The CAD Fad: Shanghai-Based Winsun Wants to Print Your Next House
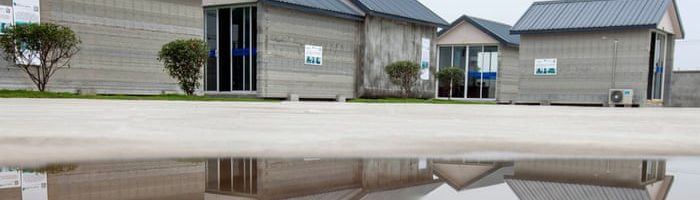
Winsun, a Chinese engineering company, uses 3D printing to create customized concrete homes quickly, cheaply, and with minimal human involvement
What’s this all about?
Waste is a tremendous problem in the global construction industry. In fact, “for every 100 houses built, there is enough material waste to build an additional 10 houses.”[1] This amount of waste causes both environmental and economic challenges. From an environmental perspective, roughly 136 tons of construction waste are sent to landfills each year in the United States alone.[1] Additionally, material waste contributes to 15% – 30% of cost overruns on construction projects[1] – which, in a highly competitive industry, puts significant pressure on operating margins.
Additive manufacturing has shown promise in addressing these issues. In construction, the 3D printing process begins with an architect designing the proposed structure using computer-assisted design (CAD) software. Next, the construction firm uses a large-scale 3D printer to bring that vision to life.
One particular area of focus among contractors has been material extrusion – also known as concrete printing — a technique which “involves extruding material through one or more nozzles mounted on a robot arm,” and “differs from the long-established sprayed-concrete method, in that it applies the material precisely and takes a layer-by-layer approach.”[3]

Okay – how can 3D printing help?
Concrete printing can benefit construction projects in three ways:
- Reduce labor, material, and equipment costs: According to research conducted by the Boston Consulting Group, 3D printers require minimal human oversight and reduce overall equipment costs, which account for over a quarter of the expense of traditional construction projects.[3] Additionally, additive manufacturing allows contractors to be more efficient in their material usage.
- Shorten project timelines: According to Rob Francis, Director of Innovation at Swedish construction company Skanska: “3D concrete printing… has the potential to reduce the time needed to create complex elements of buildings from weeks to hours.”[4] Unlike human workers, additive manufacturing equipment can work around the clock – shortening timelines and providing an important source of competitive advantage during the project bidding process.[3]
- Reduce project risk: Through limited human involvement, autonomous construction projects can greatly reduce the risk of on-site accidents and their associated liability costs.[3]
Innovation at Winsun
Winsun, a Shanghai-based engineering company, has embraced the 3D wave – transitioning away from its roots as a building materials supplier to become “the world’s first high-tech company to build houses using 3D printing technology.”[5] Winsun first experimented with 3D printing in 2005 as a way of improving the speed of its production process while reducing its reliance on costly (and highly variable) human labor.[6] By 2008, Winsun had developed “the world’s largest 3D construction printer… measuring 10 metres wide… and 150 metres long.”[6]
As a first-mover in the large-scale 3D printing space, Winsun first needed to prove that its technology could successfully build houses. In 2013, the company achieved this goal by printing ten single-story homes in under 24 hours.[5] The project was both environmentally-friendly (sourcing 50% of its “ink” from construction waste) and cost-effective (reducing overall construction costs by roughly 60%).[6]

Future challenges
Despite recent success, Winsun’s management team faces three challenges:
- Winsun must address the concerns of architects and developers who doubt whether “high-quality buildings can be constructed via 3D printing.”[6] The company has challenged this perception by inviting clients to tour its factories and encouraging architects to use 3D-printed parts in their work.[6] In the coming years, Winsun should enter high-profile architecture competitions in order to demonstrate the quality of its constructions, as well as partner with cutting-edge architects who can influence public opinion.
- Building codes lack clear standards for 3D printing, making it hard for Winsun to expand its operations. In China, Winsun’s management team has sought to modernize local building codes by working closely with the Chinese National Construction Department.[6] As Winsun looks to scale internationally, it should dedicate an employee team to assessing the attractiveness of new geographies from a regulatory perspective. Additionally, Winsun should explore partnerships with multi-national construction firms in order to leverage their ability to influence regulatory change, as well as gain access to their capital and client base.
- In order to grow profitably, Winsun must re-evaluate its production and distribution process. Currently, Winsun prints concrete parts at one of its factories before shipping finished parts to a construction site for installation.[6] However, as Winsun scales internationally, this distribution model exposes the company to high shipping costs. Despite the large up-front investment, Winsun should consider purchasing additional printers in order to accommodate international project growth.
Unanswered questions
Winsun has taken bold steps to transform the future of the construction industry. However, several questions remain unanswered:
- How might Winsun address public concerns regarding the stigma and structural soundness of 3D-printed buildings?
- Which construction projects should Winsun target next? Should it expand its technology to larger-scale buildings? In which markets?
- As concrete printing technology becomes more commonplace, how can Winsun protect itself from competition (e.g., construction firms that decide to purchase a large 3D printer)?
(Word Count: 796)
Bibliography
[1] A. O. John, & D.E. Itodo, “Professionals’ Views of Material Wastage on Construction Sites and Cost Overruns,” Organization, Technology & Management in Construction, 5 (2013) [http://search.proquest.com.ezp-prod1.hul.harvard.edu/docview/1430877905?accountid=11311], accessed November 2018
[2] Lucie Gaget, “Concrete 3D Printer: The New Challenge of the Construction Business.” 3D Printers, Materials, and Technologies (blog), Sculpteo. January 3, 2018. [https://www.sculpteo.com/blog/2018/01/03/concrete-3d-printer-the-new-challenge-of-the-construction-business/], accessed November 2018
[3] Romain de Laubier, Marius Wunder, Sven Witthöft, & Christoph Rothballer, “Will 3D Printing Remodel the Construction Industry?” Boston Consulting Group (blog), January 23, 2018, [https://www.bcg.com/en-us/publications/2018/will-3d-printing-remodel-construction-industry.aspx], accessed November 2018
[4] Progressive Digital Media Design Build News. “Skanska and Loughborough University to Test 3D Printing for Construction.” November 24, 2014. [http://search.proquest.com.ezp-prod1.hul.harvard.edu/docview/1627939035?accountid=11311], accessed November 2018
[5] Chen Juan, “Honey, I 3D Printed our Villa,” The Hindu Business Line (blog), Newtex Global Business Blogs, November 3, 2016, [http://search.proquest.com.ezp-prod1.hul.harvard.edu/docview/1835842893?accountid=11311], accessed November 2018
[6] Future of Construction Project, Boston Consulting Group, World Economic Forum, “Demonstrating the Viability of 3D Printing at Construction Scale” (PDF file), downloaded from Future of Construction Website, [https://futureofconstruction.org/case/winsun/], accessed November 2018
[7] BBC News. “China: Firm 3D Prints 10 Full-Sized Houses in a Day.” April 25, 2014. [https://www.bbc.com/news/blogs-news-from-elsewhere-27156775], accessed November 2018
[8] (Feature Image): The Guardian. “3D-Printed Cities: Is This the Future?” February 26, 2015. [https://www.bbc.com/news/blogs-news-from-elsewhere-27156775], accessed November 2018
Using 3D printing to create customized houses offers exciting opportunities for people looking for affordable housing options. In the future, I could imagine local governments working with a company like Winsun to build affordable housing because the technology reduces the labor, material, and equipment costs that are usually associated with traditional construction. In addition, there have been movements like tiny houses or prefabricated houses that people are considering who want to attain a house (and often financial freedom) at a lower cost. 3D house construction would probably appeal to people who are interested in sustainability as well as affordability in housing. The fact that 3D printing for houses significantly reduces waste might make these houses seem eco-friendly, which could have brand and marketing implications. I agree with the author that obstacles to overcome in scaling are updating building codes to recognize or incorporate 3D housing. Consumers need to know that the 3D house they buy is safe and up to codes, especially in Western markets where regulations might be more strict than in developing markets. To demonstrate the physical integrity of its product, I could imagine an ad campaign demonstrating a Winsun house surviving all sorts of challenges – strong winds, intense rain, a car running into it. This campaign might not be dissimilar from auto makers that run adds demonstrating the durability of their cars or trucks. For now, Winsun may want to focus on consumers. Overall, there are important economic and social improvements that this product achieves with its 3D technology. Whether in rural or metropolitan areas, affordable housing is a key challenge that 3D printing in construction may address in the future.
You make a great point regarding the potential for 3D-printing in humanitarian efforts. In particular, could Winsun leverage its ability to produce homes quickly and cheaply to aid in areas affected by natural disasters? They’ve demonstrated their ability to print 10+ homes in under a day for a few thousand dollars a piece. Imagine what 100 printers could do! Additionally, given Winsun’s production process uses recycled/waste material, I would suspect that homes initially built in emergency contexts could be repurposed as future “ink.”
I really like the way this article is laid out. The article mostly focuses on using 3-D printing in a residential context. Do you think there is potential to use this technology on a much larger scale in the commercial sector? I also thought this technology may change the way housing non-profits conduct business. For example, could Habitat for Humanity build a home using 3-D printing for less than they do now with traditional construction methods.
I thoroughly enjoyed reading this article. Using 3D printing to build houses seems like the obvious answer to how we will build communities in the future. I was especially struck by your report that “the amount of waste causes both environmental and economic challenges. From an environmental perspective, roughly 136 tons of construction waste is sent to landfills each year in the United States alone”. A question that came to my mind is whether this Chinese company should advance its technology to incorporate the varying method of constructing these houses based on different geographic locations of the structure. For example, in Arizona, houses can be stood up quickly because there is no earthquake or other major natural disaster risks. In contrast, a deep architectural foundation needs to be constructed prior to building any concrete buildings on top in places such as Taiwan, San Francisco, or Florida because of the risk of earthquakes and hurricanes.
Al – you raise a great point. My understanding is that Winsun’s houses (and 3D-printed homes in general) do in fact require “traditional” foundations. Therefore, Winsun would rely on a contractor or developer to 1) lay the foundation, and 2) assemble the individual elements printed by Winsun’s printers. However, as Winsun considers the option of printing homes directly on a construction site, they’ll need to consider whether to lay the foundations themselves. Given the potential regulatory advantages or partnering with a larger construction firm, my best guess is that Winsun should keep its focus specialized on additive manufacturing, rather than diversifying into more traditional methods of construction.
Thanks Daniel for such an insightful article. I was at one point considering writing about Winsun and I wanted to hear what you had to say about these 2 controversial topics around 3D printing houses:
1. Winsun Founder Ma Yihe said that “Donald Trump could build his wall much cheaper and in less than a year. We could definitely do it. Maybe at around 60 per cent of the projected cost and three to four times faster.” Although he meant this lightheartedly, how do you think Winsun management should evaluate the ethics behind projects that divide people vs. bridge gaps? Is there a place for ethics in the business of 3D printing?
Source: http://www.3ders.org/articles/20170515-winsun-founder-says-company-could-3d-print-trumps-wall-for-60-of-projected-cost.html
2. Winsun has won huge multi-year contracts with the Saudi Arabia government, and has already built office complexes in Dubai. These are regions of the world that alternatively would have employed cheap labor at massive scale. How do you think governments should regulate the 3D printing construction industry to manage the loss of livelihoods for construction labor no longer required?
Source: https://3dprintingindustry.com/news/winsun-lease-concrete-3d-printers-saudi-arabia-billion-dollar-constuction-deal-108715/
Very interesting article. I think this application has the potential to truly change lives in third-world countries. If the cost of printing an additional house can be lowered down, then governments can invest in 3-D printers and lease them to companies hoping to solves the housing crisis in under-developed countries. However, a lot of this hinges on 1) the ability of printers to print larger parts quickly and cost effectively and 20 the actual cost of 3-d printers going down over time.
This is so interesting to me- I can’t believe that a 3D printer was able to build 10 homes under 24 hours! I think this works particularly well in China because architectural beauty of homes isn’t as valued, since most live in apartment buildings, standardization is not as big a problem. I worry about this method of making homes in the future though- people in China now are becoming wealthy rapidly and expanding into suburbs. Citizens are going to care about the aesthetics and careful design of their houses more than ever. Is 3D printing of homes able to convey articulate home design? Instead of personal homes, I think this process would work very well for apartment buildings in the cities, when scale and speed is necessary to be competitive. I would actually argue that public would think 3D processes are even safer because of reduction of human error.
Awesome topic, Dan! My capstone project in undergrad involved 3D printing for petrochemical processes, and I remember thinking about the structural of 3D printed objects. A few thoughts:
1. The 3D printed approach is certainly more precise than the current spray method for applying concrete. My concern is that a 3D printed wall could fail after a few layers start moving horizontally due to uneven stresses, similar to a slipped disc in the human spine. However, I think Winsun could account for non-uniform stress when designing the CAD model and build the layers accordingly.
2. Winsun should stay small for now and tackle residential buildings. After completing several projects and earning the trust of structural engineers and designers, Winsun could consider taking on larger buildings of greater complexity.
Love this article! As I read it, I immediately thought of my dog, Nancy, her dog-husband and her two dog-children (yes I know it sounds funny but they literally live together like a happy family.) I’d totally 3-D print a new house for them, the next time they dig through the walls of their current concrete-based kernels. But why won’t I 3-D print one for myself too? Well, I don’t trust that I’d be safe in it in a certain country where crime rates tend to be high so that using concrete is the only safe way we know how to build. Irrational as it may seem, if Winsun ever seeks to expand to the developing world, which arguably needs it’s services the most, it will have to do a lot to convince the people that it’s houses are just as safe as those made from concrete.
Awesome article! I’m interested to know if Winsun is able to print other materials aside from concrete? If not, do you think this limits their growth potential? If they do, does this impact the quality of the final product/home? I’m also curious about how governments will create the proper building codes for companies like this. For example, if the home is damaged or deteriorates due to structural issues, who is liable? You also mentioned the concerns of the developers and architects; I wonder if there’s potential to leverage open innovation and get buy in from these stakeholders as Winsun grows in the future.