Chasing Glory: How Ferrari S.p.A. is embracing Additive Manufacturing to Win Again
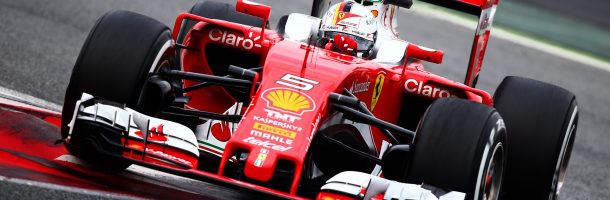
Tired of finishing second to its racing arch-nemesis, Mercedes, Scuderia Ferrari S.p.A is leading Ferrari's charge into the future by teaming with Renishaw, a British engineering firm that specializes in additive manufacturing (AM). Ferrari is looking to ride the wave of the future back onto the podium's top spot and carry their storied heritage into the 21st century.
Scuderia Ferrari, S.p.A
Why buy a Ferrari when you can just print your own? While we maybe some time off from such a possibility – and to say nothing of proprietary rights – this notion has been causing quite the buzz in the industrial manufacturing world. After languishing for a few decades after its inception in the 1980s, additive manufacturing (AM), also known as three-dimensional (3D) printing is finally starting to assert itself across a broad spectrum of industries, including the automotive industry. So great is the potential that experts are labeling the rise of AM as the ‘third industrial revolution’. [1]
Additive Manufacturing utilizes a layered fabrication process by which additional layers of a product are laid on top of the previously made layer, in contrast to subtractive manufacturing in which a part is cut from or forged from a solid block of material. [2] This leads to clear differences in waste, and therefore cost. Additionally, computer aided design (CAD) software has optimized the construction of customizable components, many of which are also exceedingly complex and unable to be constructed via traditional means. [3] In the wider automotive industry, advantages conferred by AM have resulted in lighter engine brackets and reduced complexity, leading to benefits such as increased fuel efficiency. [4]
Steeped in history and racing pedigree, Ferrari is keen to reap the benefits of AM. AM will grant Ferrari the ability to engage in more complex designs, ones which can reduce the weight of their cars, improve safety, simplify overall designs by combining part production into one step, reduce waste and its associated costs. Despite its legendary racing heritage, Ferrari – in its racing department, known as Scuderia Ferrari – has been struggling in the post-Schumacher era, with ‘the Prancing Horse’ failing to win a team championship since 2007.
Formula One Racing is a sport where every millisecond counts, every ounce of weight counts, and the performance of all the materials in the racecar counts…perhaps more than the driver in the cockpit. Due to the numerous regulations, safety needs, and stringent focus on performance margins, engineering a successful racecar is incredibly complex and expensive. In light of the recent F1 dominance of Mercedes, which many experts within Ferrari attribute to Mercedes’s partnership with US engineering, AM firm Stratasys, allowing for rapid tweaking of components in a process known as fast AM, Ferrari is already behind. [5]
The managing directors in Marenello are more than well aware of this and at the heart of Ferrari’s efforts to regain its position at the top of the podium are two new Renishaw Additive Manufacturing machines. Renishaw will utilize metal powder bed fusion technology to build challenging, metal engine pieces with complex designs and thin walls that traditional manufacturing could not achieve. [6]
While it appears Ferrari is focusing on utilizing 3D printing within its Scuderia Ferrari racing arm, there are substantial costs associated with AM that can really only be diffused with scale at the moment. Moving beyond a short time horizon, of which the goal is to win another Constructors and Drivers Championship, Ferrari must take the lessons and knowledge gained in Formula One and apply it to its street cars. Managing costs will be a particular challenge for Ferrari, a company known for its exclusivity and limited production. Ferrari has the ability to overcome some scale issues as a result of one of AM’s inherent strengths – the ability to manufacture hard-to-find parts without having to make costly new molds. [7] In this way, Ferrari can boost part sales for its large, antique collector market.
Additionally, the Ferrari-Renishaw team face other challenges, specifically, figuring out how to conduct effective material testing of 3D produced components, especially when production shifts to hollow parts, ascertaining proper 3D alloys, and ensuring there is a next generation of engineers on hand who can fully unleash the power of AM technologies. Failures to address some of these concerns can carry substantial hidden costs in the form of defective, unsafe parts, which could easily land Ferrari in costly litigation with its consumers. Fortunately, it appears that the engineers at Renishaw are acutely aware of their own equipment and engineering limitations, acknowledging, “Unless great care is taken, the quest for extreme light weight could result in weak points and fragility.” [8] Ferrari engineers are also making alterations to their engine design to account for changes in material composition and reliability, as well as temperature and pressure changes. [9]
In the coming years the AM community needs to address some fundamental concerns: How can AM be expanded into utilizing other materials (aside from metal-alloys and plastics) to further improve production processes? And how can the large costs and slower speeds be compensated in a way that companies that have not achieved scale – or cannot achieve scale – can still utilize this powerful new technology? (800)
[1] Lim, Choon Wee Joel, Kim Quy Le, Qingyang Lu, Chee How Wong. (Jul-Aug 2016). An Overview of 3-D Printing in Manufacturing, Aerospace, and Automotive Industries. [online] Harvard Library. Available at: https://ieeexplore-ieee-org.ezp-prod1.hul.harvard.edu/document/7517429 [Accessed 9 Nov. 2018]
[2] Lim, Choon Wee Joel, Kim Quy Le, Qingyang Lu, Chee How Wong. (Jul-Aug 2016). An Overview of 3-D Printing in Manufacturing, Aerospace, and Automotive Industries. [online] Harvard Library. Available at: https://ieeexplore-ieee-org.ezp-prod1.hul.harvard.edu/document/7517429 [Accessed 9 Nov. 2018].
[3] Lim, Choon Wee Joel, Kim Quy Le, Qingyang Lu, Chee How Wong. (Jul-Aug 2016). An Overview of 3-D Printing in Manufacturing, Aerospace, and Automotive Industries. [online] Harvard Library. Available at: https://ieeexplore-ieee-org.ezp-prod1.hul.harvard.edu/document/7517429 [Accessed 9 Nov. 2018].
[4] Bonnín-Roca, Jaime, Parth Vaishnav, Joana Mendonça, Granger Morgan. (MIT Sloan Management Review Spring 2017). Getting Past the Hype About 3-D Printing. [online] Harvard Library. Available at: https://search-proquest-com.ezpprod1.hul.harvard.edu/docview/1885885282/90DBF9E43AA3450FPQ/1?accountid=11311 [Accessed 9 Nov. 2018].
[5] Pooler, Michael. (23 April 2017). 3D printing starts to gain traction in industrial tool kits. [online]. Financial Times. Available at: https://global-factiva-com.prd2.ezproxy-prod.hbs.edu/ga/default.aspx [Accessed 10 Nov. 2018].
Sher, Davide.(22 June 2018). Ferrari F1 reveals using metal AM systems from Renishaw for fast part production. [online] 3D Printing Network. https://www.3dprintingmedia.network/ferrari-f1-additive-manufacturing-renishaw/ [Accessed 12 Nov. 2018].
[6] Moda, O. (2018). Ferrari additive manufacturing. [online]. Renishaw. Available at: https://www.renishaw.com/en/ferrari-additive-manufacturing—43506 [Accessed 12 Nov. 2018].
[7] Lim, Choon Wee Joel, Kim Quy Le, Qingyang Lu, Chee How Wong. (Jul-Aug 2016). An Overview of 3-D Printing in Manufacturing, Aerospace, and Automotive Industries. [online] Harvard Library. Available at: https://ieeexplore-ieee-org.ezp-prod1.hul.harvard.edu/document/7517429 [Accessed 9 Nov. 2018].
[8] Moda, O. (2018). Ferrari additive manufacturing. [online]. Renishaw. Available at: https://www.renishaw.com/en/ferrari-additive-manufacturing—43506 [Accessed 12 Nov. 2018].
[9] Davies, Sam. (1 February 2017). Ferrari look to 3D printing to revamp 2017 Formula 1 engine. [online]. TCT Magazine. Available at: https://www.tctmagazine.com/3d-printing-news/ferrari-3d-printing-revamp-2017-formula-1-engine/ [Accessed 12 Nov. 2018].
[10] Getty Images. (15 March 2016). F1 2016 Team Preview: Scuderia Ferrari. [online]. NBC Sports. Available at: https://motorsports.nbcsports.com/2016/03/15/f1-2016-team-preview-scuderia-ferrari/ [Accessed 12 Nov. 2018]
Great story about how Ferrari is trying to become #1 again in the racing industry. I was wondering how the regulatory environment would impact the ability to use some of these pieces on the circuit. Fully understand the great value of AM for building prototypes and allowing the team to test a lot of different ideas quickly and at a small scale, but assuming that the parts that go into the Ferrari for a race are likely highly regulated, do you think the proliferation of AM might cause the race organizers to ban those parts? Not sure how the committee balances the desire for innovation with the necessity of ensuring an even playing field for contestants…
Great read. Additive manufacturing in the steel space is of great interest to me. Two things concern me in the space specifically: the ability to produce materials with the same structural integrity and performance when compared to traditional manufacturing methods and the ability to perform predictive analytics such that failure becomes predictable. F1 is notorious in its history for producing HS alloys that fail in a brittle way during the races, some of which have caused life-threatening collisions. As we transition into a space that is more high performing (due to the nature of the alloys) and less predictable (due to lack of developed non-destructive testing techniques), will the added conservatism hinder the potential of this process in the short term. Moreover, F1 is considered a breeding ground for consumer car technologies. Can additive manufacturing in F1 be scalable and cost-effective enough to be transferred into the consumer car segment?
Great post! As someone who knows very little about both (a) additive manufacturing and (b) Ferrari, it was super interesting to read and learn about. I’m curious to understand whether the consumer of a Ferrari will view cars made with AM will be seen as superior or inferior to cars made the traditional way. Will cars made with AM be able to compete with cars made without AM? Furthermore, what will be the tipping point for the industry to change such that (if ever) all cars will have parts made with AM? I imagine that there will be some regulation (hopefully) to balance out companies that have money and those that do not.
Thanks for the very informative text, Ryan. As a Formula 1 fan, I had little knowledge of the impact AM had in the background of car development. Also, as I first started to read your article, I kept wondering if Ferrari would have the guts to make the first move, but when you brought up the notion that Mercedes already being one step ahead of them, it all made more sense.
Still, I am left with two questions for your future reflection. 1) From your text, I understand that partnering with Renishaw will be a costly investment for Ferrari, both in terms of money and time. How should Ferrari go about hedging this decision if the results do not show in the milliseconds of performance that separates winners from losers? 2) How should Ferrari balance the many moving parts that make a winning team (e.g. driver, engineers, car development), meaning what if Ferrari does have the best car but does not have the best driver to steer the wheel? Should they leverage this partnership to get better sponsors to afford top drivers?
Great read – Given the new opportunity with AM if Ferrari pursues these partnerships, would you think they should try and iterate on the existing designs using AM, or use the technology to rebuild from the ground up? While I think the former helps them most effectively gain speed and learning for their effort, I wonder if the engineers fully grasp how different a design could be if you essentially eliminated any manufacturing restrictions.
As an avid Mercedes-AMG fan (another great year), for Ferrari’s sake I’m afraid this may be too little too late. Engine and car development in F1 can be very difficult as there are heavy restrictions on testing, so even if Ferrari can design new systems built upon the benefits provided by AM, I’m not sure they will be able to test them adequately to make a difference in the next couple of seasons. Adding to my concerns is that there may be material property differences between parts made with AM and with traditional machining methods, ie the grain structure of metal processed in the two methods are radically different and likely behave differently under the extreme stresses of an F1 race. Do you think Ferrari will be able to close the gap to Mercedes now that they are investing in AM?
Great article, Ryan! As a car guy and a Ferrari fan, this article was very interesting to read. However, as mentioned is some of the previous comments, it is a shame that Ferrari was not a first-mover in this space, giving room for Mercedes-AMG to lead the way in developing their F1 engines using advanced AM techniques. But it is still not too late for Ferrari, as they could find a way to differentiate themselves and benefiting from AM in other aspects, other than the F1 engine. For example, as any driving enthusiast would know, car handling is just as important (if not more important) as speed, and Ferrari could lead the way in using AM to develop more sophisticated suspension, chassis, braking, and aerodynamic systems in their F1 cars, giving their drivers an edge in the more demanding tracks.