Adding Value across the Value Chain — Additive Manufacturing at Siemens
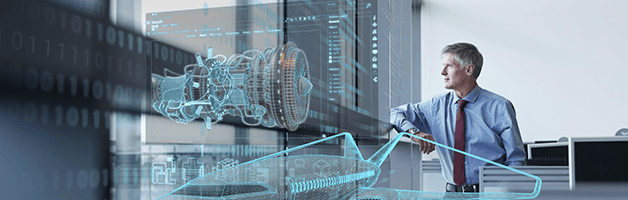
Siemens is leveraging additive manufacturing to create value across its value chain — from equipment manufacturing to repair, maintenance, and services.
As a diversified manufacturer of industrial equipment and provider of related services, Siemens has found applications for additive manufacturing (AM) that drive process improvements and product development enhancements across its value chain. Speed of innovation, design and dependability of equipment, and the ability to provide ongoing maintenance and aftermarket parts are key to Siemens’s competitive edge, all of which benefit from AM.
In the energy sector, AM has enabled Siemens to reduce product development time by up to 25% through enhanced prototyping and to cut replacement part lead times by up to 50% in the high-margin aftermarket [1]. Spare part designs are stored in 3D-datasets for easy replication, and production doesn’t require costly retooling. In conventional manufacturing, equipment manufacturers face the recurring decision of whether to incur high inventory costs resulting from upfront overproduction of large quantities of spare parts or to perform costly retooling when smaller batches of replacement parts are demanded [2]. In certain circumstances, Siemens can eschew the need for replacement parts altogether by leveraging AM to perform repairs and make upgrades directly to existing equipment [3]. Additionally, AM has significantly reduced material waste – Siemens has seen up to a 65% reduction in resource use and 30% reduction in gas emissions in certain applications [4]. This kills two birds with one stone – lowering Siemens’s cost base in an increasingly competitive market, while responding to customer demands for environmental responsibility.
In the near-term, Siemens is providing AM as a service to increase adoption through its online collaborative platform, Additive Manufacturing Network (AMN) launched in April 2018. High upfront costs, lack of requisite engineering expertise, and slow diffusion of knowledge are some of the main inhibitors of the adoption of AM among smaller scale manufactures and equipment users [5,6]. By bringing together participants from both the supply- and demand-side of the market (see Figure 1), AMN is designed to lower these barriers, while providing access to production capacity and a forum for collaboration [7]. Lowering adoption risk associated with AM and the use of 3D-printed parts has the potential to significantly increase the size of the market opportunity for Siemens.
To capitalize on expected demand growth, Siemens is investing in medium-term capacity expansion and human capital. In March 2018, Siemens announced plans to invest approximately £30 million in a new AM factory in England [8]. “This significant investment underlines our belief that there is huge potential for innovation and growth within the [AM] sector. It is also the next step towards achieving our ambition of pioneering the industrialisation of 3D printing…” said Juergen Maier, Siemens UK CEO [9]. Over the next five years, the new facility will allow Siemens to increase its AM asset base from 15 machines to over 50 [10]. The facility will create 55 jobs, strengthening the existing human capital base of engineers, metallurgists, and manufacturing specialists [11].
While Siemens’s initiatives have the potential to increase demand for AM and ensure that it has adequate capacity to capitalize on market growth, there are additional opportunities to explore. As a conglomerate, Siemens is exposed to demand trends that differ by end-market. In the near-term, Siemens can benefit from monitoring demand for AM machines across divisions to achieve higher utilization across its asset base [12]. For example, consider a hypothetical scenario in which the optimal number of AM machines are allocated to each of the Power and Gas and Wind Power segments to maximize practical capacity utilization under existing demand levels. If there were a subsequent shift in trends causing Power and Gas demand to fall and Wind Power demand to increase, Siemens should be nimble enough to identify this and reallocate capacity across the two business units to keep utilization optimized. Since AM equipment is more fungible than conventional manufacturing equipment, which is tooled to the specifications of a certain set of outputs, Siemens can realize utilization synergies across business units by virtue of being a “pan-industrial” company, as theorized by Richard D’Aveni [13].
In the medium-term, Siemens should focus on continuously evaluating opportunities to integrate production with testing and inspection. Since AM is an emerging method of manufacturing mission-critical equipment, one of the largest risks is in the lack of extensive historical data on failure rates and the mechanical properties of output [14]. If Siemens can run production and testing in parallel, it will be able to offer a dependable manufacturing solution without the risk of elongated lead times that can result from focusing on capacity versus output integrity.
Looking forward, one of the main challenges that Siemens will face is determining what production processes will not benefit from AM due to structural factors – such as large volumes or minimal customization – and resisting the urge to falsely adopt AM. As the cost-effectiveness of AM continues to improve, fluid reassessment of new applications is needed.
Figure 1: Siemens Additive Manufacturing Network
(Word Count: 784)
End Notes:
[1,3,4] Siemens AG, “Fast, efficient, flexible: Additive Manufacturing (3D-printing) in the energy sector,” https://www.siemens.com/global/en/home/products/energy/services/maintenance/parts/additive-manufacturing.html, accessed November 2018.
[2] A. Brown. Chain reaction: Why additive manufacturing is about to transform the supply chain. Mechanical Engineering 140, no. 10 (October 2018): 30–35.
[5] M. Holwef. The limits of 3D printing. Harvard Business Review Digital Articles (June 23, 2015).
[6] J.B. Roca et al., Getting past the hype about 3-D printing. MIT Sloan Management Review 58, no. 3 (Spring 2017): 57–62.
[7] “Siemens launches Additive Manufacturing Network to transform global manufacturing,” press release, April 23, 2018, on Siemens AG website, https://www.siemens.com/press/en/pressrelease/?press=/en/pressrelease/2018/digitalfactory/pr2018040255dfen.htm, accessed November 2018.
[8,9,10,11] “Siemens to invest £27m in new 3D-printing factory,” press release, March 19, 2018, on Siemens AG website, https://www.siemens.co.uk/en/news_press/index/news_archive/2018/siemens-to-invest-27m-in-new-3d-printing-factory.htm, accessed November 2018.
[12,13] Richard A. D’Aveni, “GE Goes Short-Term With Larry Culp,” Forbes.com, October 25, 2018, https://www.forbes.com/sites/richarddaveni/2018/10/25/ge-goes-short-term-with-larry-culp/#53da9ab525e7, accessed November 2018.
[14] C.W.J. Lim, K.Q. Le, Q. Lu, and C.H. Wong. An overview of 3-d printing in manufacturing, aerospace, and automotive industries. IEEE Potentials 35, no. 4 (2016): 18–22.
Thank you for providing a glimpse into how additive manufacturing (AM) is being employed by one of the premier advanced manufacturers in the world.
The challenge you highlight for Siemens at the end of your post – determining which applications will not benefit from additive manufacturing due to structural factors – seems to be the most pressing one, not just for Siemens but for all who hope to take advantage of this new technology. Thus, I found Siemens’ roll-out of its additive manufacturing network (AMN) to be impressively strategic. By hosting a co-innovation platform for designers, engineers, and producers to collaborate on the various applications in which AM might be successful, Siemens is gathering some very valuable market intelligence (and if I’m not mistaken, people either voluntarily join or pay Siemens to participate!). I’m curious as to how successful Siemens has been in attracting collaborators onto AMN, given potential concerns around intellectual property and proper compensation for contributors’ ideas.
This article recommends manager restraint in deciding which new technologies to adopt and how quickly to adopt them. Additive manufacturing has been instrumental to improving Siemens’ supply chain and can be similarly transformative for other companies. The author raises a good point; however, that managers should not embrace new technology for its own sake but should conduct cost/benefit analyses for each implementation. Traditional financial figures will naturally dominate these analyses, but human capital and cultural impacts should also be evaluated.
Hype surrounding new technologies often drives managers (and investors) to over-index early in a technology’s lifecycle during a period of inflated expectations, onl to experience a period of disillusionment when promised benefits do not materialize as quickly as expected. Gartner describes this process as the “Hype Cycle.” To avoid this Hype Cycle, companies should thoroughly evaluate investment in new technologies (AI, VR, 3D Printing, etc.) before committing resources.
One of the more pressing questions this raised for me was around how and when (if ever) AM could become a technology that will surpass traditional manufacturing even at large batch sizes or on products with low customization needs. The argument for using AM then would be more focused on the reduction of waste in industries or products where the raw materials cost is high and waste currently is high. It is unclear whether this type of innovation is more likely to be advanced at small companies pushing the edge of innovation as opposed to at manufacturing giants.
Thanks for the article. I continue to lean on this point but AM in prototyping, supply chain, etc. is one thing but when you come to installing it in industry and safety-critical components, I feel we could be moving too fast. The points you raise around failure rates and mechanical properties are so important for original equipment manufacturers. I would imagine even in the traditional product development process, time must be taken to flesh out and test those concerns. I would hope Siemens is providing the same rigor around 3D-printed equipment to maintain their credibility and reputation for quality. This may be a space where additional regulation or oversight might be needed since it is so fast-paced.
– Not only explain the technical aspect of additive manufacturing, but also addressed the business feasibility of the technology. It was great to know that some companies have success commercially by using the technology. This article implied that one of the key factors of commercial success of additive manufacturing application is “high-added value and moderate volume” product.
– Suggested practical solutions such as capacity allocation between Power & Gas and Wind Power to make the technology more profitable.
– Yet sample number is small, but I learned the reliability of additive manufacturing technology, considering the difficulty and high-safety regulation of the products that Siemens produces.