3D Printing & The Future of Army Resupply in Remote Areas
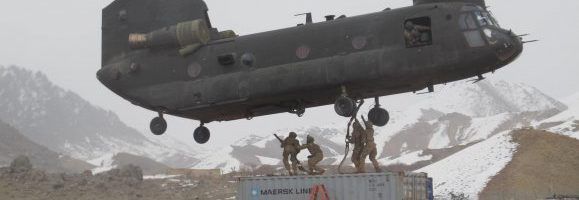
The US Army has long struggled to resupply remote combat outposts. With advances in additive manufacturing, that need may disappear.
Nothing. That’s the sound your weapon makes when it’s missing any one of a dozen critical parts that can break, be damaged through wear and tear, or get lost when a tired Soldier is conducting weapons maintenance. It’s at this point that you hope your unit’s armorer has brought enough spare parts and the right tools to fix your malfunction, especially if you are in a remote area in the mountains of Afghanistan or Syria. That’s hopefully about to change.
Additive manufacturing stands to transform the way the United States Army supplies hard-to-reach places with much needed repair and replacement parts, whether it’s for a vehicle, a weapon system, or a piece of a Soldier’s kit. The current Army supply system is based on a series of requests that are ultimately relayed through a unit’s executive officer, who can either approve or deny a request based on budget, necessity of the item, or priority of the requesting unit, among other considerations. If he or she approves, it can take anywhere from one day to three months to receive that item, based on its physical location and who is shipping it. In the remote regions that the Army so frequently operates, that lag time may be the difference between life and death. With advances in 3D printing technology, it will soon be possible to print repair and replacement parts onsite in remote locations.
The US Army has ramped up spending and research at its Army Research Labs (ARL) on additive manufacturing, especially 3D metal printing. It has also partnered with the National Center for Manufacturing Sciences, which has spent nearly $600 million [1] on R&D projects. ARL has already developed a way to print small unmanned aerial vehicles in only a few hours [2] although there are still hurdles to overcome with the production speed and the durability of the product.
Likewise, Desktop Metal, an additive manufacturing company in the Boston area, is shrinking the size and portability of these printers and has developed technology to model one-off parts that are more durable and more able to handle dynamic loads. As their name implies, they make a printer, debinder, and sintering furnace that all run off 110vac and fit through a standard door and rely on metal powder and a liquid binder instead of lasers to power their printing, which offers the advantage of being much faster and less power intensive. [4]
One of the limiting factors is that this is tech heavy, and the Army has tens of thousands of potential components that might have to be printed, even if only once. This challenge offers a unique opportunity – recruiting a new class of Soldier who is tech savvy, mechanically minded, and looking to build the foundations of an important change within the organization. While Congress has set aside $13.2 billion for 3D printing [5], it has not undertaken a formal training program to teach the necessary skills required to succeed. The Army could do this by incentivizing Soldiers to take computer-assisted design classes, mechanical or industrial engineering, or partner with ARL or other firms to do hands-on training and testing of these systems. As with anything in the Army, it will take time to build up subject-matter expertise across such a large organization, which is why it needs to leverage its large spending power and its connection with industry to get ahead now.
While there is plenty of upside that makes this worth pursuing, there are logistical and security considerations that bear exploring. Being able to successfully 3D print in remote locations implies that you have the designs and supplies on hand. From a logistical standpoint, this adds a list of supplies that you must get to a unit before it deploys. It also forces prioritization of designing and modeling the most likely parts to fail. While inconvenient, this is still better than the outrageously large inventory carrying cost of holding hundreds and thousands of different items, and the expense of moving them out to different areas. From a security perspective, as the designs evolve from repair parts to weapons and UAVs, there will be an increased need to safeguard or encrypt the CAD files to prevent easy reproduction by anyone with a 3D printer, especially the enemy. This is the most significant threat, as the Army runs the risk of losing some of its technological superiority through the widespread availability of additive manufacturing.
Word Count: 734
Citations
1. Jackson, B. (2018). NCMS and ARL open AMMP, attain $15m boost for additive manufacturing in defense – 3D Printing Industry. [online] 3D Printing Industry. Available at: https://3dprintingindustry.com/news/ncms-and-arl-open-ammp-attain-15m-boost-for-additive-manufacturing-in-defense-142219/ [Accessed 13 Nov. 2018].
2. Host, P. (2018). US Army Research Lab develops small, on-demand 3D-printed UAVs | Jane’s 360. [online] Janes.com. Available at: https://www.janes.com/article/76775/us-army-research-lab-develops-small-on-demand-3d-printed-uavs [Accessed 13 Nov. 2018].
3. Hudelson, S. (2018). Background Discussion on Desktop Metal.
4. Rotman, D. (2018). A new 3-D printer could finally let the technology live up to its promise. [online] MIT Technology Review. Available at: https://www.technologyreview.com/s/604088/the-3-d-printer-that-could-finally-change-manufacturing/ [Accessed 13 Nov. 2018].
5. Baker, B. (2018). Made to measure: the next generation of military 3D printing – Army Technology. [online] Army Technology. Available at: https://www.army-technology.com/features/made-measure-next-generation-military-3d-printing/ [Accessed 13 Nov. 2018].
Really cool post! Are the 3-D printing machines the military is using able to build any number of parts/components, or are specific machines required based on the type of part? My guess is the former, but if the latter that could pose a significant barrier to adoption of this technology.
This is fascinating and a great use case for this technology! Given the remote location, being able to have a limited stock of supplies for the 3D printer from which a variety of supplies can be produced makes total sense, even if the cost per part is higher (since inventory carrying costs will be low). What struck me as particularly important is the cybersecurity requirements around this as you mentioned at the end of your post. I’m also curious whether any thought has been given to how to best prioritize the parts which would be best made on-site using additive manufacturing vs. being carries as inventory with the other supplies. Understanding this threshold for cost, customization, frequency of use, propensity to break, and other factors may also help create a feedback loop for more robust design of critical supplies for our soldiers.
I too see huge potential but also risk in this technology. Ultimately, I think the decision on how broadly this is implemented will come down to whether innovations in reducing the cost of mobilizing these printers can outpace innovation in transportation. It may end up being a hybrid approach, I believe, where these printers are located regionally and then improvements in transportation such as the use of drones can help improve distribution from there. That said, as you mentioned, risk level would also be a factor. For example – whether the benefit of inexpensive and flexible transportation outweighs the potential cost of items being intercepted. In some cases I expect the answer would be that it does not, in which case it stands to reason that there will definitely be circumstances where having the ability to locally produce parts is highly valuable.
This article was eye-opening as I had never considered the idea of semi-mobile 3D printing. I wonder how the actual logistics of this would work. I can only imagine that it would be very difficult to have these 3D printers with a unit at all times. As such, I agree with Michael’s comment about the potential to combine this idea with some sort of transportation technology like drones.
I would also posit that very strict rules for modifying any of the plans for the products would have to be implemented. I would want to make sure that no alterations can be made after a design is signed off (e.g. no tinkering with a design on the front-lines) because of the potential security concerns if there were to be a malfunction.