BHP Billiton: Mining data to mine more efficiently
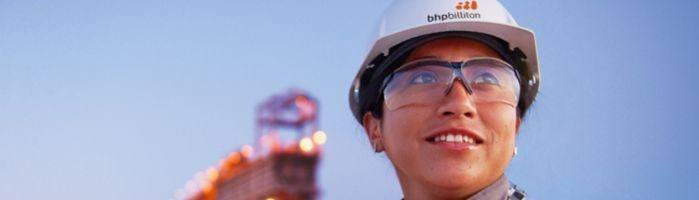
BHP Billiton is taking steps to use new technologies to improve its safety, production and cost performance.
BHP Billiton is one of the world’s largest mining companies, with revenues of AU$61B in 2015 [1]. The Australian based diversified mining company operates across commodities groups such as iron ore, coal, nickel and copper. The majority of operations are in the Australia and the United States with a total employee based of approximately 65,000 [2].
BHP Business Model
BHP’s business model is relatively simple. It can be roughly divided into four stages [3]:
- Finding a deposit: This involves finding a suitable location to mine and conducting feasibility studies.
- Establishing a mine: This is the process of regulatory approvals and establishment of the infrastructure required for the mine to operate.
- Mining: This is the process of extracting the commodity from the ground. This is typically done using heavy hauling machinery known as shovels, excavators and trucks.
- Purification: This process involves stripping the desired materials from the impurities such as rock and clay.
As with many companies, the rapid developments in technology are having an impact on all four stages of BHP Billiton’s business model. The following are three important examples of this, built around the companies’ strategic pillars of safety, volume and cost.
Improving Safety
Given the heavy machinery and high risk environments associated with mining, BHP Billiton has a focus on safety above all else. However, even the most robust safety protocols sometimes fail and the most reliable way to keep people safe is to remove them from the mine entirely. In recent years, sensors, GPS and other key technology has allowed mines to begin this process by rolling out autonomous vehicle technology. BHP Billiton has been trialing driverless trucks since 2013 and has gradually been expanding their use [4]. The company hopes that this will help to avoid tragic incidences such as the death of truck driver when the vehicle rolled in 2008 [5]. BHP is currently trialing the technology mainly in Western Australia, a region where mines are typically thousands of kilometers from the nearest cities. In addition to the safety benefits of operating the trucks from a control center in downtown Perth, moving an estimated 340 employees closer to their families and other amenities has a significant impact on employee morale. However, this is still just a very small proportion of the total employees at BHP and increasing the number and type of vehicles controlled remotely is an obvious next step.
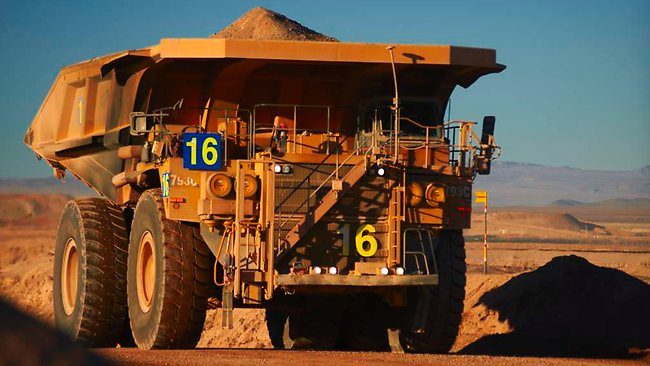
Increasing production
Digital transformation is also creating opportunities for BHP to increase production from assets with minimal additional investment. A key example of this is the use of predictive maintenance, where a vast sets of data from various connected sensors can be used to predict machinery faults before they happen [6]. In one particular example relating to offshore compressors on oil platforms, the company developed algorithms based on previous compressor failures to look for signs of an impending issue. This data was sourced from thousands of sensors located in the compressors and this project meant they were better able to predict when equipment is likely to fail. As a result, that compressors could be replaced or repaired during planned shutdowns, saving up to $20M in lost revenue each time an incident is avoided. The challenge for BHP in rolling this out more broadly is that determine which sensors are relevant for avoiding unplanned downtime is a complex and time consuming process, which is limiting the pace at which they can expand this.
Reducing cost
Another example of how technology is impacting BHP’s operations is in the way it mobile devices and applications are allowing real time access to relevant information for all employees. This allows BHP employees to access information such as how to repair a damaged piece of equipment or complete relevant paperwork while they are out of the office or away from their computer. This in turn will have a significant impact on productivity as people are able to access information more quickly, meaning reduced labor costs. BHP considers the magnitude of the opportunity to be so significant that is has recently invested in a mobile application development hub in Shanghai, where 50 application designers will work on various digital tools for the company [7].
In summary, there are enormous opportunities for technology to reshape the mining industry in the future. While fundamentally the mining business model may seem relatively simple, examples like those described above can give BHP an edge over its competitors. However, the company will need to increase the pace at which it rolls these technologies out if it is to maintain its cost advantage in the future.
(762 Words)
[1] BHP Billiton, “BHP BILLITON RESULTS FOR THE YEAR ENDED 30 JUNE 2016,” 2016. [Online]. Available: http://www.bhpbilliton.com/~/media/bhp/documents/investors/news/2016/160816_bhpbillitonresultsyearended30june2016.pdf?la=en. [Accessed Nov 2016].
[2] BHP Billiton, “About us,” [Online]. Available: http://www.bhpbilliton.com/aboutus/ourcompany. [Accessed Nov 2016].
[3] MIT, “Mining – Is current mining yield sustainable?,” [Online]. Available: http://web.mit.edu/12.000/www/m2016/finalwebsite/solutions/mining.html. [Accessed Nov 2016].
[4] A. Topf, “Two Aussie mines start moving all their iron ore with driverless trucks,” Mining.com, October 2015. [Online]. Available: http://www.mining.com/two-aussie-mines-start-moving-all-their-iron-ore-with-driverless-trucks/. [Accessed November 2016].
[5] C. Thompson, “BHP suspends operations after second death,” WA Today, 5 Sept 2008. [Online]. Available: http://www.watoday.com.au/wa-news/bhp-operations-suspended-after-second-mine-death-20080904-4a4k.html. [Accessed Nov 2016].
[6] LNT Infotech, “Industrial IoT Helps Prevent Costly Unplanned,” 12 Nov 2015. [Online]. Available: https://www.lntinfotech.com/Style%20Library/ARCview-LTInfotech-BHPBilliton-CaseStory-Nov2015.pdf. [Accessed Nov 2016].
[7] International Mining, “BHP Billiton opens mobile applications hub in Shanghai,” 10 Aug 2016. [Online]. Available: http://im-mining.com/2016/08/10/bhp-billiton-opens-mobile-applications-hub-in-shanghai/.
“While fundamentally the mining business model may seem relatively simple…”
Thank you for this thoughtful post, COG. Regarding the quotation above, I simply want to argue how complicated the minding industry is, not because of the business model, but because of the execution risks. Chevron exited the mining game in 2011 after recognizing just how difficult it is to eliminate or mitigate the risk associated with extracting minerals (http://www.forbes.com/sites/greatspeculations/2011/03/08/chevron-picks-a-fine-time-to-leave-the-coal-mining-biz/#3f57b0a85e14). I wonder if increased automation and standardization will ever reduce the risk associated with labor intensive efforts such as mining and manufacturing…