“A-Tesla”, Can Elon Musk Revolutionize The Auto Industry?

Elon Musk said, “The factory is more important than the cars it produces [1].” Tesla is transforming the auto manufacturing industry, not through electric cars, but through the digitalization of the Gigafactories production of lithium-ion batteries.
The Electric Battery Problem
For a long time the American auto industry has been located in the Midwest, but in particular my hometown Detroit, Michigan where the three American automakers are based. However, it was announced in 2014, that Tesla would build the largest auto factory and facility in the world in Reno, Nevada.
Tesla to date has completed 30% of this $5 billion, 15 million square foot Gigafactory, which is expected to produce 35 gigawatt-hours (GWh) annually. The facility is being built out of necessity as Tesla’s estimated demand of 500,000 cars per year will require more lithium-ion batteries than is currently produced worldwide [2]. Not only does Tesla need to produce more batteries, but it needs to produce them for much cheaper to be competitive in the mass market. It is believed that $100/kilowatt-hours (kWh) is where electric-powered vehicles become cost competitive with gas-powered vehicles. Tesla has not released its battery cost, but a 30-35% reduction is believed to make them competitive at a $35,000 price point for the Model 3 [3].
Source: Bloomberg New Energy finance, Ford, GM, Tesla, survey participants [4]
The Gigafactory will not only allow for price reduction, but also supply chain reliability. Tesla currently receives thousands of parts from hundreds of suppliers who are mostly single source suppliers [5]. The desire to consolidate suppliers couldn’t be more prevalent then now after Tesla missed Q3 earnings because of only producing 20% of the Model 3 cars due to “production bottlenecks” from a battery supplier. Tesla was forced to fire the supplier, redirect engineers and redesign the process [6]. Tesla can no longer rely on the old auto supply chain to achieve its mission.
Elon’s Future for Tesla
Elon has stated that the Gigafactory will be completed by the end of 2020. In order to accomplish this goal, Tesla partnered with Panasonic for production investment and research & development. However, Tesla plans to purchase the full output from Panasonic at a negotiated price and be less reliant on Panasonic’s R&D once the Gigafactory is completed [5]. The facility will be self-reliant on energy due to a 70-megawatt solar rooftop [7].
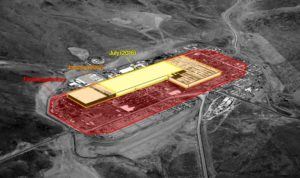
Some Advice For Elon
Although Elon is a genius, he still has areas of improvement like us all. There are two critical areas that he needs to focus on to accomplish his mission.
Improved labor Conditions In The Short Term
The reduction of the price of batteries is a critical component to achieving mass market. The variable cost reduction will not only need to come from the battery materials, but also from labor improvements. Tesla already utilizes several robotic machines to reduce cost and increase output, but the Gigafactory will still have up to 6,500 employees [1]. Given that the Freemont facility has an 8.8% incident rate, which is 31% higher than the auto industry, it will be critical to remained focus on the “human” aspects of the factory to avoid union issues and reduced productivity [9]. It would be ashamed if the Gigafactory fails because of a lack of focus on the team versus the technology.
Diversify Suppliers In The Medium Term
Tesla is still reliant on various single source suppliers even with the automation processes in place. It will be extremely difficult to prevent any supplier issues, similar to the recent bottleneck, without either internalizing or dividing the processes more. During the Q3 earnings call, Elon said, “Obviously, there are bottlenecks. There are thousands of processes in creating the Model 3, and we will move as fast as the slowest and least lucky process among those thousands. [10]” It likely does not make sense to internalize too many processes from an efficiency perspective so Tesla should find more suppliers. However, this will not be possible until there is more scale in production.
Even Elon Doesn’t Have All The Answers
Tesla has made significant progress, but still only sold 83,922 of the 77 million cars sold globally in 2016 [11]. Does Tesla even have a chance of becoming a real threat regardless of their supply chain improvement? Will GM beat Tesla at its own game given GM is planning the release of 23 electric models by 2023?
(776)
[1] Nevada, E. (2017). Everything investors need to know about Tesla’s massive ‘Gigafactory’ in Nevada. [online] Business Insider. Available at: http://www.businessinsider.com/tesla-stock-price-giga-factory-nevada-elon-musk-2017-9 [Accessed 16 Nov. 2017].
[2] Tesla.com. (2017). Tesla Gigafactory | Tesla. [online] Available at: https://www.tesla.com/gigafactory [Accessed 16 Nov. 2017].
[3] Lambert, F. and Lambert, F. (2017). Tesla is now claiming 35% battery cost reduction at ‘Gigafactory 1’ – hinting at breakthrough cost below $125/kWh. [online] Electrek. Available at: https://electrek.co/2017/02/18/tesla-battery-cost-gigafactory-model-3/ [Accessed 16 Nov. 2017].
[4] Randall, M. (2017). Tesla Flips the Switch on the Gigafactory. [online] Bloomberg.com. Available at: https://www.bloomberg.com/news/articles/2017-01-04/tesla-flips-the-switch-on-the-gigafactory [Accessed 16 Nov. 2017].
[5] Tesla, 2016 Annual Report. http://ir.tesla.com/secfiling.cfm?filingID=1564590-17-3118#TSLA-10K_20161231_HTM_ITEM_7, accessed November 2017.
[6] Tesla, Third Quarter 2017 Update. http://files.shareholder.com/downloads/ABEA-4CW8X0/5560482989x0x962149/00F6EB90-2695-44E6-8C03-7EC4E06DF840/TSLA_Update_Letter_2017-3Q.pdf, accessed November 2017.
[7] The Verge. (2017). Tesla will power its Gigafactory with a 70-megawatt solar farm. [online] Available at: https://www.theverge.com/2017/1/11/14231952/tesla-gigafactory-solar-rooftop-70-megawatt [Accessed 16 Nov. 2017].
[8] Lambert, F. and Lambert, F. (2017). Elon Musk says 2 or 3 more Tesla Gigafactories are coming to the US. [online] Electrek. Available at: https://electrek.co/2017/07/15/elon-musk-tesla-gigafactory-us/ [Accessed 16 Nov. 2017].
[9] Clifford, C. (2017). Tesla workers say factory safety is worse than sawmills and slaughterhouses. [online] CNBC. Available at: https://www.cnbc.com/2017/08/01/tesla-workers-complain-about-factory-safety.html [Accessed 16 Nov. 2017].
[10] Tesla, Q3 2017 Results Earnings Call Transcript. https://seekingalpha.com/article/4119419-tesla-tsla-q3-2017-results-earnings-call-transcript, accessed November 2017.
[11] Number of cars sold worldwide from 1990 to 2017 (in million units) | Statista. [online] Statista. Available at: https://www.statista.com/statistics/200002/international-car-sales-since-1990/ [Accessed 16 Nov. 2017].
Henri, I find the challenges that Tesla has regarding their ambitious battery production plans also very interesting. I agree with you on the importance of the cost of batteries for the success of electric vehicles (EVs). Being the most expensive part of an EV – typically around 60% of the production costs comes from battery – battery plays a significant role in market penetration. However, reading your essay, I was struggling to understand how digitization would exactly help Elon Musk reduce battery production costs. You emphasize in your text the automation (not digitization) of the manufacturing process in the planned Gigafactory; I agree. But, an automated manufacturing process will not help Tesla in “transforming the auto manufacturing industry”, which has already one of the highest utilization rate of robots in production lines.
I think there are more important problems that Tesla needs to focus on in designing its battery supply chain. Currently, almost all car manufacturers in the world are trying to secure a long-term access to metals, like cobalt or lithium, which are needed in the production of batteries. There is an extremely high competition to secure these precious metals and bottlenecks are common. With the extremely high demand, limited number of mines, mostly in Asian countries, have the absolute power to decide on which car manufacturer they want to work with and at what price, driving the costs higher. In my essay “Volkswagen’s New Electric Strategy”, I also tried to explain these similar problems in the battery supply chain and the challenges for the electric mobility. I would be happy if you could read it and put also your thoughts in the comments section.
Really enjoyed reading this — thank you! It makes sense that primary areas of focus for Tesla should be solidifying a diversified supply chain and lowering battery production costs. With over 400,000 orders of the Model 3 and Tesla’s current production bottlenecks, it is easy to imagine that supply will lag behind demand for at least the next few years. When tied to single source suppliers, Tesla is at their mercy as any issues and delays upstream (which Tesla cannot control) would be rippled throughout Tesla’s business, all the way down to vehicle delivery.
I also agree with you and Levent on batteries — it is crucial for electric vehicle companies to invest in or push forward better battery technology as it is the single biggest driver of cost. In fact, Tesla and their manufacturing partner Panasonic have begun investing massive capital into the battery factory in Reno. To leverage this high fixed cost structure, Tesla needs to drive up demand and thus production volume on their vehicles and other energy products that utilize this battery technology.
Very interesting article. Looking for new locations of Gigafactory without even having finished, not to mention having tested, the first factory of this size, is indeed a bold move that not many people but Elon Musk would make.
I agree that in the short term they must focus on growing the number of suppliers. I would consider closer cooperation with those suppliers and helping them improve their processes and reach Tesla’s standards and requirements. I believe that would be a more efficient way of eliminating a bottle neck, than just bringing all the processes and tasks under Tesla’s own roof.
In the long term however it might prove to be a right strategy. In order to win with the traditional players with very deep pockets, like GM, they must focus on maximizing efficiency and bringing costs to minimum, which might only be possible if they fully control the whole production process and build cutting edge factory.
Great article Henri! Telsa’s approach to centralize the supply chain for one of the most critical components of their vehicles is great strategy to make their cars more affordable. You raised some really great concerns Tesla should be worried about, but continued engineering support and product evolution for battery design is one factor that may determine whether Tesla will every be a real threat to traditional auto manufacturers in the long run.
Since Tesla is severing the R&D partnership with Panasonic it may indicate that Tesla doesn’t plan to iterate the battery design as they iterate the car models. Battery performance could decline as Tesla enhances the capabilities and computing power of their vehicles. Also, there is still opportunity in the Li-ion battery market to reduce size, weight and costs all of which are critically important in highway and off-road automotive equipment. Tesla may also miss out on the decreasing cost trend that Li-ion batteries have exhibited over the past few years depending the price negotiation was determined.
OEM and supplier collaboration throughout product development life cycle could be a huge competitive advantage for Tesla as more automakers transition towards electric vehicles.