Digitalization Drives “Dieselgate”
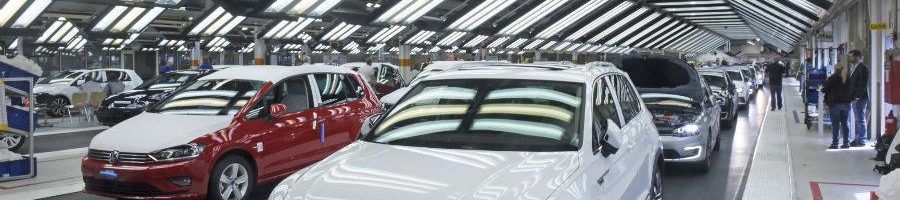
Volkswagen AG’s integrated supply chain stalls its push to become the world’s top automaker.
Running on Fumes
Firing on all cylinders in 2006, Volkswagen’s executive leadership pivoted the company’s mission to become the world’s largest car company by 2018. Motivated by low market share in the United States its’ strategy hinged on increasing the competitiveness of their fuel efficient alternatives – the EA 189 diesel engine was launched (1).
Despite being marketed as a clean diesel alternative, the management team soon learned that the EA 189 failed to meet the strict levels of nitrogen oxide emission required in the United States (2). The management team leveraged the digital software within both the supply chain and the product itself to design a response to “test-like” conditions. Engineers programmed the emissions system of the cars to output a significant power degradation and decrease in emissions when the car’s monitoring system detected a test scenario (2). On September 18, 2015 the EPA announced that at least 450,000 vehicles had these devices installed (3).
The Volkswagen scandal resulted in an expansive ripple effect to both upstream and downstream components of the supply chain. On the day the alleged “dieselgate” announcement broke, Volkswagen stock dipped 40% and a shockwave was sent across suppliers (4).

Today, data analytics, just-in-time inventory procedures, and increased part tracking create a matrix of closely linked entities that continued to operate on slimmer margins – reducing the value derived from each portion of the production process. These advancements, coupled with sustainability efforts, significantly amplified the risks associated with supply chain management. In the case of the EA 189 engine, Volkswagen knew that changes to its design and halting the supply chain would cost millions of dollars despite the increased optimization that connected products created (5,6). In effect, the interconnectedness of the software driven supply chain that enabled management to mask the emissions issue rather than addressing it.
Refueling – After the crisis
Digitalization initiatives across the automotive industry have increased information technology spending by roughly $37.9 billion as of 2015 and it will continue to grow industry-wide to nearly $168.8 billion by 2025. This increased spending will result in large part from as many as 1700 new digital startups that will significantly alter manufacturer practices during the production design and build phases (7). As of April 2017 Volkswagen’s rebuilt supplier network, post “dieselgate”, now includes approximately 40,000 partners and a new business platform, “ONE” that can efficiently redirect products at each stage of production (8).
The Volkswagen management team admitted to additional installations of the so-called “defeat devices” throughout 2016 and 2017. While the investigation is still ongoing in many areas, the initial penalties included a $2.7 billion for environmental program funding, $2 billion for research on alternatively fueled vehicles and $10 billion for a vehicle buy-back or reconfiguration program. Additionally, Volkswagen has submitted a proposal to the California Air Resources Board that details an $800m plan to build hundreds of EV charging stations in the next ten years (9). The plan is part of the larger initiative to combat the nitrogen oxide gases that were produced at 25 times the allowable amount while the cars were in use. This first wave of projects in 2017 will attempt to rebuild the brand started with $200m in outlays over the next 30 months (10).
Picking You Up Off the Assembly Line
The management team released a plan in November 2017 to partner with Google’s Quantum Computing program to drive the future of their business (11). The plan outlines autonomous vehicles, mapping technology, and massive data collection efforts to illuminate the curves on the road to the future. The plan also prioritizes incorporating quantum computing technology into their supply chain. A recent look at OEMs and the future of mobility confirms Volkswagen’s competitiveness in implementing a transparent and agile supply chain (12).

Today’s economy demands digitally interconnected production processes that help manufactures react more directly to the point of sale. Increased digital networks and clarity of the consumer’s demand will dampen the ramifications of the bullwhip effect. Communication through the internet of things and instant feedback processes have increased machine utilization and capacity while decreasing rework and lead time. In just the past 27 years, factories have gone from 25% automated to over 75% (13). At scale these components will continue to drive costs down, increase understanding of the consumer, and implement improvements faster. Volkswagen AG’s commitment to optimizing the use of these features will prevent future breaches of their integrity and lead to long term sustainability efforts across all project lifecycles.
Will the automotive industry continue to focus on reducing the bullwhip effect across suppliers and distributers with other digitalization advancements (i.e. 3-D printing)? Could any of these advances catalyze a shift to vertical integration and would integration affect a manufacturer’s profitability or ability to innovate? (15) (790 words)
References
- Jack Ewing, “ Engineering A Deception: What led to Volkswagen’s Diesel Scandal,” New York Times, March 16, 2017.
- Fracarolli Nunes, M. & Lee Park, C. 2016, “Caught red-handed: the cost of the Volkswagen Dieselgate”, Journal of Global Responsibility, vol. 7, no. 2, pp. 288-302.
- Reitze, Arnold W., The Volkswagen Air Pollution Emissions Litigation (July 1, 2016). Environmental Law Reporter, Vol. 46, 2016; University of Utah College of Law Research Paper No. 174.
- Chloe Whiteaker and Jennifer Price, “The VW Effect,” Bloomberg, October 19, 2015.
- Schlüter, Florian & Diedrich, Katharina & Güller, Mustafa. (2017). Analyzing the Impact of Digitalization on Supply Chain Risk Management.
- Porter, M. and J. Heppelmann, “How smart, connected products are transforming competition,” Harvard Business Review, (Nov. 2014).
- “Digital Transformation of the Automotive Industry – Digitalization Spending to Grow Rapidly to $82.01 Billion in 2020,” PR Newswire , April, 4 2017.
- Roberts, G. 2017, Volkswagen Group expands digital supply chain, Bromsgrove.
- “Volkswagen to recall 83,000 Vehicles & Fund Mitigation Projects,” U.S. Department of Justice Documents, December 20, 2016
- David Shepardson, “Automakers Want California to Revise Volkswagen Charging Station Plan,” Reuters, April 26, 2017.
- Christoph Rauwald, “Volkswagen, Google Cooperate on Quantum Computing in Tech Push,” Bloomberg News, November 7, 2017.
- Kompalla, A., Geldmacher, W., Just, V. & Lange, S. 2017, “Tailored Automotive Business Strategies in the Context of Digitalization and Service-Oriented Models”, Calitatea, vol. 18, no. 156, pp. 77-84.
- Daniel Newman, “Top 6 Digital Transformation Trends in the Automotive Industry,” Forbes, July 25, 2017.
- Bloomberg LP, accessed November 2017.
- Manenti, P 2017, ‘How to Approach the Digital Supply Chain Future: Digitalization is a business strategy, not just a technology implementation’, Material Handling & Logistics, 72, 4, pp. 30-31, Business Source Complete, EBSCOhost, viewed 9 November 2017.
I am not sure that digitization drove Dieselgate. The incident seems more an issue of corporate malfeasance than one of digitization-induced change.
I do agree, though, that digitization opens new areas of vulnerability for global supply chains. Industries where transactions happen through a marketplace (e.g., commodities), where buyers never meet physical sellers, are most at risk. However, I am unsure of how corporations can avoid this risk. The benefits of digitization seem to still outweigh the potential costs.
I don’t believe digitalization can further reduce the bullwhip effect in a significant way. As opposed to distribution models for other goods, the one for vehicles is actually quite short (few players). From prior work experience, I can say that a typical organization structure (at least in Latin America) consists of distributors (owning the dealerships), then country wide importers, and finally the production plants. The communication is constant between the parties and there is clear visibility of end demand. What sometimes causes the bullwhip effect is over or underestimation of future demand, which I don’t think could be solved with digitalization.
I did find very interesting the other implications explored by this article of this mega-trend on the industry.