Printing the Tip of the Spear: Additive Manufacturing at the U.S Military’s Battlefront
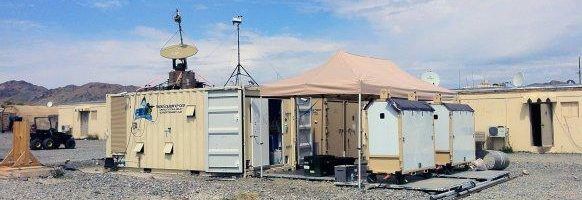
Getting repair parts to sailors at sea and soldiers at the front lines of combat is a logistical nightmare. The U.S. Military thinks Additive Manufacturing technology can help.
Examples of advanced technology have throughout history found a home in military applications. In peacetime, defense contractors stoke the fears of military leaders, convincing them to procure the most advanced systems money can buy. However, in wartime, the soldiers, sailors, and marines on the frontline of battles across the world are left to use, maintain, and repair this equipment, often across the globe and in inaccessible locations. In times like these, where getting specialty parts through a cumbersome logistics and supply chain is nearly impossible, the U.S. Military has turned to additive manufacturing (AM) as a potential solution.
AM is an attractive technology for process improvement within the U.S. military “as a way to increase availability and save costs by quickly producing small replacement parts onsite instead of waiting for the supply chain to send equipment far off.” [1] The recent history of AM initiatives within the military has been characterized by pilot programs designed to test the feasibility of this technology without going all-in on the investment.
Since 2013, the Army has installed three Expeditionary Lab Mobile (ELM) boxes at remote outposts in Afghanistan. “The 20-foot container comes equipped with 3D printers, computer-assisted milling machines, and laser, plasma, and water cutters, along with common tools like saws and welding gear. Parts can be made of plastic, steel, and aluminum. With a generator, heating and cooling systems, and satellite communications all manned by two specially trained engineers, the 10-ton ELM is effectively a digital fabrication workshop in a box.” [2]
The Navy is also currently investing in pilot projects to reap the benefits of AM, including on my own ship, the USS ESSEX (LHD 2). “The U.S. Navy already has 3D printers aboard ships and has used them to produce customized drones aboard the United States Ship (USS) Essex while underway. The availability of the 3D printer allowed the USS Essex crew to save space by only carrying the electronic components and then “print” highly customizable, mission specific components of the drone as needed. This capability can further reduce the requirement to carry critical electronic components since the printers can now produce them as well.” [3]
Military leadership has clearly bought in to the notion that AM will be key to military success in the near future. Lt. Gen. Steven Rudder, the Marine Corps deputy commandant for aviation, said just last month, “I think you’ll see in the next year … you’ll see additive manufacturing be the kind of the headline of how far we’ve come with efficiencies … out in the field.” [4]
However, while these pilot programs have been interesting to military leaders, no concrete plans are in place for a long-term broad-based rollout of AM technology. According to Lt. Benjamin Kohlmann, a fighter pilot and member of the Chief of Naval Operation’s Rapid Innovation Cell (CRIC), “Additive manufacturing has to get to the point where a part printed on the machine has the same strength and overall properties that a cast part has,” he said. “In some cases that is the case today. In others, in many more cases, it’s not…. Tensile and strength ratings don’t meet what’s required for high-stress environments.” [5] Indeed, the term “mil-spec” has come to signify the ultimate in ruggedness, and current transportable additive manufacturing platforms may not be ready to meet the stringent demands of combat equipment, where a failed part can result in loss of life.
In order to cross the chasm between an attractive future technology and one that is ready to be implemented in a broad rollout across deployed forces of the U.S. Military, it is imperative that the Department of Defense (DoD) immediately begin working directly with defense contractors to procure systems that have an initial system design that incorporates additively manufactured repair parts.
While defense contractors are wary of this, as repair parts logistics tails can add up to a significant portion of a particular program’s profit, the DoD should form contractual agreements whereby defense contractors that own these designs can be compensated on a license-fee model, so that each time a data file is used to print a part in the field, the company earns a fee.
In the medium term, it is imperative that additive manufacturing technology progress to a point at which printing platforms are modular, small enough to fit in logistics transport boxes, and accurate enough to meet stringent mil-spec standards.
This proposed approach raises a few important open questions that are as of yet unresolved:
- Would the economics of a license-fee system for AM-made parts be cost-efficient?
- With a security environment increasingly susceptible to data breaches, how do you ensure that military technology is safeguarded against hacking and therefore reproduction when you send design files over the internet?
(787 Words)
Sources
[1] Werner, Ben. “Better Logistics, 3D Printing Will Quickly Return Navy and Marine Corps Aircraft to Service.” U.S. Naval Institute News, October 8, 2018. [https://news.usni.org/2018/10/08/37127], accessed November 2018.
[2] Hill, David. “3D Printing on the Frontlines – Army Deploying $2.8M Mobile Fabrication Labs.” Singularity Hub, February 28, 2013. [ https://singularityhub.com/2013/02/28/3d-printing-on-the-frontlines-army-deploying-2-8m-mobile-fabrication-labs/], accessed November 2018.
[3] Begley, Leslie D. “Increasing Capabilities and Improving Army Readiness through Additive Manufacturing technologies.” U.S. Army War College, January 4, 2017. [http://publications.armywarcollege.edu/pubs/3389.pdf], accessed November 2018.
[4] Werner, “Better Logistics, 3D Printing Will Quickly Return Navy and Marine Corps Aircraft to Service.”
[5] Stevenson, Brittany. “U.S. Navy Installs 3D Printer on their First Ship, The USS ESSEX.” 3DPrint.Com, April 23, 2014. [https://3dprint.com/2554/uss-essex-3d-printer-navy/], accessed November 2018.
It was very surprising to me that it seems like the U.S. Military has been using this additive manufacturing approach since at least 2013, if not before. This is not something we typically hear about in the news cycle, probably because of the next question on everyone’s mind, which is how much are the taxpayers paying for this technology. I thought cost would be the biggest hindrance to why AM hasn’t grown in volume, but your comments on the strength and properties of the component make absolute sense in the military setting.
I wonder with the growing popularity in 3-D printing of guns and the latest controversy and court ruling about this, whether it has any downstream implications to the military (https://www.cnn.com/2018/08/28/us/3d-printed-guns-cody-wilson-blueprint/index.html)?
I think it is no longer a question of if, but when 3-D printing infiltrates every part of the military. Just recently the Marine Corps created the world’s largest 3-D printer to “print” a concrete barracks (https://newatlas.com/marine-corps-systems-command-3d-printing-barracks/56261/).
Would the economics of a license-fee system for AM-made parts be cost-efficient?
Although I don’t have as much experience in the additive manufacturing space, if I draw a parallel to new SaaS models I do believe the license-fee system makes economical sense and could be profitable for both the defense contractors who own the IP and for the military. Conceptually, what 3D printing does is allow the user to reuse a blueprint (the IP) multiple times, extracting value every time a new unit is printed. And in this case, whomever owns the IP should get compensated a royalty fee for its use. One way the military can aim to reduce their costs as they scale, however, is to negotiate volume discounts (i.e. if they print > x number of parts in one year, the license price per unit reverts to a reduced amount). On the user side, this would allow for economies of scale, and from the vendor side, this would be beneficial in that it encourages higher use of its technology (and thus higher total royalty revenue).
If the jet engines in Boeing Dreamliners can be 3D printed–engines that withstand various objects colliding with it at high speeds and extreme conditions–I believe military parts certainly can be as well. Like all new technologies–hopefully it’s just a matter of time until new advances lower the cost and increase the quality of the finished products!
I’m not surprised to hear that the military is dipping their toes into 3D printing. Makes lots of sense for teams who need quick repairs to standardized equipment in hard-to-reach areas. The point you raise about security does seem like a huge issue they’ll need to tackle. However, I have to imagine that all kinds of super confidential information finds its way over similar channels, so this should be solvable (with the exception of certain equipment).
I do wonder what this shift means for the massive defense contractor industry, as it will require a shift from supply chain to intellectual property provider (ie. design plans). Will existing partners embrace this shift, or will major lobbying efforts stymie innovation in this space? How do AM costs compare to traditional manufacturing so far?
https://www.designnews.com/materials-assembly/3d-printing-recycled-plastic-replace-soldier-s-supplies/137004619859478
The article above talks about 3D printing using recycled materials that are already in the field, such as water bottles and bags. Based on what we learned in the Nike case this week, where sustainable materials are often less trusted on quality, do you think this “green” initiative will help or hurt the mainstream movement towards AM in the military?
Great look at how the military is using AM! I’ve consistently heard about cost overruns in major military procurement projects. Some explanations I’ve read attribute this trend to the rapidly growing complexity of major defense projects. It sounds like additive manufacturing will continue to add complexity to the military hardware supply chain. As you note, there will be licensing requirements as well as the need to transmit plans to various forward battlefields. I would be curious to understand how AM can be managed in a cost-effective way or perhaps be used to untangle military procurement costs.
Really interesting article! To your second question, I, too, wonder how “safe” bringing our weaponry online could be. It seems that while this certainly would be helpful to us, it puts us at further risk of 1) codifying our weapons for others, and 2) possibly increasing the accessibility of dangerous weapons in countries we are opposing, if the technology were to spread. Additionally, if this were to significantly decrease costs, could this make weapons more accessible to rebels and other forces that we currently have a resource advantage over today?
Fascinating introduction to how the military is using additive manufacturing to simplify the supply chain and speed up delivery for replacement parts. Like with other military innovations, such as radar and carbon fiber, I wonder what the civilian applicability of such decentralized manufacturing of niche replacement parts could be. Would a business that uses AM to reproduce all sorts of replacements parts for industrial machinery or household appliances be viable? What are the challenges and risks that such a business would face?
Great job explaining how the military is using additive manufacturing! The question of security is an interesting one. Information compromise is a security threat the military has always dealt with, but the introduction of additive manufacturing presents another vector for attack in the physical world. By implanting a flaw in the production process, adversaries could cause critical pieces of machinery to malfunction. Controls must be in place at every level of the supply chain, from the acquisition of raw materials to the additive manufacturing machinery to the final product.
It does seem like people are very focused on this issue. Dr. Mark Yampolskiy at the University of South Alabama is working on “side-channels”, where acoustic emanations from a printer can be used to detect deviations in output. [1]
[1] https://www.southalabama.edu/departments/publicrelations/pressreleases/110218printing.html
Really interesting take on additive manufacturing in an important application! I personally find it surprising that the military is not more all-in on 3D printing, as I think the applications in the field, as you demonstrate with your story of the 3D printer on the ship, are really compelling. Being able to carry less supplies, because you have one feedstock capable of making all sorts of repair parts, appears very valuable.
Your point on design files being hacked is well taken. However, I would argue that this is not necessarily a flaw of 3D printing inherently. Most design files are shared over the internet these days, and if they are not for security purposes, then you could easily have a local 3D printer that was not connected to the internet. So, I think this is generally an issue that the industry can get past in commercializing this tech.
Super interesting article, thank you! Although I never thought about this application before, it seems to be a natural match for the military during operations. Logistics being extremely complex in war times, this solution could help fixing a lot of complicated situation. However, this argument only holds if the replacement parts can be sustainable during at least the entire length of the mission. According to Benjamin Kohlmann’s comment it seems that AM don’t deliver in consistent quality and durability. Given the risk at stake, I don’t think the military can implement AM in the long term as long as this issue is not fixed. Moreover in the cost analysis, I believe that this only make sense if an external logistic is not required anymore to fix the underlying issue. However I would argue that military cannot be assessed the same way as a business operation and that we should value the critical gains in readiness during operations in stressed conditions.
Great article on the future of the overall national defense industry. Thinking of the author’s recommendations and raised questions I would not be concerned about data transfers as current technologies of end-to-end encryption are really secure. The question that I would raise is how far should we go in replacing spare parts with a 3D printer and a stock-up of “raw material”. Wouldn’t it be safer and more reliable to just carry some amount of drone details that are often replaced than only having a #D printer?
This is a very insightful article and a very interesting topic for additive manufacturing. As I thought about using AM for military applications I first thought about transportation, maintenance, and the need for an experienced crew to run the machine. However, these three aspects are all strengths of the military. The military can transport, maintain and ship any piece of equipment anywhere in the world better than anyone. I think you point out the real hurdles: 1) strength of the parts and 2) developing a commercial model that has buy-in from defense contractors. Incorporating 3D parts into the original design seems like the right solution. I wonder if you could also use a 3D part as a temporary replacement until cast parts arrive. It might also be the case that 3D printed parts will only be able to replace some cast parts, ultimately limiting its application in the industry. Also, maybe some defense contractors would be willing to come to the site and run the 3D printer on site, in other words, this would be a service the military would directly contract out. I am glad to hear that 3D printing is already being used, the future looks bright for 3D printing in the military!
Fascinating topic and very well-written.
The second question you raise I found extremely relevant and even disturbing. In addition to data breaches, I also wonder whether there is a limit in terms of the weapons that could be produced through AM. I have seen elsewhere that it is already possible to “print guns”, expect for a few mechanical components that are really complex. Besides, even without data breaches, probably it’s possible to back-engineer some parts in order to reconstruct the data files.
Putting both points together, my concern about this topic is: what are the safety impacts of AM being applied to weapons and other military equipment, both in a war scenario and in a civil/urban environment?