“Limb”-itless Solutions with 3D PrintAbility: An Example of an Additive Manufacturing Breakthrough in the Prosthetic Limb Production Supply Chain
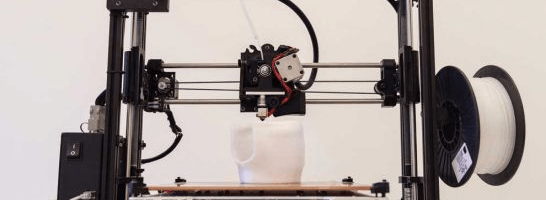
NIA Tech's additive manufacturing technology, 3D PrintAbility, is increasing access to prosthetic limbs and other mobility devices in developing countries by disrupting the supply chain of prosthetic limb production.
The Benefits of Additive Manufacturing to NIA Tech and the Prosthetic Limb Industry
It is estimated that as many as 30 million people around the world suffer from lack of or damage to one or multiple limbs resulting in required use of prosthetic limbs, braces, or mobility devices. Unfortunately, it’s also estimated that less than 20% of patients have access to these types of devices [1]. This lack of access is especially devastating in developing countries where mobility limitations affect access to education and employment [5].
Historically, producing prosthetic limbs necessary to improve quality of life has been an expensive and labor-intensive process. Problems around cost and production complexities are amplified when the patients are children or people living in developing countries due to the customized nature of prosthetics which are specially made for patients keeping in mind a variety of measurements, the patient’s weight, intended activities, etc. [3]. Since children are still growing, they’ll need several iterations of prosthetic limbs as they age [8]. Additionally, in developing countries there is an estimated shortage of approximately 40,000 trained prosthetists (the people who measure, design, fabricate, fit, and service prosthesis) [1]. Access to prosthetics is lacking due to these high production costs, complex production processes, and shortage of trained prosthetists.
Prior to the use of additive manufacturing (AKA 3D printing), prosthetic limbs were made through a variety of labor intensive steps. Measurements would be taken and a plaster cast would be created of the anatomy that was to be fitted with the prosthetic. Plastic would be heated and vacuum formed to the mold to create a socket. The other portions of the prosthetic would be made from different materials such as plastic, titanium, and wood through processes such as injection molding, extruding, die-casting, planning, sawing, and drilling [4]. All the pieces would then be assembled using a variety of methods including bolts, adhesives, and laminating. The process could take up to 2 weeks to deliver and could cost upwards of $30,000 depending on the prosthetic [2,5].
3D PrintAbility is a digital toolchain that was designed by NIA Tech to increase access to mobility devices such as prosthetics in developing countries by providing new technology to empower local healthcare technicians. 3D PrintAbility mimics the traditional manual production process in a digital environment. Instead of utilizing a plaster cast, it uses a scanner to capture the external shape of the limb. Instead of modifying the prosthetic device by adding or subtracting in plaster, it uses 3D modelling software to add or subtract material. Instead of physically wrapping the cast in plastic, it wraps the device digitally to create a 3D model which is then produced using additive manufacturing [5]. This method is faster, cheaper, and more efficient than traditional production techniques and has the potential to increase access of prosthetics to people in developing countries. With new additive manufacturing capabilities, the production can be completed in a matter of hours and the cost can be lowered to under $100 [2,5].
Short Term and Medium Term Goals
NIA Tech recently conducted a 6-month trial utilizing 3D PrintAbility to produce prosthetics for a small group of children from Uganda to prove feasibility. Now they’re completing field testing with clinical partners in Cambodia, Tanzania, and Uganda. NIA Tech is looking to deploy their technology to early adopters in the short term. NIA Tech’s medium term goal is to use their technology to fit 8,000 people with additive manufactured mobility devices within five years, across approximately 20 sites in developing countries, training the local healthcare technicians along the way [1].
Recommendations for Short Term and Medium Term
In the short term NIA Tech should really makes sure to listen to the local technicians as they continue to test and roll out the use of 3D PrintAbility technology in the developing country healthcare space. The success of the product and mission depend heavily on technicians being able to effectively utilize the technology. It’s always important to get suggestions from the frontline during projects like this as well as get buy in. Suggestions and learnings can be used to improve the product and training procedures prior to moving on to new locations.
In the medium term NIA Tech should consider looking into utilizing some alternative materials moving forward. Additive printing technology is available in a wide variety of plastic, rubber, and even metal materials currently which may prove beneficial for certain applications (due to environmental challenges or special circumstances regarding patients) [9].
Open Questions for Classmates
What threats should be considered while attempting to scale up the use of additive manufacturing to produce prosthetics in developing countries? Could 3D printing become a strong contender for prosthetic production in developed markets or will consumers continue to value traditionally produced prosthetics which are currently more sophisticated and durable?
Word Count (797)
Sources:
[1] Ian Birrell, “Print Your Own Body Parts,” Mosaic, February 19, 2017, https://mosaicscience.com/story/prosthetics-amputee-3D-printing , accessed November 2017.
[2] TJ McCue, “3D Printed Prosthetics,” Forbes, August 31, 2014, https://www.forbes.com/sites/tjmccue/2014/08/31/3d-printed-prosthetics/#6f415f5133b4, accessed November 2017.
[3] Bill Copeland, CP, LP, “The Process of Creating a Prosthesis,” Amputee Coalition, 2001, http://www.amputee-coalition.org/resources/creating-a-prosthesis/, accessed November 2017.
[4] ”Artificial Limbs,” How Products are Made, http://www.madehow.com/Volume-1/Artificial-Limb.html, accessed November 2017.
[5] “3D PrintAbility,” NIA Tech, http://niatech.org/3d-printability/ , accessed November 2017.
[6] Roopinder Tara, “Changing Lives – Custom Orthotics Let Kids Walk,” Engineering.com, March 13, 2017,https://www.engineering.com/DesignSoftware/DesignSoftwareArticles/ArticleID/14489/Changing-LivesCustom-Orthotics-Let-Kids-Walk.aspx, accessed November 2017.
[7] Amy Fallon, “How 3D printing can revolutionise the medical profession,” The Guardian, September 29, 2017, https://www.theguardian.com/media-network/2016/sep/29/3d-printing-revolutionise-medical-profession, accessed November 2017.
[8] Audrey Wilson, “Innovative trial to put printed prosthetics in reach,” Phnom Penh Post, September 3, 2016, http://www.phnompenhpost.com/post-weekend/innovative-trial-put-printed-prosthetics-reach, accessed November 2017.
[9] Anatol Locker, “9 Basic Types of 3D Printers – 3D Printing Technology Guide,” All3DP, July 20, 2017, https://all3dp.com/1/types-of-3d-printers-3d-printing-technology/, accessed November 2017.
I think the question you’ve posed is an intriguing one, regarding whether 3D printing for prosthetic production is better suited for developing vs. developed markets.
In developing markets, benefits such as cost efficiency, faster production speed, and improved patient access seem undeniable, but it seems that there is still a quality and durability deficit when compared to traditionally-manufactured prosthetics. I imagine that this gap will only continue to narrow in the future as improvements in biomaterials and biomechanical design are made. I also wonder whether there are any studies on whether the long-term cost of a 3D printed prosthetic is still competitive even after replacement costs and failure rates.
In developed markets, I believe there is still likely to be strong demand for 3D printed prosthetics among potentially underserved populations. One example would be children, who may need numerous expensive prosthetics as they grow up or may have a more favorable perception of colorfully- or playfully-designed prosthetics — 3D printing company Cyborg Beast is one such company that serves this market.
It seems to me that a key constraint in scaling the 3D-printed prosthetics across countries is the raw material inputs – both in terms of access and reception by the constituent population.
As you noted, 3D printing is currently specific to certain materials. So whether or not 3D PrintAbility will be able to penetrate a certain market will rely on ready supply of those materials, an obstacle possibly more pertinent to developing countries than in developed.
However, as Karen mentioned above, there is also a perception component to raw materials, particularly in developed markets where there is the luxury of choice. Do consumers have a preference between materials, for plastic prosthetics or for rubber? If they do, is the quality gap real or perceived? In addition to ensuring an adequate supply of raw materials, 3D PrintAbility may do well to consider a marketing campaign to educate customers and to help shape market reception and demand.
The applications of 3D printing in health care have been really exciting to follow. Building on Karen and Chloe’s points, I think this can catch on rapidly even in developing markets. With trends moving toward value based care and the issues raised around providing better care to underserved populations, this is a great way to make an impact. I am curious to see how the 3D printed prosthetics improve feel for patients. There are many documented studies around patients being unwilling to wear their prosthetics due to discomfort and even pain. I’d like to know more about how the quality of materials and customization made possible with 3D printing improves or hurts the patients’ willingness to use. Considering adherence is a huge point of debate, I hope that 3D printing can be a game changer here.