Fighting Organizational Inertia in Aerospace
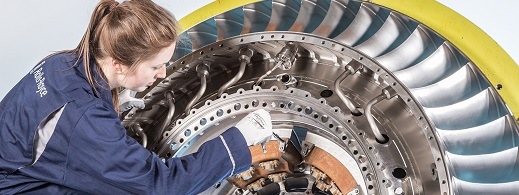
Additive manufacturing threatens to fundamentally disrupt the way parts are designed in the aerospace industry – can an established player like Rolls-Royce display enough agility to stay ahead in the market and capitalize on this new technology?
Why is additive manufacturing important to Rolls-Royce?
Additive manufacturing promises to revolutionize manufacturing and supply chain, from hyperlocal parts manufacturing to infinite customization of components [1]. However, such revolutionary technology poses great challenges for established companies such as Rolls-Royce (a supplier of aircraft turbine engines) who stand to be disrupted the most. However, before a single component can be “3D printed”, the first step is to create a digital model of the printed object [2]. Creating digital designs is one of the core competencies of a modern engineering firm and must be adapted to additive manufacturing before such technologies can be deployed more widely. Rolls-Royce has been making gas turbines for 75 years [3], and those decades of learning and best practices are embedded in internal company documents and employees’ knowledge. It is a huge challenge to shift the core competency of the company from designing parts for traditional manufacturing to designing parts that utilize the advantages of additive manufacturing, while avoiding its weaknesses.
Designers must account for the fact that 3D printed parts behave differently in the field than their traditional counterparts: their strength and deflection is nonuniform depending on the direction of load application and they can be more prone to premature failure due to repeated loads [4]. To make the most of additive manufacturing, engineers in product development primarily need two new skills. First, analysts must learn how to model the material’s behavior in the real world with computer simulation programs that typically model uniform material behavior. Secondly, engineers need to learn to develop and deploy novel design features that might have been impossible to produce using traditional methods.
What is Rolls-Royce doing about it?
In the short term, Rolls-Royce has been addressing these issues via strategic partnerships and acquisitions. For example, Rolls-Royce is a member of the Commonwealth Center for Advanced Manufacturing (CCAM), a non-profit corporation composed of members from industry, academia, and government with the goal of creating solutions to complex advanced manufacturing challenges [5]. CCAM provides to Rolls-Royce expertise in characterization (i.e. quantifying the nonuniformity of properties) and simulation (i.e. predicting behavior in the real world) of materials used for additive manufacturing [6]. These are two of the key proficiencies that will be essential is Rolls-Royce is to harness the full impact of 3D printing in their product development processes.
In the medium to long term, Rolls-Royce is partnering with other external partners such as JetX and 3D Hubs to educate the next generation of engineers on the intricacies of additive manufacturing [7]. JetX is a team of aerospace engineering students working Rolls-Royce to develop a scale model of a gas turbine using only 3D printed parts, using the experience to gain direct experience in design for assembly and simulation analysis. Such skills will allow engineer to see opportunities to reduce engine complexity via combining multiple parts into one [8], thus leveraging the capabilities of additive manufacturing and yielding engines with fundamentally different architectures compared to their traditionally manufactured counterparts. This is a ground-up, long term approach to changing the product development process – bring in new talent from universities that isn’t bound by conventional wisdom.
What further actions should Rolls-Royce be taking?
Rolls-Royce needs to work more quickly to disseminate knowledge and capabilities throughout the company, and it also needs to leverage its large legacy fleet as a test bed for experimentation. Additive manufacturing is typically viewed as a cutting-edge technology, used on the latest and greatest new engines, but this is troubling when viewed through the lens of Rolls-Royce’s product portfolio. Almost 50% of their revenue [9] comes from aftermarket support of an aging fleet, with a commensurate portion of engineering staff dedicated to supporting these aging platforms. Such staff have little opportunity for exposure to additive manufacturing, but it is an appealing deployment location for the technology within the company. Additive manufacturing offers to reduce lead times and inventory carrying costs for old, uncommonly needed components [8], while the mature engines of legacy fleets are perfect low-risk test beds for replacement parts made with additive manufacturing. Such a strategy could reduce the long tail of the supply chain for legacy products while also raising overall engineering capability to design parts for additive manufacturing.
Open questions
As additive manufacturing presents the first step change in manufacturing since the advent of computer numerical control (CNC) machining, it brings up key questions for how Rolls-Royce and the wider industry will adapt their product development operations. What techniques can managers at Rolls-Royce use to combat the inertia of 75 years of ingrained habits to extract the most creativity and innovation out of their human resources? How do they balance the need to change and adapt against the safety demands of a highly regulated industry?
(788 words)
[1] D’Aveni, Richard A. “3-D Printing Will Change the World.” Harvard Business Review, vol. 91, no. 3, Mar. 2013, p. 34. EBSCOhost, ezp-prod1.hul.harvard.edu/login?url=http://search.ebscohost.com/
login.aspx?direct=true&db=bth&AN=85463174&site=ehost-live&scope=site, accessed November 2018.
[2] Tofail, Syed AM, et al. “Additive manufacturing: Scientific and technological challenges, market uptake and opportunities.” Materials today (2017), accessed November 2018.
[3] Rolls-Royce, plc. “Our History,” https://www.rolls-royce.com/about/our-history.aspx, accessed November 2018.
[4] Frazier, W.E. “Metal Additive Manufacturing: A Review.” J. of Materi Eng and Perform (2014) 23: 1917. https://doi.org/10.1007/s11665-014-0958-z, accessed November 2018.
[5] Commonwealth Center for Advanced Manufacturing. “About.” http://wp2.ccam-va.com/about-ccam/, accessed November 2018.
[6] Commonwealth Center for Advanced Manufacturing. “Research: Additive Manufacturing.” http://wp2.ccam-va.com/additive-manufacturing/, accessed November 2018.
[7] 3D Hubs Blog. “Rolls Royce is working with this student team to create a functional 3D printed jet engine model.” https://www.3dhubs.com/blog/fully-functional-3d-printed-jet-engine-built-by-students-to-create-next-level-in-aerospace/, accessed November 2018.
[8] BROWN, ALAN S. “Chain Reaction: Why Additive Manufacturing Is about to Transform the Supply Chain.” Mechanical Engineering, vol. 140, no. 10, Oct. 2018, pp. 30–35. EBSCOhost, ezp-prod1.hul.harvard.edu/login?url=http://search.ebscohost.com/login.aspx?direct=true&db=bth&AN=132029167&site=ehost-live&scope=site, accessed November 2018.
[9] Rolls-Royce Holdings plc. “Annual Report 2017: Financial Statements.” https://www.rolls-royce.com/~/media/Files/R/Rolls-Royce/documents/annual-report/2017/ar2017-financial-statements.pdf, accessed November 2018.
It is interesting to see how a large, established company like Rolls Royce grapple with the technology of additive manufacturing (AM). I think this article shows that it is hard for large companies to change, especially given that Rolls Royce’s cash cow is their legacy product line. You raise a good point that Rolls should use AM more in their core business, but I do realize that changing technologies require a ton of cost and complexity. I think Rolls Royce needs to send its engineers out to conferences and universities to interact with new technologies and ideas as a way to get out of the Rolls bubble. Changing a culture can be quite difficult but can be done with the right incentives.
I think your identification of the JetX partnership as key to Rolls Royce’s efforts to build momentum here hits the nail on its head.
3D printing is a fast evolving technology, with the flaws of each iteration immediately obvious to its users. Especially in aerospace, engineers can quickly become risk-averse due to the high amounts of safety required in their products.
By involving fresh eyes as much as possible, I think the pace of innovation can be accelerated and new solution approaches can be found.
Great article! I enjoyed how this article forced you to take a step back and evaluate how even though additive manufacturing may be the correct move for the company, there are deeply embedded cultural and skill constraints that need to be overcome before Rolls Royce can be effective in using the technology.
To your first question on what they need to do: while sometimes difficult to swallow, the reality is, and we see this in both their long and short term plans, current employees may not be able to learn the new tricks, so, to learn and adapt, new talent must be employed and old talent let go.
That being said, you raise a very interesting point on how then do they retain their culture in this changing environment. Moving forward will definitely be a balancing act for them, but one that involves risks that seem worth taking.
This was a great example of additive manufacturing being used to inspire a ground-up re-design effort, as opposed to substitution-focused applications! Rolls Royce seems to have a comprehensive plan to position itself for capturing the additive manufacturing opportunity. While you make a nuanced point about how Rolls Royce should leverage this opportunity in light of the legacy fleet factor, I am not clear how additive manufacturing could be used in this scenario. Given your insights into how additively-manufacturing parts show different properties and behaviour compared to conventionally-manufactured parts, I am curious about the feasibility of incorporating such components into existing legacy engines. How do you look at the impact of adding such components on a piecemeal basis and integrating them into a legacy aircraft engine? How would Rolls Royce assure safety and performance in such mixed systems, and convince its airline customers to take on this risk in a heavily regulated industry that has high costs associated with system failure?
Really interesting article!
On your question related to which techniques can managers at Rolls-Royce use to combat the inertia of 75 years of ingrained habits to extract the most creativity out of their human resources, I would recommend to:
* Communicate the importance of additive manufacturing at the organizational level and the intentions of the company to actively migrate towards a full additive manufacturing enterprise in “x” years. Employees must understand the “why” and the “how” of that decision in order to even consider modifying their behaviors
* Incentivize change at the lower ranks. By creating opportunities within the organization and providing the tools to deliver (e.g. online courses on simulation of 3D pieces), the most supportive employees will feel empowered and push others toward the strategic goal
* Renovate talent. I agree with TheHen that, ultimately, new talent must be employed and old talent let go