Additive Manufacturing at Ford: A Long Way from the Model T
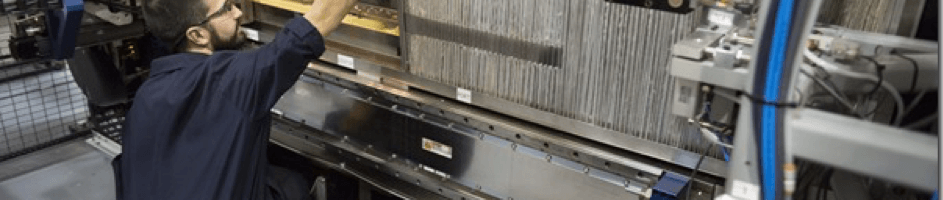
How can Ford use additive manufacturing to speed up its product-development process, improve its competitiveness, and create value for the consumer?
Henry Ford revolutionized manufacturing by promoting standardization and economies of scale. He made only one standard car model and drove down prices by producing many units efficiently in an assembly line with continuous flow.[1] So why is the Ford Motor Company interested in additive manufacturing (AM), which is touted for customization and has limited scale benefits?
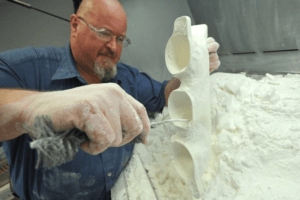
First, 3D printing technology can manufacture “complex geometric structures” that lead to better-performing products.[2] For example, China’s Shining 3D Tech Co Ltd makes exhaust pipes for Ford that weigh one-third of what simpler conventional pipes weigh.[3] Less weight means lower transportation costs to Ford and better fuel economy for the consumer.
Second, and perhaps more important, with AM, Ford gets new products to market sooner, because the fabrication of prototype components has a shorter throughput time (e.g., 40 hours instead of the 10 weeks it could take with the CNC lathing machines of the past). With 3D printing, Ford can easily produce multiple designs simultaneously, so the company can use parallel testing to achieve more rapid iteration.[4] One researcher has estimated that a two-month delay in reaching the market is associated with a 23.6% loss in a product’s lifetime revenue.[5] Therefore, AM’s benefits to Ford’s top line outweigh the high cost. Moreover, some parts may actually be less expensive to produce with 3D printing.[6]
* * * * *
Ford is taking steps to integrate AM into product development and production.
For now, in the short term, Ford emphasizes the use of AM to create prototype parts that it can test in vehicles under development. It is rapidly increasing the number of parts that it produces with AM. The company’s history with AM actually goes all the way back to the 1980s, when Ford purchased SLA 3, a stereolithography device that was the third 3D printer ever produced.[7] By the mid-2000s, Ford was printing about 4,000 prototype components each year.[8] Now, the company makes over 100,000 components per year across five 3D prototyping centers.[9]
For the longer term, Ford is working to broaden the application of AM in its business. The company has purchased a Stratasys Infinite Build System. Unlike conventional AM products, which build pieces vertically, this machine works horizontally. As a result, it can fabricate larger parts.[10]

And Ford’s newly created 3D printing research division is experimenting with emerging technologies “in hopes of using 3-D printing to manufacture more complex designs that can’t be created using traditional methods.”[11] One drawback of standard 3D printing is that it works one layer at a time, which not only is slow but also creates “tiny fault lines that can crack when stressed,” as vehicles on the road frequently are. Ford is testing a method from startup Carbon3D, which is faster and produces stronger, more solid, non-layered items that look “just like a molded part.”[12] In the future, AM may be commonly used in parts that actually make it into purchased Fords driven by consumers.
* * * * *
I recommend that Ford take additional steps to tap the potential of AM. The company has hinted at how it envisions the future: at least some production (as opposed to prototype) parts will be made with 3D printing, and consumers will even be able to create their own replacement parts at their local 3D printer.[13]
To achieve that vision, Ford must address two key factors: materials and cycle time. It needs to develop more 3D printing materials that resemble the ones used in its conventional parts.[14] Ford’s 2018 investment in Desktop Metal, which specializes in innovative technology for printing in metals like stainless steel, is likely a step in this direction.[15] But Ford should remain on the lookout for other companies with whom it can partner on materials development. If partners’ technology is sufficiently compelling, Ford should acquire them outright. On cycle time, too, Ford should be on the lookout for partners who can help reduce the build time of 3D printers.[16]
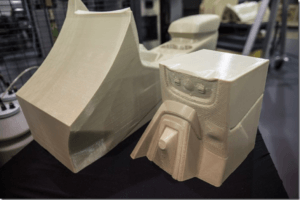
Ford is considering using the Stratsys machine to produce larger portions of vehicles (e.g., body panel),[17] and I recommend testing these possibilities soon.
I would fold Stratasys tests into a broader goal: to build a road-usable car that is 70% lighter than its conventionally fabricated counterpart. Italian startup XEV is taking orders for a car that is about 60% lighter thanks to 3D printing.[18] Ford should task a team with exceeding this weight reduction. Even if the result is not immediately marketable, the ambitious goal should spur innovation and stretch the possibilities for AM at Ford, just as the Jeopardy project developed IBM’s capabilities in machine learning.
* * * * *
The main question for Ford is: Is there a plausible future in which customization becomes sufficiently important to car buyers that they will pay the premium for 3D printing? If so, how does Ford prepare for it?
(799 words)
Endnotes
[1] Richard Koch, “How Ford Created a Huge Market by Lowering its Prices,” Entrepreneur, October 11, 2016, https://www.entrepreneur.com/article/282218, accessed November 2018.
[2] Lucas Mearian, “3D printing is now entrenched at Ford,” CIO, August 21, 2017, via ProQuest, accessed November 2018.
[3] Ma Si and Cheng Yu, “3D printing is booming,” China Daily, August 21, 2017, p. 13, via Factiva, accessed November 2018.
[4] Lucas Mearian, “3D printing is now entrenched at Ford,” CIO, August 21, 2017, via ProQuest, accessed November 2018.
[5] Biren Prasad, “Analysis of pricing strategies for new product introduction,” Pricing Strategy & Practice 5, no. 4 (December 1997): 132–141. For clarification of the relationship to the automotive industry, see “What is the cost of delay in the automotive industry?” ResearchGate, https://www.researchgate.net/post/What_is_the_cost_of_delay_in_the_automotive_industry, accessed November 2018.
[6] Lyndsey Gilpin, “3D printing: 10 companies using it in ground-breaking ways,” TechRepublic, March 26, 2014, https://www.techrepublic.com/article/3d-printing-10-companies-using-it-in-ground-breaking-ways, accessed November 2018.
[7] “Building in the Automotive Sandbox,” Ford Motor Company, https://corporate.ford.com/innovation/building-in-the-automotive-sandbox.html, accessed November 2018.
[8] Lucas Mearian, “3D Printers Churn Out Ford Prototypes,” Computerworld 48, no. 11 (June 23, 2014): 4.
[9] Lucas Mearian, “3D printing is now entrenched at Ford,” CIO, August 21, 2017, via ProQuest, accessed November 2018.
[10] Gary S. Vasilash, “Ford’s Approach to AM,” Automotive Design & Production, March 20, 2017, https://www.adandp.media/blog/post/fords-approach-to-additive-manufacturing(1), accessed November 2018.
[11] Loretta Chao, “Fast 3-D Printers Earn New Respect,” Wall Street Journal, April 26, 2016, p. B1.
[12] Loretta Chao, “Fast 3-D Printers Earn New Respect,” Wall Street Journal, April 26, 2016, p. B1.
[13] Lucas Mearian, “3D printing is now entrenched at Ford,” CIO, August 21, 2017, via ProQuest, accessed November 2018; Clint Boulton, “Printing Out Barbies and Ford Cylinders,” Wall Street Journal Online, June 5, 2013, via Factiva, accessed November 2018.
[14] Loretta Chao, “Fast 3-D Printers Earn New Respect,” Wall Street Journal, April 26, 2016, p. B1.
[15] Yuliya Chernova, “Ford Leads $65 Million Investment in Desktop Metal,” Wall Street Journal Online, March 19, 2018, via Factiva, accessed November 2018.
[16] Gary S. Vasilash, “Ford’s Approach to AM,” Automotive Design & Production, March 20, 2017, https://www.adandp.media/blog/post/fords-approach-to-additive-manufacturing(1), accessed November 2018.
[17] Lucas Mearian, “3D printing is now entrenched at Ford,” CIO, August 21, 2017, via ProQuest, accessed November 2018.
[18] Wang Ying, “3D-printed electric cars coming,” China Daily, March 13, 2018, p. 13, via Factiva, accessed November 2018.
Image Sources
[A] Ford, published in Lyndsey Gilpin, “3D printing: 10 companies using it in ground-breaking ways,” TechRepublic, March 26, 2014, https://www.techrepublic.com/article/3d-printing-10-companies-using-it-in-ground-breaking-ways, accessed November 2018.
[B] Published in Gary S. Vasilash, “Ford’s Approach to AM,” Automotive Design & Production, March 20, 2017, https://www.adandp.media/blog/post/fords-approach-to-additive-manufacturing(1), accessed November 2018.
[C] Published in Gary S. Vasilash, “Ford’s Approach to AM,” Automotive Design & Production, March 20, 2017, https://www.adandp.media/blog/post/fords-approach-to-additive-manufacturing(1), accessed November 2018.
Ford’s utilization of 3D printing for prototyping, as you mentioned, is not new, and has existed in the overall automotive industry (especially in Japanese factories) for decades, although costs of employing such a technology has certainly dramatically decreased. I found your comment on the possibility of using this technology to make something in the actual physical car (beyond the prototyping phase) quite interesting. Not sure if feasible from a scaled production process perspective, but perhaps Ford can capitalize on consumers’ obsession with “personalization” today and add touches that are unique to a particular consumer (initials on the car)?
Thank you, Tasnia, for your comment! I agree that Ford needs to explore thoroughly the possibilities for personalization that customers may demand in the future. One idea that I had pertains to a future (assumed by many these days) in which most cars on the road are self-driving and operated by ride-sharing companies in fleets. In that future, the economics of car sales will be very different, because purchasers of cars (Uber, Lyft) will have much deeper pockets than today’s individual consumer. Perhaps the fleet operators will want more and more ways to customize their cars so as to differentiate themselves to riders—and they will have the means to pay for this customization, which might come through AM.
Your information on the increased product lifetime revenue from getting product to market sooner is a great argument for faster manufacturing processes. The development of 3D printing using metallic materials certainly sounds very compelling for Ford. I’m intrigued by your idea of using additive manufacturing for body components. I’m curious how a vastly lighter car would impact safety ratings and how vehicle safety testing may need to evolve to accommodate the weight efficiencies available from alternative manufacturing techniques. Sizable weight reduction may seem like a stretch goal for now, but as achieved, regulations that still protect passengers will need to keep up.
Thanks for your comment. I had not thought about the regulatory implications, but they could be significant.
I was surprised to hear that 3D printed components can be made with superior performance to and at a fraction of the weight of parts produced through traditional manufacturing methods. How is this actually accomplished? Is it a difference in the raw material inputs that go into the printer? Or does it have something to do with how the component is shaped by the printer? I’d also be interested in learning more about Carbon3D’s new printing method, and how it differs from the layering method of current 3D printers. And as Ford looks to integrate more AM in their manufacturing, I wonder where their competitors in the automotive industry are with this as well.
Thanks, Jeff, for your question. As I understand it, 3D printing can result in lighter components because the technology allows for fabricating more complex designs that are “leaner” than could be produced with traditional methods. It is a matter of the shape, I believe. Here are the sources I found that are most relevant to your question.
Lucas Mearian, “3D printing is now entrenched at Ford,” CIO, August 21, 2017, via ProQuest, accessed November 2018.
Ma Si and Cheng Yu, “3D printing is booming,” China Daily, August 21, 2017, p. 13, via Factiva, accessed November 2018.
Wang Ying, “3D-printed electric cars coming,” China Daily, March 13, 2018, p. 13, via Factiva, accessed November 2018.
Another source mentioned a company (not Ford) that prints a part with a “honeycomb core,” which would not be possible without 3D printing.