Go Green – New Mantra for Tata Steel
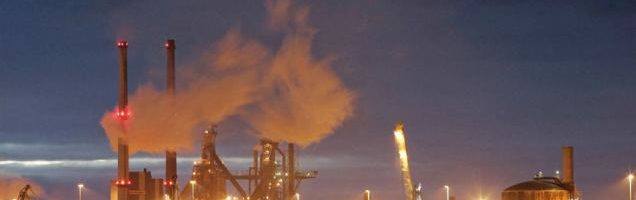
Tata Steel takes steps toward sustainable future.
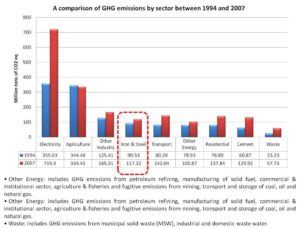
Steel is a key element of any domestic emissions reduction scenario because the steel industry is among the largest energy consumers in the manufacturing sector(Exhibit 1).Steel manufacturing involves many energy intensive processes that consume raw or recycled materials, such as iron ore and scrap metal, from around the world. Raw materials with intrinsic carbon contents (e.g., iron carbide, carbon electrodes, charge carbon, or limestone), the primary resources for steel production have substantial significance in climate impacts calculations. Virtually all of the greenhouse gas emissions associated with steel production, however, consist of the carbon dioxide emissions related to energy consumption; the primary focus of climate related impacts in the steel industry are those associated with carbon-related energy sources. About half of the steel industry’s energy is derived from coal. Tata Steel is flagship industry of Tata Group ($125 B) conglomerate. Major operations of Tata Steel are at Europe(35 Million Ton/year Steel production) and India(15 Million Ton/year Steel production).
At Tata Steel Europe electricity is main source of energy used as the process contains mainly recycled steel( which is already pure and thus needs only melting and minor alloying additions and subsequent solidification. Since the process does not involve major extraction from natural resources it is a clean process and requires less energy. Electricity costs are small but Tata Steel Europe faces costs on their carbon emissions via the European Union Emissions Trading System (EU ETS). These costs have so far been very low as a result of the free allocation of emissions permits. The real problem of ‘carbon leakage’ for is principally the blight of uncertainty about the future price of emissions permits in the 2020s and beyond, which does have a negative impact on new investment in Europe.
Tata Steel India manufactures 15 Million Ton of Steel (Steel production in India 80 Million Ton). In India at present, there is no regulation with regard to GHG emission. However, Government of India is emphasizing on technologies for energy efficiency and carbon mitigation. Considering the risks and opportunities due to climate change to the heavy energy intensive industries, Electricity Act 2003 introduced Renewable Purchase Obligations for the fossil fuel based energy consumers. As the steel industry uses captive power plants for the power generation (mostly uses Coal as a fuel), it comes under Renewable Purchase Obligations. It means Steel companies that have fossil fuel based power generation have to comply with RPO. If the obligated steel company doesn’t comply with their obligations under RPO, it will be penalized under the EA act. Either renewable power can be generated or companies can buy Renewable Energy Certificates from the renewable energy project developers. Tata Steel is currently buying 50%of renewable certificates. Purchase of REC manifests as indirect cost in steel production , increasing steel price.
Since Tata Steel is an integrated steel plant which depends on fossil fuel for power, there are limitations to increase productivity of the plant. Another threat induced by the climate change to Tata Steel is restricted availability of Natural resources. Steel industry needs natural resources mainly iron ore, coal, natural gas and dolomite. India has come up with Mines and Minerals (Development and Regulation) Act 2010, which has stringent environment clearance laws. Indian government is more concerned about deforestation. Mining resulted in deforestation and it significantly contributes to climate change. New mining grants for these minerals are restricted in near future due to the regulations.Mine lease for Tata steel will expire in 2020. New lease agreement will be based on auction and if Tata Steel does not get the lease, it will be a huge set back to Tata Steel as it will no longer be able to produce low cost steel. In addition, natural disasters like floods and storms as result of climate change can affect productivity of the mines. Tata Steel also depends on Australian Coal Flooding in Australian coal mines, led to stoppage of production at Tata Steel for a week.
Tata Steel India is working with national Metallurgical Laboratory to develop technologies which minimize usage of coal and allow use of low cost coal. To combat the effect of mining activities in surrounding areas, Tata Steel in doing plantation drive and is investing heavily in pollution control equipment. It should also invest in mining low quality coal from Indian mines to reduce imported coal supply chain disruptions due to climatic uncertainties.
Though Tata Steel India is actively working towards mitigating effects of new regulations, there is scope of more which can be done. Tata Steel can relocate its rolling facilities to areas where hydro or solar electricity is easily available, instead of relying on coal for electricity generation. It should also work to develop one third of industrial space into green belt cover, so that GHG emissions are reduced as is the norm at European plants. Installation of waste recovery equipment should be next investment for Tata Steel.
Word count :774
Sources:
1.Science Direct” The impact of climate targets on future steel production”. http://www.sciencedirect.com/science/article/pii/S0959652614004004
2.Green Clean Guide. http://greencleanguide.com/climate-change-risks-and-opportunities
3.Spinger Link : Carbon Mitigation Plan. http://link.springer.com/article/10.1007/s11027-014-9605-0
4.Journal of Environment Research and Development. www.jerad.org/ppapers/dnload.php
5.Climate change & Steel Industry ec.europa.eu/clima/events/docs/0067/4g_en.pdf
6. www.worldsteel.org/publications/…/Steel-s-contribution-to-a-low-carbon-future.html
This is a very thoughtful post on the impact the steel industry has on the environment and the different levers of change Tata Steel may be able to employ to improve the current situation.
I think the steel industry is extremely interesting in this context also because of the length of its supply chain. The main raw materials iron ore and coking coal are produced predominantly in Australia and Brazil and are then transported via bulk vessel to China, Japan, the US, India or Europe for further processing into steel. The responsibility of a large steel manufacturer with regards to climate change and environmental impact therefore may extent beyond their own operations into aiming to optimise within the context of the supply chain as a whole.
The automobile industry is one of the largest users of steel. Most recently we have seen (especially among the premium car manufacturers) a substitution effect to aluminium. Aluminium and carbon fibre in automobiles are considered as “energy efficient” given their lightweight nature leading to a lower consumption of gasoline by the end customer. Tata could therefore also consider increased innovation and R&D into developing different grades of steel that may be equally durable, but also have some of the environmental benefits of more lightweight materials.
Great post, Pooja – thanks for the information and insight. I like your idea for relocating steel manufacturing facilities to areas where solar and hydro power are available. I will look into it more, but is this cost-prohibitive – i.e. are these forms of power going to lead to costs being passed onto Tata India’s customers, similar to its current purchases of RECs? Also, what is holding Tata India back from primarily focusing on recycled steel, similar to Tata Europe? Given Tata Europe’s volume relative to Tata India’s (35M vs. 15M), I assume this would be difficult to implement, but that the raw materials (i.e. steel waste) would be available. It would be interesting to see the cost of making one of those two changes (solar/hydro or recycled steel refining) vs. the current cost Tata India is incurring by purchasing RECs.
Thanks again, really – very interesting read!