above, it is also critical that NASA conducts the appropriate level of change management with employees and key stakeholders to ensure buy-in and alignment to using this new technology and new product development processes.
Wow – I was struck by several of the facts cited in this great article. First, the cost saving stats are quite remarkable: rocket engine cost reduction of 80%, raw material efficiencies of 90% and weight reduction of 40-60%. In addition, it’s amazing that NASA is already able to accomplish these 3D printing feats in zero gravity conditions when the additive manufacturing revolution seems to just be taking off here on earth. In addition, I was encouraged to read that NASA is partnering with universities and commercial enterprises in prototyping and testing aerospace-focused 3D printing solutions – this seems like a highly effective way of speeding up and, importantly, externalizing the government funding burden of additive innovation for the aerospace industry.
To address your question on safety, it seems that NASA has already established environments to compare their 3D product development in zero vs. non-zero gravity environments here on earth, which is critical. The bar on using 3D printing in space should be high, and therefore investment in the requisite training facilities should be made and multiple (perhaps repetitive?) “test runs” should be conducted before any of these products are used in space. In the short run, I would prioritize using additive manufacturing for applications that don’t jeopardize human life if they fail in space. For instance, prioritizing use of 3D printing for rocket propulsion tests is a good way of testing the technology and building expertise; this expertise will then be valuable when “higher risk” additive manufacturing solutions, such as developing mission-critical ISS parts or creating covers for holes caused by space debris, are introduced that have real implications for astronaut lives while in orbit.
Fascinating read! I was very surprised that NASA, an organization that in my mind stood for creative thinking, (how else could they have gotten to the moon??) is known instead for rigid thinking. For all the more, it was very interesting to see how they have used 3D printing on the ISS and how NASA hopes to use it in the future. I can see how transportation logistics, repairs, and astronaut safety can be improved if this type of technology were perfect to work in zero gravity. Seeing the habitat challenge made me think of all of the things that could be built once that was perfected! (Cars, appliances, maybe even food!?).
In response to your question about balancing innovation in a safety-driven organization made me agree with the above comments that partnerships and outsourcing innovation is critical to this mission. The more that new ideas can be crowd sourced and developed externally lessens the risk on NASA. As mentioned by Mark Walport, the Government Chief Scientific Advisor of the UK, sharing risk and funds between the government, private companies, and R&D competitions is critical to finding proven and scalable innovative technologies (https://www.oxfordmartin.ox.ac.uk/downloads/reports/14-1190b-innovation-managing-risk-evidence.pdf). In addition, maintaining a quality- and test-driven product development cycle is crucial to ensuring that new innovations go through the proper checks.
How can and should NASA maintain its pursuit of innovation in their product development processes as a large federal organization whose core mission revolves around safety critical systems?