Rio Tinto – Mining Data like Diamond
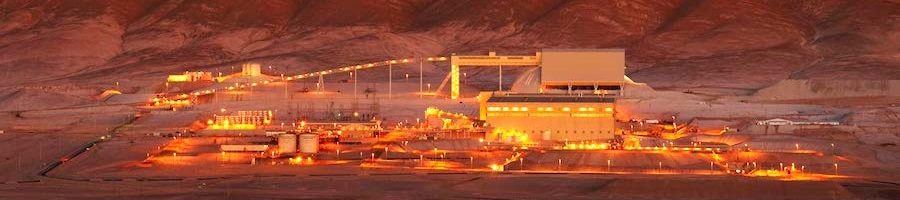
When surviving competitively afloat the mining industry’s ocean of high and low tides seemed impossible, Rio Tinto leveraged Big Data and Machine Learning to revolutionize the mining industry over the past decade, through its state-of-the-art autonomous operations.
“…we miners have little choice but to adopt the mindset of Silicon Valley… we will seek to take a new approach to capitalise on the megatrends… of the future…”
– Bold Baatar, Chief Executive – Energy & Minerals, Rio Tinto[3]
Mining industry – at the cusp of change
Surviving competitively afloat the mining industry’s ocean of high and low tides will require firms to transform. Climate change, declining ore-grades, disruptive technological-breakthroughs, ever-tightening safety and environmental regulations – are today’s norms. To cope with these changes, mining firms must embrace digitization with open arms. Today, their competitive edge is defined by how well they organize, manage and process data to optimise performance.
Rio Tinto’s ‘Intelligent’ mines – digging data more than strata[4]
Rio Tinto is one of the world’s leading mining corporations with ~$40B in revenues, ~50000 employees and leadership in extraction of many commodities including coal, diamonds, iron-ore and copper. Spotting trends and adapting to changes has been their ethos for 145 years.[5] In 2008, Rio Tinto launched the Mine of the Future program to develop technological breakthroughs to extract minerals from deeper levels while improving operational efficiencies, safety and reducing environmental impacts.[3]
Owning over 80 automated driver-less hauling-trucks that use GPS-courses to navigate complex terrains while avoiding their peers, Rio has improved material-movement efficiency (15% cost-reduction) and productivity significantly. Their automated-drills and automated-blasters have enabled operators to run multiple rigs from an offsite-console, improving safety tremendously.[6]
Internet-of-Things technology and millions of terabytes of data power these systems. Each haul-truck has 45 sensors, each processing 5TB of data daily; each processing-plant has more than 30000 sensors. Utilising machine learning has enabled Rio to extract invaluable insights from this data-stream. Their Predictive-Asset-Health tool utilizes advanced-modelling to identify variations in temperature, speed and vibration through millions of lines of sensor-outputs, performing predictive-maintenance on trucks, increasing their technical-life by over 20%.[3]
“…one of our haul-truck drivers with a passion for computers… developed an integrated real-time digital-monitoring-system for the entire pit, bringing together all streams of data in a highly usable, 3D-touchpoint, visual platform – integrating drill, dig, load and haul data, equipment performance and safety management – all in one place”
– Bold Baatar [3]
Rio’s Operations Centre in Perth is a large-scale application of this same principle – Digital-twinning (replication of real-time operations on a virtual console). Leveraging AI tools, this unit handles more than 2.4TB of data/minute from millions of sensors across 16 mines and 1000 miles of rail by integrating them into a central processer that allows offsite operators to make data-driven decisions.[4]
Also being controlled by them are the world’s biggest robots – the 1.5-mile-long, 244-car ‘Autohaul’ driver-less trains carrying 28000 tons of iron-ore across large distances.[7] Once on their course, the multitude of sensors on their wheels and couplers enable their on-board computers to communicate with their counterparts in Perth, empowering the actuators to make decisions. Removing the need to transport drivers across a million risky miles annually not only saves lives, but also saves cycle-time by eliminating unwanted stoppages. What next – autonomous-ships?
Opportunity gaps
AI has the power to reduce 610 million tonnes of CO2 emissions, save a 1000 lives, prevent 44000 injuries, and create a value of $320 billion for the industry over the next decade.[1] Becoming an insights-driven-organization is the next step for Rio. Shifting away from traditional ERP-systems to cloud-based platforms will enable a more judicious use of this data, generating insights from real-time and historical analysis, to inform day-to-day decision making.
Can Wearable VR/AR-technologies like glasses, watches and vital-trackers[2] help miners interact with systems and robots around them, simultaneously allowing central-management to capture critical real-time information and provide immediate remote assistance in case of medical emergencies?
‘Intelligent’ drones performing in-situ 3D-scanning[1] can be used to observe rock-faces that are at impossible angles to otherwise observe, signalling commands to auto-drillers to make better drilling decisions.
Long term, Artificial-Intelligence coupled with swarm-robotics can open new avenues. Cooperative segregation-bots can leverage machine learning and image-processing techniques to match against a continuously evolving image-database helping automatically separate valuable ores from debris, significantly reducing human involvement in high-risk operations. Who knows, one day swarms of underwater-mining-robots may provide access to billions of tonnes of unexplored minerals.
In parallel, upskilling humans through vocational technology-training is crucial, given the pace at which we are migrating toward algorithmic decision-making. Once mastered, AI will be the foundation for marketing initiatives – tracking consumer demands, global economic trends and emergence of new technologies to assess profitable commodities of the future. Blockchain technologies will increase transparency in transactions, enabling stakeholders to verify Rio’s ethical sourcing practices.[8]
What If…
With all the technological advancements, what if AI results in drastic reduction of human employment? On the contrary, what if the upfront investments are too astronomical to even consider? Will radical advancements take Rio to mining on iron-rich asteroids? Or, will it result in major workforce-upheavals?
Words: 799
Citations:
[1] Reports.weforum.org. (2017). World Economic Forum: Digital Transformation Initiative Mining and Metals Industry. [online] Available at: http://reports.weforum.org/digital-transformation/wp-content/blogs.dir/94/mp/files/pages/files/wef-dti-mining-and-metals-white-paper.pdf
[2] Mining.com. (2018). Deloitte: Tracking the trends 2018: The top 10 issues shaping the mining in the year ahead. [online] Available at: http://www.mining.com/wp-content/uploads/2018/01/Deloitte-Tracking-the-Trends-Global-Mining-Study-FINAL.pdf
[3] Riotinto.com. (2017). Digging, Data, and Disruption – Mining in a world of change – Bold Baatar. [online] Available at: https://www.riotinto.com/documents/170706_Digging_Data_and_Disruption_Mining_in_a_world_of_change.pdf [Accessed 13 Nov. 2018].
[4] Strharsky, J. (2017). The future of mining: more digging through data than strata | AusImm Bulletin. [online] AusIMM Bulletin. Available at: https://www.ausimmbulletin.com/opinion/future-mining-digging-data-strata/ [Accessed 13 Nov. 2018].
[5] Riotinto.com. (2017). Annual report. [online] Available at: http://www.riotinto.com/investors/annual-report-16577.aspx [Accessed 13 Nov. 2018].
[6] Riotinto.com. (2018). Mine of the Future™. [online] Available at: https://www.riotinto.com/australia/pilbara/mine-of-the-future-9603.aspx [Accessed 13 Nov. 2018].
[7] Marr, B. (2018). The 4th Industrial Revolution: How Mining Companies Are Using AI, Machine Learning And Robots. [online] Forbes. Available at: https://www.forbes.com/sites/bernardmarr/2018/09/07/the-4th-industrial-revolution-how-mining-companies-are-using-ai-machine-learning-and-robots/#3b26d47d497e [Accessed 13 Nov. 2018].
[8] Jacques, J. (2018). IMAARC, Melbourne: We won’t wake up tomorrow as Microsoft, but how will we pioneer the mining industry into the 21st Century?. [online] Riotinto.com. Available at: https://www.riotinto.com/documents/181029_J-S_Jacques_IMARC.pdf [Accessed 13 Nov. 2018].
Mining is a really interesting application of automation and AI. I would guess the single biggest factor as to whether or not you’d consider full-scale automation is the “life” of the mine in terms of extraction period (linked below), which varies considerably both by commodity and by specific mine. While it would be very tempting to automate a mine that you knew you going to be running for the next 70 years, some mines appear to take as few as 2 years to fully extra which would really make the business case difficult to justify. I don’t know the sector well enough to weigh in on the extraction period distribution, but I would guess that very few meet all of the criteria.
One of the most frustrating elements of automation and IoT in remote locations like mines is the lack of telecom infrastructure. Telecoms that own spectrum don’t want to put up high bandwidth towers in the middle of nowhere, and Mining companies may be willing to pay for the infrastructure but lack the spectrum licences to legally operate. It’s not an unsolvable solution to bridge the gap, but it definitely takes a lot of time and effort.
Duration of the extraction period of a mine, by selected commodities:
https://www.statista.com/statistics/255479/mine-life-per-commodity/