More than Looks: Audi’s Smart Warehousing Disrupting Automotive Industry
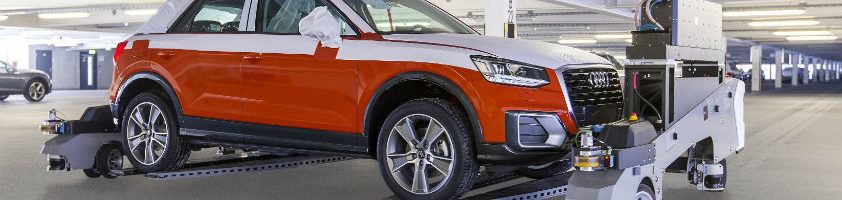
Can the industry that created the assembly line adapt to an ever-changing digital world? What exactly is inside Audi’s smart factory?
In an industry that created the assembly line, the concept of digitalization within the supply chain can be daunting. With complex networks of suppliers, a widespread footprint of unique plants, and intricate production lines, the automotive supply chain may be tough to disrupt. If manufacturers don’t embrace digitalization, however, they risk giving way to new competitors – looking more like technology companies than traditional manufacturers. As customers demand more flexibility and customization, become more accustomed to ride-sharing and even autonomous vehicles, the transportation industry begins to look very different. Audi, known for its luxury cars and cutting-edge technology, is actively addressing these challenges by digitizing its supply chain and testing out innovations for its smart factory – the factory of the future. It has plans to disrupt its entire supply chain network and revolutionize the way cars are produced, aiming to remain competitive in this ever-changing world.
Towards a Smart Factory
Supply Chain 4.0 brings forth the idea that companies need to become faster and much more precise[1] in the way they handle logistics and operations. Opportunities exist within planning, physical flow, performance management, order management, collaboration, and strategy to digitize the ecosystem and increase overall efficiencies. Audi is testing various aspects of its supply chain, ultimately hoping to build a factory that is entirely digitally-connected. This smart factory would include a “combination of production, information, and communication technologies with the potential for integration across the entire supply chain”[2].
Modular Assembly
Audi’s biggest innovation is the idea that the traditional assembly line has “had its day”, introducing a new form of production known as modular assembly. This approach includes individual work stages manned by one or two workers and connected via driverless transport systems known as “Automated Guided Vehicles (AGV)”. A central computer monitor manages all activity, and the AGVs provide stations with the supplies they need in a just-in-time fashion. Modular assembly allows for flexibility – both in re-directing vehicles when there is a bottleneck, and in future technology improvements, as Audi would no longer need to re-adapt an entire line but rather replace only affected stations. The manufacturer claims that this form of assembly would lead to an increase in productivity of at least 20%[3].
Toolmaking
“Toolmaking has always been one of Audi’s core competences. With our inventive talent, we succeed again and again in pushing the boundaries of what is technically feasible,” says Prof. Dr. Hubert Waltl, Board of Management Member for Production at AUDI AG[4]. This has been proven by their various new developments in the department, including intelligent tools and 3D printing. Intelligent tools come in the form of self-controlled instruments that monitor the flow of material and ensure optimal distribution and precision in parts creation. 3D printing allows Audi to be cost-efficient in the production of complex parts, particularly by allowing a more tailored and specific cooling channel for die casting molds and hot working segments. This optimized performance is expected to reduce cycle time by 20%6[5].
Robots
Contributing to this smart ecosystem is the addition of robots, both in the production process itself and as driverless vehicles. Along the production line, Audi is working to advance human-robot cooperation, hoping to relieve employees of monotonous and ergonomically negative tasks. As vehicles, Audi has developed two concepts – its AGV and its Laser Tracking System. AGVs supply parts from the warehouse to the production line, and are controlled for safety and optimized routes. The Laser Tracking System is a system that can guide multiple driverless vehicles, for example to load cars onto transport containers3.
Recommendations
When these technologies are put together in a factory, Audi can expect to see added efficiencies in physical flow. One additional benefit of digitalization is the accessibility to an entirely new set of data. Audi should begin to think about how to leverage that data to forecast demand and implement predictive analytics – helping it become more responsive and competitive. Additionally, Audi should begin to think about planning and collaboration to integrate its supply chain across the various players in its network, enhancing visibility and ultimately working in an integrated manner.
Food for Thought
As Audi heads towards its smart factory, how is it approaching employment challenges and the need for high-skilled workers? How does implementation of these multiple technologies play out, and what role will technology companies play in the competitive landscape?
(793 words)
[1]Alicke, K., Rexhausen, D., Seyfert,A. Supply Chain 4.0 in Consumer Goods. McKinsey & Company. April 2017.
[2] Schulz, B. (2017, 09). Driving a new generation of toolmaking. MoldMaking Technology, 20, 46-49. Link.
[3] Feigle, K. Audi TechDay Smart Factory. Audi Media Info. November 2016.
[4] Audi toolmaking is the best in the industry. (2015, Nov 12). M2 Presswire
[5] Ford, J. (2017, Feb 06). Audi partners with additive minds for 3D formulations. The Engineer (Online)
Very interesting article! The question you raise about how to approach potential employment issues is key for Audi’s success. If Audi does the rollout of its automation process too fast there could be significant risks that could harm production and supply chain operations.
Employees from other plants could see the automation initiative as a threat for their current jobs and seek to create or join labor unions. This at the same time could increase total labor expenditures or diminish the impact of expected efficiencies with automation. More drastic actions that employees could take could be strokes in current plants operating at capacity creating additional production problems.
I believe Audi should focus more on the efficiencies that don’t require lay-offs (as you mention for instance 20% decrease in cycle time) and implement a massive training and relocation program for the jobs that might be at threat. For instance, with automation Audi might not need workers in the line but will need more people in the innovation and R&D departments. Skilled workers with high expertise and experience that receive the appropriate training could be a great add to those teams.
Thank you for the interesting aritical! It is exciting to see how Audi is making revolutionary changes to its manufacturing line with the concept of Industry 4.0. It seems to me that so far the practice is still more at experimenting phase to test out the feasibility of the technology.
From business perspective, there are two elements that I am curious to see going forward. First, how does the business equation look like with increased investment in automation and reduced cost of labor. Does it have a profitable business case to justify the investment? Second, how such smart factory upgrade decison time table might differ from country to country given the different levels of labor cost. At country level, will the relatively high labor cost in developed countries end up becoming the driving force for industry upgrade and, as a result, helps developed countries to lead again in the next era of industry 4.0.
Great read! Your question about the labor force is an interesting one, and I was intrigued by Juan’s point about automotive industry workers forming unions to minimize lay-offs related to digitization. Funnily enough, when I started to do some research on how labor unions are reacting, I found an article from the 1980s where a similar shift was occurring! In 1984, General Motors (GM) was investing in significant automation increases in their factories through the use of robots and other technologies. In the end, it seems as though the United Auto Workers union decided not to fight against the technology, acknowledging that automation was a necessary step to increasing car quality and securing the number of jobs that will remain once the innovations are put in place [1]. This was a good lesson to me that the digitization we see today is simply the next iteration of a production improvement process that has been occurring for decades as new technologies emerge. I wonder if as the technology exponentially improves, the impact we will see on the labor force will be similarly much greater than it was back then.
[1] https://www.washingtonpost.com/archive/politics/1984/07/06/auto-workers-accept-automation-in-exchange-for-job-security/66a9adda-66ec-4a25-aa5c-7663962daddb/?utm_term=.e85bff22b9bb