Building the Future at GE, One Layer at a Time
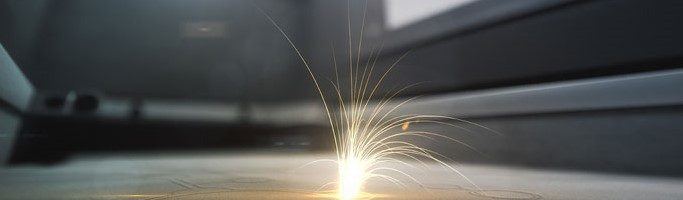
Additive manufacturing will transform the way industrial companies design, develop, and support their products. How is GE layering up its defenses to compete in this new world?
Speaking Volumes
This summer, the oldest founding member of the Dow Jones Industrial Average, GE, made very modern waves when it announced it would be creating the world’s largest 3-D printer [1][2]. ‘ATLAS’, will be a laser based powder metal printer with a build volume of 1.0 m3[2]. To put that in perspective, the current record holder, Concept Laser’s XLine 2000R, has a build volume that is 6.25x smaller at 0.16 m3[2]. A machine of this size opens the door for GE to produce even higher value components for its aviation business and cements the company as a leading player in additive manufacturing [5]. Additive manufacturing (equivalently referred to as 3-D printing), is a collection of technologies and methods that are capable of building components by depositing layers of material and melting or adhering them together [3]. This contrasts with traditional, subtractive, methods which achieve desired geometries by removing material.

As a company, GE has made additive a core component of its industrial strategy stating that it believes it will usher in a transformative age of expanded product design capability, flexibility, and speed, as well as improve service delivery and asset management[4]. Indeed, President and CEO of GE Aviation David Joyce recently stated “Additive changes…the paradigm between the cost of manufacturing and the complexity of design. Design is going to optimize for performance and productivity with new and better cost entitlements and faster cycles.”[4] This strategy comes as no surprise, as industry analysts have been extolling benefits such as low/zero inventory costs, increased profitability within low-volume/high-value products, hyper customization, reduced product life-cycles, and lack of re-tooling costs since 2012[6][12].
If You Print It, They Will Come
In a prime example of putting your money where your mouth is, GE acquired competitors Concept Laser (German) and Arcam AB (Swedish) to jump-start its industrial printer capability [5]. These acquisitions, which led to the rapid development of ATLAS, will allow the company to build large jet engine and aircraft structural components not previously possible before.[5] GE will also be testing a new version of its ATP turboprop engine which will have 1/3 of its components 3-D printed, reducing 855 parts down to 12, lowering weight and thus fuel consumption why a whopping 20% and lasting 1000 hours more between overhauls[6][7].

GE’s longer terms goals are certainly much greater than just fuel nozzles and jet engines. Now ex-CEO Jeff Immelt believes that the total additive market resides around $75 Billion and fairly new GE Additive business will reach $1 Billion by 2020[8]. The Arcam and Concept laser acquisitions really serve to stabilize their industrial base so they can pursue opportunities in healthcare, automotive, oil & gas, and power. GE Additive also recently opened the Additive Training Center(ATC) near Cincinnati (along with a similar facility near Pittsburgh). A 130,000 ft2 facility that holds 30 metal 3-D printing machines and hosts 3-D printing “boot-camps” where engineers from all parts of the business can come and learn how to design for additive manufacturing [8][9]. The long-term goal of this facility is to shift the design culture within GE’s business to better take advantage of the new technology.
Layering Up the Challenges
One aspect of the additives space that GE is not targeting however is the spare parts market. Now a $400 Billion business, the aviation spare parts business is bereft with inefficiencies and opportunity that would benefit from 3-D Printing[10]. Currently, almost 10% of the spare parts stock of most MROs is considered obsolete or sunk and the industry is notorious for long lead times[11]. Today, 30% of airlines and MROs have said they are looking to 3-D print their spare parts and in 10 years German parts suppliers will be spending $3 Billion in printing their inventory [11]. GE’s current strategy keeps the company is its place as an OEM (traditionally a low margin game, ~10%) and fails to map its entrance in the spares parts business (traditionally a high margin game, 20%-25%)[12]. GE must also not allow culture and design heritage to get in the way of its progress. While the ATC is a necessary step forward, it might not do enough to cement the change necessary for its engineering communities to stray from decades of design history.

Questions:
As the company extrudes itself forward into the future, what strategy should it use in entering and disrupting the spare parts industry? Does it make sense for GE to do so?
As its engineers shift a new layer of culture and design philosophy over decades of hardened (and outdated) standards, how should GE approach workforce retraining to maximize the potential of 3-D printing? Is the ATC enough on its own? Should GE increase its 3-D printing training opportunities?
(Word Count: 782)
References
[1]Forbes.com. (2017). Forbes Welcome. [online] Available at: https://www.forbes.com/2011/05/26/dow-at-115-longest-tenured-stocks_slide/#5ddd8a124e14 [Accessed 13 Nov. 2017].
[2]Clarke, C. (2017). GE announces development of ATLAS world’s largest powder bed metal 3D printer. [online] 3dprintingindustry.com. Available at: https://3dprintingindustry.com/news/ge-atlas-metal-3d-printer-announces-development-of-worlds-largest-powder-bed-3d-printing-116490/ [Accessed 13 Nov. 2017].
[3]DU Press. (2017). The 3D opportunity primer. [online] Available at: https://dupress.deloitte.com/dup-us-en/focus/3d-opportunity/the-3d-opportunity-primer-the-basics-of-additive-manufacturing.html [Accessed 13 Nov. 2017].
[4]Mohammad Ehteshami – VP, Additive Integration, GE Additive, GE Company (General Electric Co.) 2016, , Boardroom Insiders, Inc, San Francisco.
[5]Kellner, T. (2017). How GE Is Growing 3D Printing Operations in Germany – GE Reports. [online] GE Reports. Available at: https://www.ge.com/reports/heirs-gutenberg-ge-adding-next-chapter-3d-printing-push-germany/ [Accessed 13 Nov. 2017].
[6]Jackson, B. (2017). A closer look at GE’s 3D printed ATP aircraft engine. [online] 3dprintingindustry.com. Available at: https://3dprintingindustry.com/news/closer-look-ges-3d-printed-atp-aircraft-engine-119268/ [Accessed 13 Nov. 2017].
[7] “Mad Props: A 3D-Printed Airplane Engine Will Run This Year,” General Electric press release (2017) (https://www.ge.com/reports/mad-props-3d-printed-airplane-engine-will-run-year/)
[8]Kellner, T. (2017). How 3D Printing Will Change Manufacturing – GE Reports. [online] GE Reports. Available at: https://www.ge.com/reports/epiphany-disruption-ge-additive-chief-explains-3d-printing-will-upend-manufacturing/ [Accessed 13 Nov. 2017].
[9]Additivemanufacturing.media. (2017). GE Opens Additive Manufacturing Center in Pittsburgh. [online] Available at: https://www.additivemanufacturing.media/news/-ge-opens-additive-manufacturing-center-in-pittsburgh [Accessed 13 Nov. 2017].
[10]Wyman, O. (2017). 3D Printing Is Already Starting To Threaten The Traditional Spare Parts Supply Chain. [online] Oliverwyman.com. Available at: http://www.oliverwyman.com/our-expertise/insights/2017/aug/3d-printing-is-already-starting-to-threaten-the-traditional-spare-parts-supply-chain.html [Accessed 13 Nov. 2017].
[11]Geissbauer, Wunderlin, Lehr, (2017). The Future of spare parts is 3D: A look at the challenges and opportunities of 3D printing. [online] Available at: https://www.strategyand.pwc.com/reports/future-spare-parts-3d [Accessed 13 Nov. 2017].
[12]Financial Times. (2017). Lucrative aircraft maintenance market scrutinised. [online] Available at: https://www.ft.com/content/a5c89a0a-719e-11e5-ad6d-f4ed76f0900a [Accessed 13 Nov. 2017].
[12]Berman, B. 2012, “3-D printing: The new industrial revolution”, Business horizons, vol. 55, no. 2, pp. 155.
When you asked does it make sense for GE to do it, my only thought was what would be the reason for GE to not do it? They have predominantly not entered into spare parts manufacturing because their core competency is manufacturing and not last-mile distribution, which is exactly what additive manufacturing takes off the table. For example, An aircraft might break down in Houston and the spare parts manufacturing centre would be in Boston. This is extremely expensive because:
– the spare part was increasing inventory cost sitting in Boston
– the transit time to send the part means the flight is parked in Houston for days increasing parking charges and causing loss of revenue since it can’t fly
– Add the costs further of the ripples this one missing link sends across the entire network of flight schedule management
With additive manufacturing, the spare part is just lying as a “design inventory” and can be shipped to the closest 3D printing unit of the site of breakdown.
Long story short, one of the key components of the strategy should be to identify locations in the market which have a higher rate of breakdown and are furthest away from existing manufacturing locations.
Fascinating piece, thank you.
Financially, the spare parts business certainly appears to be an attractive, high-margin opportunity. It also aligns well with the promise of additive manufacturing: faster production cycles and lower inventory costs. In capital-intensive industries such as airlines, I would imagine spare parts inventories represent a significant investment – one that 3-D printed parts could hopefully reduce.
However, for GE, I wonder if there is an inherent tension between additive manufacturing capabilities and the need for spare parts. If additive manufacturing reduces the number of parts in an engine from 855 down to 12, as in the ATP Turboprop referenced above, will the spare parts market still be profitable in a few years? Put another way, if GE uses additive manufacturing to reduce the number of parts in an engine, will they need to produce spare parts at all?