Flying High: GE’s Billion Dollar Bet on Additive Manufacturing
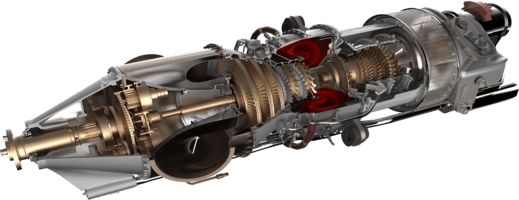
GE is investing heavily in additive manufacturing and has achieved early success in the aerospace industry. Will these early successes help to revolutionize conventional manufacturing?
A decade ago, engineers at GE Aviation made a breakthrough while designing a more fuel-efficient jet engine. The breakthrough was a new fuel injector nozzle that sprayed fuel into the engine’s combustor and allowed for better fuel and air mixing. The problem, however, was the geometric complexity of the nozzle’s interior. It was impossible to construct through traditional subtractive manufacturing, which required the welding and brazing of 20 parts into complex internal shapes. Rather than giving up on the idea, the engineers turned to additive manufacturing to solve their issue. Additive manufacturing, or 3D printing of parts from digital models, combined all 20 of the nozzle’s parts into a single unit. This process improvement not only made the construction feasible, it reduced the nozzle’s overall weight by 25% and improved its durability by five times. [1] The fuel injector nozzle, which was approved for flight by the Federal Aviation Administration in 2015, highlighted the ability of additive manufacturing to make complex parts economically. [2] Realizing its potential, GE quickly invested significant resources into additive manufacturing and began focusing on an even more ambitious project—the Advanced Turboprop engine (ATP).
Why is additive manufacturing important for GE’s ATP development?
What differentiates the ATP from the fuel injector nozzle is scale and complexity. The ATP, which will be used in the Cessna Denali single-engine turboprop aircraft, originally consisted of thousands of subtractive manufactured parts. Like the fuel injector nozzle, the engine has a complex geometric design which normally would use bolts and welds to fit each of the parts together. These joints are often the weakest points within a design. The revolutionary aspect of additive manufacturing is that it reduces the number of unique parts, thus limiting the number of joints. This fundamentally changes the creative design process for engineers. As Chris Schuppe, general manager of engineering for GE Additive, explains, “When we free an engineer’s mind from the constraints of how a part needs be designed so it can later be assembled, the engineer can activate the creative side of his or her brain to design parts that have never been built before.” [3] Within the ATP, GE engineers have reduced 855 subtractive parts into 12 additive parts. The additive parts account for 35% of the engine’s total architecture, reducing the weight by 5% and increasing specific fuel consumption, a measure of efficiency, by 1%. [4] In addition to the engine’s improved metrics, printing parts occurs more quickly than conventional assembly methods. In terms of the product development process, engineers can test hardware sooner and use the resultant test data for next iterations—additive manufacturing expedited initial testing for the ATP 6 months ahead of schedule. [5]
Next steps
GE believes the additive manufacturing market could grow to $76 billion within a decade. [6] In order to capture market share early, the company invested over 1 billion dollars in 2016 to launch GE Additive, a network of manufacturers up and down the additive supply chain. Leveraging the learnings and success of the fuel injector nozzle and ATP, GE Additive looks to move from producer of additive parts to the leading supplier of additive machines and materials over the next 10 years. [7]
Recommendations
While GE’s advances in additive manufacturing are exciting, the days of 3D printers on every corner to print parts just in time for customers is still far off. In fact, additive manufacturing only makes sense for highly complex and customizable products, like jet engines, and almost all currently manufactured products are standardized. [8] If GE wants to make additive manufacturing feasible for local manufacturers, they need to focus on the economics of the additive decision. This not only includes offering machines at comparable prices to traditional manufacturing equipment, but also involves making the technical training for the setup, operation, and troubleshooting of printers more affordable to reduce labor costs. In addition, expertise currently does not transfer easily from one type of printing process to another (for example, plastic to metal manufacturing), so GE should develop machines with convenient, multiple-use printing capabilities. [9]
Key Questions
- In the future, how can additive manufacturing be used most effectively in product development? Should it be limited to prototype development and the production of complex parts? Is it too expensive and technical to be used for mass production of commercial products?
- Is GE making a smart investment in additive manufacturing? In what industries and use cases should they be focusing their efforts?
(739 words)
Notes
[1], [7] Tomas Kelner, “An Epiphany of Disruption: GE Additive Chief Explains How 3D Printing Will Upend Manufacturing,” GE Reports, November 13, 2017, [https://www.ge.com/reports/epiphany-disruption-ge-additive-chief-explains-3d-printing-will-upend-manufacturing/], accessed November 2018.
[2] Alan Brown, “Chain reaction: Why additive manufacturing is about to transform the supply chain,” Mechanical Engineering 140(10) (2018): 33.
[3], [4] “General Electric Announces Launch of GE Additive,” Additive Manufacturing Today, 2016, [https://additivemanufacturingtoday.com/general-electric-announces-launch-of-ge-additive], accessed November 2018.
[5] “GE tests additive manufactured demonstrator engine for Advanced Turboprop,” GE Aviation, November 1, 2016, [https://www.geaviation.com/press-release/business-general-aviation/ge-tests-additive-manufactured-demonstrator-engine-advance-0], accessed November 2018.
[6] Sam Davies, “GE Additive sets out in its role in the growth of AM as an industry-standard production tool,” TCT Magazine, April 10, 2018, [https://www.tctmagazine.com/3d-printing-news/ge-additive-role-am-industry-standard-production/], accessed November 2018.
[8] Matthias Holweg, “The Limits of 3D Printing,” Harvard Business Review Digital Articles (June 23, 2015): 3-4.
[9] Jaime Bonnín-Roca et al, “Getting Past the Hype About 3-D Printing,” MIT Sloan Management Review 58(3) (Spring 2017): 58.
I find the $1B investment by GE very comforting when thinking about the future of additive manufacturing. Some of the biggest challenges preventing AM from becoming mainstream is the technological inefficiencies associated with the process. As we advance the processes, costs will reduce and impact will increase, but it will take manufacturing giants like GE with the available capital resources to fund these advancements in AM.
This was a really interesting article – in part because I hadn’t considered the design implications of additive manufacturing. In particular, I think it’s striking that GE was able to effectively eliminate the need for a high number of subtractive parts, while also reducing weight of the component and improving efficiency with additive manufacturing. In my mind, this highlights the value of AM.
I would question the notion that that GE should pursue development of “convenient, multiple-use printing capabilities” to assist with training implications of AM technology for two reasons. 1) I wonder how much printing processes differ for AM when switching between types of printing materials – in which case – is it even feasible to print plastics and metal or alloy based components on the same machine? 2) There are a number of other producers of competing additive manufacturing technologies. Differentiation in the type of machine, software and function will widely vary until there are higher levels of consolidation in this space. Will GE’s investment in this area truly function as a method of standardization or would the company be better served to simply train experts on AM tech based on type of material printed?
The example presented for GE presents as an innovative way that the company is able to gain a competitive edge in Aerospace Manufacturing. This technology also appears to enable designers to push the limits of what can be built as well as the timelines required to manufacture complex machinery. I think GE is making a smart investment when looking to expand its capabilities in additive manufacturing. One area that I think this type of manufacturing can be most value add is in the assembly and repair of remote large machinery such as wind turbines. This would potentially hasten the build times as well as reduce the down time required for the machines to be fixed.
I really liked the article Tom, and just like Saggitariutt, I also find it really encouraging that a giant such as GE is heavily invested in the technology. Like several other ground breaking innovations in our history, the capital required to make the technology work at scale is out of reach for many players. However, the fact that the economics of the technology are not viable for mass production now, certainly does not mean they won’t be in future. GE could be one of the organizations that is best suited to take on the challenge in terms of resources required and for that, I believe it could be a smart investment. When thinking about industries to expand into, I would think about those use cases in which customization is important and reducing the number of players on the supply chain as well as increasing the speed of production can generate savings high enough to balance the implementation costs.
Thank you for sharing your thoughts on the exciting topic of additive manufacturing. I would echo Tom Raider’s sentiments, that just because the unit economics don’t support mass production today, doesn’t mean it won’t be possible in the future. Though we’re not there yet, and it continues to suffer from limitations such as the thinness of the material it can support[1], we’ve already seen the technology advance and is now capable of making structures and of using materials that weren’t previously possible.
I think it’s absolutely critical that GE seeks to maintain its leadership in core markets. To do so, GE must be at the forefront of emerging disruptive technologies. For this reason, I think it’s a smart investment for them to be making. As GE continues to restructure and rationalize its portfolio, they should be thinking about their core market positions, assess the degree of disruption risk, and quantify the long-term franchise value of focusing R&D efforts in an area like this. The criteria I think they should use to prioritize their efforts and resources (which includes financial capital, R&D energies, and talent) should be areas for which 3D printing is the strongest: where the innovation cycle is fast, and where rapid prototyping can be a source of competitive advantage. Within their current portfolio, I’d imagine some of their healthcare device and imaging assets could prove fruitful. Along those same lines, GE should also target areas where the bill of materials is high and competitive intensity is driving pricing and margin pressures. Or, connecting back to today’s TOM class, areas where complicated and dispersed supply chains become problematic.
Overall, I believe additive manufacturing holds great promise. The one caution I’d call out is that GE should be disciplined, since first movers in emerging technologies don’t necessarily prevail in the long-term, depending on the barriers to entry / ease of replication.
[1] Bonnín-Roca, J., Vaishnav, P., Mendonça, J., & Morgan, G. (2017). Getting past the hype about 3-D printing. MIT Sloan Management Review, 58(3), 57-62. Retrieved from http://search.proquest.com.ezp-prod1.hul.harvard.edu/docview/1885885282?accountid=11311.
This article is relevant for two seemingly opposite reasons, brought together in this example: additive manufacturing is one of the most innovative developments in industry today — and GE is one of the old guard that seems unable to keep up. I’d be curious, like the author, to see where additive manufacturing makes sense and where it doesn’t. On one hand, I’m inclined to agree it makes most sense in production of complex items that would otherwise require too many disparate parts. That said, one thing we learned early on in TOM was that parallel assembly lines can be created to save time when a product is modular — say, a blender that can be built in different parts simultaneously and then brought together at the end. The interesting thing about 3D printing is that in some ways it seems organizationally less advanced (even if technologically more advanced) — like a job shop building a custom baseball bat where the same piece of wood needs cut, shaped, stained, imprinted, etc. all sequentially without being able to do any of those steps at the same time.
Wow – great topic! You raise a good point with regards to expertise being limited to materials used in the printing process. I would be curious to see how GE intends to scale and train its workforce to adapt to technology that would enable mixed materials in the printing process, e.g., metal and plastic. So many of the business units that live under the wider GE umbrella could benefit substantially from mixed materials technology, in addition to the knowledge base to power this technology.
Excerpt from the New York TOMs review:
Mr. Riddle presents an enlightening and well-researched summary of additive manufacturing’s contributions to GE in the context of the Advanced Turboprop engine. Especially interesting is the article’s case that 3D printing represents a change not only in quantity (the type and cost of materials) but in quality, freeing engineers to think of better designs that would not have been possible with normal manufacturing constraints on assembly. Although the article would ideally have followed through on the impact of reduced material consumption on total cost, it offers an excellent breakdown of the scale of the change in total architecture, weight, and specific fuel consumption.
The article’s recommendations note that 3D printing currently makes the most sense for highly customizable projects, and recommends future investments in unit economics to make mass production more effective. This analysis is spot-on, although a deeper look at the fixed and variable cost breakdown at present, and the advancements needed to make mass manufacturing cost-effective, would have further enhanced Mr. Riddle’s case.