Keeping fighter jets in the fight; additive manufacturing’s solution to supply chain woes
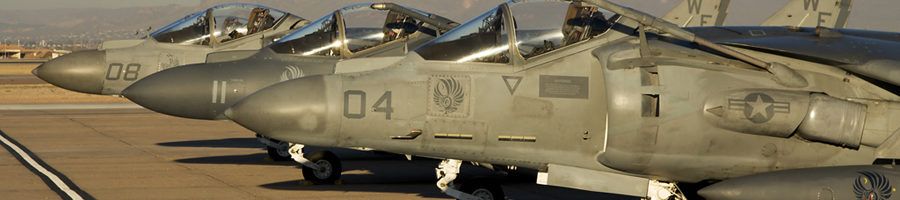
How additive manufacturing could be the solution to part shortages in military aviation
The Joint Strike Fighter program was intended to be a cost effective replacement for an aging fleet of legacy fighter aircraft across the Department of Defense (DoD). However, cost overruns and engineering glitches delayed the implementation of this program. The quick fix to cover this unintended gap between aircraft generations was to overextend the useful life of legacy aircraft such as the F/A-18 Hornet and AV-8B Harrier (pictured). Unfortunately, the flexibility of this decision was not met with an equally flexible supply chain. Most legacy replacement parts are no longer manufactured because plant lines were shut down long ago, and the low, sporadic demand for such individualized parts makes any restart economically unfeasible. Two demanding campaigns in Iraq and Afghanistan coupled with this parts shortage have resulted in a dearth of flyable aircraft and an improvised practice of cannibalizing spare parts from some aircraft to keep others alive.
Additive manufacturing (AM), in principle, would have not only allowed maintainers to produce these “one time only” parts on short notice, it could have also greatly streamlined the entire supply process for replacement parts. “If I have a mission and take two spare water pumps, they only can do a water pump function,” [Captain Matthew Friedell, Marine Acquisitions Command] said. “But if I bring eight pounds of powdered aluminum instead, I can make 300 parts that might break down.”[1]
The principle of AM creating a highly responsive supply chain is alluring, however there is a significant and necessary roadblock that prevents hasty implementation. The Federal Aviation Administration (FAA) requires certification and qualification of critical parts before they can be implemented for commercial (or military) use. This means AM development for aircraft parts has been sluggish.[2]
The DoD therefore relegates the use of AM to non-critical parts in order to adapt to this FAA constraint. Even so, the fact that AM has been showcased in any form is a huge leap for short term proof of concept. On April 16, 2018, Marine Fighter Attack Squadron 121 manufactured a plastic bumper for a landing gear door that was produced locally by a 3D printer[3]. This measure avoided the need to order an entire replacement door from the manufacturing plant. Besides the cost savings, the time saved was game changing, especially for a deployed squadron whose mission can live or die by “Just in Time” supply of aircraft parts.
Experimentation on non-critical parts supply is a short term focus for the DoD, however long term interest lies in AM’s influence on R&D prototyping. The Defense Advanced Research Projects Agency (DARPA) already chartered this territory back in 2013, when a requested proposal to design a vertical takeoff and landing (VTOL) aircraft was additively manufactured by Boeing in just 30 days vice the several months it could have taken without AM[4]. With the emerging generation of highly evolving unmanned vehicles set to replace manned fighters, AM will fill an even stronger role in R&D prototyping.
Though R&D prototyping is an interesting application of AM, the supply chain issues for critical aircraft parts are a more tangible and relevant focus point for this cutting edge technology. A key sticking point is producing metal parts that are load bearing and resistant to high temperatures. The current AM process for metals requires zapping millions of microscopic particles of powder with a LASER using variable levels of heating. This process causes a lot more variability in the structural integrity of the metal, a variable that did not exist under conventional machining[5]. To overcome this more pressing hurdle, more time and money needs to be invested in this collective aerospace challenge. Furthermore, the DoD needs to consolidate the AM effort under one umbrella to enhance “economies of learning”. A 2015 report by the Government Accountability Office (GAO) found that the “DOD does not systematically track and disseminate the results of additive manufacturing efforts department-wide, nor has it designated a lead to coordinate these efforts.”[6]
If the DoD can drastically consolidate research efforts in the short term, then the long term possibility of easing critical part shortages using AM would be entirely feasible. In fact, it could go a step further and truly bring the supply chain as close as possible to the point of consumption. A squadron of aircraft, remotely deployed and cut off from the traditional supply chain, could have the organic capability of producing critical aircraft parts overnight using AM. The squadron would remain healthy no matter how remote the deployment location. But what about the other hurdle? Should the FAA ever “digitally” certify the blueprints of an aircraft replacement part without the requisite physical testing?
[Essay is 777 words without footnotes]
[1] “Chain Reaction. Why Additive Manufacturing is about to transform the supply chain” by Alan S. Brown (Oct 2018)
[2] “An overview of 3-D printing in the manufacturing, aerospace, and automotive industries” by Choon Wee, Joel Lim, Kim Quy Le, Quigyang Lu, and Chee How Wong (2016)
[3] Marines use 3-D printer to make replacement part for F-35 fighter” by Stormy Mendez (April 2018)https://dod.defense.gov/News/Article/Article/1498121/marines-use-3-d-printer-to-make-replacement-part-for-f-35-fighter/
[4] “3D opportunity in the Department of Defense; Additive Manufacturing fires up” by Matthew J. Louis, Tom Seymour, and Jim Joyce of Deloitte University Press (2014)
[5] “Getting past the hype about 3-D printing” by Jaime Bonnin Roca, Parth Vaishnav, Joana Mendonca, and M. Granger Morgan of MIT Sloan Management Review (Spring 2017)
[6] “Defense Additive Manufacturing – DoD needs to systematically track department-wide 3D printing efforts” GAO report to Congressional Committees (Oct 2015)
The massive potential of AM in the aerospace industry is not something that I had considered before, but clearly, as explained above, has significant potential. Not only could it keep aircraft in operation at lower cost over longer periods of time (once spare parts replacement manufacturers have stopped producing those parts), but it also has the ability to keep aviators flying by giving them the tools they need to produce replace parts while in the field. While determining how AM could reduce variability in its printed products to meet the standards fo the FAA is certainly a challenge, the value of the potential benefits indicate to me that there will be plenty of people in the defense industry working to overcome these challenges, even for critical parts. In other words, with appropriate technology development–for which I believe there is immediacy to develop–I believe the FAA will, eventually, approve the use of AM to produce replacement parts.
I also knew nothing about how the military was leveraging additive manufacturing before reading this article; thanks for illuminating these exciting developments in a powerful industry! I agree that, as the military and the FAA obtain increased familiarity with the performance of 3D-printed materials in different situations, they will likely reach a compromise to enable faster incorporation of AM parts in the manufacturing process.
I am curious if, how, and at what point the application of additive manufacturing on existing planes will impact the timeline and/or the process of developing new generations of aircraft. Will the military decide to hold back on the huge expenditures needed to produce a new line of jets if existing planes could be easily maintained with 3d-printed parts? Even if 3D printing allows for extending the life of an aircraft, should there be a limit to how long the military can do so, given the importance of having state-of-the-art/unfamiliar technology?
It is very interesting to see how Additive Manufacturing can actually help overcome the spare part challenge for old jets. I can be very costly to keep stock of spare parts of an old plan without knowing precisely If those spare parts will ever be needed. Most of the time, some piece of equipment that could still have a useful life are replaced just because manufacturers are no longer producing the spare parts. I actually think that AM can change the economics of some industries such as aerospace for that reason: massive equipments such as trains or plans could be kept for longer time if maintained properly.
In addition, I also really liked how you highlighted the challenges that AM could address for the military on the field. When on a mission it is essentially impossible to carry all the specific spare parts and components that could potentially be needed during the mission. it is very exciting to see that AM reshapes the way planning could done for a mission: in the future, all engineers will need is a computer with the design of all the components and a 3D printer!